Jul 15 2009
Like the Energizer Bunny, a reinforced, 100-percent-solids thick-film epoxy interior lining, Tnemec Bridgeport Glass Armor 300, keeps going and going and going as it protects several petroleum storage tanks in Pasadena, Texas, from corrosion. Originally applied to the tanks in 1977, the Glass Armor linings were recently found to be in good condition when tested in accordance with the American Petroleum Institute (API) 652 Linings of Aboveground Petroleum Storage Tank Bottoms, according to Tnemec coating consultant Eddie Borne. "The tanks coated with the Tnemec Glass Armor thick-film epoxy will have been in service for nearly 50 years on their next scheduled API 652 inspection," Borne acknowledged.
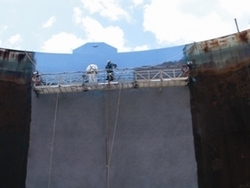
With some thin-film epoxy industrial coatings, recoating is often required following these inspections. Borne cited the example of a large oil refinery in Norco, Louisiana, where thin-film epoxy coatings are being replaced every 10 years following inspections. "This can be a waste of time and money considering that tanks lined with thick film material are lasting decades," Borne noted.
The rate of corrosion in aboveground storage tanks (ASTs) can vary dramatically depending on the type of materials that are being stored and on the atmospheric conditions. Studies have shown corrosion rates in carbon steel tanks are higher on the Gulf Coast compared to the northern U.S. and when protective coatings begin to fail, repair and replacement can be expensive - usually costing as much as $500,000 to repair the surface and reline the tank. This amount is in addition to the estimated $1 million cost of inspection on larger ASTs, which usually requires one month for the tank to be drained, cleaned and refilled.
Selecting protective interior industrial coatings with proven long-term performance can help reduce these costs by extending the service life of petroleum storage tanks as in the case of the Pasadena ASTs. The tanks were originally used to store leaded gasoline and then later were used to hold gasoline with MTBE. Today, the tanks are used to store a blend of gasoline and ethanol with average ambient temperatures of less than 110 degrees F depending on the size of the tank and content turnover.
According to company records, the Glass Armor lining was spray-applied at 40 mils dry film thickness (DFT) to the tank bottoms and 18-inches up the interior shell where the heaviest corrosion occurs due to water and bacteria which can cause microbiological induced corrosion (MIC). "Most corrosion in petroleum terminal storage tanks is caused by water and bacteria," Borne added.
During their latest inspections, each tank was tested using 100 percent Magnaflux technology to determine the thickness of the steel and to check for cracking. Film thickness reading and visual inspections were performed and the coatings in each tank were found to be in excellent condition and put back into service with the next inspections scheduled 20 years from the time of the last inspection.
Periodic integrity testing of ASTs is required under the Environmental Protection Agency's (EPA) Spill Prevention, Control and Countermeasure (SPCC) regulations. These inspections are designed to detect visible signs of leakage, as well as evaluate the corrosion rates and remaining corrosion allowance. The frequency and type of testing performed depends on the size of the tank and its design (e.g., floating roof, skid-mounted, elevated or partially buried), although California requires that all ASTs be integrity tested as least once every 10 years. Typically, ASTs are integrity tested by a professional engineer who must re-certify the tank is structurally sound and capable of holding the specific material being stored.
The SPCC rule also requires inspection of the tank's exterior for signs of deterioration, discharges or accumulation of oil inside diked areas. The effects of salts from the Gulf of Mexico, the industrial environment, acid rain and ultraviolet (UV) light often cause exterior coating systems on petroleum refinery and terminal ASTs to fade and lose as much as 2.0 mils of film each year due to erosion. The EPA expects that visual inspections will occur on a routine basis.
Exterior industrial coatings are specially formulated to protect the outer shell, piping and exposed structural steel at petroleum facilities against UV degradation, abrasion, corrosive fumes and weathering. At many Gulf Coast refineries and terminals, gasoline and water storage tanks are maintained using Tnemec's Series 30 Spra-Saf EN, an advanced technology acrylic polymer, over existing coating systems that have been high-pressure washed using a rotary spray nozzle. Spra-Saf EN resists unsightly mold and mildew growth on the coating film and provides good gloss and color retention so that tanks stay clean after many years of service.