Aug 17 2009
In an exclusive arrangement, Machinery Values Inc. of Harrison, NJ is distributing Pressmaster's new design 10' x 1/4" hydraulic shear into the US market. This shear's revolutionary design solves many problems encountered in other designs of hydraulic shears. This new design has the added benefits of being simpler with fewer moving parts, so has less that can go wrong and results in lower manufacturing costs, so, despite it's significantly heavier frame and extremely solid design, it can be sold at a price well below competing, lower quality shears made in North American, and even matches or beats the price of the lowest quality, cheapest shears made in third world countries.
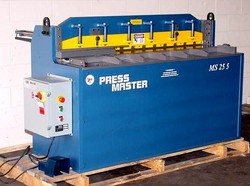
In an exclusive arrangement, Machinery Values Inc. of Harrison, NJ is distributing Pressmaster's new design 10' x 1/4" hydraulic shear into the US market. This shear's revolutionary design solves many problems encountered in other designs of hydraulic shears. This new design has the added benefits of being simpler with fewer moving parts, so has less that can go wrong and results in lower manufacturing costs, so, despite it's significantly heavier frame and extremely solid design, it can be sold at a price well below competing, lower quality shears made in North American, and even matches or beats the price of the lowest quality, cheapest shears made in third world countries.
The two key elements of the design of the Pressmaster Shear are the unique hydraulic system and the extraordinary rigidity of the shear frame. Pressurized oil is sent to two synchronized cylinders which press down uniformly together. No matter where the operator places the metal to be cut the ram comes down perfectly level. There is no racking or twisting of the ram in its guides and this fact equates to many years of quality cuts and trouble-free service. When pressure is removed (when the operator takes his foot off the foot pedal) pressurized oil is sent into the opposite end of the cylinder pushing the pistons back up and pushing the oil out a separate return valves and back to the tank. This system has three terrific advantages over conventional designs. First, the cylinders are always exactly in sync and always move in tandem without the need for any kind of balancing system. Second, the oil is continuously circulated back to the tank where it can cool off before being used again. Third, the instant return feature, when the foot pedal is released, besides the obvious safety advantage, there is a productivity gain because it greatly increases the strokes per minute the machine can achieve when cutting less than full length pieces - the shorter the piece cut, the more strokes per minute and the more productive the machine
Another key feature of this new design is the complete lack of adjustments for Rake Angle and Blade Gap. All other shears in the below $50,000 price range require the operator reset the blade gap when changing from thicker to thinner materials or vice versa. Some shears require a change in rake angle as well. These changes take time and, what's worse, if forgotten about can cause damage to the shear requiring a great deal of time and effort to repair. Thin materials cut with a big blade gap setting tend to fold over causing the damage. When attempting to cut thick materials with a small blade gap the shear will stall and fail to finish the cut. The Pressmaster shear is built so solidly that the blade gap and rake angle are both fixed and the machine is capable of cutting paper thin to full 1/4" material with no adjustments whatsoever. In fact, in demonstrations the Pressmaster shear is shown to cut a standard manila envelope cleanly, like a paper shear.
Standard equipment on the new Pressmaster is a Siemens PLC based Touch-Screen Set & Go digital back gauge. The operator punches in the size needed on the touch screen and the back gauge smoothly and quietly moves to the new position. The back gauge mechanism is extremely well made with two large diameter acme screws held by 3" long nylon acme threaded bushings in a heavy steel frame. Everything about the Pressmaster shear is over-built - designed for severe duty and long life. The back gauge comes standard with 36" of travel.
One of the nicer features of the Pressmaster shear is the low rake angle of the blade. Most less costly hydraulic shears have a blade rake angle of 2" per foot. The Pressmaster has a rake angle of just 1/4" per foot. This results in a better cut with much less distortion of the metal (curl). The Pressmaster can use this lower rake angle because the construction is so much heavier than normal 10' x 1/4" shears.
All electrical, hydraulic and mechanical components are industry standard and readily available in North America. You'll never be down waiting for a part to be shipped from overseas - this cannot be said for the comparably priced machines made in third world countries. The Pressmaster is made in North America with parts made in the US and Canada and Germany.
Safety is a major consideration with the Pressmaster shear. One of the main safety features is the foot pedal. You actuate the ram travel down by pressing on the foot pedal. To stop the downward travel you just remove your foot from the foot pedal and the ram immediately reverses travel and returns to the up position.
Overload protection is built into the machine by design. There are two independent systems, one trips if the electrical current draw exceeds a pre-determined amount, and a second system trips if the hydraulic pressure exceeds limits. In either case, the machine stops before any damage can be done by a careless operator trying to cut material this machine is not rated for.
Another nice feature of the Pressmaster shear are the blades themselves. First, they are made of D2 high-carbon premium-quality tool steel - usually an option on most shears. This super hard metal makes the Pressmaster shear blades last many times longer than standard shear blades. Also, instead of the normal, costly one-piece 10' long blades that come with most shears, the Pressmaster shear is made with a segmented blade. Each upper and lower blade is comprised of (4) 30.5" long pieces. In extensive testing, Pressmaster discovered there is no discernable difference in the quality of the cut between a one-piece blade and a segmented blade. But, there is a tremendous difference in the cost to sharpen or replace a 30.5" long segment or a 10' long blade. Just call around and get prices for a local grinding shop to re-sharpen a 10' blade or a 30.5" long blade - just finding a shop with a 10' capacity grinder is quite difficult. Then, consider the cost to replace a damaged blade if the damage is in just one spot (as it usually is) - you'll only have to replace a single section. Then there is the labor - one man can replace 30.5" sections but it is a two man job to replace a 10' blade.
The blade on the Pressmaster shear has another unique feature, it is not flat at the bottom like most shear blades, it is back-beveled at 5 degrees. Most shear blades do not come down straight, they come down at an angle. The result is a cut that has an angle to it - the work piece edge is slightly beveled - usually about 4 degrees. The Pressmaster blade comes down at exactly 90 degrees giving a cut that results in a square edge on the work piece.
Other features include the 19 trouble-free hold-downs with large pressure pads to protect sensitive work. The two hold-downs next to the squaring arm are close together and share one large pressure pad. This design makes it easy to shear small narrow pieces. Also, the hold-downs are guaranteed never to leak oil for the life of the machine. A 4' squaring arm is standard equipment. Low speed electric motors and low pressure hydraulics translate to long, trouble-free lif