The Italian company Aidro, which as been producing hydraulic systems since 1982, has recently begun to research how additive manufacturing can improve hydraulic systems. Now, after being acquired by 3D printing manufacturer Desktop Metal, Aidro’s 3D printed hydraulic technology is capable of surpassing conventional hydraulic system inefficiency and lead time.
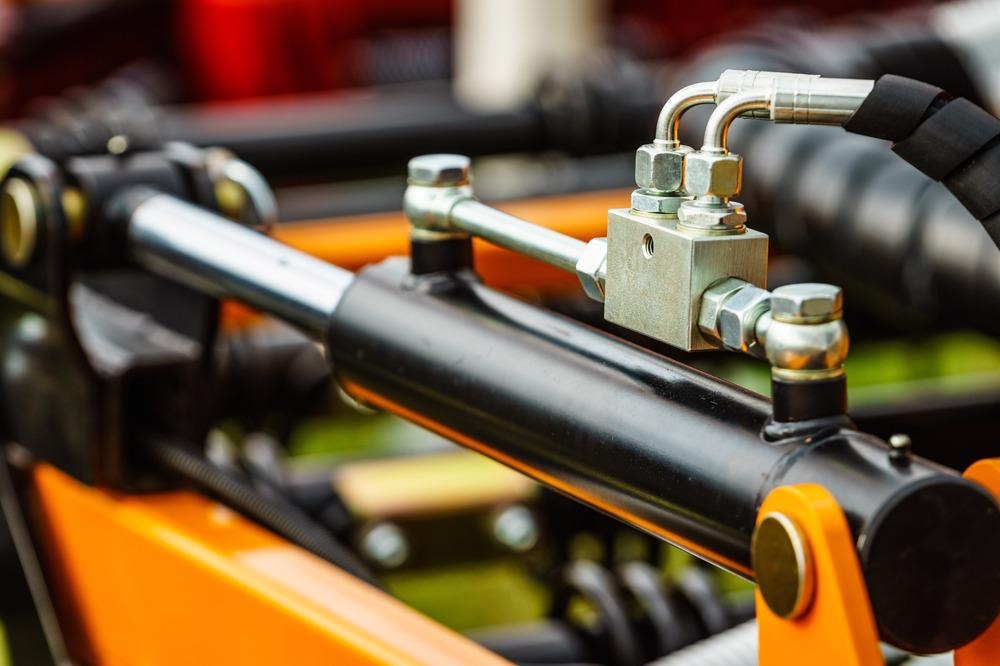
Image Credit: Voyagerix/Shutterstock.com
Aidro, after 35 years of manufacturing hydraulic system components using conventional methods, began to implement additive manufacturing methods such as 3D printing and Selective Laser Melting in 2017.
Since this development Aidro have expanded their manufacturing range significantly, producing components for aerospace, maritime, and even fashion: 3D printing watches, rings, and other jewelry.
In September of 2021, the American 3D printer manufacturing company Desktop Metal acquired Aidro. This acquisition would allow Desktop metal to expand its additive manufacturing methods into oil and gas, as well as aerospace.
The wide variety of uses for hydraulic systems, however, mean that desktop metal are also able to market to maritime, industrial heavy lifting machinery, and more.
In addition to the benefits received by Desktop Metal, this acquisition greatly benefits Aidro who, since 2017, have begun to focus almost wholly on additive manufacturing methods.
Now being a desktop metal company, Aidro is able to make use of the cutting-edge 3D printing technology to develop further components and grow their company’s reach even further.
Advantages and Disadvantages of Additive Manufacturing for Hydraulic Systems
Hydraulic Systems are a widely used method of power transmission, because of their ability to produce large forces efficiently with a high degree of precision.
Using additive manufacturing to create hydraulics may have its drawbacks.
Certain hydraulic components are required to contain large amount of internal pressure. The nature of certain additive manufacturing methods means that high internal pressure may cause AM components to crack or undergo layer delamination (where the layers of the component separate).
Furthermore, many cycles of pressurization and depressurization may cause fatigue due to high hoop stresses.
Until recent developments, most components built using additive manufacturing were relatively brittle compared to their more traditional counterparts. Fatigue over many cycles will lead to the growth and propagation of cracks, which is a serious issue for the integrity of brittle components.
Advancements in AM have reduced these issues significantly, however.
Though any 3D printed component can suffer separation between laminae, there are several solutions to prevent layer delamination, and the use of materials with high strength allows for a greater tolerance of hoop stress, reducing the risk of cracking and fatigue failure.
Like conventional hydraulics, the 3D printed hydraulic components created by Aidro are stainless steel, and able to withstand an internal pressure up to 350 times the average atmospheric pressure.
With the setbacks addressed, Aidro can make use of the many advantages AM has over conventional manufacturing.
Typically, hydraulic components are created by machining down steel into the correct shape, before having its internal cavities created using a drill.
One of additive manufacturing’s most desirable characteristics is its ability to create complex geometries faster and simpler than with subtractive manufacturing.
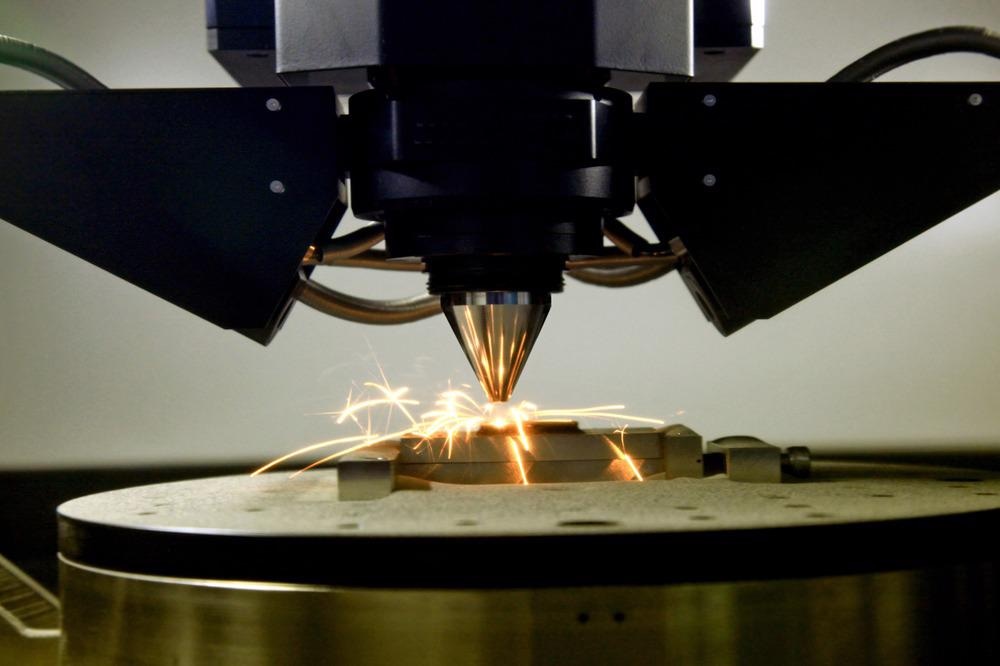
Image Credit: sspopov/Shutterstock.com
This is especially true if the component has a complex internal geometry. It is much more difficult to intricately ‘sculpt’ the interior of a component by removing material than it is to start with nothing and slowly build up an interior layer by layer.
Not only is the ability to create complex geometries faster and simpler for AM, but using this method allows for much easier customization and optimization for internal channels of the valve block.
Removing the requirement of subtractive manufacturing also eliminates the risk of leakage within the valve due to the drilling process.
The rapid manufacturing of 3D printing also means that Aidro and Desktop metal can produce more space-efficient, customizable components on a much larger scale.
The reduction in lead time not only benefits customers, but allows Aidro more time for research and development, and to appeal to new industries with rapid prototyping.
Applications of Hydraulic Systems
Hydraulic systems serve to bear and move large loads efficiently, providing more force relative to other methods of actuation.
For this reason, Hydraulics are used largely in industries that involve bearing heavy loads such as bulldozers, floor jacks, and hydraulic shock absorbers.
Another benefit of hydraulic systems is their ability to operate efficiently under virtually any condition.
Additionally, the liquids used in hydraulic systems are incompressible, unlike air. The compressibility of air results in a loss of precision with controls (a pneumatic system can essentially only be at 0% or 100%).
The liquid in hydraulic systems (oil, typically) can produce a more continuous and precise control system.
Hydraulics in Aerospace—Advantages and Disadvantages
Because of these benefits, hydraulics are widely used in the aerospace industry. Their efficiency under any condition is critical, as the altitude of an aircraft results in significant changes in temperature and pressure.
Their precision makes them useful for flight control systems, and their ability to produce large amounts of force allows them to be used in situations of high load bearing.
The landing gear and brakes of an aircraft are always powered by hydraulic systems, which are able to absorb shock much more efficiently than other methods. Any movement of slats, flaps, elevators, and rudders are performed using hydraulics.
The dependance on hydraulic systems, however, does have some setbacks.
Though it is possible for hydraulic system failure to be immediately noticeable, a small leak of fluid may not be detectable until the system has failed completely.
At that point, the pilot’s only method of controlling the plane would be to change the thrust of the engines, and even then they would not be able to lower the landing gears of the aircraft.
The 3D printing method of hydraulics performed by Aidro is able to tackle these adverse effects to some degree, as no longer drilling the inner valves of hydraulic systems lessens the risk of fluid leakage, and therefore the change of total system failure, dramatically.
Further AM Aerospace Developments by Aidro
In addition to hydraulic solutions, Aidro have begun to expand their additive manufacturing to other components, spanning a wide range of industries.
In aerospace, for example, the company made use of AM to create the ServoFly T4/1, in collaboration with various other companies such as Tecno Elettra Impianti.
The Servofly T4/1, created using Selective Laser Melting (SLM) over 3D printing, is an easily integrated device that allows disabled pilots to fly using only one hand.
The device consists of an actuator mounted over the aircraft’s throttle bar (a typical throttle control for ultralight aircraft), which is connected to a control system mounted on the center stick, allowing the pilot to alter the thrust and control the aircraft with one hand.
References and Further Reading
Aidro. (2021). Aidro: Hydraulic and 3D Printing quality components. [online] Available at:
https://aidro.it/
AMFG. (2020). Application Spotlight: How 3D Printing Enables Better-Performing Hydraulic Components. [online] Available at:
https://amfg.ai/2020/04/16/application-spotlight-how-3d-printing-enables-better-performing-hydraulic-components/
Aviation Stack Exchange. (2016). Why do aircraft use hydraulics instead of pneumatics? [online] Available at: https://aviation.stackexchange.com/questions/21426/why-do-aircraft-use-hydraulics-instead-of-pneumatics
Businesswire.com. (2021). Desktop Metal Acquires Aidro, Adding Critical Capabilities in Design and High-volume Production of Fluid Power Systems Through Additive Manufacturing. [online] Available at: https://www.businesswire.com/news/home/20210909005488/en/Desktop-Metal-Acquires-Aidro-Adding-Critical-Capabilities-in-Design-and-High-volume-Production-of-Fluid-Power-Systems-Through-Additive-Manufacturing
Hanaphy, P., (2021). Desktop Metal to "disrupt oil, gas and aerospace" with Aidro acquisition - 3D Printing Industry. [online] 3D Printing Industry. Available at:
https://3dprintingindustry.com/news/desktop-metal-to-disrupt-oil-gas-and-aerospace-with-aidro-acquisition-195977/
RG Group. (2019). Hydraulic Cylinders: How They're Made & Used
Servofly.it. (2021). ServoFly T4/1. [online] Available at: https://www.servofly.it/en
Skybrary.aero. (n.d). Hydraulic Problems: Guidance for Flight Crews. [online] Available at: https://www.skybrary.aero/index.php/Hydraulic_Problems:_Guidance_for_Flight_Crews
Twi-global.com. (n.d). What are the Advantages and Disadvantages of 3D Printing? [online] Available at: https://www.twi-global.com/technical-knowledge/faqs/what-is-3d-printing/pros-and-cons
Yuken Hydraulic Specialists. (2019). Advantages of using a hydraulic system. [online] Available at: https://www.yukeneurope.com/advantages-of-using-a-hydraulic-system/
Disclaimer: The views expressed here are those of the author expressed in their private capacity and do not necessarily represent the views of AZoM.com Limited T/A AZoNetwork the owner and operator of this website. This disclaimer forms part of the Terms and conditions of use of this website.