Sep 1 2009
LyondellBasell Industries is launching a new high-performance range of Lupolen high density polyethylene (HDPE) resins to address the diversified requirements of customer rotomolding applications.
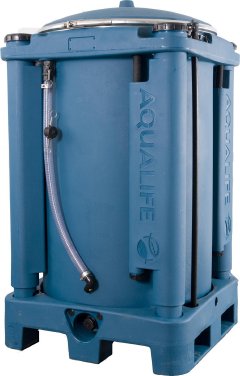
Produced using LyondellBasell's Lupotech G low pressure gas phase process technology which employs a unique catalysis system, Lupolen GX 5002 and Lupolen GX 5003 resins achieve excellent cold temperature impact and environmental stress cracking resistance. Typical customer applications may include industrial storage tanks, containers, intermediate bulk containers, furniture, and playground and sporting equipment.
Industry-defining performance
With a combination of good impact/stiffness balance and low temperature impact down to -30°C applications produced with these resins can withstand harsh transport conditions in cold weather. Lupolen GX 5002 resin can be considered by customers for use in the production of tanks and large containers; it outperforms other polyethylene resins particularly in terms of environmental stress cracking resistance. Full Notch Creep Test (FNCT) results showed that Lupolen GX 5002 resins performed better than competitive resins. With similar advantages in mechanical properties and a melt flow rate of 7.5 g/10 min, Lupolen GX 5003 can be considered by customers for use in a variety of complex parts such as containers, crates, marine equipment, outdoor furniture, and leisure and playground equipment.
Historically unattainable with other processes such as blow molding, injection molding or thermoforming, the rotomolding technology enables the design and production of complex, intricate parts, without the high pressures typically required during the processing and subsequent welding of final parts. Due to their elevated fluidity, Lupolen GX 5002 and GX 5003 resins offer converters the potential to improve processing conditions compared to conventional materials.
According to Cees Besems, Technical Manager of Industrial Packaging for LyondellBasell, it is important to balance the melt flow rate against mechanical properties. "Typically, melt flow rate and cold temperature impact performance contradict each other, but these new grades now offer the mechanical properties required, with a significantly optimized melt flow rate."
Thin-wall design possibilities
With the launch of the new resins, LyondellBasell is expanding the performance envelope of HDPE used in rotomolding applications. "A higher melt flow rate and improved stiffness enable converters to address thin-wall design and lightweight part requirements. In addition, the increased density combined with a high environmental stress cracking resistance can increase the creep stress level of polyethylene, which is particularly important for large rotationally molded containers and tank applications typically exposed to internal pressure during storage.
Another advantage offered by the new Lupolen grades is a wide processing window. Cooking time, one of the determining factors of cycle time in rotomolding technology, is shorter, thereby reducing the overall cycle time.