Sep 27 2016
Following the Indian government’s push for a green future and economic development, the manufacture of supercritical components for power generation is vital. Using a Nikon Metrology ALTERA coordinate measuring machine (CMM), Sri Sai Durga Engineering (SSDE) in Patancheru, Hyderabad, is helping to increase energy efficiency by 40 per cent through the production of supercritical turbine blades.
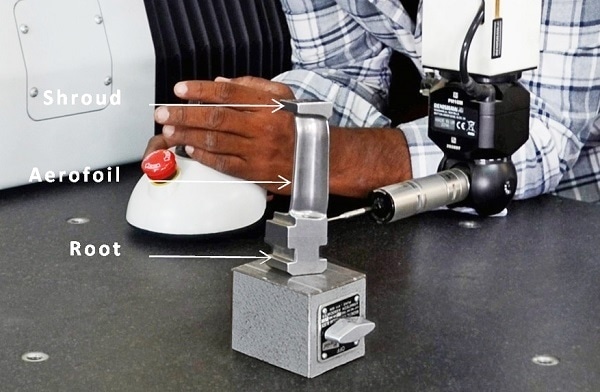
The company has expertise in CNC turning and milling, wire erosion, weld cladding and mechanical assembly and has been particularly successful in the power generation industry, due in part to its focus on customer satisfaction and reduced lead times. Innovative, cost-effective solutions for producing components with challenging specifications allow products to be manufactured to outstanding standards of accuracy and reliability.
The quality department plays an important role to ensure that every component produced meets the correct geometrical specification. However, production of components for supercritical systems, with their tighter tolerances, different dimensions and more complex shapes, has made the metrology more demanding. To maintain the required levels of quality assurance and cope with demand, new measuring equipment that combines speed, accuracy and automation was needed.
The difference between subcritical and supercritical power generators
Supercritical generators have several benefits in the power generation industry, primarily for reducing emissions, enabling power plants to meet ever tightening regulations as well as lower running costs.
There are significant differences in quality requirements between subcritical and supercritical turbine blades. They have to be strictly adhered to, as the efficiency of a turbine depends on the design and manufacture of the blade.
Naveen Reddy, Managing Partner at SSDE
The distinction between subcritical and supercritical generators is defined by the pressure at which they operate. Subcritical generators operate below 220 atm (3,200 psi), while supercritical generators operate above that figure. At a temperature and pressure greater than the critical point, gaseous and liquid phase properties become similar, resulting in a supercritical fluid.
When operating at these parameters, water in the system becomes steam that can power the turbines. Below these conditions, a subcritical generator involves energy loss from latent heat, which is needed for the phase change from liquid to gas. Increased efficiency means fewer fossil fuels are burnt to power the generator and CO2 emissions are lower.
To meet the demanding requirements of supercritical turbine blades, SSDE needed an efficient, comprehensive inspection solution. Naveen explained that components such as the turbine blades SSDE manufactures are vital in maintaining the efficiency of these generators, so the quality and integrity of the parts are of the utmost importance.
The turbine blades are required to be much stronger and a more complex design is required to optimise steam flow. A variety of custom alloys as well as X20, a composite material often used for high temperature steam piping, are employed to meet the required specifications. Blades are manufactured to much tighter specifications, hence the need for geometrical inspection tools to offer micron accuracy when measuring the complex shapes.
Previously, when manufacturing basic blades for subcritical turbines, manual methods were viable for inspecting the straightforward designs. Basic templates or calipers were sufficient for inspection of blades with fixed section geometry. In contrast, for use in supercritical power generators, turbine blades are of complex designs. The twisted aerofoil in particular, with its varying geometry from root to shroud, would pose difficulties for any manual method, not least the length of time needed for inspection.
SSDE invest in the latest metrology equipment
As a company that is always looking to improve its methods, Naveen knew that SSDE needed a new inspection system capable of achieving the highest levels of accuracy, with turbine efficiency largely depending on the quality and integrity of its blades.
He said, “Customer satisfaction is always a priority in my business and limitations of the previous method would mean uncertainty in product quality, leading to customer dissatisfaction.”
Before choosing the Nikon Metrology solution, SSDE consulted several CMM suppliers. The company wanted a machine capable of fast, accurate inspection and selected the ceramic bridge 8.7.6 ALTERA with SP25 continuous scanning probe and Digigraph blade analysis package, part of Nikon Metrology’s CAMIO software suite. The accuracy and repeatability that the system introduced has been a major bonus for SSDE when inspecting components for supercritical generators.
With its ability to follow complex shapes and contours, the SP25 is the ideal tool for measuring blades and has proved to be a big advantage in this application. CAMIO software enables straightforward programming for such inspections due to its ease of use. Profile reporting with blade analysis in Digigraph displays, manipulates and analyses scanned data. Naveen highlighted the best fit feature as important to SSDE, as the quality assurance team can be certain that inspected components conform to specification. Automatic best fitting can be calculated with both text and graphical outputs for direct comparison of measured and nominal profiles.
The Nikon Metrology system has not only raised accuracy and repeatability, making it possible for SSDE to progress to production of supercritical components, but has also made the process much faster. Use of the ALTERA has reduced inspection cycle times by at least 30 per cent since moving from manufacturing subcritical to supercritical components.
Turbine blade manufacture is a major part of day-to-day work at SSDE, but the industry has peaked, so SSDE has diversified into other sectors. It has now started to offer its expertise for the production of components in other industries, such as tricone rock bits used in borehole drilling for extracting ground water, oil and gas.