While it could offer excellent potential for use in polymer tribology applications, there has been little research thus far into the potential of 3D printing in optimizing polymer friction and wear characteristics. The research was published in the journal IOPScience.
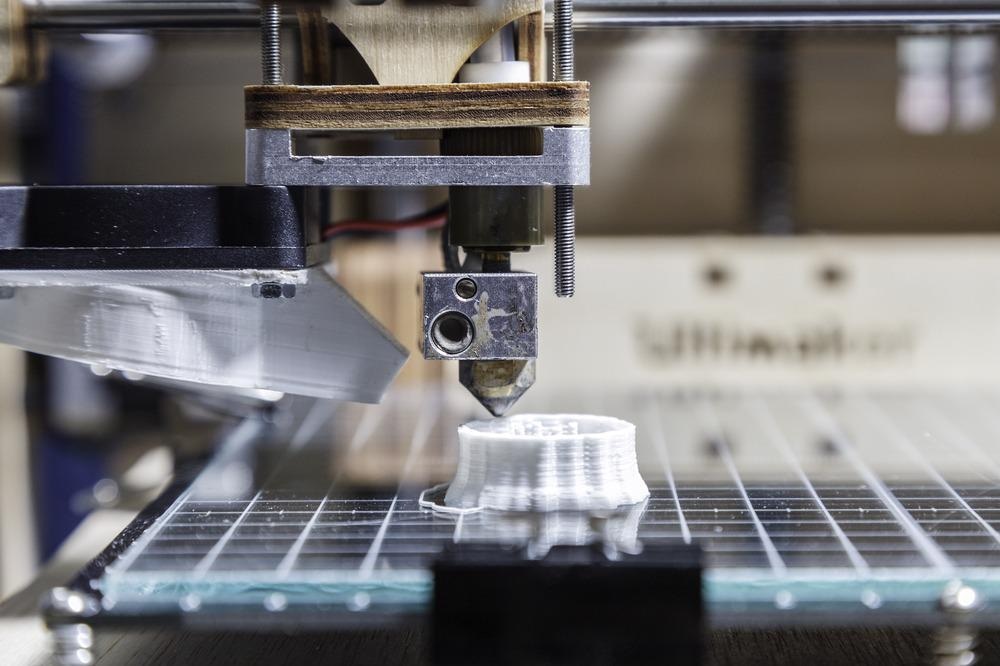
Study: Measurement Science and Technology in press. Image Credit: Sergi Lopez Roig/Shutterstock.com
Polymer’s potential for the formation of transfer film (TF) on the counterface is extremely useful, because this TF acts as a vital protective layer, limiting damage to the soft polymer and better stabilizing its coefficient of friction.
Where specifically high wear resistance is required, manufacturers of PTC (polymer tribo-composites) will tend to include additives such as PTFE, bronze, and MoS2 to the bulk material. These additives act as solid lubricants, but their addition can limit the polymer composite’s overall mechanical strength.
Tensile test specimen (ISO 527-1:2012 standard). Image Credit: Mátyás Ando et al., IOPScience
Because only the top surface’s characteristics are important in defining a PTC’s tribological properties, more recent research has looked at the possibility of only including additives in the top surface, developing what is essentially regarded as hybrid polymer tribo composites (hPTCs).
Recent advances in 3D printing methods have led to their application in the production of these hPTCs. 3D printing allows the additives designed to optimize a polymer’s tribological properties to be inserted into its matrix at predetermined locations; for example, the top surface.
A 3D printed material’s alignment and composition are known to have a central role in its friction and wear characteristics.
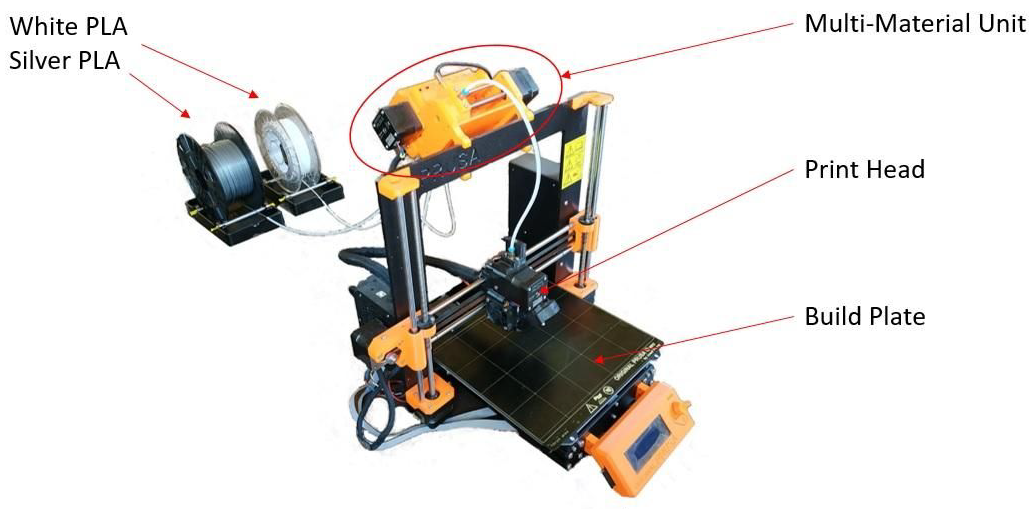
Prusa i3 MK2S printer used to manufacture the PLA specimens. Image Credit: Mátyás Ando et al., IOPScience
In order to explore the potential of 3D printing to optimize and customize these qualities, a new study presented in the Measurement Science and Technology journal has highlighted the application of fused deposition modeling – a popular technique ideal for multi-material 3D printing - in the printing of advanced hPTC materials.
The study used 3D printing techniques to generate two different surface patterns—line and circular—on a number of 3D printed test specimens. The patterns were printed using white and silver Poly Lactic Acid (PLA) and the test specimens themselves were printed with varying amounts of each type of PLA to enable easy mapping and analysis of wear patterns and surface plastic flow as testing progressed.
Using a pin-on-disc tribotester, the researchers were able to perform a series of wear tests that involved continuous sliding of the specimen (which acts as a pin) against the instrument’s steel discs.
The number of tests and length of testing were optimized to avoid thermal degradation of the polymer – an important consideration in ensuring that any deformation, modification, or other material loss was solely the result of wear and not heat. The tests were air-cooled as an additional means of ensuring this.
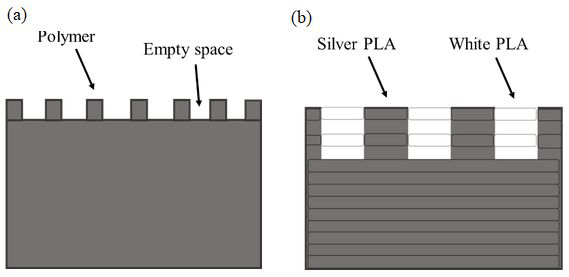
Types of top surfaces: (a) textured surface, alternating polymer, and empty spaces (b) surface pattern, which is fully filled with polymer material, as the specimens used in the present work. Image Credit: Mátyás Ando et al., IOPScience
The study yielded a number of interesting results. Statistical analyses confirmed that neither line pattern nor dot pattern had any significant impact on the polymer’s tribological properties, based on the friction and wear testing undertaken as part of this study.
It was noted that two different types of transfer film (TF) formed on all of the tested specimens: a heterogeneously and a homogeneously distributed film. This was determined to be the result of an adhesive wear mechanism, caused by material from the polymer being torn from the pin and becoming attached to the metal disc of the testing instrument.
The study found that it was the homogeneous transfer film that was most prominent. This was the case for both the line and circular surface patterned specimens, and it was noted that the type of TF did not correlate with any significant change in the coefficient of friction.
Perhaps the most significant finding of this study was that the dot surface pattern appeared to be more resistant to plastic flow. The researchers determined that this was because the dot patterns were more widely distributed across the polymer surface, making specimen structure more concise and therefore distortion more difficult.
It is clear from these findings that, while there is significant work to be done in terms of optimizing and customizing the tribological properties of 3D printed polymer composites and similar materials, the potential to use specific 3D printed structures to help improve wear and friction resistance offers excellent potential.
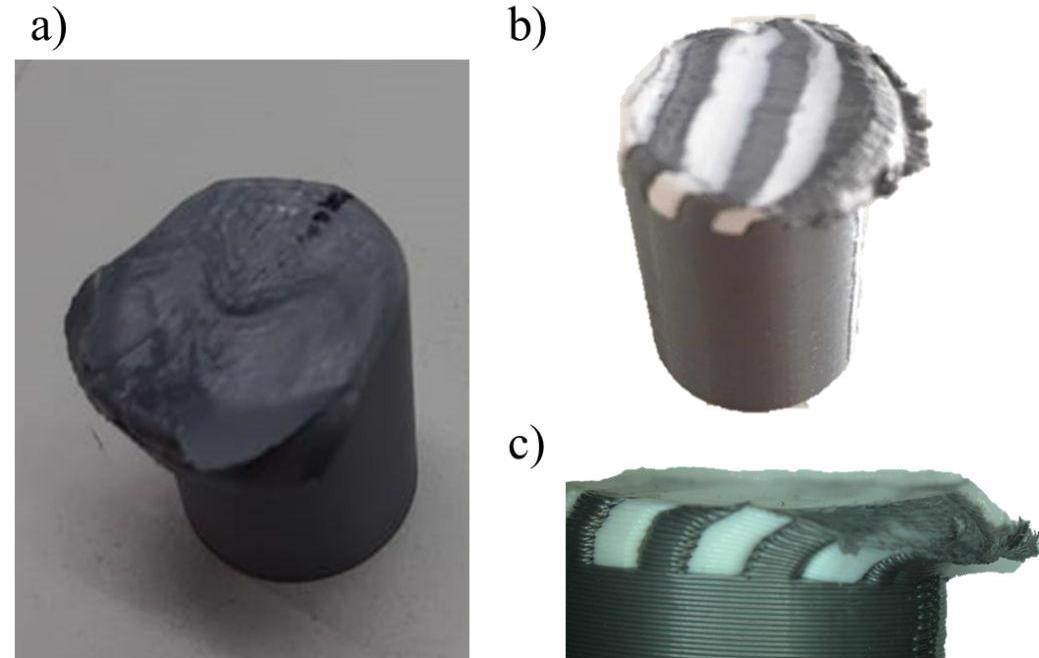
Images of the PLA specimens after tests with severe parameters: (a) specimen S, specimen L50 (b) whole view, and (c) cross-sectional view. Image Credit: Mátyás Ando et al., IOPScience
Polymers already see a myriad range of uses across a number of industrial and commercial sectors, and their use has enabled the fast, efficient production of many essential consumer goods, medical devices, and components for transport applications.
Given their centrality to contemporary society, infrastructure, and industry, advances in optimizing their wear resistance and other key properties are vital to ensuring the longevity, usefulness, and applicability of polymers as their use continues to expand and develop.
Disclaimer: The views expressed here are those of the author expressed in their private capacity and do not necessarily represent the views of AZoM.com Limited T/A AZoNetwork the owner and operator of this website. This disclaimer forms part of the Terms and conditions of use of this website.
Source:
Mátyás Ando et al. (2021) Measurement Science and Technology in press https://iopscience.iop.org/article/10.1088/1361-6501/ac3549