Researchers from Australia and China developed a new method to recycle waste silicon powder produced during the process of solar cell manufacturing, to be used in lithium-ion anodes. This research is published in the journal Materials Today Nano.
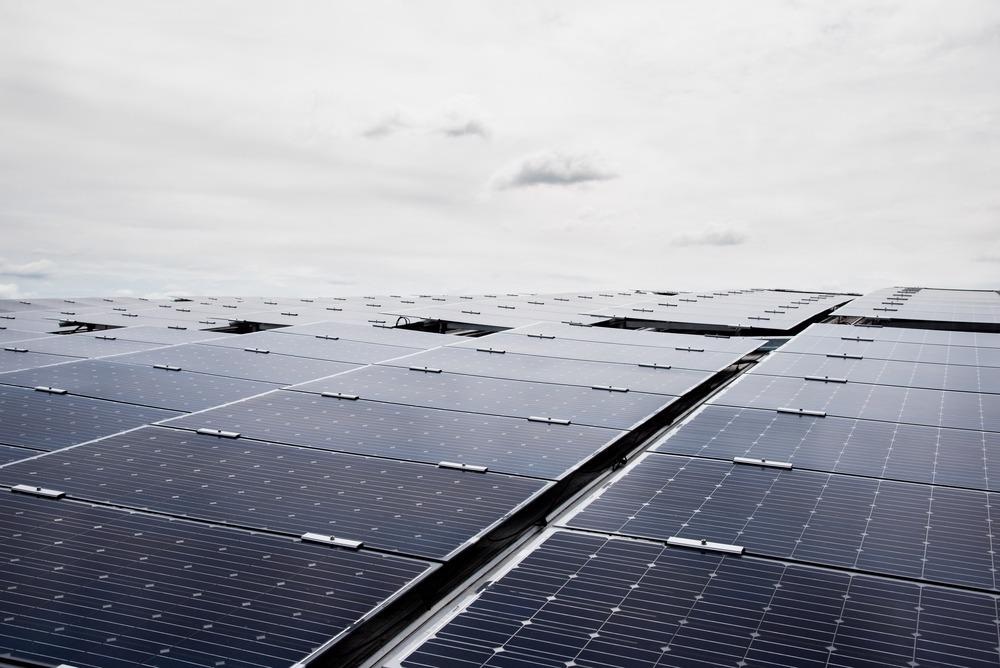
Study: Nano-silver Actuated High-performance Porous Silicon Anode from Recycling of Silicon Waste, Image Credit: DimonGi/Shutterstock.com
Why is Silicon a Promising Material in Anodes of Lithium-ion Batteries?
Silicon is an abundant and one of the most promising materials for use in anodes of high-energy-density lithium-ion batteries (LIBs). It has an ultrahigh theoretical capacity of 4200 mAhg−1 and a low operation potential of less than 0.5 V compared to traditional graphite anodes.
However, the significant volume changes up to 300% during lithiation or delithiation causes cracking and pulverization of silicon particles, detachment of anode materials and current collector, and continuous formation and deformation of solid electrolyte interphase (SEI) films, low initial coulombic efficiency (CE), poor cycling stability, and rapid capacity attenuation.
Many pieces of research have demonstrated that nanostructured silicon-based anode electrodes with high pore density exhibit enhanced electrochemical performance, as the porosity provides a buffer to accommodate stress during the lithiation process.
Also, limited electrode expansion is achieved by mixing carbon-coated porous silicon with graphite. Nano-silicon materials are usually synthesized by the etching silicon templates, chemical vapor deposition, dealloying, and magnesium reduction.
Silicone Waste Recycling is Both Profitable and Sustainable
High-purity silicon is widely used in the solar photovoltaic (PV) cell industry, comprising 95% of most products. The solar energy industry shows 40% to 60% annual growth, making it one of the most rapidly growing renewable energies.
During the manufacturing of silicon solar batteries, diamond wire saw (DWS) technology is used to slice crystalline silicon ingots into wafers 170-190 μm thick, with up to 35% of silicon loss during the wafer cutting process. This material is mainly composed of Si particles, with an average size between 0.3 and 1.2 μm.
However, the properties of diamond wire saw silicon particles (DWSSPs) namely, layered structure, submicron size, and an active oxide layer on the surface limit the effective removal of impurities.
How was the Porous Silicon-Silver-Carbon Anode Fabricated?
The edgeless Si particles were obtained by copper-assisted chemical etching (Cu-ACE) of the washed DWSSP (scrap Si). Then, Si nanoflakes were obtained by removing copper nanoparticles with HNO3 solution.
The Si nanoflakes were then immersed into a mixture of AgNO3, HF, and C2H5OH to obtain porous Si-Ag composites. Ultrasonic dispersion was performed on the mixture of porous Si-Ag and dopamine hydrochloride to form a polydopamine layer on the surface of the Si/Ag. Finally, the Si-Ag-C composite was obtained by carbonization at a higher temperature in an argon environment.
Further, Si-Ag-C composite material, black carbon, and sodium alginate binder were mixed in deionized water to form a uniform paste, which was evenly pasted on the copper foil and cut into pieces of the desired size to obtain the anodes.
Performance of the Prepared Anode
The researchers found that due to the expansion of silicon during lithiation, there are more point-to-point contacts at the edges and corners of these materials, which lead to excessive particle cracking and stress gradient.
This stress concentration can be eliminated by transforming edges of silicon particles into rounded corners and designing porous structures with dispersed nanoparticles. The final Si-Ag-C composite has a double-coated and porous structure that allows release of the volume expansion of the silicon anode, and layer by layer dispersion of the carbon and oxide layers, thus protecting the silicon core from stress damage.
The preparation of Si-Cu and Si-Ag composites is based on nano-metal-assisted chemical etching technology, which reduces copper-silver ions to copper-silver in successive steps. The Cu nanoparticles will first form and deposit on the Si surface by the reduction of Cu2+ ions, as Cu is more positive than Si during the Cu-ACE process, leading to the formation of holes (h+).
Similarly, as Ag is more positive than Si, Ag nucleates and deposits on the Si surface with the reduction of Ag+ ions. Ag+ has a stronger oxidation capability than Cu2+, which results in more abundant h+.
X-ray photoelectron spectroscopy (XPS) of Si/Ag/C indicates that SiC is formed at the interface of Si and C, the carbonization process of dopamine causes a small amount of C-Si bonding, and SiOx is present in the carbon matrix on the surface of the silicon.
Field emission scanning electron microscopy (FE-SEM) demonstrated that a large number of macropores or nanopores formed on Si/Ag composites. These pores act as buffer spaces to accommodate volume expansion in Si during use as a LIB anode material.
The macropores were formed after the nano-copper assisted etching process and nanopores were introduced by nano-silver assisted etching, resulting in both macropores and nanopores in the Si/Ag composites. The cyclic voltammetry (CV) curves of Si/Ag/C and Si/C indicated no reaction between Ag and Li and thus no lithiation of Ag.
The Si/Ag composites anode displayed an enhanced electrochemical performance that was superior to that of pure and porous Si. Also, even after 50 cycles, capacity was maintained at 1535 mAhg−1 with capacity retention of 54%.
Carbon cladding coating was used to further enhance the cyclic stability of the Si/Ag anode. The cladded anode exhibited a great reversible capacity of 1794.6 mAhg−1 after 50 cycles. Additionally, the capacity retention rate increased to 88%, which was the greatest value achieved by any of the anodes.
To conclude, the findings of the study demonstrate that the optimal conditions for the selective recovery of Si from solar cells are 3 M HCl acid solution, 60℃ reaction temperature, 120 min reaction time, and 150 W ultrasonic intensity. Also, the Si purity and recovery rate obtained using this method were 99.85 and 99.24%, respectively.
Reference
Z. Zhang, F. Xi, Q. Ma, X. Wan, S. Li, W. Ma, X. Chen, Z. Chen, R. Deng, J. Ji, H. Fan, C. Chong, Nano-silver Actuated High-performance Porous Silicon Anode from Recycling of Silicon Waste, Materials Today Nano, 2021, 100162, ISSN 2588-8420. https://www.sciencedirect.com/science/article/pii/S2588842021000547?via%3Dihub
Disclaimer: The views expressed here are those of the author expressed in their private capacity and do not necessarily represent the views of AZoM.com Limited T/A AZoNetwork the owner and operator of this website. This disclaimer forms part of the Terms and conditions of use of this website.