By Susha Cheriyedath, M.Sc.Reviewed by Skyla BailyNov 30 2021
In a paper published in the journal Molecules, researchers from China have developed a CaCO3@SiO2 hydrophobic composite by depositing nanoscale silica on calcium carbonate. The composite material has a micro-nano complex structure similar to a "lotus leaf" surface.
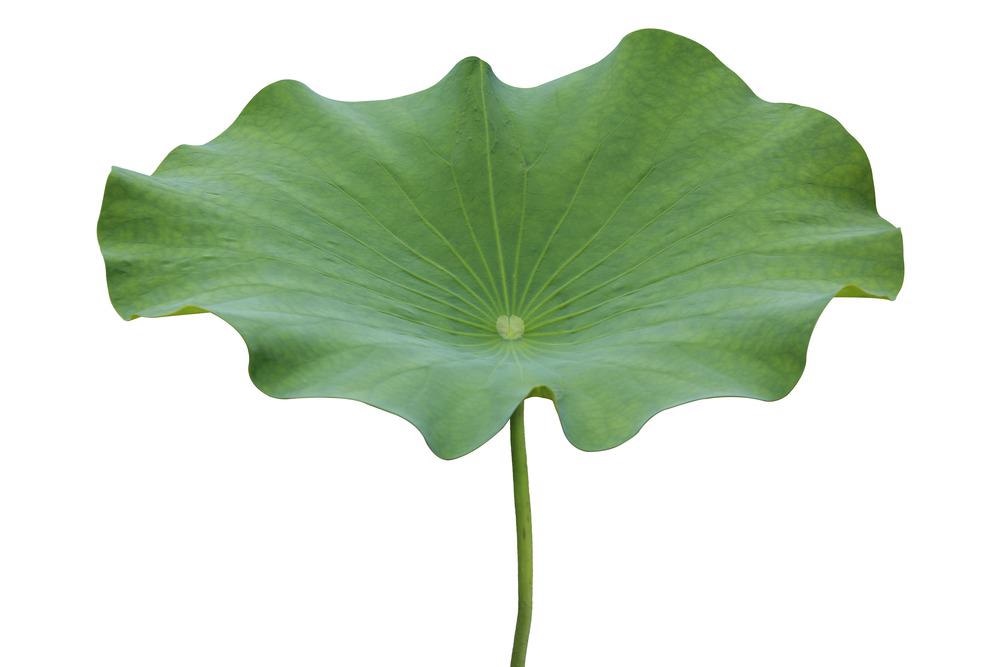
Study: Calcium Carbonate@silica Composite with Superhydrophobic Properties. Image Credit: cyo bo/Shutterstock.com
Hydrophobicity and Composites
Some natural systems can perform self-cleaning, which provides them with the ability to repel contaminants. The lotus leaf is a typical example and is known for its hydrophobicity or self-cleaning properties; this ability is therefore known as the "lotus effect".
Properties such as sliding angle, contact of a drop, hydrophobicity, and low contact angle hysteresis are essential for self-cleaning surfaces. Calcium carbonate is an inorganic chemical with advantages such as a simple working process, high product quality, and low cost.
The high surface fineness of calcium carbonate results in higher surface energy and ease of self-agglomeration in polar solvents. Nano-silica is a nonmetallic nanomaterial; the bonded hydroxyl groups in nano-silica have three forms—vicinal silanols, isolated silanols, and geminal silanol—which improves water absorption.
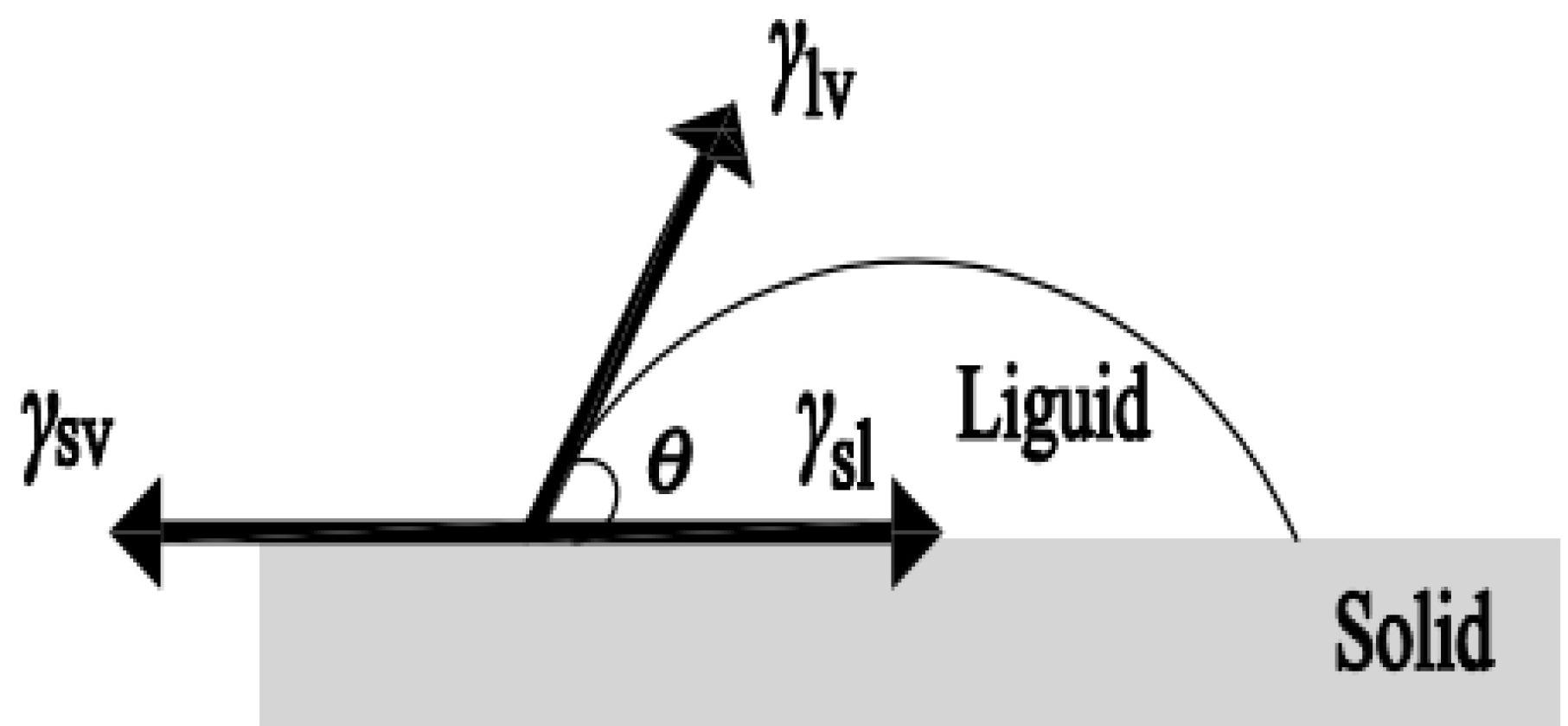
Standard vapor-solid-liquid three-phase interface. Image Credit: Ma, Y. et al., Molecules
In this study, a CaCO3@SiO2 composite material is developed using nanoscale silica deposited on the calcium carbonate surface to improve overall roughness and hydrophobicity. CaCO3@SiO2 composite material particles prepared in the study resemble the mastoid of lotus leaf surfaces due to the presence of nano spherical silica adhering to the micron calcium carbonate surface.
Preparation of CaCO3@SiO2 Composite Material
The preparation process of the CaCO3@SiO2 composite material is divided into the following steps: preparation of spherical calcium carbonate, CaCO3@SiO2 composite material preparation, cubic calcium carbonate development, and surface treatment.
Calcium chloride aqueous solution was prepared with calcium chloride and ammonia water, while TEOS (tetraethyl orthosilicate), ethanol, and ammonia were used to generate the nanoscale silica. The cubic calcium carbonate was prepared by calcium chloride aqueous solution OP-10 and ethyl alcohol.
During surface treatment, 20 g of dry powder of the materials mentioned were dispersed in stearic acid n-hexane solution (45 mL 0.5 mol/L), stirred for 0.5 h, and oven-dried at 70 °C. To perform the surface treatment, the modified materials were spread on the surface of the pressure-sensitive adhesive tape, gently pressed with a glass cover, and flushed with air under pressure to remove free materials.
This process was repeated several times until material particles fully covered the adhesive tape.
SEM image of cubic calcium carbonate (a,b), spherical calcium carbonate (c,d) and CaCO3@SiO2 composite material (e,f). CaCO3@SiO2 composite materials were formed by loading nanosized silica onto spherical calcium carbonate. Image Credit: Ma, Y. et al., Molecules
Observations
Techniques such as X-ray powder diffraction (XRD), scanning electron microscopy (SEM), thermogravimetric analysis (TGA), Fourier transform infrared spectroscopy (FTIR), and X-ray photoelectron spectroscopy (XPS) were used to characterize the morphology and structure of the composite material.
The three composites—cubic calcium carbonate, spherical calcium carbonate, and CaCO3@SiO2 composite—were compared in the tests.
The morphology test observed that the surface of the cubic calcium carbonate is smooth without any bumps and spherical calcium carbonate is slightly concave and convex. The CaCO3@SiO2 composite material’s surface roughness is significantly increased due to the overall surface heterogeneity caused by spherical silica.
The X-ray diffraction pattern of composite material indicates that the composite material is composed of some amorphous silica, a large amount of calcium carbonate, and a small amount of calcite.
The thermogravimetry test is used to test the thermal stability of materials mainly performed to study weight loss in response to the temperature of composites; the results indicate that the weight loss of CaCO3@SiO2 is highest, and thus it can adsorb more.
The initial contact angle (θ) of cubic calcium carbonate, spherical calcium carbonate, and CaCO3@SiO2 composite material are 57.9°, 73.5°, and 76.8°, respectively, while post-treatment with stearic acid, the contact angles of the modified materials (θ) improved to 127.1°, 136.1°, and 151.3°.
The influence of material roughness on its hydrophobicity was investigated using the Cassie model theory and it showed that the CaCO3@SiO2 composite has the highest surface roughness.
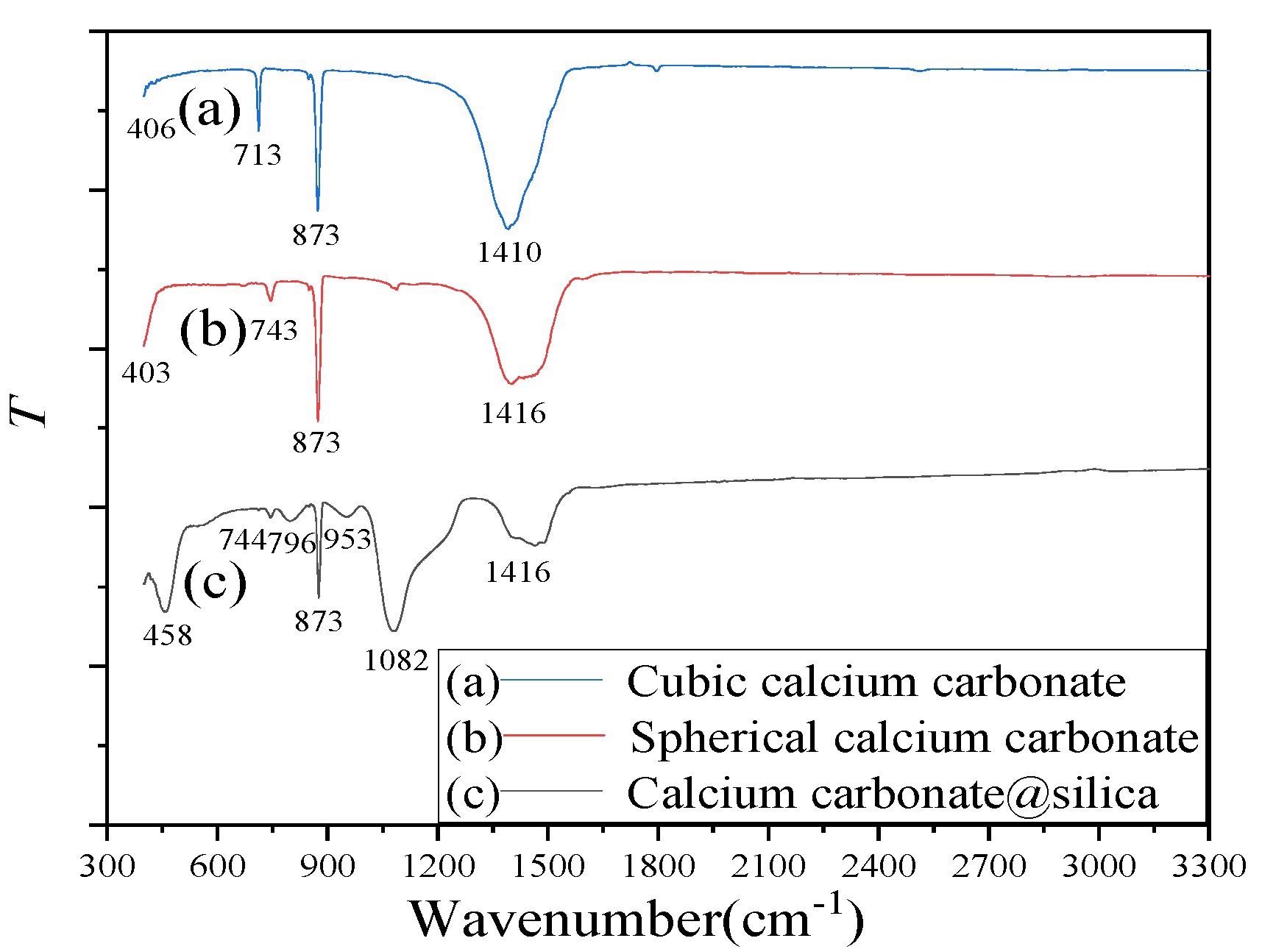
The FTIR of (a) cubic calcium carbonate, (b) spherical calcium carbonate, and (c) CaCO3@SiO2 composite material. Image Credit: Ma, Y. et al., Molecules
Conclusions
The new CaCO3@SiO2 composite material was prepared by combining the nanostructure with the micron structure, and the superhydrophobicity of the material was realized by increasing the surface roughness. After modification with stearic acid, the CaCO3@SiO2 composite had good superhydrophobicity as the contact angle improved, indicating the significance of stearic acid in achieving superhydrophobicity.
The structure became the most critical factor affecting the hydrophobicity of composites as they were coated with stearic acid.
This work offers a new method to analyze the superhydrophobic properties of rough surfaces using the Cassie equation. The CaCO3@SiO2 composite materials prepared are suitable for use in raincoats, superhydrophobic coatings, the construction industry, and waterproof glass.
Disclaimer: The views expressed here are those of the author expressed in their private capacity and do not necessarily represent the views of AZoM.com Limited T/A AZoNetwork the owner and operator of this website. This disclaimer forms part of the Terms and conditions of use of this website.
Source:
Ma, Y.; Tian, P.; Bounmyxay, M.; Zeng, Y.; Wang, N. Calcium Carbonate@silica Composite with Superhydrophobic Properties. Molecules 2021, 26, 7180. https://www.mdpi.com/1420-3049/26/23/7180