By Surbhi JainReviewed by Susha Cheriyedath, M.Sc.Feb 23 2022
In a pre-print article posted to the server Research Square in submission to the journal Nature Portfolio, researchers reported the development of inverse vulcanized polymers via mechanochemical methodology.
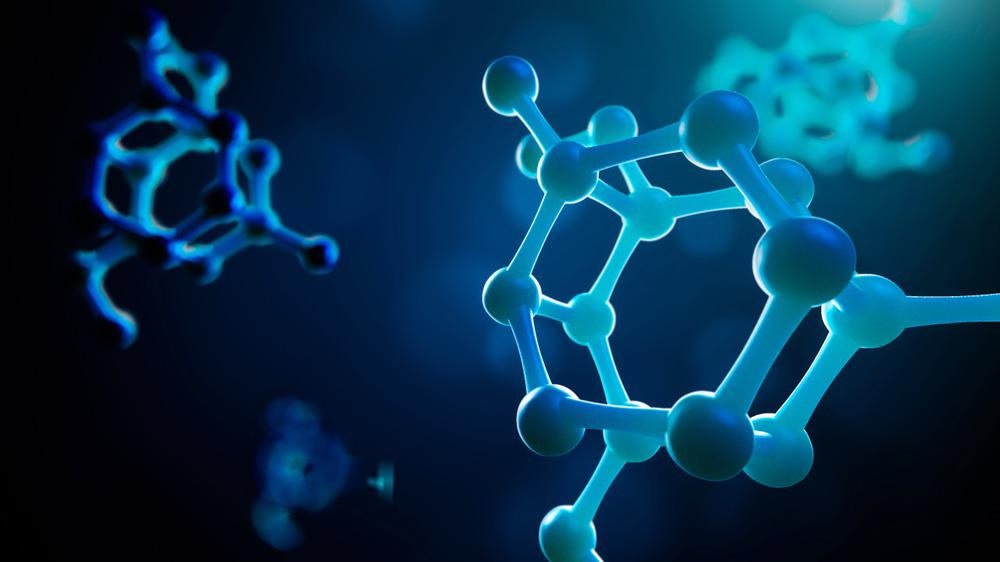
Study: Mechanochemical synthesis of inverse vulcanized polymers. Image Credit: Egorov Artem/Shutterstock.com
Background
Elemental sulfur is produced in large quantities as a by-product of the crude oil hydrodesulfurization process, although it is only partially utilized despite its primary use in the manufacturing of sulfuric acid. As a result, there is a pressing need to find a cost-effective strategy to convert this trash into useful products. Inverse vulcanization functions are a sustainable platform that give plastics a more sustainable future, starting with waste material and progressing to practical applications.
This is a sustainable method that can convert sulfur, a by-product of the chemical industry, into polymers with a wide range of green uses, including heavy metal capture and recyclable materials. However, because the method normally necessitates high temperatures (about 159 °C), the crosslinkers required to stabilize the sulfur are limited to monomers with a high boiling point.
Because of the conditions required to cleave the S-S bonds to permit ring-opening and subsequent polymerization of the eight-membered ring through heating, inverse vulcanized polymers are often generated through bulk polymerization at a high temperature (159 °C). However, there are also plenty of issues with this polymerization process. Alternative, easier, and safer synthesis processes should be investigated in order to employ this new material in an industrial setting.
Reaction scheme of MS of inverse vulcanized polymers and monomers used. Image Credit: Yan, P et al., Nature Portfolio
About the Study
In the present study, the authors presented a novel method for inverse vulcanization called mechanochemical synthesis (MS), which possessed the benefits of moderate conditions (room temperature), a quick reaction time (3 h), excellent atom economy, reduced H2S, and a wider monomer range.
The method’s versatility and power were demonstrated through its ability to generate polymers utilizing a wide range of crosslinkers, including aliphatic, aromatic, and volatile crosslinkers, as well as renewable monomers. When compared to thermal synthesis (TS), the MS products captured more mercury. Thermal and light-induced recycling was seen in the prepared polymers.
The researchers showed that ball milling could be utilized to produce inverse vulcanized polymers using a green mechanochemical synthesis (MS) method. This technology used mechanical energy and represented an environmentally friendly process with benefits such as quicker reaction times, homogenous reactions, and excellent atom economy, among others. For the first time, the MS technique was used to examine the production of inverse vulcanized polymers.
This polymerization process exhibited several characteristics like no need for heating, quick reaction, reduced hydrogen abstraction, solvent-free, broader monomer possibilities, no auto-acceleration, and more homogenous reaction regardless of sulfur miscibility with monomers.
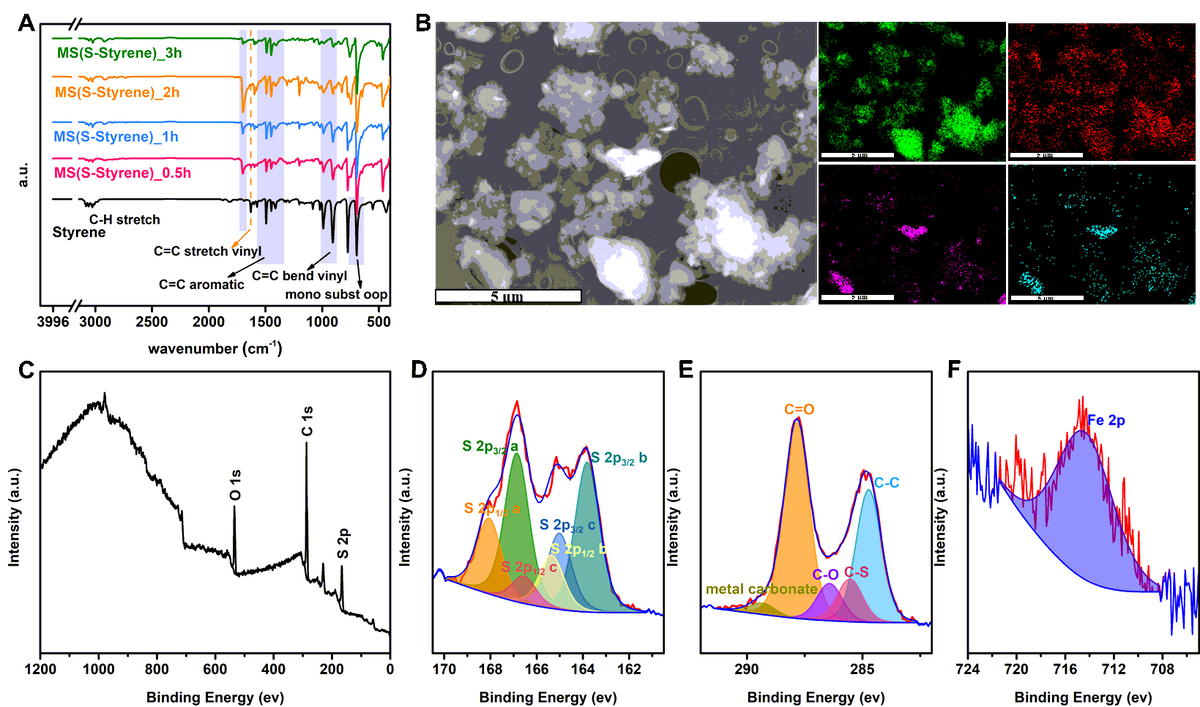
A) Synthesis of MS(S-Styrene) monitored by using FT-IR. B) SEM and EDS images of product MS(S-DIB) with same size bar (5 µm). Panels C) to F) show XPS spectra of MS(S-Styrene); wide scan, and corresponding S 2p, C 1s, and Fe 2p spectra with associated curve fits. Image Credit: Yan, P et al., Nature Portfolio
Observations
In this study, the researchers observed that after 1 hour of reaction, the produced polymer MS(S-1,3-diisopropenylbenzene) exhibited a clear glass-rubber transition, with a clear increase in glass transition temperature (Tg) from -11 °C to -1 °C as reaction time increases from 1 hour to 3 hours.
By using the MS technique, the volatile monomer isoprene was shown to successfully combine with sulfur to generate sulfur polymer. According to the FTIR studies, the peak observed at 1626 cm-1 belonging to the C=C stretch and the peaks observed at 989 cm-1 and 906 cm-1 belonging to the C=C bend both decreased with the increase of the reaction time, which implied that vinyl groups in styrene were consumed to produce the polymer.
Furthermore, it was observed that the polymers had Fe concentrations ranging from 8 to 20 wt%, but the control sample—ball milled pure elemental sulfur—contained only 0.77 wt% Fe. It was also observed that when the temperature reached 80 °C, a slight H2S concentration was discovered in some MS products, but when the temperature reached 140 °C, a large H2S concentration was detected in all MS polymers and TS polymers. In 24 hours, the polymer MS(S-Myrcene) removed the maximum ratio of 62% Hg from a 138 ppm HgCl2 solution and subsequently yielded the highest capacity of 42.3 mg/g. After 40 minutes of UV irradiation at 285 nm, two portions of MS(S- 5-ethylidene-2-norbornene) films were healed together.
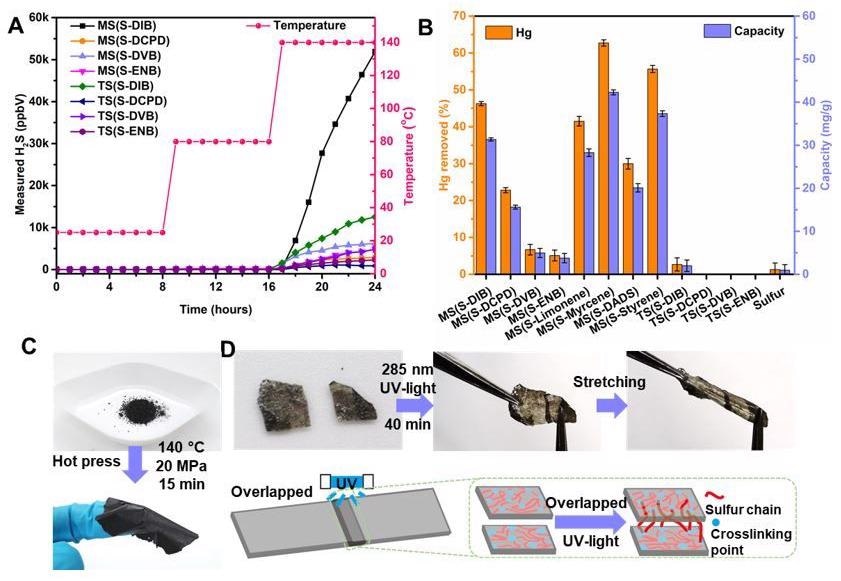
A) H2S measurements on selected MS and TS polymers with ramping temperature at room temperature, 80 °C and 140 °C. B) The percentage mercury removed in solution after 24 hours exposure to each of the materials listed. C) The capacity of mercury removing of each of the materials listed. D) Polymer MS(S-DIB) as an example to show the polymer film is able to be made from polymer powder. E) Polymer MS(S-ENB) film as an example to show the UV-induced self-healing ability of the MS polymer. Image Credit: Yan, P et al., Nature Portfolio
Conclusions
In conclusion, this study elucidated the ability to produce inverse vulcanized polymers via a mechano-chemical technique. It was also determined that iron from steel balls can react with the sulfur polymer to generate inorganic sections that anchor the polymers.
The authors emphasized many improved features of the resulting polymers, including excellent solvent resistance and high mercury uptake efficiency and capacity. This work also demonstrated that the synthetic materials also have strong processing ability, suggesting that they could be employed for a variety of applications beyond UV-induced self-healing.
Overall, the authors believe that in comparison to traditional thermal synthesis, the mechanochemical inverse vulcanization process allows for a greater monomer selection and potential product range, all while starting with a by-product, sulfur.
*Important Notice
Research Square publish preliminary scientific reports that are not peer-reviewed and, therefore, should not be regarded as conclusive, guide clinical practice/health-related behavior, or be treated as established information.
Disclaimer: The views expressed here are those of the author expressed in their private capacity and do not necessarily represent the views of AZoM.com Limited T/A AZoNetwork the owner and operator of this website. This disclaimer forms part of the Terms and conditions of use of this website.
Source:
Yan, P., Zhao, W., McBride, F., et al. Mechanochemical synthesis of inverse vulcanized polymers. Nature Portfolio (2022).https://www.researchsquare.com/article/rs-1296181/v1