By Surbhi JainReviewed by Susha Cheriyedath, M.Sc.Mar 11 2022
In an article recently published in the open-access journal Polymers, researchers presented the development of aluminum (Al) platelet-based conductive plastics in a poly(butylene terephthalate) (PBT) - poly(ethylene terephthalate) (PET) polyester blend with co-continuous morphology.
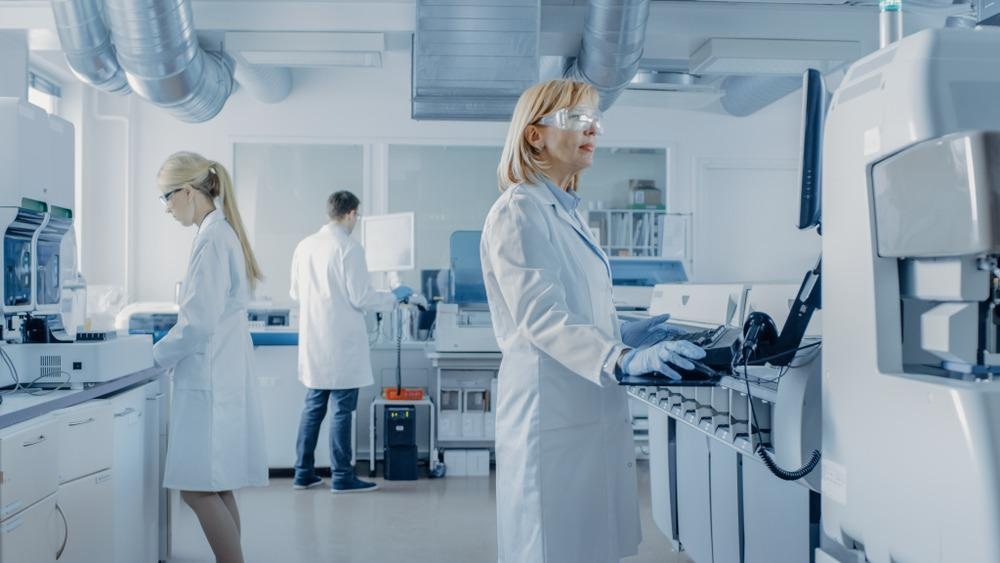
Study: Conductive Plastics from Al Platelets in a PBT-PET Polyester Blend Having Co-Continuous Morphology. Image Credit: Gorodenkoff/Shutterstock.com
Background
Due to applications in electronics and the burgeoning electric car industry, there is a demand for thermally and electrically conductive plastics. Electronic housings must be lightweight, thus conductive polymers would be an excellent choice. Electromagnetic interference (EMI) and radio frequency interference (RFI) from neighboring devices prevent ordinary plastics from being utilized for in-house electronics.
Electronic packaging, light-emitting diode (LED) assembly, and the developing electric car sector all use thermally conductive composites for heat dissipation and heat management. The hunt for conductive plastics continues since meeting all of the needed parameters at the same time is challenging. Some of the conductive plastics principles have been established.
Placing conductive fillers in polymer matrices produces conductive polymers. Because it supports the establishment of a 'segregated conducting network,' a conductive filler in a binary polymer blend with a co-continuous morphology is more effective than in a single polymer.
Schematic diagram of the composite preparation process. Image Credit: Alhamidi, A et al., Polymers
About the Study
In the present study, the authors presented the placement of Al nanoplatelets, a comparatively low-cost conductive filler, in a 60/40 PBT/PET polymer combination. The feasibility of creating a conductive composite with Al platelets by combining them with a 60/40 PBT/PET blend was investigated. This mixture produced a co-continuous morphology which was favorable to the double percolation mechanism, in which conductive particles clustered at domain boundaries and formed a segregated electrically conductive network.
The Al platelets were inserted into a PBT-PET polyester mix with a weight composition of 60/40 to create a co-continuous immiscible blend that allowed for electrical conductivity percolation. To reduce hydrolysis during the melt compounding process, the PET and PBT pellets were dried in an oven at 120 °C for 24 hours. PET and PBT pellets, as well as Al nanoplatelet powder, were combined together physically. With a total injection period of 45 seconds, the mold temperature and holding pressure were kept at 24–26 °C and 6 bar, respectively.
A field emission scanning electron microscope was used to examine the morphology of the Al-60/40 PBT/PET bar at a 5 kV accelerating voltage. Wide-angle X-ray diffraction (XRD) patterns of the unfilled PBT, PET, 60/40 PBT/PET bars and the Al-filled 60/40 PBT/PET bars were recorded using Cu-K radiation to determine the long-range order in the matrix. Differential scanning calorimetry was used to evaluate the melting and crystallization behaviors of PBT, PET, the 60/40 PBT/PET mix, and the Al/PBT/PET bars.
After annealing at 150 °C in an oven for 30 minutes, the length shrinkage of the as-molded bars of amorphous PET, 20 vol.% Al-PET, 60/40 PBT/PET, and 20 vol.% Al-60/40 PBT/PET was measured.
Flexural parameters were determined, including flexural modulus, flexural strength, and strain at maximum tension. The impact resistance of the Al-PBT/PET composites, the resistivity of injection-molded plaques, and the thermal conductivity of the 60/40 PBT/PET blend and its composites were also evaluated.
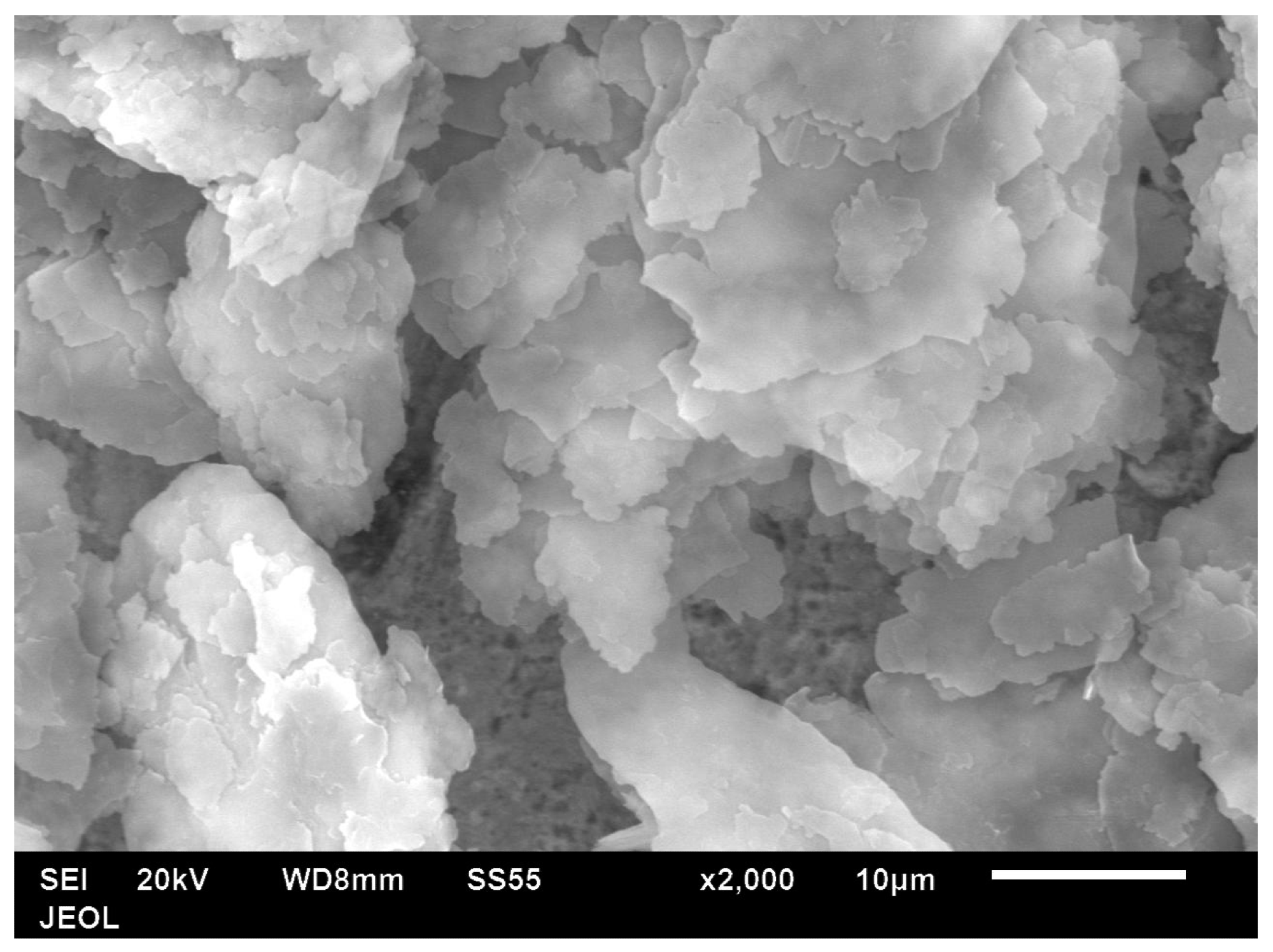
SEM image of Al nano platelet particles. Image Credit: Alhamidi, A et al., Polymers
Observations
While placing 25 vol.% of the Al nanoplatelets in a single polymer (PET) resulted in a material with the resistivity of an insulator (1014 Ωcm), placing the same Al nanoplatelets in a 60/40 PBT/PET blend resulted in a material with the resistivity of an electrostatic charge dissipation material (7.2 x 107 Ωcm).
The results also demonstrated that a drop in electrical resistivity of 6 orders was achieved with 20–25 vol.% Al nanoplatelets in a 60/40 PBT/PET blend matrix. The co-continuous morphology in the 60/40 PBT/PET blend had finer domain sizes, and the contrast was weaker than in other polymer blends.
The Al flakes utilized were found to be not appropriate for aggregating between domain boundaries owing to the finer scale of the co-continuous morphology of the 60/40 PBT/PET blend. When 25 vol.% Al platelets were used, the heat conductivity improved by 2x. The mechanical parameters were found to be within acceptable limits. The tensile modulus as well as the tensile strength increased.
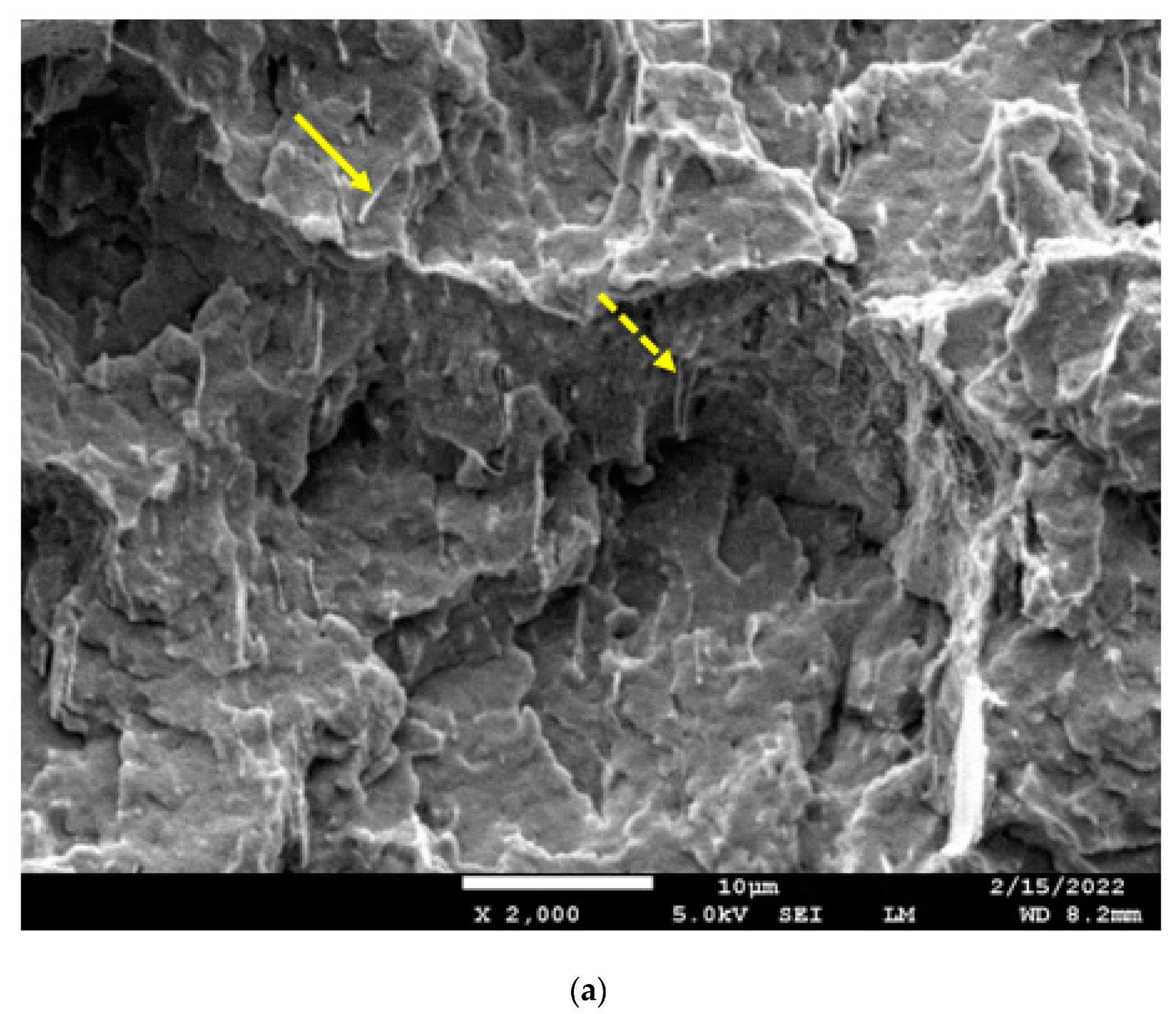
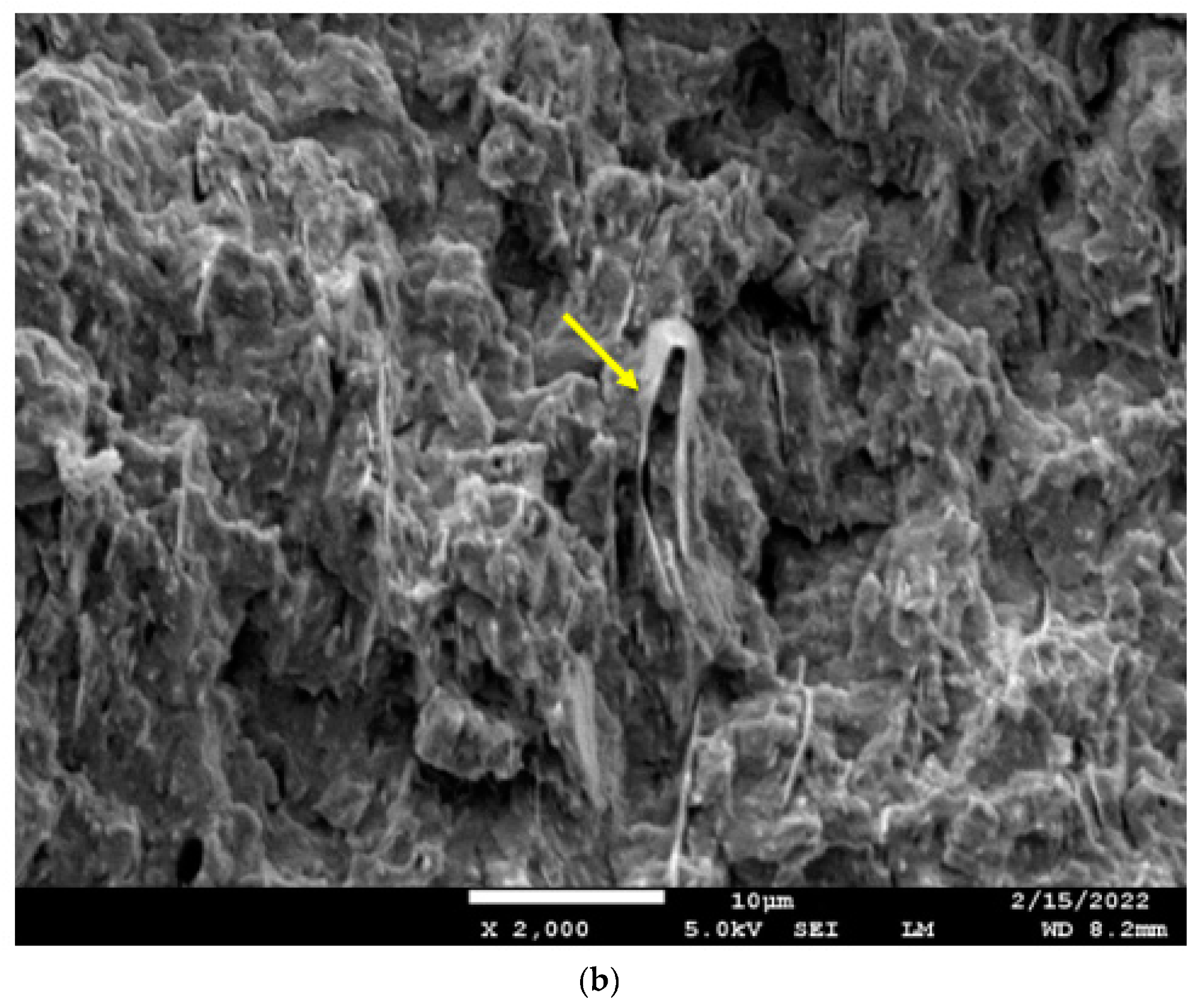
(a) SEM image of the cryo-fracture surface of a bar of the 60/40 PBT/PET blend with 10 vol.% Al flakes. The platelets are seen edgewise. The rectangle in the left corner is the cross-section of the bar (not to scale) and is placed to visualise the platelet orientation relative to the bar. The arrow shows polymer coating on a platelet. Dotted arrow shows a folded platelet. The white size bar = 10 μm. (b) SEM image of the cryo-fracture surface of a bar of the 60/40 PBT/PET blend with 25 vol.% of Al nano platelets. The platelets are seen edgewise. The arrow shows a folded platelet with polymer coating. The white size bar = 10 μm. Image Credit: Alhamidi, A et al., Polymers
Conclusions
In conclusion, this study demonstrated the development of an electrically conductive composite by using an injection-moldable Al-60/40 PBT/PET polyester composition as the matrix. When heated to 150 °C, the products made from this combination shrank by less than 1%, compared to more than 1% for Al–amorphous PET.
Hence, the authors emphasized that for electrically conductive plastics, the 60/40 PBT/PET matrix is a better and more convenient matrix than Al–amorphous PET. Spherical Al nanoparticles were found to be a better choice than Al platelets for forming the 'segregated network' in 60/40 PBT/PET blends.
They also believe that the composition of Al-PET-PBT can be improved further by reducing the Al volume fraction at which electrical percolation begins from 20–25%.
Disclaimer: The views expressed here are those of the author expressed in their private capacity and do not necessarily represent the views of AZoM.com Limited T/A AZoNetwork the owner and operator of this website. This disclaimer forms part of the Terms and conditions of use of this website.
Source:
Alhamidi, A., Anis, A., Al-Zahrani, S. M., et al. Conductive Plastics from Al Platelets in a PBT-PET Polyester Blend Having Co-Continuous Morphology. Polymers 14(6), 1092 (2022). https://www.mdpi.com/2073-4360/14/6/1092