By Surbhi JainReviewed by Susha Cheriyedath, M.Sc.May 31 2022
In an article recently published in the journal Additive Manufacturing, researchers discussed the utility of greyscale printing and characterization of the binder migration pattern during 3D sand mold printing.
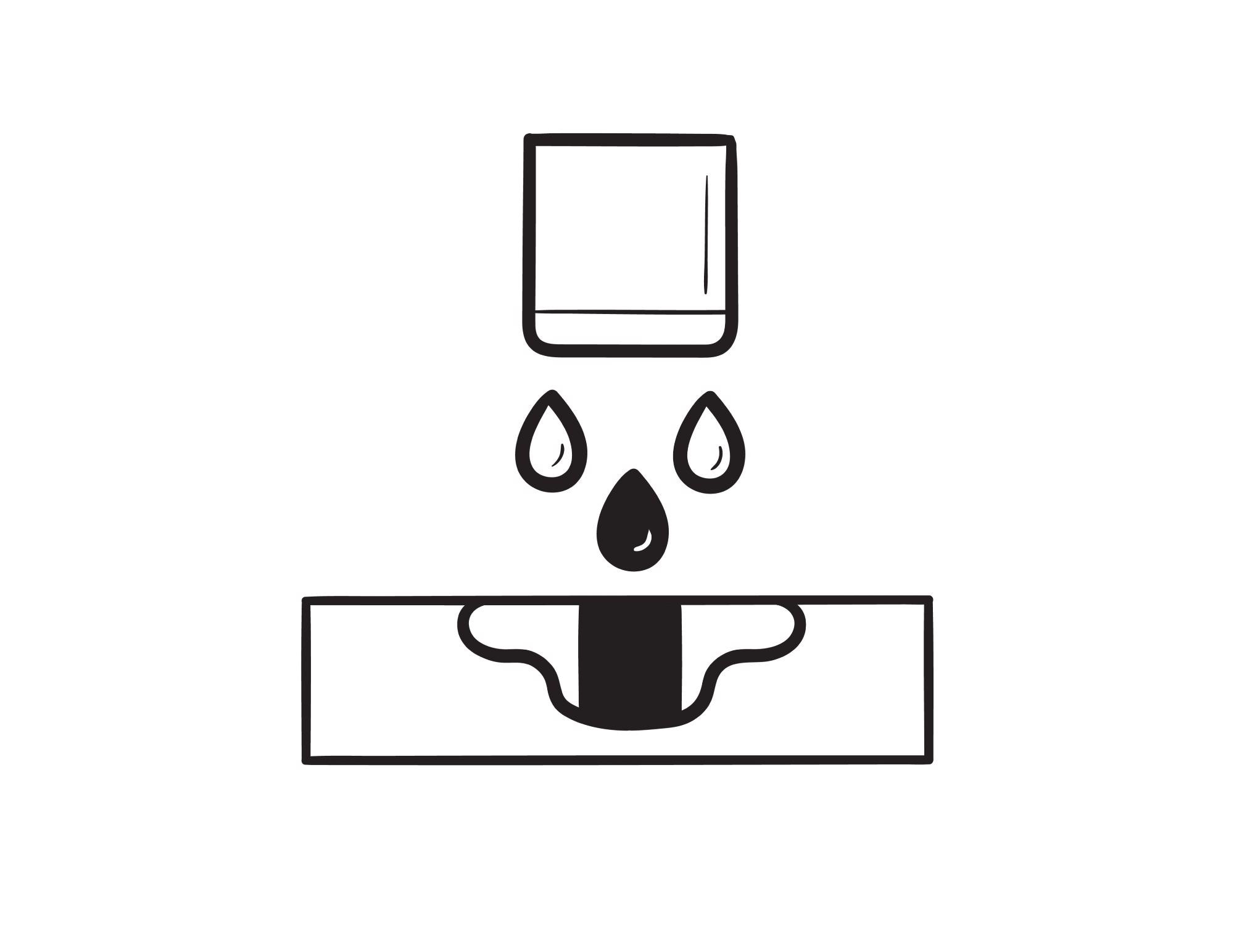
Study: Greyscale printing and characterization of the binder migration pattern during 3D sand mold printing. Image Credit: Visual Generation/Shutterstock.com
Background
The emergence of additive manufacturing (AM) technology has changed the foundry sector in recent decades. Binder jetting, one of the most important AM processes, is presently the most extensively used sand mold technology. The qualities of the resulting molds are influenced by the physical, thermal, and mechanical properties of the binding materials and the powders in binder jetting. Binder jetting sand mold printing, unlike traditional casting, eliminates the action of sandbox rodding.
Binders often permeate to the sand mold bottom during printing, affecting the sand mold's vertical dimension inaccuracy. Previous investigations revealed that the goal of dimension inaccuracy, balancing strength, and formability in the 3D printing of sand molds has yet to be achieved. As a result, establishing excellent sand mold formability, dimensional inaccuracy, and strength through the precise control of droplet volume, or even generating a new type of binder, have become key research objectives in binder jetting.
About the Study
In this study, the authors discussed the utility of greyscale printing in binder jetting. Six sets of samples with varying droplet volumes were created using Furan resin as the liquid binder and silica particles as the sand bed. Afterward, the ensuing migration patterns were evaluated and quantified based on deposited liquid saturation. The migration patterns were compared to the printed samples' strength, dimension inaccuracy, and formability.
The team modified the notion of greyscale inkjet printing to obtain precise control of binder volume in the binder jetting production process. Shades of grey were created in greyscale inkjet printing by adjusting the density of the corresponding black binder droplets in each pixel. Binder volume was used instead of density. The link between saturation and sand shaping was the primary focus. The waveform of the piezoelectric nozzle was controlled on a scale of four distinct droplet volumes using self-built equipment. Each layer was allocated one of four droplet sizes on a scale of one to four.
The researchers performed a one-time printing of sand layers with various particle sizes and binder volumes to see how they affected horizontal dispersion and vertical penetration. After that, samples were printed with various binder volumes and particle sizes ranging from 70 to 200 µ m. Dimension error, strength, and formability of the samples were all assessed and compared.
Observations
The dimension inaccuracy was 0.04 mm in samples employing eight pl for the first ten layers and 12 pl for the last ten layers. Dimension inaccuracy was effectively decreased even with just five layers of 8 pl droplets followed by fifteen layers of 12 pl droplets. Grayscale printing had the lowest 0.7%-dimension inaccuracy. Because of the high droplet volume and strong particle binding force, 17.9 pl droplets performed better than 8.1 pl droplets in forming vertical planes and acute angles. The printed samples had a permeability of 110-145 cc/min. When the droplet volume was 7.8 to 13.6 pl, the dimension error varied the most, and the rate of change reduced from 13.6 to 17.9 pl.
The findings revealed that an increase in the liquid saturation improved strength and formability at the expense of a significant reduction in dimension inaccuracy. It was shown that grey-level printing, which involved controlling the droplet size of the liquid binder individually at each print head, could achieve the necessary dimension inaccuracy, strength, and formability at any precise site by using this quantitative framework. The results demonstrated that the binder volume and particle size had a logarithmic effect on diffusion and penetration. Furthermore, saturation had the greatest impact on dimension inaccuracy in the vertical direction.
The strength of resin-bonded bridges between particles was increased. Furthermore, an increase in the binder's droplet volume improved performance in sharp corners and perpendicular faces.
Conclusions
In conclusion, this study discussed the influence of saturation on the dimension inaccuracy, strength, and formability of sand molds and sand cores. In the X, Y, and Z directions, saturation had varied effects on dimension error. Capillary processes predominantly affected the X and Y directions, whereas gravity and inertia had a higher impact on the Z direction, resulting in more overflow.
Greyscale printing, in comparison to traditional printing at a constant binder volume setting, provided greater flexibility in binder jet AM processes. The findings of this study showed that greyscale printing could significantly enhance dimensional accuracy. It was also shown that greyscale printing can achieve the desired local attributes of sand molds using dynamically changed binder volume in a single print cycle. The authors emphasized that grayscale printing must be put to a more severe test to see if it outperforms standard binder jetting in terms of strength, disintegration, air permeability, and other common sand mold casting qualities.
More from AZoM: Use and Applications of Flame Atomic Absorption Spectroscopy
Disclaimer: The views expressed here are those of the author expressed in their private capacity and do not necessarily represent the views of AZoM.com Limited T/A AZoNetwork the owner and operator of this website. This disclaimer forms part of the Terms and conditions of use of this website.
Source:
Cheng, Y-L., Li, Y-T., Yang, Y-T., et al. Greyscale printing and characterization of the binder migration pattern during 3D sand mold printing. Additive Manufacturing 102929 (2022). https://www.sciencedirect.com/science/article/abs/pii/S2214860422003256