A new paper in the journal Energies has investigated the potential of biogas production in the textiles industries. Scientists from Brazil and Sweden have contributed to the new research.
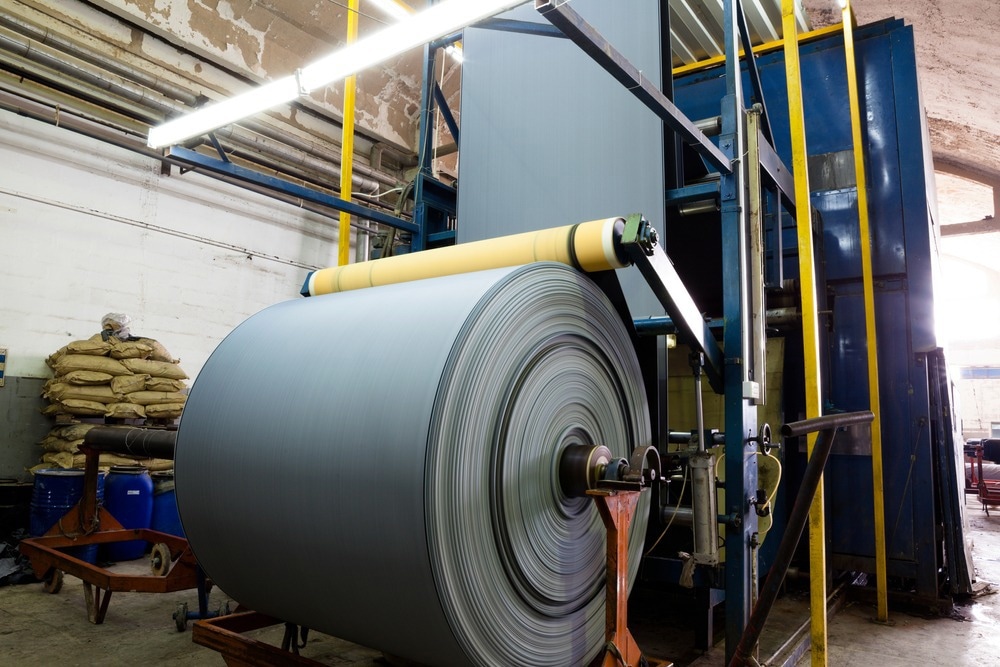
Study: Comprehensive Meta-Analysis of Pathways to Increase Biogas Production in the Textile Industry. Image Credit: Danish Khan/Shutterstock.com
Waste in the Textiles Industry: A Critical Global Environmental Issue
The global textiles industry produces an estimated 92 million tons of waste per year, making it a major polluter. Waste is produced at all stages of the textiles manufacturing process. Fiber production, wastewater, solid by-products, transportation, logistics, retail activities, and consumer waste all contribute to this critical issue.
In the textiles industry, several thousand chemicals, including dyes, heavy metals, solvents, and surfactants, are used to produce clothing and other products. The presence of these chemicals increases the potential toxicity of discharged solid waste and effluents, causing environmental damage, which can prove harmful for protracted periods of time.
A key challenge currently facing the industry at the moment is the trend toward fast fashion, which follows a business model of low cost, rapid manufacturing, and the sale of inexpensive items. This model has significantly increased the waste produced by global clothing and textiles manufacturing. Whilst many challenges face the industry today, there is a growing awareness that the textiles industry must adapt to the environmental challenges of the 21st century.
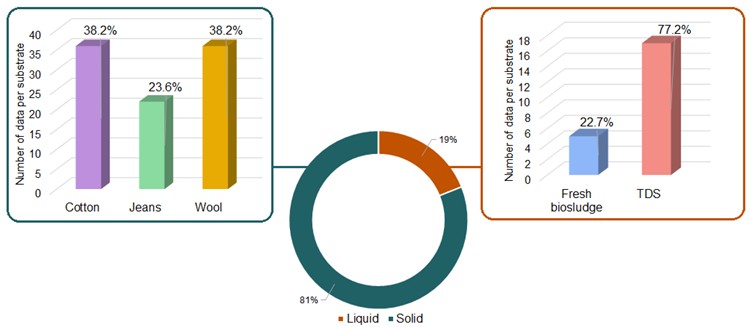
Different sources of textile waste used in AD reported in the literature included in the meta-analysis. TDS = textile dyeing sludge. Image Credit: Anacleto, T.H et al., Energies
Sustainable Manufacturing
Sustainable manufacturing has become a key goal in multiple industries, and has the potential to significantly mitigate the environmental and health impact of the global textiles industry. In recent years, there has been an increasing international drive to reduce the damage caused by several industrial sectors, including COP 21 and the United Nation’s Sustainable Development Goals.
These agreements have been integral to reframing the textiles industry. A major aim of governments and international bodies such as the United Nations and the European Union is to vastly improve the circularity of industry, utilizing waste streams to produce value-added products such as biogas and industrial chemicals.
Biogas Production
Recently, there has been growing interest in the potential to utilize textiles waste to produce biogas, a key technology in the push toward net zero carbon. Biogas has emerged as a promising energy alternative for the industrial and transportation sectors.
Anaerobic digestion has been widely applied in several industries to produce biogas and industrial chemicals as well as proving to be an environmentally sustainable and inexpensive alternative for waste management. Aside from biogas production in the textiles industry, anaerobic digestion has vast benefits for wastewater treatment and reuse.
Key challenges exist with the efficient production of biogas and other important value-added products in the textiles industry using anaerobic digestion on its own, however. Chief amongst these is the presence of chemicals, recalcitrant compounds, and organic pollutants in waste streams. To overcome these challenges, the use of pretreatments has been widely proposed.
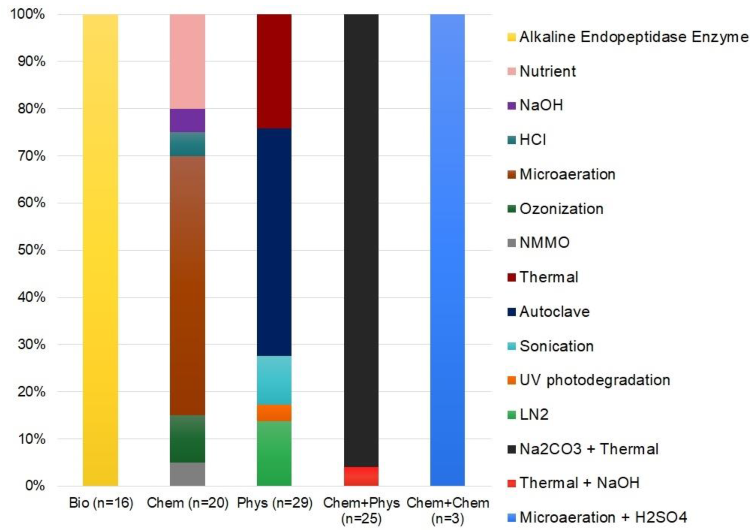
Diversity of methods composing the pretreatment categories applied to improve AD of textile waste reported in articles included in the meta-analysis. Biological: alkaline endopeptidase (n = 16); chemical: nutrient (n = 4), NaOH (n = 1), HCl (n = 1), microaeration (n = 11), ozonization (n = 2), N-methylmorpholine N-oxide (NMMO) (n = 1); physical: thermal (n = 7), autoclave (n = 14), sonication (n = 3), UV photodegradation (n = 1), liquid nitrogen (LN2) (n = 4); chemical + physical: Na2CO3 + thermal (n = 24), thermal + NaOH (n = 1); chemical + chemical: microaeration + H2SO4 (n = 3). Image Credit: Anacleto, T.H et al., Energies
Pretreatments improve the degradability of organic matter, increase the yield of biogas, and enhance the removal of toxic compounds such as dyes. Chemical, biological, and physical pretreatment methods can be applied either in isolation or in combination with each other.
Amongst these methods, biological pretreatments using microorganisms have proven beneficial due to their cost and energy efficiency, along with their green credentials due to the lack of harmful chemicals and toxic by-products.
The Study
The researchers behind the new paper have performed a systematic review and meta-analysis of current literature and data to evaluate the effectiveness of pretreatments for the production of biogas from textile waste. Best choices were identified from available chemical, biological, physical, and hybrid pretreatments. Optimal cost-benefit ratios were proposed by the authors.
Based on their analysis of current peer-reviewed literature, the authors revealed that biological pretreatments promote optimal anaerobic digestion biogas production. An average of 360% methane yield increase is facilitated by enzyme pretreatment compared to physical and chemical processes.
In addition, no additional chemicals are required in biological pretreatments, decreasing the instance of toxic by-products. This has vast benefits for wastewater treatment and water reuse. Effluents from the textiles industry are cleaner, with lower levels of soluble chemicals and solid waste, reducing the environmental and health damage caused by wastewater runoff.

Effect size by natural log response ratio (RR) of methane yield with 95% confidence interval (CI) (p-value = 0.05), comparing the performance of the biological, chemical, physical, chemical + physical, and chemical + chemical pretreatments. Significant code p ≤ 0.05 (*); n = number of effect sizes per treatment type. Image Credit: Anacleto, T.H et al., Energies
Biological pretreatments also possess a favorable cost-benefit ratio, with low capital cost and energy usage achieved using these processes for the treatment of textiles waste before anaerobic digestion and biogas production.
Implementing these processes in the textiles industry provides huge benefits for the reduction of harmful waste products and the utilization of waste streams to produce value-added products such as biogas. This improves the circularity of the global industry, helping it to meet its sustainability goals. However, whilst there are vast benefits, further research into new enzymes and wastewater treatment are required if this solution is to be fully realized in the future.
Further Reading
Anacleto, T.H et al. (2022) Comprehensive Meta-Analysis of Pathways to Increase Biogas Production in the Textile Industry Energies 15(15) 5574 [online] mdpi.com. Available at: https://www.mdpi.com/1996-1073/15/15/5574
Disclaimer: The views expressed here are those of the author expressed in their private capacity and do not necessarily represent the views of AZoM.com Limited T/A AZoNetwork the owner and operator of this website. This disclaimer forms part of the Terms and conditions of use of this website.