Fraunhofer researchers have created a method for extracting lucrative, high-purity ethyl acetate from whey in cooperation with TU Dresden. In place of traditional ethyl acetate derived from fossil-based raw materials, this can be used, for instance, to create environmentally friendly adhesives.
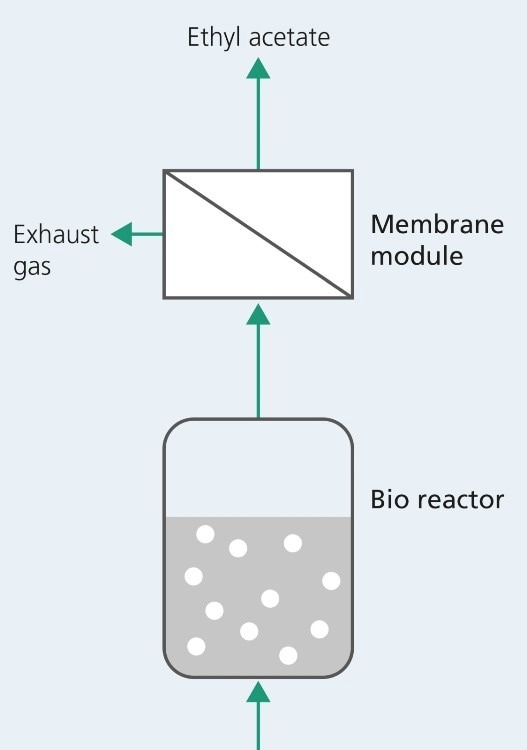
Furthermore, it eliminates the requirement for an expensive molasses disposal process that is necessary after processing whey.
Whey is a by-product of the dairy industry that is produced in vast quantities every day. This equates to 12.6 million tons annually in Germany alone. For instance, 9 Kg of whey is produced for every kilogram of cheese.
A portion of this is processed further, for instance, into mixed drinks or beverages with whey base and fruit additives. The lactose and proteins in whey can also be isolated and used in other products, such as baby food or as raw ingredient in medications. Molasses is left behind after the proteins and lactose have been separated, though.
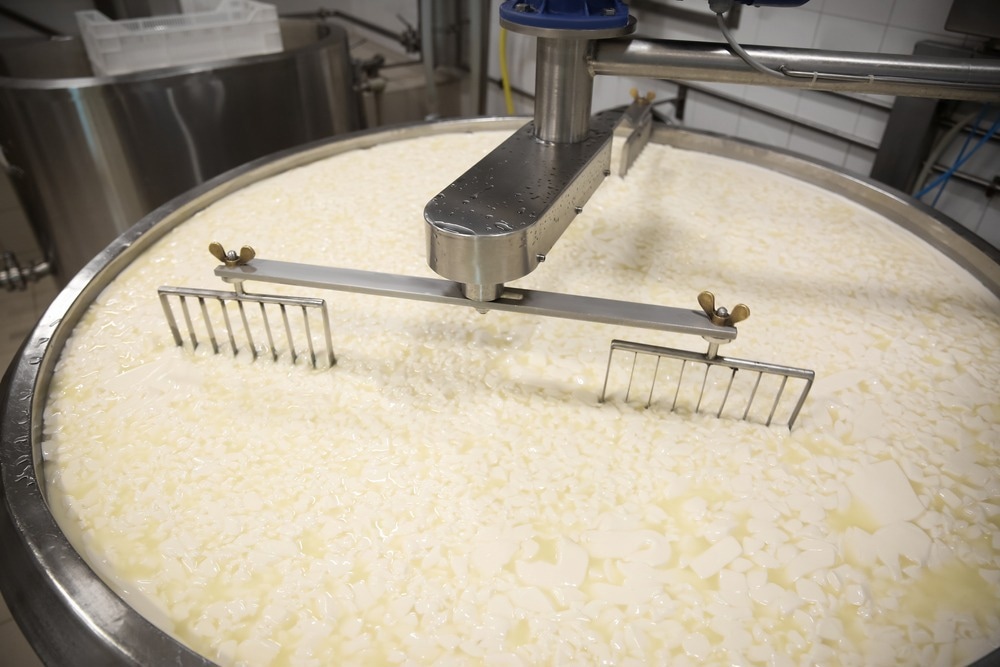
Image Credit: New Africa/Shutterstock.com
Due to this substance’s very high salt concentration, disposal is both difficult and expensive.
Researchers from the TU Dresden and Fraunhofer Institute for Ceramic Technologies and Systems IKTS in Hermsdorf have now created a method to separate the valuable colorless solvent ethyl acetate from the molasses. When creating varnishes, inks for printing, or adhesives, ethyl acetate is frequently utilized. Surfaces can also be cleaned with it.
Up until now, natural gas and petroleum derivatives have been used to make ethyl acetate. On the other hand, ethyl acetate made from whey is clearly superior than solvents that are detrimental to the environment due to its simple microbial degradability and autonomy from changes in the price of crude oil and natural gas.
Another benefit is that the method created by TU Dresden and Fraunhofer IKTS eliminates the need for expensive molasses disposal. With a high purity of 97.5%, the isolated ethyl acetate can be used right away as a raw material with no additional processing required.
Fermenting the Molasses and Separation in the Membrane
The separation procedure is simple in theory. The molasses is first fermented in a bioreactor that has ventilation to promote aerobic conditions. Ethyl acetate is present in the gas-vapor mixture created by the process. Then, using specialized composite membranes, this is separated.
A mixture of gas and water vapor remains as a waste product, which can be released into the environment without issue."
Dr Marcus Weyd, Manager, Membrane Process Technology and Modeling Group
Fraunhofer IKTS researchers contributed their decades of experience in the field of materials, notably membrane technologies, to the creation of the membrane. The composite membrane, which was created especially for the procedure, is made up of a mix of polymers and inorganic zeolite-based particles.
We use liquid silicone rubber as a polymer. This is mixed with zeolite (silicalite-1), applied to a supporting polyester fleece and cured. The membrane is only 10 µm thick in total and the pore size is 0.5 nm."
Dr Thomas Hoyer, Fraunhofer IKTS
Even though the membrane has pores, the actual separation process—which separates the ethyl acetate—does not function like a sieve. Instead, interactions between zeolite and ethyl acetate produce the gas separation effect.
Dr Hoyer added, “The molecules are adsorbed by the zeolite, slide along the pore surfaces, causing them to diffuse through the composite membrane. Creating a certain partial pressure difference is sufficient to initiate the chemical reaction and subsequent diffusion.”
Furthermore, it is not required to “force” the ethyl acetate through the barrier by using a lot of pressure.
Wanted: Possible Uses for Molasses
The TU Dresden came up with the concept while researching potential uses for the molasses and enlisted the assistance of Fraunhofer IKTS. The Fraunhofer team developed and improved the membrane technology, while the TU team dealt with the fermentation process.
Dr Weyd stated, “We have succeeded in producing a highly advanced membrane with extremely small pores through a relatively simple and cost-efficient process.”
It is convenient for industrial businesses since the gas separation process only needs one step and hence only needs a few membrane and control modules. The separation process works autonomously and steadily after the process parameters for fermentation and gas separation are properly established.
Scaling up the membrane modules’ size will be the next task for the researchers to complete before releasing the technology for commercial application. Other uses for the technology exist besides ethyl acetate extraction from molasses.
It can be utilized in any procedure that calls for the separation of gas mixtures or the filtration of volatile substances like hydrocarbons.