By Surbhi JainReviewed by Susha Cheriyedath, M.Sc.Sep 30 2022
In an article recently published in the journal Additive Manufacturing, researchers discussed the utility of automated robotic concrete spraying in the digital manufacturing of ribbed concrete shells.
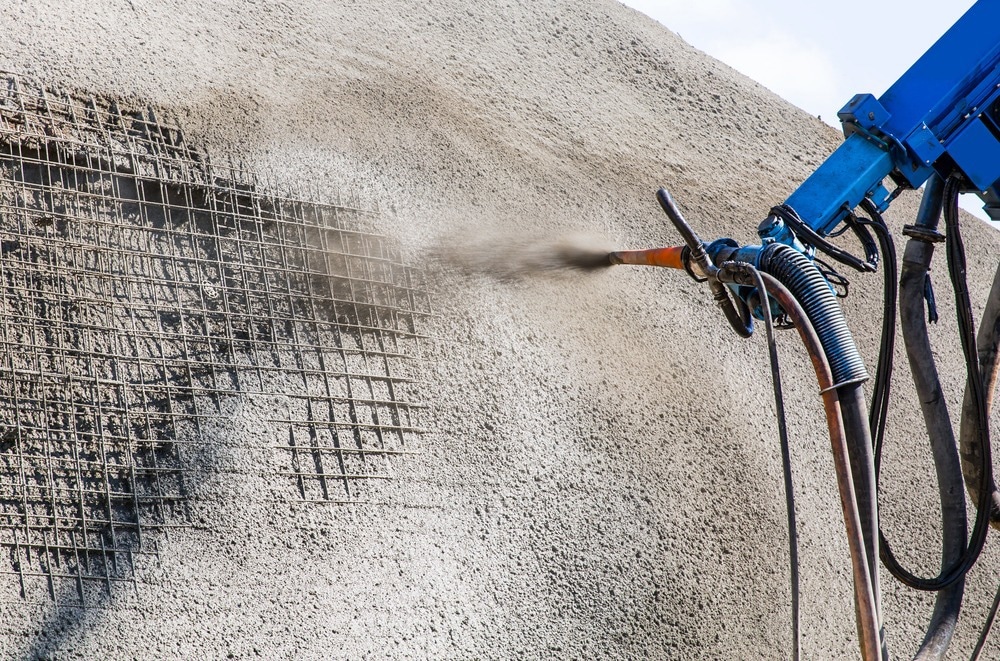
Study: Digital fabrication of ribbed concrete shells using automated robotic concrete spraying. Image Credit: muratart/Shutterstock.com
Background
Concrete stands out among other frequently used construction materials because of its adaptability. Designers can produce highly efficient designs that reduce overall material costs and associated carbon emissions by making use of the material's fluidity. The thin-shell concrete structure is one such design that has been widely employed to span large areas.
Engineers and architects devised techniques to make the formwork manufacturing of concrete shells more straightforward after realizing the difficulties in producing curved concrete shapes. However, the use of thin-shell concrete structures subsequently decreased as labor prices increased globally. Thin-shell concrete structures have recently attracted renewed interest, in part due to the form's potential to save material.
It has taken a lot of effort to assess the possibilities of thin-shell concrete structures. However, the process of building these thin-shell concrete flooring still requires a lot of manual labor. Curved ribbed shells are not compatible with this technique, even though 3D printing of concrete may produce precise geometries. As an alternative to concrete 3D printing, several attempts have been undertaken to combine sprayed concrete with a robotic assembly.
Robotic concrete spraying has largely been used to produce thin architectural features. To assess the possibility of robotic concrete spraying for creating curved load-bearing structural parts, more research is needed. There are various difficulties in creating ribbed concrete shells for structural application. A variable distribution of thickness is desired to optimize material placement. Finally, to upscale the fabrication process for industrial application in a precast manufacturing facility, a high turnover and fast fabrication speed are required.
About the Study
In this study, the authors discussed an innovative fabrication technique known as automated robotic concrete spraying (ARCS), which used glass fiber reinforced concrete (GFRC) to build thin shell components with a range of thicknesses by spraying it onto a curved formwork. To construct the components, the trajectory planning and generation method created and implemented in ARCS was described.
A larger structural floor demonstrator made up of two sets of prototype shells was created, and another one was made out of a single component with deep ribs on a thin shell. Each prototype used two distinct methods to add ribs to the manufactured shells, with the sequencing that was utilized to construct the spray routes for each component. While a pin-bed mold actuating flexible formwork was used in conjunction with the manufacturing process to construct the spraying surface, the trajectory planning approach was flexible enough to work with any formwork.
The team inferred that variable thickness concrete shells with distinct ribs could be produced quickly by spraying GFRC onto a curved base form. The GFRC mix design was introduced initially to better contextualize the spray path generation. The proposed algorithm for ARCS to generate the robotic code for the manufacture of concrete shells with varied thicknesses was described in detail.
The researchers created two sets of prototypes using the ARCS process. The first was a ribbed shell measuring 1.5 m by 1.2 m with highly prominent ribs and the second one was a nine-segment shell that serves as the structural floor of a demonstration measuring 4.5 m by 4.5 m. Each prototype's fabrication process was described in detail, and the thickness distributions that were achieved were examined. The findings showed that ARCS offered a method for accurate and quick manufacturing of concrete shells with variable thickness ribs.
Observations
With a normalized variation with a mean of 0.0224 and a standard deviation of 0.472, the intended thicknesses were frequently met. The manufacturing method successfully produced each segment at the intended thickness, with a normalized variance that had a mean of 0.195 and a standard deviation of 0.202. The segments would not fit with one another because of problems with the timber frame's tolerances, which led to around 10 mm variances at each segment that amounted to an error of about 0.5%. The mix was less dense than typical concrete and had a notional density of 2000 kg/m3 as a result of the absence of coarse aggregates.
The HAL Robotics Framework and the integrated Grasshopper3D plug-in could be used to create robotic code that could precisely deposit GFRC into formwork surfaces. Although only one physical manufacturing setup was employed in conjunction with the design process, it was sufficiently broad to be applied to any robotic assembly system with a concrete sprayer connected. The digital control of the robot could be integrated with the slurry output rate, calibration, and air supply of the concrete sprayer to further increase the repeatability, flexibility, and precision of the fabrication process. In comparison to traditional concrete mixes, the slurry's high cement content resulted in a higher embodied carbon value per weight of the material.
Conclusions
In conclusion, this study described two sets of ARCS-fabricated prototypes. Both prototypes demonstrated the process's adaptability and the increased production efficiency provided by robotic concrete spraying. Geodesics were used as distance functions to create constant distance isolines on a surface in the new trajectory planning and stacking approach proposed in ARCS.
The authors mentioned that it would be advantageous to use a gantry-mounted robotic arm in an off-site manufacturing facility, which would lessen the size and reach restrictions imposed by a six-axis floor-mounted robot. They also stated that ARCS could make it possible to produce expressive and physically effective structural ribbed concrete shells at an industrial pace, regardless of the mix design used.
The team believes that the proposed study would make it easier to create concrete shell structures that are both resource- and carbon-efficient.
More from AZoM: How Far Can Semiconductor Manufacturing Be Automated?
References
Nuh, M., Oval, R., Orr, J., et al. Digital fabrication of ribbed concrete shells using automated robotic concrete spraying. Additive Manufacturing, 103159 (2022). https://www.sciencedirect.com/science/article/pii/S2214860422005486
Disclaimer: The views expressed here are those of the author expressed in their private capacity and do not necessarily represent the views of AZoM.com Limited T/A AZoNetwork the owner and operator of this website. This disclaimer forms part of the Terms and conditions of use of this website.