By Surbhi JainReviewed by Susha Cheriyedath, M.Sc.Oct 5 2022
In an article recently published in the journal Additive Manufacturing, researchers discussed the micro-direct ink writing's complex ink flow mechanisms and how they affect flow rate control.
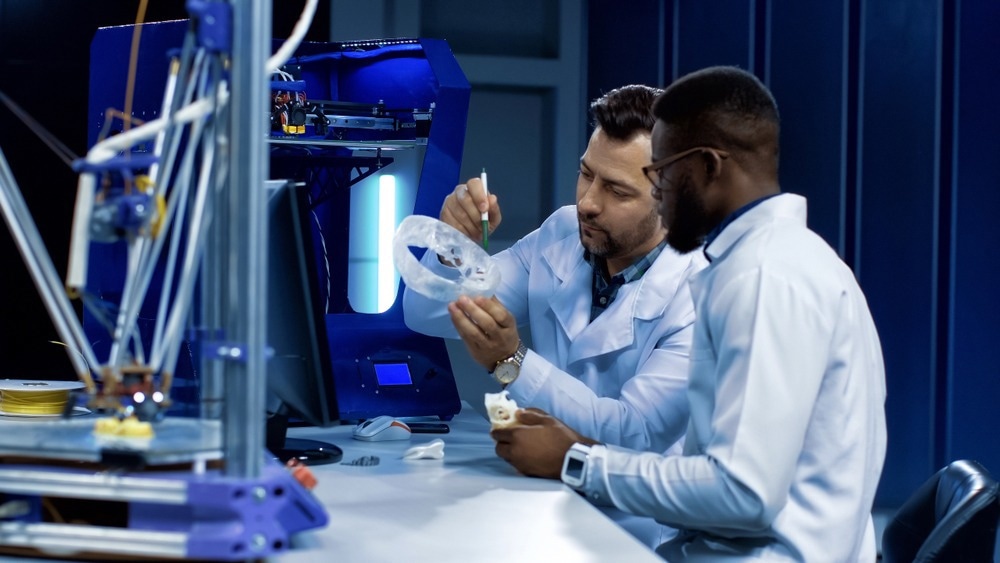
Study: Complex Ink Flow Mechanisms In Micro-Direct-Ink-Writing And Their Implications On Flow Rate Control. Image Credit: Frame Stock Footage/Shutterstock.com
Background
Direct-ink-writing (DIW) is an additive manufacturing technique renowned for its ease of use, versatility, and affordability. Due to these qualities, it has become a fundamental technique for cutting-edge technologies like bioprinting and printed electronics. However, DIW suffers from relatively low printing resolution due to its poor dimensional precision.
While it has been demonstrated that some of these problems are made worse as size scales shrink, others are size-dependent and need further study. The existing state-of-the-art print head implementations frequently utilized for DIW, in addition to having troublesome ink behavior, are not robust enough to handle the level of uncontrollability in volume flow rate connected with extruding these inks.
An in-depth understanding of the ink rheology and capillary flow mechanisms is needed to calculate the correct input pressure associated with the desired volume flow rate. Recently, various initiatives have been made to develop closed-loop volume flow rate control techniques based on these traditional printing schemes. Fundamental knowledge of how these intricate inks react during micro-extrusion is lacking.
The lack of this knowledge has revealed the untapped potential for more sophisticated printing systems as well as the particular conditions that must be met for them to be able to manage the difficulties of direct-ink-writing of complex inks at the micro-scale. Before a viable printing system can be created, the ink rheology and capillary flow mechanics must be better understood.
About the Study
In this study, the authors discussed printing solutions to improve flow rate accuracy in direct-ink-writing at the micro-scale to alleviate this constraint by elucidating intricate ink flow mechanics that make flow rate control challenging. The pressure-flow rate relationships for a water-based sodium carboxymethyl cellulose (NaCMC) solution ink were obtained as a function of printing nozzle diameter in the range from 510 to 100 μm using a DIW system that employed hybrid pressure and velocity-controlled extrusion. These tests showed that the piston velocity-controlled extrusion's transient response dramatically slowed with nozzle diameter reduction.
The team inferred that for pressure-controlled extrusion, the wall slip increased as nozzle size decreased, and below a certain diameter, the constant slip velocity assumption was no longer valid. Temperature-controlled parallel plate rheometry was applied to the inks to contextualize the impact of such behavior on flow rate accuracy, and rheological ink models were created as a result.
It was demonstrated that, particularly for smaller nozzle sizes, the accompanying flow rate calculations were inaccurate because wall-slip consideration was not taken into account. To resolve the accuracy concerns for micro-DIW, an iterative pressure-controlled DIW solution was investigated.
The researchers showed that the proposed strategy significantly outperformed both the traditional pressure control approach and the velocity control approach for nozzle diameters as small as 100 μm in terms of transient response and flow rate accuracy. The size-dependent non-Newtonian ink behavior during micro-extrusion, which restricted the most advanced printing techniques, was explained. The construction of a closed-loop method to obtain flow rate control that could handle the issues related to micro-DIW processes was explored as a final preliminary effort guided by the results.
Observations
The final shear stress for the 32 and 21ga nozzles in the iterative pressure control experiments was 1228 and 1365 Pa, respectively. Around the target flow rate, the input flow rate fluctuated by roughly ±1E-12 m3/s. To manually calculate the average value, the input flow rate was watched for 20 to 60 seconds for the 21ga nozzle and 100 to 200 seconds for the 32ga nozzle. The pressure increased from 10 to 70% towards the projected steady-state pressure in the case of a constant piston velocity of 0.0005 mm/s across all nozzle sizes in 4 minutes. When all nozzle sizes had an exit velocity of 0.5 mm/s, the biggest nozzle exhibited the greatest pressure increase.
The smaller nozzles increased the complexity of DIW and made it more difficult to manage the ink flow rate. Smaller nozzles demonstrated a noticeably slower transient response, especially for the velocity-controlled technique where the flow rate was directly regulated. When small nozzles were included in the pressure-control technique, where the flow rate was indirectly controlled by pressure, flow rate-pressure correlations were substantially more challenging to anticipate.
Furthermore, due to complicated ink yielding processes and compressibility dynamics, the transient behavior of the flow of ink in any method was substantially more complex for tiny nozzles. These findings demonstrated the importance of size scale in DIW processes and showed that towards the lower ends of the
The findings illustrated that the suggested method improved transient performance and accuracy for smaller nozzles at all angles. This gain was attained with minimal pressure controller or iteration algorithm optimization. This showed that the basic strategy of including both pressure input and flow rate in a closed-loop method was a successful one for obtaining high accuracy flow during micro-DIW. The general composition and characteristics of this ink were typical of polymeric bioinks, which were frequently utilized in DIW applications. Numerous additional functional inks had more intricate rheological characteristics and used micro- and nano-scale solid fillers. As a result, when various inks were involved, one would anticipate much more complicated size dependant behavior.
Conclusions
In conclusion, this study presented an extensive analysis of the flow of yield-pseudoplastic inks during the DIW process with different nozzle sizes. Important elements including wall slip during ink extrusion,temperature-dependent ink rheology, and ink compressibility were considered. A unique DIW printhead implementation that allowed for the simultaneous monitoring of ink flow rate and pressure was introduced. The final printed dimensions and their accuracy were influenced by the evolution of the shape of deposited ink filament under the impact of ink rheology, ink-surface, ink-nozzle interactions, and drying or thermal-based shrinkage effects.
The authors emphasized that although flow rate accuracy is fundamental to the total DIW process accuracy, it is not the only element affecting it. They mentioned that more sophisticated controller designs could further enhance the transient response, allowing the flow rate to settle more quickly between iterations.
More from AZoM: How Far Can Semiconductor Manufacturing Be Automated?
References
Estelle, K. T., Gozen, B. A., Complex Ink Flow Mechanisms In Micro-Direct-Ink-Writing And Their Implications On Flow Rate Control. Additive Manufacturing, 103183 (2022). https://www.sciencedirect.com/science/article/abs/pii/S2214860422005723.
Disclaimer: The views expressed here are those of the author expressed in their private capacity and do not necessarily represent the views of AZoM.com Limited T/A AZoNetwork the owner and operator of this website. This disclaimer forms part of the Terms and conditions of use of this website.