Rice University researchers have discovered a way to employ 3D printing to create sustainable wood structures, providing a more environmentally friendly option to conventional manufacturing processes.
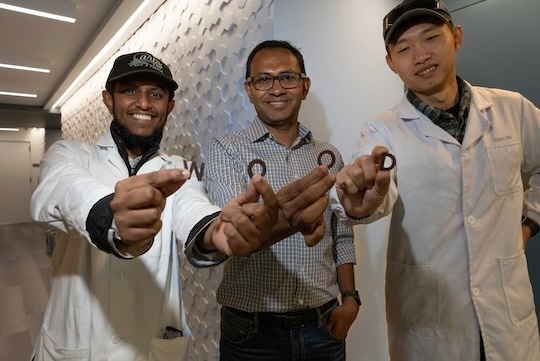
Muhammad Rahman (center), an assistant research professor of materials science and nano engineering at Rice and lab. Image Credit: Gustavo Raskosky/Rice University.
Historically, inefficient practices created during shaping procedures have marred wood, increasing expenses and negatively impacting the environment.
Now, materials science and nanoengineering researchers at Rice have developed an additive-free, water-based ink made of lignin and cellulose, the fundamental building blocks of wood.
Using lignin and cellulose, the basic components of wood, Rice University materials science and nanoengineering researchers have created a water-based ink that does not need any additives. Using a 3D printing method called direct ink writing; the ink can be utilized to create architecturally intricate wood structures.
The study was recently published in the journal Science Advances.
The ability to create a wood structure directly from its own natural components sets the stage for a more eco-friendly and innovative future. It heralds a new era of sustainable 3D-printed wood construction.
Muhammad Rahman, Assistant Research Professor, Department of Materials Science and Nano Engineering, Rice University
The ramifications are extensive and can completely transform sectors like furniture and construction.
Unlike previous attempts, this method exclusively uses nanoscale wood components for 3D printing, marking a significant advancement in the field.
Pulickel Ajayan, Benjamin M. and Mary Greenwood Anderson, Professor and Chair, Department of Materials Science and Nano Engineering, Rice University
According to study lead co-authors M.S.H. Thakur and Chen Shi, the university’s research centered on optimizing the composition of the ink by varying the ratio of lignin, cellulose nanofibers, and nanocrystals while preserving the natural lignin-cellulose balance.
According to Amit Naskar, a senior research and development employee at Oak Ridge National Laboratory and project collaborator, lignin is the least valued product in industries despite being one of the most abundant biopolymers on Earth.
Post-printing, detailed analyses were carried out to compare the 3D-printed wood’s internal and external structures to those of natural \ wood. The resultant product not only had a texture that was highly similar to natural wood, but it also smelled and felt strong like wood.
Furthermore, mechanical tests were conducted to assess the compressive and bending strengths, and the findings showed promise that exceeded that of natural balsa wood.
Rice and the Rice Shared Equipment Authority and the U.S. Department of Energy’s Office of Science, Basic Energy Sciences and Engineering Division under FWPERKCK60 supported the study.
Journal Reference:
Thakur, M. S. H., et al., (2024) Three-dimensional printing of wood. Science Advances. doi.org/10.1126/sciadv.adk3250