A recent article published in Materials explored the effects of temperature on the wear resistance of FeNiCrCoCu high-entropy alloy coatings using molecular dynamic simulations. The study used a Cu matrix as the base material for the FeNiCrCoCu coating.
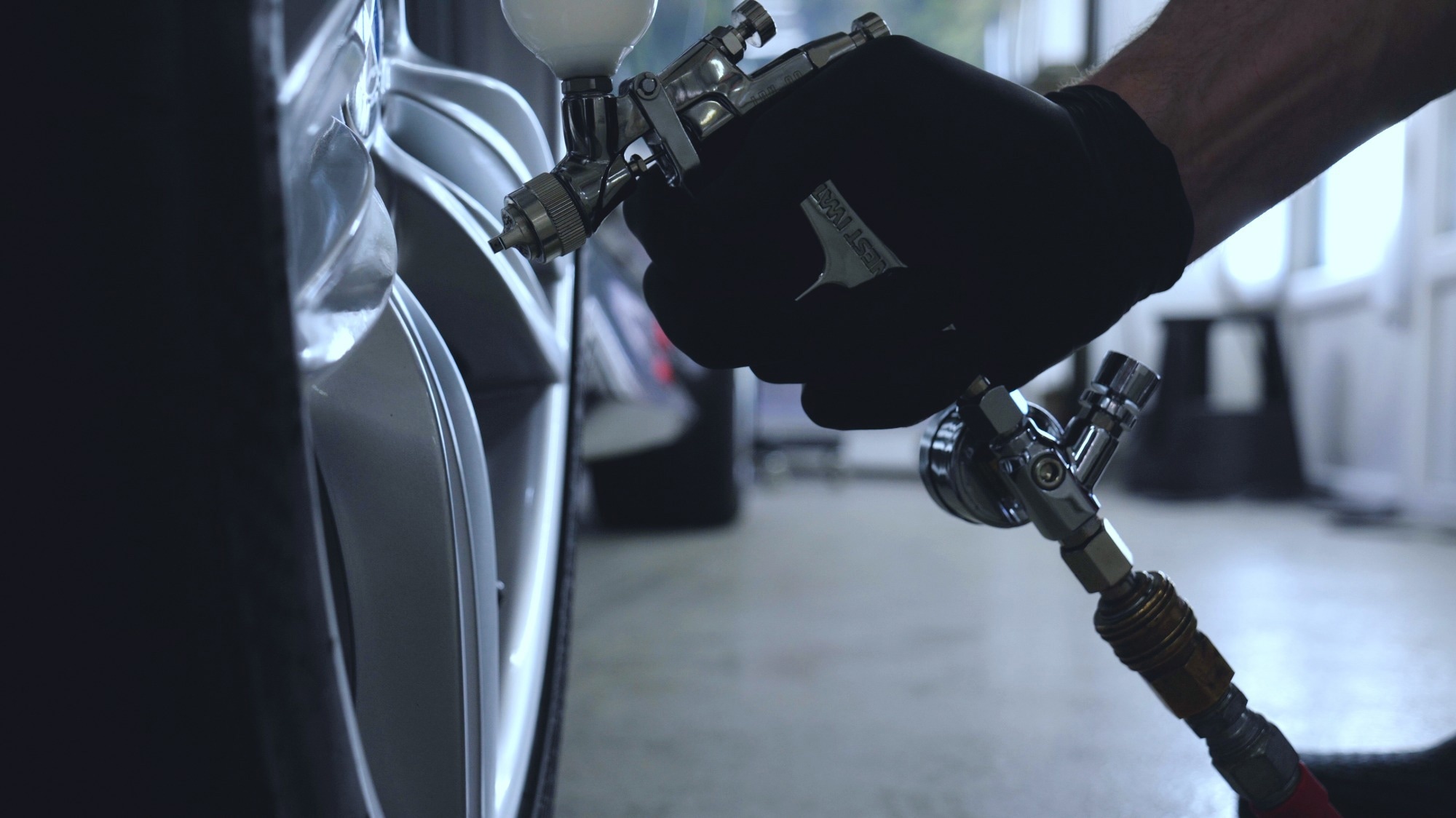
Image Credit: dkHDvideo/Shutterstock.com
Background
High-entropy alloys, characterized by high-entropy, lattice distortion, sluggish diffusion, and the "cocktail" effect due to their multiple elements, are promising for various applications, including marine engineering, automotive, energy development, chemical processing, and biomedicine.
FeNiCrCo-X high-entropy alloys have gained popularity due to their unique physical properties, such as high-temperature stability and strength. Among these, FeNiCrCoCu highentropy alloy is particularly notable for its excellent wear resistance, making it a potential candidate for use as a thin film coating on traditional metal surfaces.
However, the wear resistance of FeNiCrCoCu high-entropy alloys at different temperatures has been scarcely studied. Additionally, microscopic deformation mechanisms are challenging to observe experimentally. This study, therefore, employed molecular dynamics to analyze the wear resistance mechanisms of FeNiCrCoCu high-entropy alloy coatings on a Cu matrix across different temperatures.
Computational Methods
Two simulations were conducted in this study: friction and nanoindentation. A single crystal Cu matrix served as the base material, while a 21 Å thick FeNiCrCoCu high-entropy alloy was used as the coating. Both materials shared the same lattice structure—face-centered cubic (FCC). Simulations were performed at ambient temperatures of 300 K, 600 K, 900 K, and 1200 K.
For the friction simulation, a Cu matrix of size 72×185.2×52 Å3 was modeled with 62,423 atoms. An initial energy minimization was achieved using the conjugate gradient algorithm, followed by model relaxation with periodic boundary conditions and initialization at 300 K.
The Nosé-Hoover thermostat was then applied, with periodic boundary conditions in the X and Y directions and contractive boundary conditions in the Z direction. The simulation utilized both thermostat and Newtonian layers.
In the nanoindentation simulation, a Cu matrix of size 100×100×55 Å3, containing 47,111 atoms, was modeled. The relaxation process was identical to that of the friction simulation, achieving equilibrium in the Fe, Ni, Cr, Co, and Cu distribution in the coating layer. The Langevin method controlled the coating's temperature.
A virtual indenter was positioned in contact with the top of the simulation model, initially without applied pressure. The indenter was then pressed into the matrix at a speed of 10 m/s for 300 ps, reaching a depth of 30 Å, followed by unloading at the same speed and duration.
Results and Discussion
The simulations conducted at four different temperatures revealed intriguing trends in the behavior of the FeNiCrCoCu coating. The tangential force exhibited a slow increase with rising temperature, varying by only 20 nN between 300 K and 1200 K.
In contrast, the normal force decreased significantly with increasing temperature, varying by 20 nN between 300 K and 900 K and 40 nN between 900 K and 1200 K. The force curve demonstrated that the FeNiCrCoCu high-entropy alloy maintains excellent high-temperature resistance between 300 K and 900 K.
During the friction process, the lattice structure of the alloy changed with temperature. The number of hexagonal close-packed (HCP) atoms increased as friction intensified with rising temperature. Additionally, defect structures corresponding to new stacking faults were observed due to friction.
While the alloy structure remained predominantly stable with an FCC crystal phase at 300 K, a small increase in disordered structures was noted in the coating at 1200 K. Conversely, the lattice structure of the Cu matrix became notably unstable at this higher temperature. The deformation mechanism transitioned from stacking faults to lattice disorder due to lattice softening as temperature increased.
The elastic modulus of the coating increased significantly as the temperature rose from 300 K to 600 K, attributed to a reduction in dislocation density. However, the opposite trend was observed as the temperature increased from 600 K to 1200 K. Furthermore, the hardness of the coating decreased with rising temperature, likely due to enhanced atomic disorder.
The number of dislocations increased with deeper indentation, manifesting as segment dislocations within the Cu matrix at a depth of 30 Å. The rise in temperature further compromised the contact surface as the coating penetrated deeper into the matrix.
Conclusion
This study provided a comprehensive analysis of the wear resistance of FeNiCrCoCu high-entropy alloy coatings using molecular dynamics methods. The research examined changes in lattice structure, dislocation behavior, friction coefficient, and hardness of the coating as influenced by temperature.
However, the study did not address the effects of varying elemental proportions within the FeNiCrCoCu high-entropy alloy on wear resistance. Additionally, the influence of surface roughness on the material’s wear resistance was not explored. The researchers plan to consider these factors in future studies.
Journal Reference
Zhang, X., Yang, Z., Deng, Y. (2024). Molecular Dynamics Study on Wear Resistance of High Entropy Alloy Coatings Considering the Effect of Temperature. Materials. DOI: 10.3390/ma17163911, https://www.mdpi.com/1996-1944/17/16/3911
Disclaimer: The views expressed here are those of the author expressed in their private capacity and do not necessarily represent the views of AZoM.com Limited T/A AZoNetwork the owner and operator of this website. This disclaimer forms part of the Terms and conditions of use of this website.