Introduction
Solid Oxide Fuel Cells (SOFC) have been of interest in research and development for an alternative power generator. Electricity is generated via electro-chemical reactions using hydrogen-based gas and oxygen as a fuel and oxidant, respectively. A planar design SOFC is advantageous as the power density produced is greater than that of a tubular design [1]. Nevertheless, sealing in a planar design requires all the desired properties i.e. good gas tightness, good adhesion, chemical and thermal compatibilities with other components and electrical insulation [2]. Under simulated SOFC stack condition, the electrical properties and corrosion behaviors are different in dual atmospheres [3]. The formation of highly conductive oxide products near the cathode side significantly lead to bridging formation between two sides of interconnectors. “Chemically Exfoliated Vermiculite” has been successfully used at high temperature up to 970°C [4] but this seal must be used under compression which is not appropriate to the planar design. A multi-phase composite of mica hybrid seal also requires a compressive load to maintain gas-tightness [5]. A borosilicate glass is widely used as a seal in an SOFC test station. The softening temperature is close to the operating temperature of SOFCs therefore the gas sealing property is relatively good [6]. Nonetheless, boron oxide vapor is produced in both oxidizing and reducing atmospheres [7] and the glass reacts with yttria-stabilized zirconia (YSZ) pellets after 200 hours at 800-1000°C [6]. Nevertheless, solubility of Cr2O3 from the stainless steel interconnects or in silicate glasses results in good adhesion to the steel surface [8]. However, the adhesion varies with the ratio of BaO, CaO and SiO2 in the compositions.
In our research work, we have concentrated on the study of some ceramic adhesives not being examined by Boersma et al. [9]. Several compositions of ceramic-glass composites have been studied in chemical and thermal compatibilities. The result is promising for use in SOFC application.
Experimental Procedure
Ceramic Adhesive Investigation
X-ray diffraction (XRD) patterns of all the as- received ceramic adhesives supplied by Aremco Products, Inc., USA, were investigated using JEOL JDX-3530 theta-2theta X-Ray diffractometer.
Ceramic Adhesive Preparation
The ceramic adhesive supplied by Aremco Products, Inc, denoted as 569 (Al2O3a), 586 (ZrO2/MgO) and 575 (Al2O3b), was applied on 430 stainless steel pieces of size 10 mm x 10 mm. Each set of 200 µm thick adhesive sandwiched in between stainless steel, was cured at 94°C for 2 hours and then soaked at 800°C for 2 hours using 3°C per minute heating and cooling rate. The adhesion between the ceramic adhesive and the stainless steel was determined after the heating cycle. The surface morphology was investigated using a scanning electron microscope (SEM: JEOL JSM 5410). The same types of ceramic adhesive as with stainless steel preparation were used but sandwiched in between pellets of YSZ (8 mol% yttria stabilized zirconia, Daiichi Kigenso Kagaku-Kogyo Co.,Ltd, Japan) pressed into pellets of diameter 13 mm, sintered at 1550°C for 2 hours at 5°C per minute heating and cooling rate.
Glass Ceramic Composite Preparation
Various ratios between pyrex glass (60-80 wt%) and YSZ (20-40 wt/%) powder denoted no. 1 to no. 4 in Table 3 (Results and Discussion) were mixed in a pestle and mortar and applied between YSZ pellets prepared in the same procedure as with the ceramic adhesive.
Chemical Compatibility
Each ceramic adhesive was mixed with YSZ and 430 stainless steel powder and pressed into pellet. The pressed pellets were heated at 1000°C for 10 hours in air and another set in 7% H2 in Ar. The phases of each component before heating and of the pellets after heating were determined using an XRD. The same procedure was carried out using glass-ceramic composites instead of ceramic adhesive for the chemical compatibility test.
Thermal Compatibility
The samples of glass-ceramic composite was pressed and fired at 800°C for 10 hours and then ground to a size of 5x5x8 mm for the coefficient of thermal expansion measurement using a dilatometer (Netzsch, Germany, DIL 402 CD). The measurement was taken between 200-1000°C with the heating and cooling rate of 3°C/min using an alumina rod as a reference.
Leakage Rate Measurement
The leakage rate measurement setup was constructed according to ASTM F 37-89 (method for sealability of gasket materials) as shown in Figure 1.
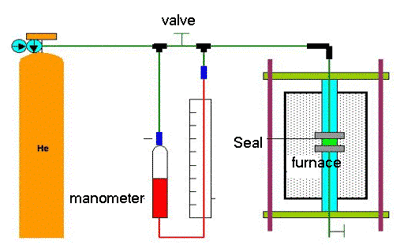
Figure 1. Leakage rate measurement setup.
Selected ceramic adhesives were applied on the ferritic stainless steel flanges in the shape of a flat ring (28 mm outer diameter, 14 mm inner diameter). The specimens were cured as mentioned earlier and heated to 800°C. He gas was used to fill the whole pipeline system. After the pipeline was filled with He, the valve was switched off to allow the gas to pass into the manometer for measurement of leakage.
Various ratios between Pyrex glass and YSZ powder were mixed in an pestle and mortar and applied between ferritic stainless steel flanges in the same size as with the ceramic adhesive. The same procedure as with the ceramic adhesives was followed.
Results and Discussion
Ceramic Adhesive
The phase contents in the ceramic adhesives denoted as 569, 586 and 575 are shown in Figure 2 (a), (b) and (c), respectively. From the XRD patterns, it is seen that there are no other impurities phases present at least above 5% which is the detection limit of the XRD method used here.
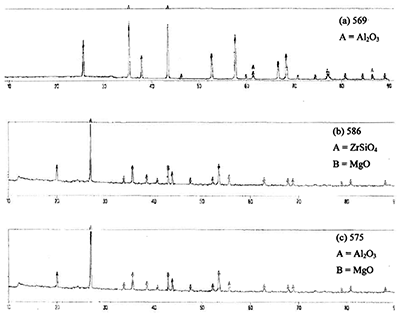
* Coefficient of Thermal Expansion data from Aremco Products, Inc.
Figure 2. XRD patterns of ceramic adhesives before heat treatment for (a), (b) and (c).
From the adhesion test between several ceramic adhesives with stainless steel and YSZ pellets at 800°C, the results are summarized in Table 1.
Table 1. Adhesion and leakage rate measurement between ceramic adhesive with stainless steel and YSZ.
|
|
|
|
|
ZrO2 a |
7.4 |
poor |
- |
- |
Al2O3 a |
7.6 |
good |
good |
0.5089 |
MgO a |
12.6 |
good |
- |
- |
Al2O3b |
7.7 |
good |
good |
0.3582 |
ZrO2/MgO |
4.9 |
good |
good |
0.3482 |
MgO b |
10.8 |
poor |
- |
- |
ZrO2 b |
7.2 |
poor |
- |
- |
Mica |
9.0 |
poor |
- |
- |
The compatible coefficient of thermal expansion (CTE) between ceramic adhesives and other materials does not suggest a good adhesion. The compatible coefficients of thermal expansion of MgOb is 10.8 K-1 compared with that of ferritic stainless steel of 10.5 K-1. MgOb compound showed poor adhesion with ferritic stainless steel although they have close coefficient of thermal expansion. The results from Table 1 indicate that the ceramic adhesives Al2O3a, MgOa, Al2O3b, and ZrO2/MgO adhered well with stainless steel therefore they were tested further with YSZ. The compound of MgOa was not further tested with YSZ as scattered pores were shown in the microstructure. The three adhesive compounds except MgOa adhered well with stainless steel after heating and cooling. The SEM micrographs in Figsure 3 a, b, c revealed the surface of stainless steel and the ceramic adhesive Al2O3a, Al2O3b, and ZrO2/MgO after disassembly with force as a result of good adhesion. They leave a rather clean surface on stainless steel. On the contrary, Figure 3 d showed the surface of MgOb with some parts chipped off during disassembling.
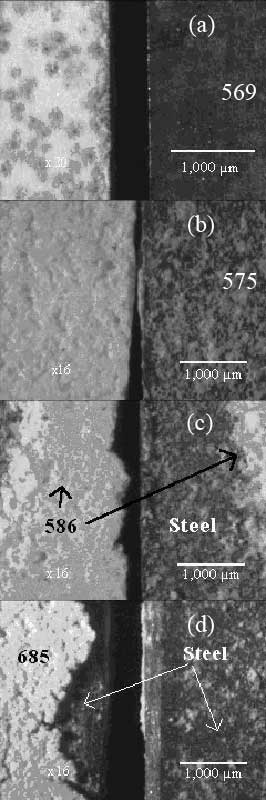
Figure 3. SEM surface morphology of (a) Al2O3a (569), (b) Al2O3b (575), (c) ZrO2/MgO (586) and (d) poor adhesion of MgOb (685) base ceramic adhesive (left) with stainless steel (right).
The microstructures from Figures 3 (a), (b), and (c) showed some rough surface which may affect the gas tightness property. The leakage rates of these three adhesive compounds are in the same order of magnitude from 0.34-0.51 cm3/min cm. All the selected adhesives were chemically stable in contact YSZ electrolyte. The ZrO2/MgO base compound with the lowest leakage rate was also the most chemically compatible with SOFC’s interconnector (stainless steel 430) and YSZ in both oxidizing and reducing atmospheres as shown in Table 2. All three compounds are chemically inert without any reaction products in all tested conditions. The Al2O3 compounds only showed (Fe0.6Cr0.4)2O3 in air and Fe in reducing atmosphere. Further investigations such as ICP or AA must be used to analyze the trace elements of chemical composition of all the adhesive compounds, stainless steel and attached components from all the measurements. From the leakage rate measurement and chemical compatibility, the ZrO2/MgO base adhesive compound is the most preferable.
Table 2. Phases present from XRD patterns of ceramic adhesives chemical compatibility test with YSZ and stainless steel.
|
|
|
|
|
|
|
569 Al2O3 a) |
YSZ, Al2O3 |
YSZ, Al2O3 |
Al2O3 |
Fe, Al2O3 |
575 Al2O3 b) |
YSZ, Al2O3 |
YSZ, Al2O3 |
Al2O3, (Fe0.6Cr0.4)2O3 |
Al2O3 |
586 ZrO2/MgO |
ZrSiO4, YSZ |
ZrSiO4, YSZ |
ZrSiO4 |
ZrSiO4 |
Glass Ceramic Composite
Pyrex glass and YSZ powder were mixed together in different ratios. The details are listed with the leakage rate measurement in Table 3. All the composites from each ratio adhere well with both stainless steel and YSZ pellet.
Table 3. Adhesion and leakage rate with glass-ceramic composite.
|
|
|
|
|
|
1 |
80 |
20 |
good |
good |
2.41 x 10-4 |
2 |
75 |
25 |
good |
good |
5.21 x 10-4 |
3 |
70 |
30 |
good |
good |
3.31 x 10-3 |
4 |
60 |
40 |
good |
good |
0.4411 |
In general, the leakage rate of the glass-ceramic composite is much lower than those of the ceramic adhesive compounds due to the wettability of Pyrex glass. The composite no. 1 exhibited the lowest leakage rate, even lower than the value from literature of 3.6x10-4 cm3/min cm under the same load [10]. Although the composite no. 4 has the most compatible thermal expansion with YSZ pellet and stainless steel, the leakage rate seemed to be the highest, in the same order as the leakage rate from ceramic adhesive compounds. The ratio of composition can be further examined as the softening process, phase separation and crystallization were controlled by varying the ratios of B2O3/SiO2 [11].
The surface morphology of the composite no. 1 on stainless steel and YSZ pellet were similar to Figure 2(a). Figure 4 (a) showed a good wettability of this compound on YSZ which is related to good adhesion. Figure 4 (b) also showed smooth surface similar to Figsure 2 (a) and (b). Table 4 lists the XRD results from the chemical compatibilities test between the composite no. 1 with YSZ and 430 stainless steel.
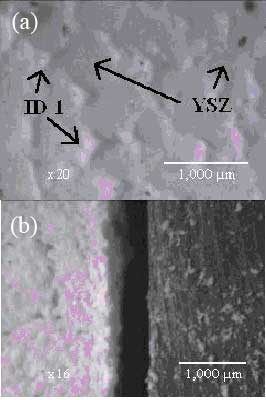
Figure 4. SEM surface morphology of the composite no. 1 on YSZ pellet (a) and on stainless steel (b).
Table 4. The chemical compatibilities test between the composite no. 1 with YSZ and 430 stainless steel.
|
|
Air |
H2 7% in Ar |
Air |
H2 7% in Ar |
YSZ, SiO2, ZrSiO4 |
YSZ |
YSZ, ZrSiO4 |
SiO2, ZrSiO4 , ZrO2 |
The major compound from the chemical compatibilities result was ZrSiO4 which occurred in nearly every condition after heat treatment for 10 hours at 1000°C except in reducing atmosphere with YSZ contact. In contact with stainless steel, Al3.21Si0.47 was present with 7% H2 in Ar. Eichler et al reported that phases of barium disilicate (BaSi2O5) and celsian (BaAl2Si2O8) were present after 2000 hours stability test as reaction products between borosilicate glass and ferritic stainless steel [12]. These compounds are mainly from the SiO2 compound in the glass part and added elements in stainless steel. Therefore, the direction is going towards a glass-ceramic composite compound without SiO2 to suppress its reaction with ZrO2 and to have a protective layer on stainless steel surface to prevent species transport.
Conclusions
The ceramic adhesive Al2O3 base showed good chemical and thermal compatibilities with SOFC components but the leakage rate was rather high. The chemical compatibilities were rather good for all the adhesive compounds with YSZ and 430 stainless steel in both oxidizing and reducing atmospheres. The adhesive compounds of ZrO2/MgO and Al2O3b bases showed less leakage in the same range of 0.34-0.35 cm3/min cm. The glass-ceramic composite of 80/20 Pyrex/YSZ ratio leaked the least at 2.41 x 10-4 cm3/min cm and did not show any impurity phases after heat treatment at 1000°C for 10 hours with YSZ and 430 stainless steel in both oxidizing and reducing atmospheres. In comparison, the glass-ceramic composite showed much lower leakage rate after a thermal cycle than the adhesive compounds.
Acknowledgements
The authors would like to thank financial support from the National Metals and Materials Technology Center for research funding and the COE programmed from Nagaoka University of Technology for travel expenses.
References
1. N.Q. Minh and T. Takahashi, “Science and Technology of Ceramic”, Fuel Cells, Elsevier, Netherlands, 1995.
2. B.C.H. Steele, “Materials for Fuel Cells”, in Encyclopedia of Advanced Materials, (eds. D. Bloor, R.J. Brook, M.C. Flemings and S. Mahajan), No. 18616RB007, London, Pergamon Press, 1994.
3. V.A.C. Haanappel, V. Shemet, I.C. Vinke and W.J. Quadakkers, “A novel method to evaluate the suitability of glass sealant-alloy combinations under SOFC stack conditions”, J. Power Sources, 141 (2005) 102 – 107.
4. J.R. Hoyes, “A Commercial Sealing Material Suitable for Solid Oxide Fuel Cell Applications”, in Proceeding of the 6th European Solid Oxide Fuel Cells Forum, Lucerne, Switzerland, 2004, 834 - 839.
5. J.W. Fergus, “Sealants for solid oxide fuel cells”, J. Power Sources, 147 (2005) 46 – 57.
6. L. Kindermann, D. Das, D. Bahadur, R. Weib, H. Nickel and K. Hilpert, “Chemical interactions between La-Sr-Mn-Fe-O-based perovskites and yttria-stabilized zirconia”, J. Am. Ceram. Soc., 80 (1997) 909 - 914.
7. S.P. Simner and J. W. Stevenson, “Compressive mica seals for SOFC applications”, J. Power Sources, 102 (2001) 310 - 316.
8. S.M. Gross, R. Conradt, P. Geasee, V. Shemet, W.J. Quadakkers, J. Remmel and U. Reisgen, “Chemical Interactions between Glass-Ceramic Sealants and High Chromium Containing Steel”, ibid 4, 800 - 809.
1. 9.R. J. Boersma, N. M. Sammes and Y. Zhang, “ Measurement of Properties of Sealant Materials for Solid Oxide Fuel Cell System”, J. Aust. Ceram. Soc., 34 (1998) 242 - 247.
9. Y.S. Chou, J.W. Stevenson and L.A. Chick, “ Ultra-low leak rate of hybrid compressive mica seals for solid oxide fuel cells”, J.Power Sources, 112 (2002) 130-136.
10. R. Zheng, S.R. Wang, H.W. Nie and T.- L. Wen, “ SiO2-CaO-B2O3-Al2O3 ceramic glaze as sealant for planar ITSOFC”, J. Power Sources, 128 (2005) 165 – 172.
11. K. Eichler, M. Kusnecov, K. Jaenicke-Rössler and P. Otschik, “Glass Foils as Sealing Elements in SOFC Stacks”, ibid 4, 792-799.
Contact Details |