In this interview, individuals from H.C Starck Soutions talk about the benefits of H.C. Starck Soutions' spun molybdenum crucibles for growing sapphire crystals for touchscreens.
What are molybdenum crucibles used for?
Crucibles made from molybdenum are primarily used for growing sapphire crystals using the Heat Exchanger Method (HEM) and are commonly produced using spin forming.
Molybdenum and molybdenum alloy crucibles have been used in other sapphire growing methods such as Edge Defined Film Fed Growth (EFG) and are commonly produced by machining from a rolled plate or a pressed and sintered near-net shape input material.
In all of these processes, the crucibles, normally cylindrical in shape, contain or hold the molten alumina during the crystal growing process.
.jpg)
"Molybdenum has excellent thermal conductivity, which combined with its low thermal expansion coefficient, makes the entire crystal growing system very stable."
Why is molybdenum well-suited to these applications?
Molybdenum is well-suited, because its thermal properties match the process requirements extremely well. The high melting temperature and creep resistance of molybdenum are required to survive the harsh environment found in sapphire crystal growing.
Molybdenum has a low thermal expansion coefficient (CTE), which is excellent for the design of the components in the sapphire growing furnace. Molybdenum has excellent thermal conductivity, which combined with its low CTE, makes the entire crystal growing system very stable.
Molybdenum and other refractory metals also do not contaminate the alumina melt, resulting in a higher quality sapphire.
How do the requirements for crucibles change depending on the sapphire crystal growing method used?
The method used does tend to affect the crucible selection. During crystal growth via HEM, the temperature required for melting the alumina crackle is held constant. Because the thermal stress affecting the crucible is low, thin-wall spun molybdenum crucibles can be used.
In other methods such as Kyropoulous, the thermal gradient is quite severe and requires thicker-walled crucibles made from molybdenum or tungsten.
Can you give an introduction to your spinning process for making crucibles?
The core component of H.C. Starck Soutions crucible is our pure molybdenum plate, which is input into the spinning process. We have developed and follow a very strict rolling and post processing procedure to ensure our input material delivers a perfect crucible.
Beyond the input material, the spinning procedure is performed the same way it would be on steel, but the material is heated during the spinning process to improve formability.
After spinning, the crucibles are trimmed as required and cleaned to remove any surface oxidation created during hot forming. Once clean, the crucibles are ready to be loaded into a HEM furnace.
.jpg)
"H.C. Starck Soutions can manufacture a wide-range of diameter, height and thickness crucible sizes to suit our customers' needs."
What are the other main ways to manufacture crucibles, and how does spinning compare to these?
There are other ways to make crucibles, but not large diameter, tall, thin-walled crucibles. Spinning is ideal, because the material yield is high, wall thickness can be precision-controlled, and post processing beyond trimming and cleaning is generally not required. The cycle time to spin a thin-walled crucible is very short and well-suited for high volume production.
For shallow crucibles, deep drawing is sometimes used, but the height of a spun crucible cannot be matched with deep drawing. Pressing, sintering and machining can also be used to make crucibles, but it's not practical to get such a thin-wall using this method. Handling prior to sintering is very difficult and sintering time increases cycle time.
Moreover, slight deformations in sintering can require machining afterwards to finish the part. Although, there are other methods to make crucibles, spin forming remains the most economical.
How was the spinning process developed?
The spinning process for molybdenum is an adaptation of metal spinning for materials like steel. Working with a conventional spinning machine manufacturer, they developed a machine with capabilities for spinning material while being heated.
At the same time, H.C. Starck Soutions' engineers were developing the input material to be used for spinning crucibles. As the process development moved along, the machine and input material were refined until we were able to repeatedly make defect-free crucibles with little down time in the crucible production process.
Can the spinning process be used for other metals, e.g. Tungsten?
Yes, spinning can be used for other materials like tungsten. Just like molybdenum, tungsten needs to be heated to become more ductile and improve formability.
In the case of tungsten, the temperature required for spin forming is higher than that of molybdenum, so the machine and facility need special capabilities to handle the higher temperature.
Regardless of the material used, the quality of the input plate is critical to the spinning success.
What are H.C. Starck Soutions' plans for growth/development in this area in the future?
With the addition of molybdenum spin forming, H.C. Starck Soutions has become a vertically integrated company with the capability to refine molybdenum powder, press and sinter ingots, roll input material for spinning, spinning to form, trim, and clean molybdenum and molybdenum alloy crucibles.
H.C. Starck Soutions can manufacture a wide-range of diameter, height and thickness crucible sizes to suit our customers' needs.
Beyond molybdenum crucibles, we are a forward thinking company that listens to our customers' and their complex requirements in order to help them develop next generation materials and products.
About H.C. Starck Soutions
The H.C. Starck Group is a leading global supplier of technology metals and advanced ceramics. The company operates modern manufacturing facilities in Europe, America, and Asia and serves growing industries such as the electronics, chemicals, automotive, medical technology, aerospace, energy technology, and environmental technology industries, as well as engineering companies and tool manufacturers.
On December 31, 2017, the H.C. Starck Group had 2,600 employees in the United States, Canada, Great Britain, Germany, China, Japan, and Thailand.
H.C. Starck’s products are predominantly based on technology metals: Tantalum, Niobium, Tungsten, and Molybdenum.
The Fabricated Products Division converts technology metal powders into customized semi-finished and finished products through pressing, sintering, rolling, melting and thermo-mechanical processing and surface treatment.
The Tungsten Division provides high performance products for the mechanical engineering and tool making, automotive and energy industry, aviation industry, and the chemical industry, for example:
- tungsten carbides for carbide tools and wear parts
- tungsten and cast tungsten carbides for oil and gas drilling
- tungsten metal powders for heavy metal alloys
- tungsten chemicals as precursors for catalysts
The Advanced Ceramic Components (CER) Division manufactures specialized technical ceramic parts and films. CER produces engineering parts such as sealing rings, functional parts including fuel cells for solid oxide fuel cell (SOFC) systems and products for dental applications as well as for armor and wear protection. Furthermore, CER focuses on technological developments to expand the portfolio toward product applications in the semiconductor industry.
In 2018 H.C. Starck sold the division Surface Technology & Ceramic Powders to the Swedish Höganäs Group, effective March 1st and the division Tantalum and Niobium to the JX Nippon Mining & Metals Group, effective July 1st.
The group is led by a two-member Executive Board: Dr. Jens Knöll (Chairman of the Executive Board), Dr. Jan Lösch (Member of the Executive Board).
H.C. Starck was founded in Berlin in 1920. Since 2007, the company is owned by financial investors Advent International and The Carlyle Group.
H.C. Starck is registered in Goslar (Germany) and the Group’s headquarters is located in Munich (Germany).
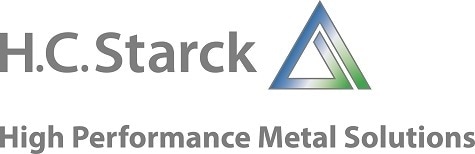
This information has been sourced, reviewed and adapted from materials provided by H.C. Starck Soutions.
For more information on this source, please visit H.C. Starck Solutions.
Disclaimer: The views expressed here are those of the interviewee and do not necessarily represent the views of AZoM.com Limited (T/A) AZoNetwork, the owner and operator of this website. This disclaimer forms part of the Terms and Conditions of use of this website.