Sep 20 2016
The rheological behavior of materials, including powders, is intensely affected by stress and strain. For example, consolidation stresses caused during handling or transport of the powders are normally non-uniformly distributed, leading to inhomogeneous distributions of the agglomeration state and the packing density. Flow behavior is also largely affected when air is trapped in the powder bed during handling. Performing a homogenizing preparation step before carrying out rheological measurements on cohesive powders is vital.
One type of homogenization procedure is to completely fluidize the powder. For bulk solids that are sufficiently fluidizable, the Anton Paar powder cell can be utilized. Fluidization of very fine particles is difficult, as the cohesive interparticle forces of very fine particles tend to dominate over the hydrodynamic forces and body forces. These types of particles are known as “Geldart class C” particles. The Geldart class C powders require an alternative homogenization procedure.
One example of the Geldart class C powders is modified starch; used as an additive in paper coatings, as a stabilizing or thickening agent in food products, as feedstock for fermentation procedures, and as an excipient (inactive component) in pharmaceutical formulations. The size distribution and size of the starch particles is highly influenced by the type of crop the starch was extracted from. The mean particle size varies from 5 µm in the case of rice starch, 20 µm for corn starch, and 50 µm in the case of potato starch. Modified starch is obtained by chemically modifying the starch to enhance particular properties, such as processing behavior, but this modification has an impact on it's rheological properties. Different types of modified starch may exhibit different powder flow behaviors during handling.
This article presents a robust and repeatable technique for homogenizing cohesive powders before carrying out rheological measurements.
Samples
Investigations were carried out on three types of modified starch, named A, B, and C. All of the starches seemed to have similar properties, and there was no information regarding their chemical modification or particle-size distribution.
Test Methodology
Equipment
The MCR 302 rheometer coupled to the ST36-8V-10/PC/WS Warren-Springs (WS) geometry and the powder cell was used to complete all measurements, however any MCR xx2 or xx1 instrument could be used. Figure 1 depicts an example setup of an MCR 302 with the powder cell.
.png)
Figure 1. MCR 302 equipped with the powder cell.
The WS measuring geometry comprises of a stainless-steel paddle wheel with a height of 10 mm, a diameter of 36 mm and eight vanes. In addition, an air-permeable piston prototype was utilized for the compaction step. The equipment is depicted in Figure 2.
.png)
Figure 2. Air-permeable piston prototype (left) and Warren-Springs measuring geometry (right).
QC Methodology for Cohesive Powders
The technique of using the powder cell to homogenize the cohesive powders is based on the research of Geldart and colleagues who used a torsional device (the WS-Bradford Cohesion Tester) to characterize powder cohesion. This approach was modified for use with the powder cell.
As volume measurement is highly inaccurate in granular media, an exact mass of 55 g of the material was introduced into the powder cell to perform all of the tests. Each measurement was carried out with a fresh filling of the cell.
Figure 3 illustrates the measurement procedure. The powder is first vertically compacted by applying a vertical stress (sv) of 9 kPa for 1 minute using an air-permeable piston (Figure 3.1 and 3.2). The air permeability of the piston allows the air trapped within the powder to be uniformly released. If a uniform level surface is not achieved at the end of this step, a rotational stress can be applied to evenly distribute the powder, which results in a powder bed with reproducible mean bulk density and a flat surface.
An insertion (penetration) test is carried out, by penetrating the compacted powder bed using the WS geometry at a zero rotation rate and a constant speed. The magnitude of powder cohesion is determined by measuring the normal force. Previous research has suggested that highly precise results to measure the cohesive strength of powders can be obtained by carrying out these penetration tests.
During the penetration test, the WS geometry is automatically positioned so that the surface of the compacted powder is in contact with the bottom edge of the WS geometry (Figure 3.3). The WS geometry is penetrated into the compacted powder bed at a constant vertical speed of 0.5 mm/s up to 10 mm depth, which is equal to the height of the measuring geometry (Figure 3.4). This yields a curve of the penetration depth versus the normal force.
For comparison, a characteristic parameter distinctive for this penetration curve is used. The penetration work or the energy spent can be calculated from the area under the normal force over the penetration path curve. The penetration work (Wp) can be expressed as:
.jpg)
where p = penetration path, z = vertical coordinate (depth penetrated), and FN = normal force. The integral denoted in the above equation can be evaluated by using the rheometer software.
A shearing step is carried out immediately after the penetration step, where the WS geometry is rotated at a constant speed of 0/03 rpm and the torque is measured (Figure 3.5) Prior to initiating the the shearing step, any residual normal stresses caused during the penetration step are removed by raising the WS geometry by 0.5 mm. For all intents and purposes, the shear measurement is carried out at zero load conditions.
.jpg)
Figure 3. (1) Steps of the measurement, (2) consolidation, (3, 4) penetration, and (5) shearing.
A primary advantage of the above measurement sequence is that it is a “two-in-one” test in which two independent results can be used to compare different types of powders, which is specifically suited for quality control procedures.
Results and Discussion
Figures 4 and 5 illustrate the results for the two starch specimens. The starch depicted by the turquoise line is far less cohesive than the starch depicted by the red line.
.png)
Figure 4. Penetration test on two starches with different cohesiveness.
.png)
Figure 5. Results of the shear test for two starch powders of different cohesiveness.
The normal force fluctuations observed during the penetration tests probably occur because of the interplay of failure of the bulk solid, internal friction, and the wall friction. As it is evident from Figure 4, this behavior is exhibited by both samples. There was a large difference in magnitude of these fluctuations between the starch samples tested. Although the visibility is obscured in extreme cases, such as Sample C, the curves display high reproducibility, and on average the measured penetration work varied by only 1.1%.
Results of the Shear
To produce a granular flow, the dilatancy (the volume expansion) and the cohesive forces caused due to consolidation have to be overcome. This causes the appearance of a torque peak at the beginning of the shearing interval. This is followed by the steady-state flow, indicating that the shear stress and the bulk density in the shear plane remain constant.
To validate the measurement repeatability, two measurement runs carried out for all of the three modified starches (Samples A, B and C) are illustrated in Figures 6 and 7. Here, the difference in normal stress fluctuations is clearly visible (Figure 6). While marked fluctuations are exhibited by Sample C over the entire measurement range, Sample B exhibits slight fluctuations only near the end of the penetration. The penetration work was computed for all of the measurements (Table 1). The penetration work magnitude for Sample C is greater than that for A or B. In addition, the repeatability is exceptional.
.png)
Figure 6. Penetration measurements of three modified starches.
Table 1. Calculated penetration work values.
|
Sample A [J] |
Sample B [J] |
Sample C [J] |
Run 1 |
0.078 |
0.069 |
0.714 |
Run 2 |
0.076 |
0.070 |
0.711 |
The shear measurements illustrated in Figure 7 also exhibited high repeatability. The different starch types were easily distinguishable.
.png)
Figure 7. Shear measurements of three modified starches.
Conclusion
This article presented a robust and repeatable technique for characterizing cohesive powders, such as the Geldart class C powders, using the powder cell. The test comprised of three steps: (1) consolidation of the sample with an air-permeable piston; (2) measurement of the normal force by penetrating the consolidated powder bed with the WS measuring geometry at a constant vertical velocity; (3) measurement of the torque through a shearing step that involves moving the WS measuring geometry at a constant rotational speed. This technique enabled different types of modified starches to be clearly distinguished. The technique also provides an analytical method to characterize most of the cohesive powders.
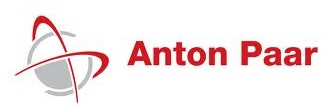
This information has been sourced, reviewed and adapted from materials provided by Anton Paar USA.
For more information on this source, please visit Anton Paar USA.