Informed decisions have to be made when it comes to substituting fluids that have reached the end of their life with the same brand or a different kind of brand. For instance, decisions would need to be made regarding the amount of money and time that would have to be spent to carry out this work. Other factors that need to be considered are: labor including personal protection equipment, process down time including draining, cooling, and filling, the cost of the new fluid, and disposal costs. With most fluids being adequately compatible, a basic drain and fill are all that are required, but just to be sure, users can check with their new fluid supplier.
Cold Spots
In case the system has cold spots, users can consider utilizing a system cleaner. Lines that are fully plugged would need to be substituted because such lines can be unplugged only through water-based cleaners. Non-aqueous cleaners can be used if there is some sort of flow via the affected area. As such, two types of cleaners are available: additive cleaners and cleaners that are designed for faster “off-line” cleaning. Additive cleaners are mixed to an existing fluid while the system continues to function, and as soon as the lines are hot again the system is drained and recharged, while “off-line” cleaners need an extra flushing step for removing the cleaner. However, it should be ensured that the cleaner is compatible with the fluid.
Fluid Removals
Sometimes, drains are situated at all low points of the piping, allowing the fluid to be drained or pumped out easily. If not, users would need to break flanges, remove valves, open pressure taps, and flex hoses and other components from the piping to make sure that fluid is removed completely. Compressed nitrogen can also be used to push the fluid out from one end of an open loop. While this approach is difficult to implement, it is quite effective. Less solids and fluid would be left in the lines by draining the system hot/warm, rather than draining it cold. The heater should be closed down and the pump should be allowed to run continuously until the fluid has cooled down to 150°F and 180°F and then draining the fluid as fast as possible.
Flushing Fluids
Highsolvent-content liquids are often used as flushing fluids and are mainly used to dilute existing fluids that are very thick at ambient temperature to fully drain off from the system. A flushing fluid, unlike a cleaner, is not capable of removing system deposits and further adds two more steps. This is because the flushing fluid has to be removed from the system so as to prevent untimely degradation of the newly replaced heat transfer fluid. New fluid suppliers would be able to tell whether flushing is required or not. It should be noted that new systems do not have to be flushed often before filling. In such systems, the major contaminants are leftovers like shop rags, metal particles, welding slag, and other solids. During initial circulation, these contaminants can be removed using a 60-mesh start-up strainer.
In the case of new piping, the quantity of soluble contaminants like oils, lacquers, and other metal coatings present is relatively small with respect to the system volume. Incomplete flushing of the flushing fluid itself will reduce the life of the heat transfer fluid and this would translate to increased time and disposal costs.
Charging and Initial Run
The main circulating pump should not be used to charge the fluid, as this can break the seals. Instead, a stainless braided Teflon hose can be used to join a small positive- displacement pump to the main pump suction as closely as possible. High point vents and all control and block valves should be opened, but a bucket should be placed beneath the vents to catch the fluid as it runs out, and there should also be an adequate number of workers to track the vents. In case the system lacks a dearator, the warm-up valve to the expansion tank should be kept open and fluid should be added until the expansion tank is approximately 1/2 full. If it is too difficult to measure the expansion tank level, then the overflow from the expansion tank vent should be checked. The main pump discharge block valve should then be closed almost fully, followed by starting the pump and opening the block valve to one-fourth of full flow. If required, more fluid can be added when the pump begins to cavitate or the low-level switch trips. As soon as the fluid is steadily circulating through the entire system, the discharge valve can be opened and fluid can be added as needed. The system is considered to be full when the pump runs steadily with the fully opened block valve. All the high level vents should be checked to ensure that the lines are filled. Fluid should be added to reach the right level in the expansion tank.
Paratherm | Heat Transfer Fluids | Hot-Oil Technology Made Easy
Start-Up
When it converts to steam, 7oz of water will push 55 gallons of potentially hot fluid via the expansion tank vent. Hence, each cold start up for existing or new systems should be approached thinking that water is present somewhere in the system. Although gross amounts of water can be removed by draining the low points on the piping, the only approach to fully remove the water is to flash it off as steam via the expansion-tank vent. To realize this as rapidly as possible, the expansion tank temperature should be kept over 212°F, and steam condensation within the tank should be reduced.
The most effective setup is warm-up or vent lines, which run from the heater outlet to the expansion tank. While dearators can suitably separate air and other non-condensing gases from the fluid, they are not useful for venting gases that condense similar to steam. If users do not know how to boil out their systems, they can contact their fluid or heater manufacturer. Before starting, the following steps should be considered:
- The end of the pipe should be visible if the expansion tank vent discharges into a catch tank. Further, the system catch tank should be kept fully empty.
- The manual valve on the expansion tank vent line should be opened.
- If there is a nitrogen blanket on the tank, the nitrogen inlet pressure control valve should be set as low as possible to render a steady purge via the vent. This approach will prevent fluid oxidation and expedite water removal.
- All control valves should be opened.
- To reduce condensation, welding blankets should be laid on top of the expansion tank.
Finally, the heater should be started and the setpoint should be increased gradually to 220°F. The presence of water in the fluid can be detected when there are popping/crackling noises, pressure fluctuations, pump noise, and/or unexpected level changes in the expansion tank. At this stage, steam will be exiting from the vent. As soon as the steam stops, the outlet temperature should be increased to another 3°F and steam should be allowed to vent. The temperature should be continuously increased by 3°F increments till the temperature of the fluid at the pump suction reaches 220°F and the pressure becomes stable. Next, the warm-up valve should be closed and the heater temperature should be gradually increased to the required operating temperature. The fluid level in the expansion tank should be checked and the vent should be closed if the tank has a nitrogen blanket. Any insulation placed over the expansion tank should be removed, and fluid from the low points in the thermal buffer tank and expansion tank should be drained. Users are done if everything looks good.
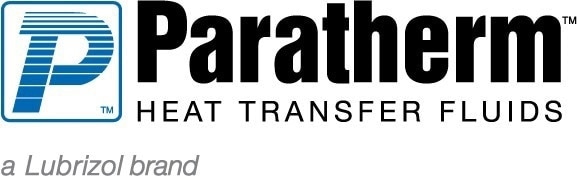
This information has been sourced, reviewed and adapted from materials provided by Paratherm.
For more information on this source, please visit Paratherm.