A best practice before starting up a new thermal oil system is to take a sample from a low point drain into a glass jar. A murky sample indicates the presence of water in the fluid which has to be eliminated by performing a system boilout. A rust colored or clear layer at the bottom of the jar indicates pure water. The time required to thoroughly boilout the system can be reduced by draining the excess water from some of or all the low point drains.
An important point to be noted here is that even if water is not seen in the sample, some amount of residual water might be hidden in the system.
Detecting Water After Startup
Upon conversion to water vapor, the volume of water is expanded to more than 1100 times, making it highly impossible to be ignored in a closed-loop thermal fluid system.
Following are some of the indicators for the presence of water:
- Low pump discharge pressure: In the case of a normal cold start-up, the pump discharge pressure slowly decreases with increase in temperature. In contrast, a sudden drop in the pump pressure, once the heater outlet temperature increases close to 220°F, indicates the presence of water. Therefore, one must cautiously observe any sudden change.
- Pump pressure fluctuations: The presence of water in residual amounts, i.e. <300-400 ppm, is revealed as pump cavitation. At times when the heater outlet temperature of the thermal oil system is more than 212°F, i.e. 100°C, such pressure fluctuations are ignored or misinterpreted. One should take into account the fact that steam from an 8 oz glass of water can displace about 55 gallons of fluid. When the tank is full, the fluid is first forced up into the expansion tank and then out of the vent by the steam bubble. Such incidents can cause severe damage, probably even fire, particularly when an open drum is utilized as the catch tank.
Boilout the System to Remove Water
Water remaining in the thermal oil system is not purged out when the system is operated at low heat until stabilization of the pump pressure. Conversely, the residual water is only relocated to the bottom of the expansion tank. Therefore, the sole method by which water can be entirely removed is by forcing it to flash off as water vapor through the vent of the expansion tank.
It is important to note that in the case of a severely contaminated thermal oil system, it is advisable to completely replace the fluid. Although this process may not avoid the need for a boilout, it can minimize the needed time.
Below are some of the points to be followed for rapidly performing boilout of a system:
- Ensure that the temperature of the tank is maintained to more than 212°F. In case the system does not have a warm-up, i.e. boilout, line, it is advisable to run an insulated line including a valve directly connecting the heater outlet to the top of the expansion tank. To speed up the process, temporary insulation of the tank is also recommended.
- The boilout must be performed continuously until the pump suction temperature reaches more than 220°F, i.e. 105°C. As soon as the system starts to run properly, inspection should be made for presence of water at the bottom of the expansion tank.
Paratherm | Heat Transfer Fluids | Hot-Oil Technology Made Easy
Preventing Contamination by Water
Invariably, water contamination is mostly self- inflicted. Therefore, the following points should be followed for preventing contamination by water.
- A thermal oil system should never be “hydro-tested” with water. Either the system should be pressurized with very dry gas and tested for leaks with soap solution, or the fluid should be pressurized after being charged to test for leaks. Once the system gets heated up, all the seals, flange bolts, and so on must be tightened. Upon replacing a component, care must be taken to ensure that the vendor completely dries it before installation.
- In case the fluid has to be stored outside, the drum should be laid on its side to prevent accumulation of water in the drum head. The fluid should be discarded upon observing any water stains or rust on the drum head.
- Dedicated pump and lines should be used for charging fluid into the system, but these pump and lines should not be used for any other materials. If there is a need to add a fluid directly into the piping of an operating system, then only fluid from sealed drums that are stored properly should be added. If not certain, the fluid should be added to the expansion tank.
- While working in a high humidity area, a nitrogen blanket should be installed on the expansion tank to prevent condensation of water vapor into the fluid when there is a drop in tank temperature below the dew point through the course of a shutdown. As the change in volume of water upon conversion to steam may be up to 1600 times (i.e. a 7oz glass of water can expand to make 85 gallons of steam), it can easily disrupt the operation of a system, hence thorough removal of residual water from any system should be ensured.
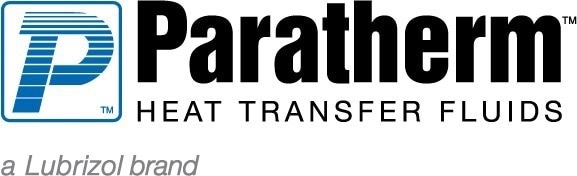
This information has been sourced, reviewed and adapted from materials provided by Paratherm.
For more information on this source, please visit Paratherm.