When people thing of mountaineering, rock climbing and abseiling equipment, the first thing that comes to mind is rope. While this is a fair response, there are many other pieces of equipment that are required for these sports. Some of these pieces of equipment include harnesses, karabiners and anchors, which are reviewed in the following sections. The Harness The next link in the fall arrest system after the rope is the harness. Climbers soon realised that simply tying the rope around their waist was not an ideal way of distributing a fall load to the body. The tendency for the rope to crush the internal organs, constrict the chest and damage the spine was first alleviated by the use of a wide belt made initially from leather, then nylon webbing. However, it wasn't until the 1960s, with the introduction of the Whillans sit harness, that forces generated in a large fall could be distributed comfortably, primarily to the thigh muscles and pelvic girdle. The Relationship between Climber and Harness Despite modem climbing harnesses being padded and comfortable, studies have shown that prolonged free hanging rapidly leads to unconsciousness. Physiological comparative research has shown that hanging in a sit harness can render the victim unconscious within 20 minutes - the simple rope around the waist tie-in method takes less than 30 seconds. Furthermore, hanging with the body vertical poses a far greater risk than hanging with the body horizontal owing to potential compromise of cerebral blood flow. These issues pose a problem when it comes to setting standards for the manufacture and design of harnesses. Design Standards The EN standard has avoided stipulating any regulation concerning load distribution to the body, and has set only requirements for the minimum external load that a harness must withstand without failure or distortion. The static load of 15kN attempts to model the maximum load that may occur with an ample safety margin, remembered the body cannot easily withstand loads in excess of 12kN. The test is carried out using a solid anthropometric mannequin with the load applied at the harness tie-in point. Karabiners and Anchors The final link in the fall arrest system is the hardware that secures climbers to the rock face and protects them from falling. An elaborate range of equipment has evolved to do this job, from pegs hammered into cracks to wedges and camming devices jammed into suitable fissures. To attach such anchors to the climber or their safety rope the quick release link, or ‘karabiner’, has been developed, figure 1. Originally produced from steel, this loop of metal with a sprung gate in the circumference provides an essential rapid link in the safety system. 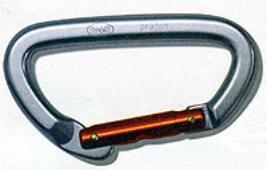 | Figure 1. A modern lightweight age-hardened aluminium alloy karabiner. | Design and Manufacture Today, there are various types of karabiner available, mainly manufactured from aluminium alloys such as Al 7075 T6, although stainless or alloy steels are used in specific applications in which weight is not as important. In its basic form the karabiner is created by bending a circular section bar before the age hardening process. However, more elaborate sections can be formed in the material using hot or cold forging operations. This capability means that further weight reductions can be achieved by forming the metal into stronger cross-sections in critical areas of the karabiner where stresses are highest. Such processes have generally been achieved through trial and error for karabiners, cams, friction brakes and rope grippers, but now finite element techniques are starting to be used in the manufacture of climbing equipment to develop shapes that give optimum strength to weight ratios. Design Standards In order to find the strength requirement for a karabiner, the worst-case scenario of arresting a falling climber must again be looked at. If a karabiner is used to connect the rope to a rock anchor (a ‘running belay’) then during a factor two fall a force nearly twice the impact force generated by the rope will be applied to the link. In reality, the force on one side of the rope is reduced by a third due to friction at the karabiner. An extreme fall with an impact force of 12N will generate a force of up to 20kN on the karabiner. For this reason the minimum breaking force for most karabiners is 20kN, as required by EN12275. It is not just the closed gate strength of a karabiner that is important. Component failures have shown that the open gate strength is just as critical. During a fall, the sprung gate can open accidentally owing to the inertia of the gate during shock loading. It can be snagged open on a rock protrusion or by the rope running rapidly through the karabiner, generating vibrations that cause the gate to flick open. Such incidents have led to a minimum requirement of 7kN open gate strength, although some believe this value should be increased. Materials for Climbing Equipment Mechanical Properties There are a number of important properties that materials used to make climbing hardware must exhibit. Apart from having a good strength to weight ratio, good hardness and fracture toughness characteristics are required. This is as a result of use in an environment in which abrasion and impacts are common and surface defects in highly stressed components are likely to occur. Therefore, materials with good resistance to impacts, as well as high fracture propagation resistance are preferable. For these reasons, developments in high-strength reinforced plastics have not been used in the climbing industry, although there could be advantages in using materials such as reinforced PEEK for specific applications. Corrosion Resistance Corrosion resistance is also an important requirement, particularly for equipment such as pegs or bolts left ‘in-situ’ at popular climbing areas. Rapid environmental degradation in high chloride environments such as sea cliffs can make equipment extremely dangerous, and the failure of such components is relatively common. Summary Great advances have been made in materials and designs over the past 100 years, but the quest for stronger, lighter and innovative designs continues. Advances in computer aided design (CAD) and finite element methods have only recently been applied to mountaineering equipment and provide an exciting opportunity for the designer. Similarly, future advances in polymers and composites will inevitably provide further improvements in both the performances of current products and lead to the development of new equipment for the sport |