The significance of water volume measurement is growing, particularly in large diameters. The challenge related to fresh water or cooling water processes is to form accurate flow recordings or to document and control individual consumptions and withdrawal volumes. However, flow detection particularly in large diameters is very challenging. In such situations, the transit time measurement – because of its high flexibility as a reliable and cost-efficient measurement system – is literally created for permanent flow metering.
.jpg)
Figure 1.
Securing the Water Supply
The requirement for a number of processes is to consume as little fresh water as possible. Water feed and withdrawal quantities also have to be monitored continuously. All these tasks mean that the flow rates have to be permanently examined and verified. Integration into higher systems such as SCADA systems is vital as the systems are usually used within large areas.
Conception and Selecting the Measurement System
So as to guarantee constant flow recording, a measurement system that can establish the medium velocity covering the whole wetted area has to be used. This is particularly vital with varying flow conditions. Most of the measurement systems that are usually used either provide only the spot velocity measurement or the required penetration depth. Quite basically, when it comes to installation, certain measurement systems either entail too many costs or require too many employees. Measuring high medium velocities to many systems is also an equally difficult task.
One cost-efficient method to obtain reliable information on the prevailing flow/discharge is the measurement using the ultrasonic transit time difference principle. Such types of systems are prominent for low maintenance expenses and high operational safety. They can be flexibly used with all the required sizes and media. When compared to other techniques, the measurement system also has the benefit to be largely autonomous of the media’s properties to measure such as fluctuating temperatures, viscosity, or electrical conductivity.
This measurement principle is based on directly defining the transit time of an acoustic signal between two ultrasonic sensors. Such types of sensors are also described as hydro-acoustic converters (A and B in the illustration provided below). Two sonic impulses are transmitted sequentially after each other, followed by measuring the different transit times between the transmitter and receiver. The impulse traveling downstream (t2) reaches the receiver sooner than the impulse heading upstream (t1).
Extremely accurate time measurements and a signal correlation were used to measure the mandatory times. This signal correlation compares the signal transmitted with the signal received by the opposite converter. Thus, the comparison enables the determination of the accurate moments of transmission and reception of the measurement signal. The difference between both determined times is proportional to the average flow velocity within the measurement path.
.jpg)
Figure 2. Schematic illustration of transit time difference principle.
t1 = Impulse time against flow direction
t2 = Impulse time in flow direction
L = Transit time / distance between sensors
Formula: Average transit time difference in a measurement path
The average cross-sectional velocity can be established by using this formula, and thus the flow rate from the measured average velocities within the different layers is related to the velocity coefficients accordingly.
Q = flow rate
k = measurement place-specific correction factor
A = wetted area
vg = average velocity
Formula: General flow calculation
The more measurement paths are used, the more data on the flow profile predominant at the measurement spot can be acquired. Here, the total flow rate is the total of the individual flow rates. Thus, the accuracy of the flow rate determination will be increased using numerous measurement paths. The effects of disturbing flows crossing the main flow direction can be decreased by arranging the sensors of a multi-path measurement crosswise. Cross flows may result in measurement errors. If a multi-path measurement arrangement is used, it may also decrease the length of intake and discharge sections required to calm down the flow profile at the measurement point.
.jpg)
Figure 3. Schematic illustration of multiple measurement paths.
Owing to new Computational Fluid Dynamics (CFD) models and in-depth testing at leading institutes, the behavior and effect of flow profiles downstream of regular disturbances could be examined. Based on the results, flow profiles can be combined downstream of elbows and other disturbances into calculation models directly in the transmitter of the measurement system. Only the distance to the measurement spot and the type of disturbance need to be indicated. From these specifications, the correction factors to be used are automatically established by the measurement. Thus, the result of the flow measurement is extremely accurate and can also be used along with shorter calming and intake sections.
.jpg)
Figure 4. CFD-model of a disturbance (elbow).
The new types of devices from NIVUS GmbH allow for the transit time technique to be used both as a clamp-on system and invasive measurement. Here, the type of sensor used must be selected based on the situation on the measurement place. Using a multi-path system with wetted sensors in a defined arrangement can help accomplish the maximum measurement accuracy. If the sensor cannot be inserted into the process (abrasive, corrosive, or other problematic media), they can be installed on the pipeline from the outer side without disturbing the process (clamp-on measurement system).
Implementing a Measurement
.jpg)
.jpg)
.jpg)
Figure 5. Transmitter and various sensor types.
Tasks of the example shown: long-term recording of flow velocity and flow rate for archiving in a drinking water supply pipeline of a distribution system operator.
Here, accuracy needs are very high as the measurement place has to be used for billing purposes.
A NivuFlow 600 system with invasive sensors by NIVUS GmbH was used. By using tapping nozzles, the sensors were inserted into the pipe. This is how the readings can be provided to the following SCADA system with the preferred level of accuracy through data connection. The broad range of sensors and installation material enables picking up readings at various measurement spots.
A very minimalistic technique can be followed in terms of spare parts stock:
There is no need to stock diameter-specific parts; there is one measurement system for almost all pipe diameters and measurement places.
Summary
Based on the ultrasonic transit time variance principle, flow measurements have undergone a number of years of elaborate testing. They have also been demonstrated to be effective in practical use and stand out for a high level of flexibility and accuracy with regards to applicability in different measurement places. Owing to ease of maintenance and robustness, the ultrasonic transit time principle is suitable for measuring in pipes with smaller diameters (such as cooling water or process water) and also for permanent measurements on challenging measurement sites (such as hydro-electric plants, high process water volumes, large pipe diameters, and varying media).
However, with new-generation devices, the technique’s benefits have been significantly extended. Among other things, accuracies of flow measurements and measurement ranges have been considerably increased.
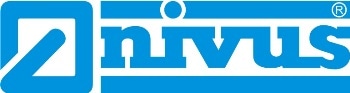
This information has been sourced, reviewed and adapted from materials provided by NIVUS GmbH.
For more information on this source, please visit NIVUS GmbH.