The NanoManipulator system, as this novel scanning probe microscope technology is known, was originally developed at the University of North Carolina, in a collaboration between the Department of Computer Science and the Department of Physics. Together they created a system that provides interactive, precise, and real-time control of an SPM. 3rdTech, a company that develops products and businesses from the university’s research programmes, has now begun to market the unit under the name of the NanoManipulator DP-100. Using this system, a scientist can take control of the SPM probe, move it to precisely the desired location in a sample, and then manipulate atomic-sized structures. These capabilities enable explorations and manipulations that are difficult or impossible with traditional SPM controls. 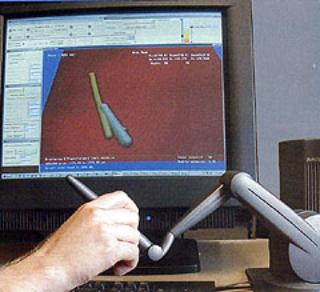 | Figure 1. The NanoManipulator from an operators point of view.. | Advantages of the NanoManipulator The DP-100 provides a force-feedback or ‘haptic’ display, which lets the user ‘feel’ the surface of the sample. When the probe on an SPM is being used for manipulation, it is no longer scanning the surface and the visual display will be slightly mis-registered owing to drift and hysteresis - the lagging of an effect behind the cause of that effect. The haptic display is not subject to these effects and provides accurate location information throughout any manipulations. This makes it possible to select and move single carbon nanotubes. Application of the NanoManipulator at NASA The nondestructive evaluation (NDE) research group at NASA-LARC will be using the NanoManipulator to precisely extract, manipulate and place individual carbon nanotubes. The goal is to create devices employing carbon nanotubes that can be used to test for structural weaknesses in aircraft surfaces. This may seem far fetched, but by 2015 NASA envisages nondestructive evaluation approaches that will require micro-engineering. These inspection systems are intended to be multidisciplinary, using intelligent micro-sized NDE sensors, multiple miniature robotics, and micro-sized repair tools. Autonomous, self-healing smart structures will provide the raw materials to make repairs, and integral materials sensors will deform the structure to redistribute loads while the repair is being made. The inspection data will be analysed by small, near optical-speed, failsafe micro-computational systems that operate at each individual sensor, and at the same time as an integrated computational decision-making network that co-ordinates activities with the entire inspection system. The Future This is still a long way into the future, but the manipulation of atom-sized structures is the starting point, as Buzz Wincheski, Aerospace Technologist at NASA-LARC, points out. ‘Today engineers use optical microscopes to wire electronic circuitry’, he says. ‘We’re using the NanoManipulator to wire circuits ten thousand times smaller.’ |