Through innovations in physics, chemistry, and technology, non-destructive testing (NDT) allows material analysis without damaging samples. This is a relatively recent technique, where previously the idea of being able to accurately analyze the chemical composition of something without removing a piece, or burning it, seemed fanciful.
NDT is now an essential part of everyday materials testing by ensuring that the structures and components we depend on every day are safe and reliable. From pipelines and oil refineries to bridges and automobile parts, being able to accurately test components without detracting from their usefulness provides a huge range of benefits.
Why is NDT Important?
There are a number of analysis techniques that fall under NDT, including those that use electromagnetic radiation, soundwaves or other kinds of signal conversions to evaluate a range of materials. What links them all is the requirement that the material or component being tested is still able to be used once the testing is finished.
This makes these techniques particularly well suited to testing system components in situ after they have been installed or during quality control where you cannot leave marks on what you are testing. NDT is also widely used to measure slight variations in chemical composition. For example, changes in the chemical composition of piping can have dramatic effects on a component’s ability to withstand corrosion, high heat and pressure. Through NDT, it is possible to gain an accurate picture of exactly what elements or compounds a component consists of and how this may change over time.
Hitachi High-Tech offers a number of systems that use X-ray technology for NDT positive material identification (PMI) solutions, in both benchtop and handheld sizes. X-ray fluorescence (XRF) is one such type, where the sample is first excited with an X-ray, and when the electrons in the sample return to a normal state, the excess energy is released in the form of a secondary X-ray. This secondary X-ray is collected by a detector and translated to the elemental composition.
When it comes to non-destructive testing, XRF has a key advantage over the two other primary PMI methodologies: optical emission spectroscopy (OES) and laser-induced breakdown spectroscopy (LIBS). While each of these techniques is extremely accurate and effective, both OES and LIBS leave small, but noticeable, burn marks on the sample once tested.
.png)
Key Applications for XRF NDT
Being able to offer completely non-destructive testing and accurate materials analysis in seconds, XRF is the optimum testing solution for many industrial sectors.
PMI in QA/QC
At every stage of the products path, from manufacturer, supplier to purchasers, the operator must be able to quickly tell if they are getting what they paid for. With XRF testing, it can be quickly established if this is the case, without damaging the material.
PMI in Aerospace and Automotive
The aerospace and automotive industries extensively use aluminum alloys in their components. In-situ testing of the composition of these materials is essential to ensuring safety.
PMI in Petrochem, Oil and Gas, and Power Plants
To keep sites safe and compliant, components must be inspected before, during and after installation to ensure alloy chemistry and grade ID, all without making any structural changes.
Coatings
For areas where it's not practical to use a benchtop instrument, it is possible to use quick, non-destructive XRF for analysis of heavy and bulky items.
Precious Metals
The clue’s in the name. Due to these materials having extremely high value as well as being highly sought after for a range of industrial applications as well as the jewelry industry, it could severely harm their value if the analysis caused the barest mark or imperfection.
Regulatory
XRF is crucial when making sure industrial sites are safe and compliant. If components can be tested in the context in which they are used, operators can develop an up-to-date and comprehensive overview of their sites health and quickly spot and deal with any areas where a problem may arise.
Archaeometry
The last thing that you want to do when trying to accurately determine the chemical composition of archaeological artifacts and materials is cause any harm to them. XRF is used by universities around the world to analyze soil, ceramics, pigments, glass and metals found on archaeological sites.
Choosing the Right Solution
Hitachi High-Tech offers field-leading XRF solutions in both handheld and benchtop options.
The handheld X-MET8000 is easily carried, allowing the user to bring it to the area that needs analyzing, instead of it coming to them. The measurement takes seconds and is output on a screen on then device. The results can also be stored and shared easily with ExTOPE Connect.
The FT range and X-Strata920 microspot XRF coating thickness and materials analyzers work in seconds to produce rapid quality control and validation testing across a range of applications from corrosion and wear resistant coatings to decorative finishes.
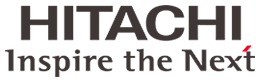
This information has been sourced, reviewed and adapted from materials provided by Hitachi High-Tech Analytical Science.
For more information on this source, please visit Hitachi High-Tech Analytical Science.