BIP® gases are all available with a minimum purity of 6.0, however, is purity everything? Even with a purity of 99.9999%, what exactly is in the other 0.0001%? Despite it only being a tiny amount, what if it was affecting your results and processes? Ultra-high purity gases delivered with BIP® technology from Air Products, guarantee the lowest possible levels of potentially harmful impurities: oxygen (≤ 10 ppb), moisture (≤ 20 ppb) and total hydrocarbons (< 100 ppb), available in the marketplace today.
BIP® Technology
The hidden BIP® technology in each cylinder filters out potentially harmful impurities before the gas leaves the cylinder. Purifiers work more efficiently at higher pressures and so the purifier is incorporated into the cylinder to make removal of gas impurities more effective. Furthermore, because of the innovative valve design, the purifier is sealed from atmospheric contamination.
.jpg)
The slightest contamination could compromise our isotope measurements or damage our equipment. BIP® technology has enabled us to balance our technical demands with cost constraints.
Cyril GIRARDIN, Engineer, INRA
Ultra-High Purity and Ultra-Low Impurities
By filling the BIP® technology cylinders with ultra-high purity gases, this results in gases that are up to 300 times purer than the traditional equivalent cylinders. The only gases available in BIP® technology cylinders are the ultra-high purity gases from Air Products.
BIP® gases have a minimum purity of 6.0, however higher specification grades have been developed for more demanding applications. The table below shows BIP® Plus grade gases, up to 6.8, for specific gases.
For those using GC-ECD (Electron Capture Detector) technique, where low levels of halocarbons are demanded Air Products have developed an ECD grade for both nitrogen and helium gases. (<1 ppb)
* THC = total hydrocarbons as CH4 ** CFC = halocarbons
Saving You Money
In a standard cylinder, typically, as it starts to empty, impurity concentrations increase as a result of the impurities desorbing from the cylinder wall. These can then contaminate the gas stream as the pressure drops further within the cylinder. As a result of this phenomena, users typically switch to a full cylinder once it drops below a certain pressure. This pressure varies from user to user, but is usually found to be in the 30-50 bar range.
With BIP® technology however, this is not a concern as any potential impurities are filtered out by the integrated purifier. This enables the use of gas to a point beyond which cylinders would typically be switched, providing users with potentially up to 20% additional usable gas from each cylinder.
.jpg)
No More Inline Purifiers
Concerns about impurities become a thing of the past when you switch to BIP® gases, as inline purifiers are no longer needed. This eliminates the cost of their initial purchase, time needed to maintain, service each purifier, and their disposal when they become saturated.
Inline purifiers can be helpful; however they can introduce a significant maintenance program to the analytical process.
Extended Column Life for Gas Chromatography Users
The life of your column can be significantly improved by minimizing the impurity content of moisture, hydrocarbons and oxygen in the carrier gas. Column life was extended from 24.5 days to 104 days in a case study with a leading laboratory by changing from standard helium 5.0 to BIP® helium.
The BIP® cylinder technology from Air Products has demonstrated the potential for cost savings up to 70% in the FAME (fatty acid methyl ester) analysis system.
Dr. A Edge, Case study partner, UK
Perfect for Gas Chromatography
Reducing impurities is especially important during gas chromatography. Moisture, oxygen and hydrocarbon content within the carrier gas will affect detection limits as well as causing column bleed and reducing column life. A number of gas chromatography users rely on external inline purifiers to minimize the impurities entering the column.
.jpg)
Inline purifiers can be helpful; however, they introduce a significant maintenance program to the system:
- When purifiers need to be replaced there is the inconvenience of system downtime
- The spent purifier needs to be disposed of in accordance with regulations as it is treated as chemical waste
- The performance of purifiers needs to be tracked to work out how many cylinders of gas can travel through them before they need replacing
BIP® gases offer a simpler solution, whilst saving you money and improving your results. There is no actual requirement for inline purifiers, as the key impurity values (moisture, oxygen and hydrocarbon) from BIP® technology cylinders are extremely low. This removes the financial costs and time associated with in-line purifier use.
GC operators often pay very little attention to the purifiers. It is difficult to check whether they are still working properly, and they are rarely maintained to specification. Gases using BIP® technology decrease the maintenance efforts in a GC laboratory.
Dr. Frank David, Research Institute for Chromatography
BIP® Technology, Award Winning Innovation
When it was launched, BIP® technology received the Queen's Award for Innovation in the UK. Today, there are thousands of loyal BIP® gas customers throughout Europe, including leading manufacturers of analytical equipment and several national laboratories.
What our customers have to say…
Switching over to BIP® cylinder technology is very easy because no adaptation of the current system is required.
Dr Frank David, R&D Manager, Research Institute for Chromatography, Belgium
We dramatically improved the performance of our glove boxes with increased lifetime of the catalyst and reduced regeneration downtime. We wouldn’t recommend anything other than BIP® cylinder technology and its very low levels of H2O and O2 .
Arend Kooi, Sales manager MBRAUN Glove Boxes, BFI OPTILAS B.V., The Netherlands
In our business, we cannot afford any production stops . . . with BIP® technology we now have an insurance on product consistency for each single cylinder we use, from the first to the last molecule.
Willem van Wijk, Production Manager from Alcontrol Laboratories BV Nederland
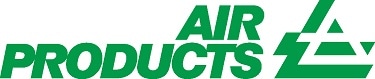
This information has been sourced, reviewed and adapted from materials provided by Air Products.
For more information on this source, please visit Air Products.