The Cryo-Condap® system from Air Products uses liquid nitrogen to condense and freeze Volatile Organic Compound (VOC) vapours. The condensed and frozen particles are then removed from the process, leaving a clean process gas stream which conforms to environmental legislation and can be discharged into the atmosphere.
Not only does this technology reduce VOC emissions to below legislative levels and so enable customers to meet the toughest and most stringent environmental legislations, it can also recover nearly 100% of most solvents and so facilitates reuse in the process.
Furthermore, during the solvent recovery process, the liquid nitrogen is vapourised into gaseous nitrogen which can be reused in other applications including blanketing, purging, product movement and pressurizing. This further reduces operating costs.
Air Products and Herco Kühlteknik have been collaborating for over 35 years. The original Cryo-Condap® system was developed jointly by Air Products and Herco for the application of solvent recovery in video tape production. Since then, Air Products has worked exclusively with Herco to manufacture Cryo-Condap® systems and together they have gained extensive experience in solvent recovery applications covering a wide variety of global industries.
Client
The client is one of the ten largest multinational pharmaceutical companies in the world.
Many pharmaceutical and chemical manufacturers use VOC's or solvents in their production processes. They are often used both as the medium in which reactions take place, as well as in the purification of the final product.
As a result of tightening environmental legislation, this global pharmaceutical company has invested in an emissions control system, a Cryo-Condap® system from Air Products, in order to recover VOCs from process gas streams to near 100% efficiency. The compact system can be easily adapted on site to recover different VOCs at varying freezing temperatures and concentrations, and can recover even the most complex VOCs at low gas flow rates.
VOCs: The Emissions Challenge
Keeping our air safe and clean by reducing pollution is one of the key roles of governments at European and international levels.
Solvents in products such as coatings, inks, and consumer products can emit substances into the air known as VOCs. These VOCs emissions from solvent-based products are regulated to protect air quality and are being driven down as a result of laws and increasingly stringent regulations on environmental protection.
In 1999, the EU Solvent Emissions Directive (1999/13/EC) came into force, aiming to reduce VOCs emissions within certain processes and industrial installations. In 2011-2013 the Commission conducted a review of the EU air policy which resulted in the adoption of the Clean Air Policy Package. The Commission also proposed a Clean Air Programme for Europe and set new objectives for EU air policy for 2020 and 2030. Directive 2016/2284, the new National Emission Ceilings Directive (NEC Directive), on the reduction of national emissions of certain atmospheric pollutants entered into force on 31 December 2016. This Directive sets national reduction commitments for the five pollutants (sulphur dioxide, nitrogen oxides, volatile organic compounds, ammonia and fine particulate matter) responsible for acidification, eutrophication and ground-level ozone pollution which lead to significant negative impacts on human health and the environment. EU and its Member States under the revised Gothenburg Protocol sets more ambitious reduction commitments as from 2030 so as to cut the health impacts of air pollution by half compared with 2005.
The VOC Solvents Emissions Directive requires installations in which such activities are applied to comply either with the emission limit values set out in the Directive or with the requirements of the so-called reduction scheme.
The UK’s Environmental Protection Act set demanding discharge limits for VOCs such as organic solvents and monomers. A typical emission value for trichloroethylene (TCE) a common solvent, is 20 mg/m3, although allowable emissions vary according to the nature and source of each VOC. It is important for manufacturers handling VOCs to seriously consider ways to meet these new and increasingly restrictive limits. Adsorption of active carbon and various methods of incineration are among the traditional technologies used for controlling emissions.
Condensation with liquid nitrogen is the cleanest way to remove VOCs from exhaust gas streams. Air Products’ Cryo-Condap® process uses proprietary technology to remove VOCs and meet emission levels of 20 mg/m3, as well as overcoming many of the limitations imposed by traditional emission-control methods. The Cryo-Condap® system is adaptable to suit most process types and can be customized fully to remove most VOCs.
With the enforcement of the EU Solvent Emissions Directive (1999/13/EC) and posterior Directives 2004/42/EC and 2016/2284 Cryogenic Condensation to recover solvents has suddenly become a thing.
Air Products
Pharmaceutical Company Meeting the Challenges of Environmental Legislation
The pharmaceutical company researches and develops vaccines, pharmaceuticals and consumer health care products.
The company is a world leader in topical antibiotic manufacturing. One of the company’s processes emits methyl acetate and methanol (VOCs). However, it is necessary to limit the release of these substances into the atmosphere in order to comply with Environment Agency regulations.
.png)
Cryo-Condap® technology for VOC recovery. A 255 m3/h Cryo-Condap® installation with redundant low temperature condensers.
While the site was currently meeting its legal permit requirements, a request from the Environment Agency asked the site to reduce the emissions from this pharmaceutical process by Best Available Technology (BAT). The process is operated batch wise and the emission profile has a number of line blows which generates a short sharp emissions profile, along with a period of powder drying which generates a long, slowly decreasing profile. This emission profile meant common abatement technology faced challenges in providing the low emissions required.
Pharmaceutical Company
Why Cryogenic Condensation?
Designed and engineered by Herco and supplied by Air Products, the Cryo-Condap® technology on VOC recovery and solvent abatement combines the inerting properties of nitrogen gas with the refrigeration power of liquid nitrogen. This combination results in a modular, skid-mounted VOC control system which is easy to install, highly effective and economical to run.
Liquid nitrogen has a boiling point of -196oC and so is an ideal medium in which to recover most VOCs almost totally. Typically, solvent recovery performance is better than 99.9%. This creates discharge concentrations that are low enough to meet even the most stringent environmental standards.
.png)
How Does the Cryo-Condap® Technology Work?
Cryo-Condap® is Air Products’ proprietary technology for recovering VOCs and solvents. The system cools down the process gas using liquid nitrogen in a heat exchanger. The capacity of the gas to carry the VOCs as vapour drops with the temperature. The VOCs are removed once they have condensed and frozen into particles. The process gas can then be discharged into the atmosphere because it conforms to environmental legislation.
Often, recovered VOCs can be re-used directly, which is more difficult with adsorption systems and not possible with catalytic oxidizers or incinerators. The nitrogen can also be re-used and this plays an additional role in cost reduction. Gas recovered from the Cryo-Condap® process is effectively free and sites that handle VOCs often use this nitrogen to purge and blanket pipework and tanks. Sometimes, the costs of the control are exceeded by the recovered costs.
Air Products supplies industrial gases, technology and services internationally, has more than 75 years of cryogenic experience, and has more than 200 Cryo-Condap® systems installed worldwide.
Designing and Installation
Methanol and methyl acetate are emitted from a process on site. In order to meet stringent UK Environment Agency Laws, they need to be recovered.
The solution was: a Cryo-Condap® system to condense the methyl acetate and methanol requiring a proprietary heat exchanger, with the installation and control package surrounding the heat exchanger being key to providing accurate temperature control capabilities.
Air Products
The company completed a questionnaire and provided Air Products with a performance specification for the process of methanol and methyl acetate recovery.
Herco’s bespoke design was arrived at during our first meeting and much of the functionality that was required, was able to be incorporated. Over a period of several months, the design was refined and HAZOP and SIL reviews brought in extra design requirements. The incoming process gas could not rule out a water component, which can freeze onto the surface of the liquid nitrogen cooled condenser. Functionality had to be designed into it to ensure the equipment could be defrosted during periods of inactivity.
Pharmaceutical Company
Basic Cryo-Condap® Process
Overall: The Cryo-Condap® process uses liquid nitrogen in a proprietary low temperature condenser in order to treat emission streams containing VOC.
Pre-Cooling: First, the VOC gas system is pre-cooled with a mechanical chiller or available cooling fluids in order to condense the bulk of the VOCs and moisture. Scrubbers are also used to neutralise acetic acids NH3 or CO2 sometimes present in the process gas stream.
Energy Recovery: The incoming VOC gas stream is further cooled by the cold exhaust streams from the low temperature condenser.
Cryogenic Condensation: To help ensure compliance, the flow rate of the liquid nitrogen is regulated so that the temperature inside the low temperature condenser can be controlled. This cools the VOC gas stream to the desired temperature.
VOC Recovery: Condensed VOCs travel through droplet separators and are collected in a buffer tank, where they are pumped and reused.
Nitrogen Recovery: The liquid nitrogen is vaporised fully during the process and so exits the system as clean nitrogen gas which can be reused for other applications.
.png)
The Result
The result is that emissions have been reduced and the Environment Agency commitment to reduce the levels of solvent emitted from this process has been met. Since the unit has been commissioned, solvent has been recovered that would otherwise have been emitted to the atmosphere.
Pharmaceutical Company
Air Products understands how environmental regulations can impact on businesses. Cryo-Condap® technology has been developed for this reason: not only to meet the most stringent government legislation worldwide, but additionally to improve process efficiency.
Air Products’ Cryo-Condap® System vs. the Traditional Way
One of the main advantages of Air Products’ Cryo-Condap® technology is it's inherent flexibility, allowing it to be customised to meet specific customer process needs, whilst matching the properties and requirements of their process.
The Cryo-Condap® system’s ability to cope with stop-start and fluctuating emissions profiles, as it is normally seen in a batch process, by having a ‘cold-sink’ of a refrigerant bath is a major advantage. It does not produce the over or under cooling as would be seen by a system using direct process gas to liquid nitrogen heat exchange. Another advantage is the ability to create the bespoke system tailored to the process’ flows and solvent loads.
Pharmaceutical Company
Another benefit of the Cryo-Condap® system is that the solvent can be recovered and recycled.”
Air Products
Conclusion
Previously the process had removed solvent using glycol condensers. Whilst they take the majority of the solvent load generated, an emission was still generated. The use of the Cryo-Condap® system allowed an even greater amount of solvent to be removed from the process gas.
Pharmaceutical Company
With increasingly restrictive legislation on solvent emissions to the atmosphere, there has been a greater need and urgency for industry to reduce emissions to meet or exceed targets, now and in the future.
Air Products
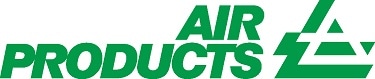
This information has been sourced, reviewed and adapted from materials provided by Air Products.
For more information on this source, please visit Air Products.