In the early days of additive manufacturing (AM), the technology was primarily focused on design and rapid prototyping applications. However, recent additive manufacturing is progressively being employed to create high-performance mechanical components from refractory and technical materials.
.png)
This is particularly common in space and aerospace engineering, where the combination of affordability, versatility, speed, and precision make additive manufacturing a desirable choice.
Its ability to print refractories in lightweight architectures makes it an appealing method, supplying high-temperature performance at a tiny proportion of the weight of traditionally fabricated refractory metal parts.
This article outlines the key strengths of AM compared to conventional subtractive manufacturing, and how these are being implemented to transform the landscape of space engineering.
NASA performed tests on a recent rocket injector design in 2013. During these tests, the subscale injectors, while burning hydrogen gas and liquid oxygen, were subjected to extreme temperatures greater than 3300 °C and extreme pressures for more than 46 seconds.
The tests were successful. An engineer supervising the tests explained that the new components ‘operated beautifully’, coping with the extreme conditions with no sign of failure. What is more outstanding is that these high-performance parts were each produced in a single-step additive manufacturing process.1
The subscale injectors used for these tests by NASA previously were manufactured utilizing conventional ‘subtractive’ methods: machining and milling bulk material and joining parts together.
The previous injectors cost $10,000 a piece to manufacture, had four parts, and were made over six months. The additive manufacturing of the new injectors did not only produce functionally indistinguishable components but also achieved this in less than three weeks and at half the cost.
NASA’s fuel injectors are only one example of the multiple ways in which additive manufacturing technologies are being applied for space applications to enhance manufacturing efficiency and component performance.
The Advantages of Additive Manufacturing
There are many advantages of additive manufacturing when applied to space engineering. First of all, additive manufacturing makes the construction of geometrically complex components possible, which would alternatively need highly specialized methods of production.
Once requiring several distinct processing steps, components such as NASA’s rocket injectors can now be manufactured in one consistent AM process.
Produced using AM, Researchers at the German Aerospace Center recently developed and prototyped a reusable rocket engine. The new additively manufactured design decreased the weight by 10%, reduced the number of parts from 30 to one, and provided enhanced performance over the previous design.2
Economic advantages are a further offering of additive manufacturing in comparison to conventional subtractive manufacturing methods. Practically eliminating the requirement for re-tooling or revision of manufacturing procedures for new parts, components can effectively be produced on-demand using a single machine, meaning that economy of scale is achieved much more easily.
AM can offer economy of scale for small unit volumes, frequently as low as one, meaning that manufacturers can order or produce components whenever they are required as opposed to ordering thousands of components to create economic efficiency.3
Additive manufacturing is both a cost-efficient method of producing large quantities of aerospace components and producing highly customizable components.
Lastly, the critical benefit of utilizing additive manufacturing for space applications is that it can be employed to significantly decrease the mass of components.
Additive manufacturing methods can be utilized to conveniently hollow-out components with closed cells, pockets, and holes to drastically reduce the mass of components. In contrast, subtractive manufacturing almost always creates ‘solid’ components of uniform density.
As an example, weight reductions of an astounding 70% have been evidenced for satellite components created by AM.4 This is not a trivial matter as the reduction of the mass of satellite components significantly decreases the amount of fuel needed to launch the satellite and to maneuver it upon reaching orbit.
The significance of shedding every gram possible in space applications can hardly be overstated. AM offers a means to decrease the mass of existing components without undermining performance. This is especially important when the generation of high-performance components from dense technical metals and refractories is required.
Additive Manufacturing Solutions for Space Engineering
There are very few components utilized in space technologies that would not benefit from a reduction in mass and enhanced turnaround times. As such, applications for AM in space engineering are virtually limitless.
AM is a chief candidate for the manufacture of satellite propulsion systems and rocket, shielding, and space vehicle components (for example, those utilized to clean up space debris).
Applying its years of expertise as an international leader in refractory metal solutions, H.C. Starck Solutions is redefining what is achievable with AM technology and the use of refractory metals in the space sector to stay ahead of the curve in the rapidly developing AM market. 5
It is taking full advantage of the lightweight features offered by AM to provide refractory metal solutions to applications where they were not previously considered.
Following critical investment in the development of AM methodologies and expertise on various AM platforms, H.C. Starck Solutions has become an international leader in the use of AM techniques with an extensive range of refractory metals for high-performance applications in space engineering.
H.C Starck Solutions is skiLlful in the production of precisely engineered three-dimensional components from demanding materials such as tantalum, niobium, molybdenum, tungsten, and their alloys; with further metals available on request.
For printed part applications in space engineering, H.C. Starck Solutions also offers engineered AM feedstocks: high-density spheroidized refractory metal powders with finely tuned particle size distributions, along with wires specifically designed for various AM deposition techniques.
References and Further Reading
- Boen, B. 3-D Printed Rocket Parts Rival Traditionally Manufactured Parts. (2015). Available at: https://www.nasa.gov/exploration/systems/sls/3dprinting.html
- Schulz, B. Additive Technology Delivers Small Satellites to Space. (2019). Available at: https://www.additivemanufacturing.media/blog/post/additive-technology-delivers-small-satellites-to-space.
- Joyce, J. Additive manufacturing paths to performance, innovation, and growth. (2012). Available at: www.deloitte.com/about.
- Dehue, R. The Possibilities of Weight Reduction With Additive Manufacturing. (2016). Available at: https://3dprinting.com/metal/possibilities-weight-reduction-additive-manufacturing/.
- Additive Manufacturing | HC Starck. (2019). https://www.hcstarck.com/
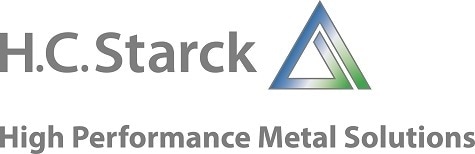
This information has been sourced, reviewed and adapted from materials provided by H.C. Starck Solutions.
For more information on this source, please visit H.C. Starck Solutions.