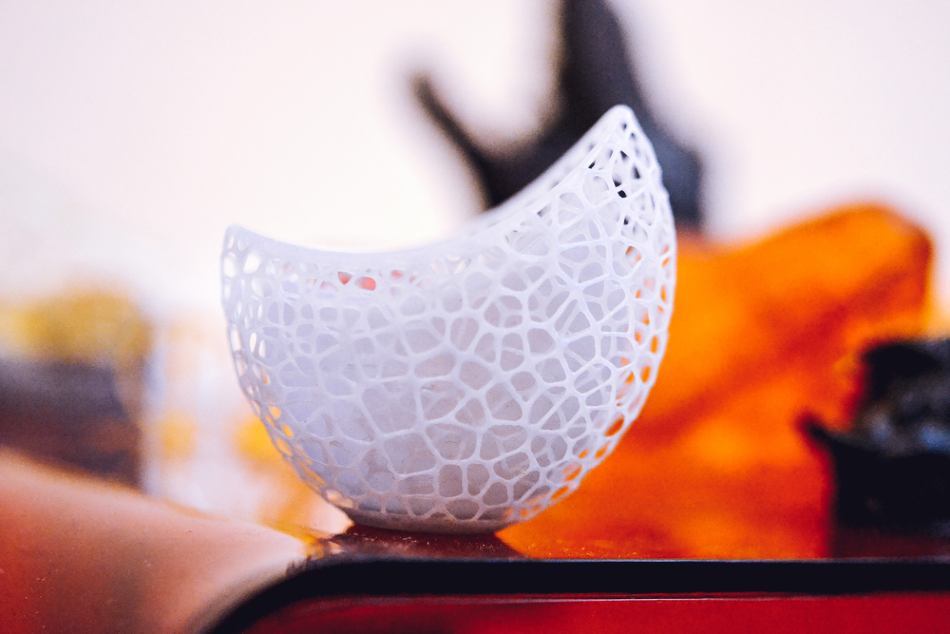
Image Credit: MarinaGrigorivna/Shutterstock.com
Additive manufacturing, commonly referred to as 3D Printing, is a technique that is growing in the manufacturing world to make various complex parts and huge designs. What started as a tool for making small models has now established itself as an effective manufacturing technique and its use is only going to grow in the future as people look to maximize productivity while minimizing material usage.
Polymers are a common material used in 3D printing methods as they can be easily processed into a solution that can be 3D printed. The use of metals is growing, but as it stands, polymers are the most widely used choice. While there are many different additive manufacturing methods, there is a specific one that is used for the extrusion of polymers (i.e. the creation of polymers with a fixed cross-sectional profile). The additive manufacturing method that can be used to extrude polymers is called fused filament fabrication (FFF), although it is more widely known in the commercial world as fused deposition modeling (FDM).
How Fused Deposition Modelling (FDM) Works
FDM can be used with several materials (including materials other than plastics) with some of the most common being acrylonitrile butadiene styrene (ABS), polylactic acid (PLA), Nylon, polyethylene terephthalate glycol (PETG), thermoplastic polyurethane (TPU), polycarbonate (PC), and polyetherimide (PEI). The polymers used can either be semi-crystalline or amorphous and the application often governs the choice of material – i.e., is it the cost, structural performance, or physical properties that are the main driving factors for the material choice.
In terms of the operational principle, FDM starts with the modeling stage, much like any additive manufacturing method, where the intended product is designed. For FDM, the design is saved as a standard triangle language (STL) file and transferred to the interfacing software. From here, the design is sliced into images to determine how to print each layer of the polymer product. The data is then transferred to the manufacturing equipment.
The product is built up layer by layer by selectively depositing the melted polymeric material. The polymer is fed through a nozzle with a predetermined cross-sectional area, while simultaneously being heated. The temperature of the nozzle, alongside the build area, filament size, build speed, layer height, and cooling efficiency, all affect how well the polymer is extruded and deposited on to the surface.
Each layer is added on top of the next, and because the polymer is in a melted state when it is extruded, the layer being deposited fuses under pressure with the already deposited layers to build a complete structure. Each layer is typically anywhere between 50 and 400 microns in thickness.
However, because the deposition of each layer exhibits a force on the previous layer, the shape of the layers is often oval. For a complete product, the texture can be quite ‘wavy’ in nature, where the oval layers fuse. These effects can be negated through post-processing methods, which are commonly used to smooth out the product, as well as remove any small holes that arise from this wavy formation.
Advantages and Disadvantages of FDM
Depending on the material used, the product is likely to have advantages and disadvantages which are specific to the material choice. This is why the material choice is often tailored to the application. Aside from this, the methodology of FDM has some advantages and disadvantages over other additive manufacturing methods.
In terms of operational advantages, FDM has become one of the most efficient ways of producing both products and prototypes with thermoplastic materials, as well as being inexpensive to use, having short lead times (products can be created within a day), and can be used with a wide range of plastic (and non-plastic materials), including some with very strong structural properties (such as ABS).
However, one of the main disadvantages of FDM is that it has one of the lowest dimensional accuracies and resolutions of all additive manufacturing methods, which limits its use with intricate and complex parts.
Other disadvantages include the need for constant pressure being applied to the product to fuse the layers effectively (and increase the quality), the nozzle thickness limits the accuracy of the model to the initial design, the parts are likely to have visible layer lines (unless post-processed efficiently) and the layer deposition mechanisms makes FDM products anisotropic.
References and Further Reading
White Clouds: https://www.whiteclouds.com/3DPedia/extrusion.html
3D Hubs: https://www.3dhubs.com/knowledge-base/introduction-fdm-3d-printing/#work
Loughborough University: https://www.lboro.ac.uk/research/amrg/about/the7categoriesofadditivemanufacturing/materialextrusion/
Disclaimer: The views expressed here are those of the author expressed in their private capacity and do not necessarily represent the views of AZoM.com Limited T/A AZoNetwork the owner and operator of this website. This disclaimer forms part of the Terms and conditions of use of this website.