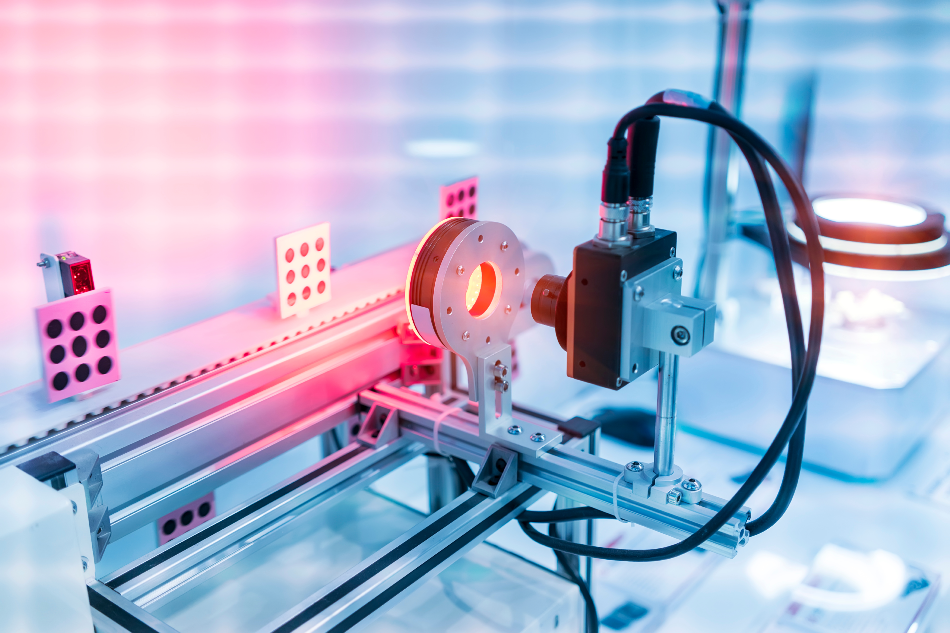
Image Credit: asharkyu/Shutterstock.com
Machine vision (MV) is the term applied to a series of methods and technologies which are used in industry to inspect and analyze products and data. These uses include process control, robot guidance, and automatic inspection. Many different industries benefit from the correct application of MV processes.
The processes themselves require specialized equipment and highly trained operators. Machine vision processes provide automatic solutions to analytical techniques that are much more efficient than human-based analysis alone.
Even though they are overlapping technologies in the field of artificial intelligence, machine vision differs from computer vision in one important way: while computer vision uses algorithms to process and interpret the image, machine vision uses a digital camera and lighting system to enable a computer to recognize an image.
Back-end image processing hardware and software are also integral to an MV system. The digital camera captures the image and sends it to the back-end system, which then processes or stores it accordingly.
Over the years, many different methods have been developed to provide a clear and in-depth automatic analysis of images in MV systems. Some of these will be briefly discussed in this article.
MV Imaging Methods: An Overview
All MV imaging methods are designed to provide fast, efficient image analysis and interpretation of images. Some of these are:
Conventional 2D Visible Light Imaging
This is the most commonly used MV technique to capture details of objects under analysis. However, 2D visible light imaging is limited by the wavelengths of light that can be detected, meaning that the technique is not suitable for some applications. There are some key differentiations in this technique, which include frame rate, resolution, and monochromatic vs. color systems.
Multispectral Imaging
In multispectral imaging, image data that ranges across the electromagnetic spectrum is used to create images. This type of imaging provides visual information beyond the limited range of the human eye and visible light, including ultraviolet and infrared spectra.
Originally developed for military applications, early space-based imaging systems were developed with multispectral imaging to detect features for mappings, such as coastlines and vegetation. Multispectral imaging is employed in many different areas, including artwork and document analysis, weather forecasting, and land mine detection.
Hyperspectral Imaging
Hyperspectral imaging (otherwise known as imaging spectroscopy and 3D spectroscopy) differs from multispectral imaging in that it measures continuous spectral bands instead of spaced spectral bands. Hyperspectral imaging provides an even more in-depth analysis of an object’s spectral fingerprint to form a 3D hyperspectral data cube by utilizing a vast portion of the electromagnetic spectrum. There are four ways one of these systems can sample the hyperspectral cube: spectral scanning, spatial scanning, snapshot imaging, and spatio-spectral scanning.
Hyperspectral imaging has been used in molecular biology, oil exploration, astronomy, surveillance, agriculture, and physics.
Line Scan Imaging
Line scan imaging builds up an image one line at a time using a linear array with a very high degree of precision. A line scanning camera uses a single row of light-sensitive pixels that scan a moving object on a conveyor belt at a very high frequency, capturing multiple “slices” of an image.
However, the data must be interpreted accurately, or the image produced may make no sense. Therefore, encoders are used to capture the speed of the web/conveyor so that the slices can be stitched together properly. Trigger pulses are utilized to identify the beginning and endpoint of the product being imaged.
Line scanning is used in product development and QA applications. It is especially useful for identifying rotating or cylindrical objects. Distortion, which would be produced by area scanning techniques, is limited as the line scanning camera or sensor records the same optical position across the entire cylinder.
3D MV Techniques
The above 2-dimensional MV techniques are limited by factors such as parallax, ambient light, depth of focus, and contrast variations. A two-dimensional image does not provide enough Z-axis data, making 2D MV of limited use where shape information is critical. There are also issues with sensitivity to light in 2D systems.
While machine vision has been in use for decades, recently, three dimensional MV techniques have been emerging within the field to address the issues with what is a very dependable technology.
The four main 3D MV techniques are laser triangulation, time-of-flight, stereo vision, and structured light. Although these systems require a larger degree of complexity and processing power than their 2D counterparts, they help to provide more in-depth analytical data in areas where 2D imaging falls short, such as:
- Dimension and space management
- Detection of surface and assembly defects
- Measuring features such as angles, shapes, holes, and curves
- Object scanning/digitization
- Robot guidance
- Surface tracking
- Verification against 3D CAD models
Conclusion
Machine Vision is a highly dependable technique that can provide in-depth information on products and processes, weather patterns, military target identification, biomedical applications, product quality, and much more. There are a variety of processes available to analysts, and recent developments in 3D MV techniques have helped contribute to the continuing relevance of this method in laboratories, factories, and field-based studies.
References and Further Reading
Line Scan Technology – Stemmer-imaging.com. https://www.stemmer-imaging.com/en-gb/knowledge-base/cameras-line-scan-technology/
Introduction to Machine Vision - A guide to automating process & quality improvements. https://www.assemblymag.com/ext/resources/White_Papers/Sep16/Introduction-to-Machine-Vision.pdf
Schumman-Olsen, Henrik - Why 3D machine vision? What’s wrong with 2D machine vision? https://info.zivid.com/blog/why-3d-machine-vision-whats-wrong-with-2d-machine-vision
Chapman, Aofie – Multispectral Imaging in Machine Vision. https://www.prophotonix.com/blog/multispectral-imaging-in-machine-vision/
Disclaimer: The views expressed here are those of the author expressed in their private capacity and do not necessarily represent the views of AZoM.com Limited T/A AZoNetwork the owner and operator of this website. This disclaimer forms part of the Terms and conditions of use of this website.