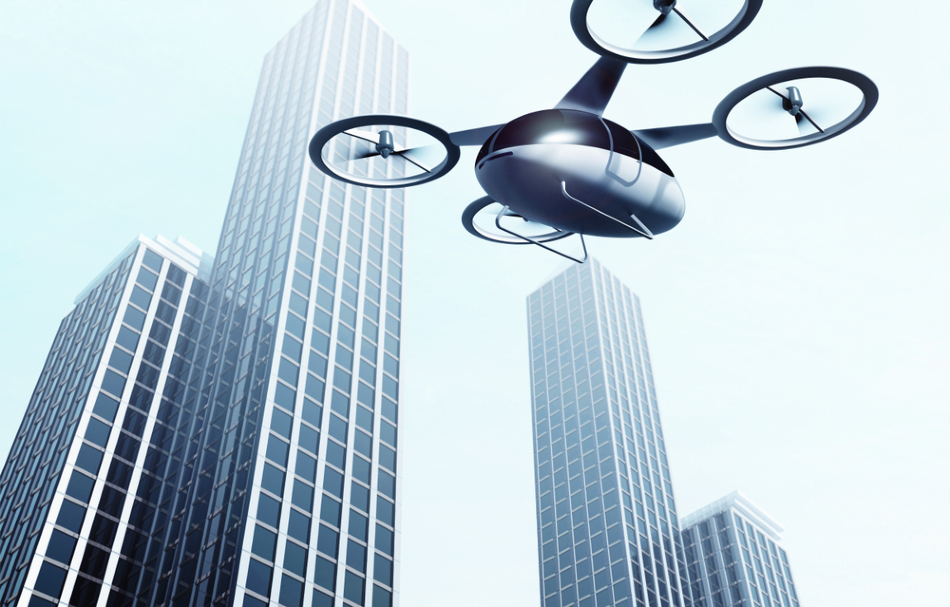
Image Credit: andrey_l/Shutterstock.com
The aviation industry is currently seeing a shift towards urban air mobility aircraft capable of carrying 1-8 passengers. The dream of personalized flying vehicles was conceived as far back as the 19th century, with nearly 80 filed patents on flying cars at the United States Patent and Trademark Office.
The earliest design of a flying car dates back to 1917 when Glenn Curtis built the Autoplane. The design featured a triplane configuration with a four-blade pusher propeller attached to an aluminum body fuselage inspired by the model T.
The vision of urban air mobility vehicles faces several challenges that have to be overcome before it can be considered a viable means of transportation.
Find out more about nanofiber production equipment
One of the major problems faced in development is being able to design vehicles rigid enough to withstand minor collisions when on-ground and light enough to fly effectively.
Furthermore, current battery technology does not have a high enough energy density to allow for longer flight time in all-electric aircraft. This hugely limits the range of electric aircraft in comparison to their fuel-powered counterparts.
Large batteries are required to increase the aircraft's power output. This increases the overall weight of the aircraft, requiring an even larger battery to operate. Urban air mobility vehicles also face the inherent danger of control when flying, with airline pilots having to secure a pilot’s license before flying. A viable solution would be to implement full autonomy of the flying vehicles with no need for a driver's input as seen in self-driving cars.
Autonomous UAM Vehicles will be able to detect where other vehicles in its vicinity are located and act accordingly to prevent collisions. By using highly effective control and automation networks Urban Air Mobility vehicles will prove to be a safer more viable means of transportation.
Recent advancements in technology have led to a resurgence of the idea of medium-sized Air Mobility vehicles for urban transportation. The implementation of 3D printed carbon fiber techniques will allow for the production of Aircraft parts that are lighter and stronger than traditional materials.
A case of this implementation can be seen with the Utah Advanced Materials and Manufacturing Initiative (UAMMI). UAMMI uses composite-based additive manufacturing (CBAM) 3D printers developed by Impossible Objects to fabricate Aircraft parts for the Airforce.
The aircraft parts are created by first creating a digital CAD model of the part being fabricated, the 3D printer then segments the CAD model into thin layers in preparation for printing. Layers are printed onto thin stack carbon fiber sheets using a thermal inkjet aqueous fluid. High-performance thermoplastic polymers are then added onto the sheet.
Find out about nano 3D printing
The polymer powder sticks to the sheet where the fluid was added. The printed stack is then compressed and heated to the melting point of the polymer. The layers become fused into a solid part, the finished part is revealed by a sandblasting unit. The process produces carbon fibre reinforced plastic (CFRP) which has a comparable strength to weight ratio to aluminum but at half the weight.
A number of companies have kept the dream of UAM alive with news of Uber announcing plans to implement flying taxis to transport passengers within cities and vehicles such as the AeroMobil.
ElectraFly provides a more personalized approach to flight, with its transport drone capable of carrying a passenger. The ElectraFly aircraft features an eight-rotor configuration for added redundancy during flight. ElectraFly is equipped with wings to reduce the lifting burden on the motors. It is also equipped with a jet-powered turbine making it a hybrid system capable of reaching high altitudes but designed for an optimum altitude just below 5000 ft at a speed of 50 mph.
ElectraFly: These Guys Put a Jet Turbine on a Huge Drone...
Video Credit: Roswell Flight Test Crew/YouTube.com
CBAM Technology proves highly beneficial when implemented into Urban Air Mobility Vehicle parts as stronger and lighter parts can be printed up to 10x faster than conventional printing methods. These parts can also be printed in a wider selection of materials. This can be seen in the recent collaboration between UAMMI and ElectraFly to replace its parts with 3D printed composite materials.
The use of CBAM technology will also allow for rapid prototyping as design changes can be built at a faster speed than the conventional printing method. UAMMI and ElectraFly collaboration will first see a replacement of the vehicle's metal gears with composite fabricated parts.
Constant innovation in battery technology to improve energy density has resulted in speculations of a one million mile battery at Tesla, which will be able to withstand about 6000 charge cycles with a 10% battery life degradation. The implementation of 3D-printed carbon fiber aircraft parts and future battery technology will greatly improve the viability of Urban Air Mobility vehicles.
References and Further Reading
Chem, S. (2020) New Partnership To Develop 3DP Carbon Fiber-Reinforced Plastic Aircraft Parts. [Online] Omnexus.specialchem.com. Available at: https://omnexus.specialchem.com/news/industry-news/3dp-plastic-aircraft-parts-000221720 [Accessed 23 June 2020].
JEC Group (2020) 3D Printed Carbon Fiber Aircraft Parts For The Urban Air Mobility Market. [Online] Available at: http://www.jeccomposites.com/knowledge/international-composites-news/3d-printed-carbon-fiber-aircraft-parts-urban-air-mobility [Accessed 23 June 2020].
Disclaimer: The views expressed here are those of the author expressed in their private capacity and do not necessarily represent the views of AZoM.com Limited T/A AZoNetwork the owner and operator of this website. This disclaimer forms part of the Terms and conditions of use of this website.