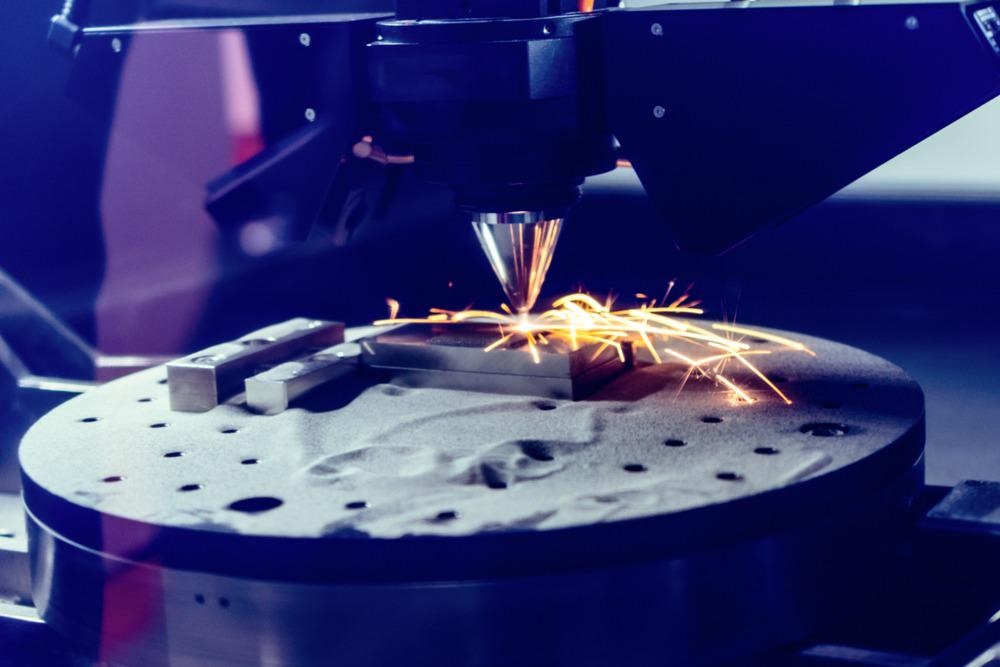
Image Credit: Nordroden/Shutterstock.com
Additive manufacturing, or 3D printing, enables designers and engineers to build up complex geometries layer by layer to yield high-quality, high-performance parts. It allows items to be produced onsite, meaning a reduced manufacturing time, cost savings, and a positive impact on the environment thanks to reduced shipping.
A new system from Desktop Metal, an expert in mass production and turnkey additive manufacturing solutions, looks set to make additive manufacturing even more attractive by allowing the 3D printing of complex metal parts in an office environment in a simple two-step process which eliminates the solvent debinding step.
Building on Success
Studio System 2 is a simplified, office-friendly metal 3D printing technology that utilizes Desktop Metal’s proprietary Bound Metal Deposition (BMD) technology. This powder metallurgy-based process swaps the loose powders and lasers traditionally associated with metal 3D printing with bound metal rods to shape parts layer by layer.
The new system keeps all the critical features of the original Studio System, but its improvements aim to make metal part 3D printing in low volumes for pre-production and end-use applications even easier, more reliable, and accessible.
As additive manufacturing adoption advances worldwide, Desktop Metal continues to drive innovations that enable the technology to more effectively compete with conventional manufacturing processes."
Ric Fulop, CEO, and co-founder of Desktop Metal
“Our next-generation Studio System 2 takes the best features of the original Studio System+ and significantly improves upon them, delivering higher quality end-use metal parts through a more streamlined and accessible process, and within an even smaller footprint,” Fulop adds.
Additional Functionality
Arguably, the most significant advancement is the two-step process that eliminates solvents' use with all-new material formulations, allowing parts to be moved directly from the printer to the furnace. Desktop Metal says the “breakthrough” results in a “nearly hands-free process that also reduces consumable usage and overall system footprint”.
The new system also features new print profiles and an all-new material system which will minimize part trial and error by enabling even shrinkage during sintering. It also increases part success across a broader range of complex geometries. Furthermore, the printer’s heated build chamber and new print profiles offer superior part quality, accuracy, and an outstanding surface finish right out of the furnace.
Studio System 2 is initially launching with 316L stainless steel, a general-purpose material with excellent corrosion resistance used in several industries for manifolds, nozzles, brackets, as well as latches and jewelry. A wide selection of other materials that can be utilized in the updated, two-step process is in active research and development, and new releases are expected throughout 2021.
The system will be backward-compatible through the use of a debinder, meaning all material previously supported by 2017’s Studio System can be used, including 17-4H stainless steel, 4140 low alloy steel, H13 tool steel, and copper.
Controlling Fabrication
The Fabricate software is supervising the process. This technology fully automates part creation to create high-quality end-use items similar to those produced with casting. It features new, default print profiles that simplify build groundwork while permitting access to more than 90 custom print settings.
It also creates separable support structures with strategic splits to prevent locking during post-processing, while fully automating the thermal debind and sintering cycles.
Based on the success of our original Studio System, we know companies around the globe are eager to adopt our new, more streamlined Studio System 2 process to produce difficult-to-machine parts featuring complex geometry like undercuts and internal channels."
Ric Fulop, CEO, and co-founder of Desktop Metal
Fulop added, “Across manufacturing, tooling, automotive, consumer products and electronics, and medical applications, companies are sharing how additive manufacturing is challenging their design and engineering teams to think differently about how to optimize designs for best-in-class part success.”
Desktop Metal aims to begin shipping Studio System 2 in the first quarter of 2021 and boasts MIT, Ford Motor Company, and Google LLC amongst its numerous customers.
References and Further Reading
Desktop Metal (2021) Desktop Metal Launches Studio System 2, the Easiest Way for Designers and Engineers to Print Complex, High-Performance Metal Parts in the Office [Online] Available at: https://ir.desktopmetal.com/news/press-releases/detail/44/desktop-metal-launches-studio-system-2-the-easiest-way-for (Accessed 15 February 2021).
Desktop Metal [Online] Available at: https://www.desktopmetal.com/ (Accessed 19 February 2021).
Disclaimer: The views expressed here are those of the author expressed in their private capacity and do not necessarily represent the views of AZoM.com Limited T/A AZoNetwork the owner and operator of this website. This disclaimer forms part of the Terms and conditions of use of this website.