As air traffic is projected to increase dramatically over the next decade, reducing noise pollution becomes an even more necessary and demanding challenge. Decades of research have been dedicated to reducing the noise of an aircraft’s engine but have tended to neglect the noise caused by the airframe during landing. Recent research published in Journal of Aircraft from Texas A&M University has suggested that shape memory alloys may be the key to solving noise pollution during landing without degrading the aerodynamic properties of the airframe itself.
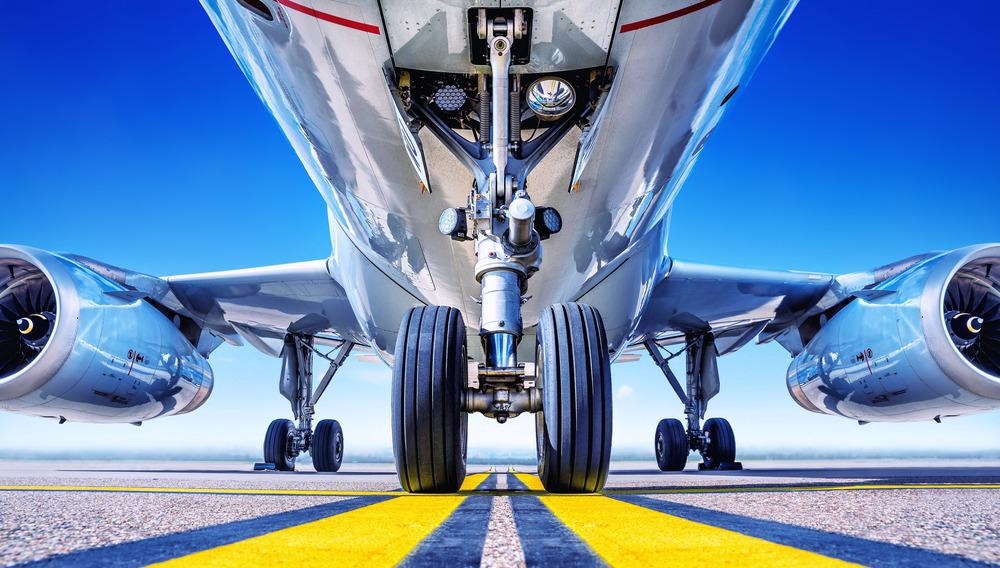
Image Credit: frank_peters/Shutterstock.com
Aero-Engines and Sound Pollution
Though the mechanics and composition of an aero-engine are complex, creating propulsion is simple. Cold air enters via the engine’s intake and is then pressurized through a compressor, increasing its temperature to make it combustible. Then, the air is mixed with fuel and ignited, further increasing its internal energy before being expanded again through the engine’s turbine, leaving through the outlet. The energy difference is caused by compression, while thrust is generated by combustion.
The three main types of aero-engines (Turbofan, Turboprop, and Turbojet) all share this basic premise, though they can differ in intake methods, fuel efficiency, and thrust generation. Some engines also have additional components like mixers, which combine cold intake air with hot ignited air at the exhaust, increasing efficiency.
Mixing air at the exhaust, adding additional components such as active noise control (ANC), and even the engine's geometry are all methods of reducing the noise created by aircraft engines. These methods, however, cannot reduce noise entirely and do little to reduce noise at all during an aircraft's landing phase.
The Problem with Landing
As aero-engines are typically idle or producing very low thrust during landing, the engine itself no longer becomes the primary noise source, giving way to airframe noise. For decades, engine-related noise pollution was considered a priority over airframe noise. As a result, little research had been done until engine noise had been reduced to a level equal to airframe noise.
The two most significant problem areas for airframe noise are the wings and the landing gear. As landing gear is lowered from the plane during landing, the slats (leading edge) and flaps (trailing edge) of the wing extend to ease landing by providing equal lift at lower speeds. These changes to the aircraft profile alter the airflow around it. Air enters the vacuum-like space created by the extended flaps and slats, forming turbulent eddies, which then resonates and makes an unpleasant high-pitched noise.
Researchers are met with a difficult decision when considering the problem of airframe noise. Aeronautical engineering is an intricate science, and small changes to an airframe's characteristics can dramatically affect its efficiency. Although tackling airframe noise is necessary, minimal changes must be made to the airframe's aerodynamic properties.
Shape Memory Alloys to Reduce Airframe Noise
One potential method proposed to reduce airframe noise pollution is to insert an elongated 'S’-shaped filler inside the space created by the extended leading edge. This membrane, researched by Dr. Darren Hartl and various NASA collaborators, would effectively disable the circulation of the turbulent air, stopping the resonance and, consequently, the unpleasant sound it produces. However, subsequent research has found that all proposed materials could not form the S-shape during landing, then return to their original shape inside the retracted slat to a satisfactory degree.
The material used had to be malleable to sufficiently form the S-shape on landing while still resisting high stresses and cycle fatigue. Hartl's research began to analyze using a shape memory alloy for the filler to solve these issues.
Using a shape memory alloy would mean that the alloy could change form during each landing. The airflow itself would change the shape of the alloy, optimizing its shape to reduce noise cancellation.
Recent Developments in Shape Memory Alloys and Their Applications in Aerospace Engineering
Shape memory alloys refer to materials that can be deformed plastically, then return to their original shape when activated by heat; the atomic structure remains similar to its original shape. en if the structure undergoes shear forces, the atoms are connected in the same way as in their high-temperature phase. When heated, these connections straighten like in their high-temperature phase, returning the component to its primary form.
This similarity in atomic structure is unique to shape memory alloys compared to other conventional metals. If these metals undergo enough force, they will undergo slip, where a section of an atomic crystal deforms more than the rest of the crystal. Deformation due to slip does not reverse under heat, as it does in shape memory alloys.
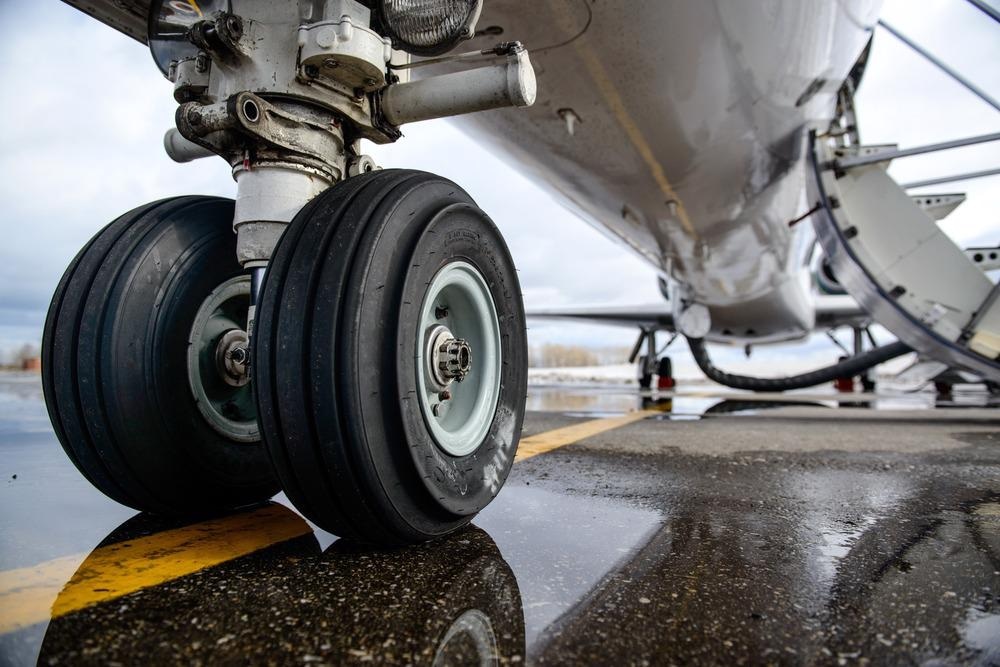
Image Credit: Yuri Kabantsev/Shutterstock.com
Nitinol, a Nickel-Titanium shape memory alloy, is the most common shape memory alloy and the most useful in aerospace engineering. The most well-known application for Nitinol is its use on the curiosity rover. Initially, the thin aluminum wheels of the Mars rover would become damaged from the rough terrain of Mars. To solve this, NASA replaced Curiosity's wheels with a wire-mesh wheel of Nitinol. Its superelastic properties meant the wheels could deform to Mars' rough terrain with no permanent damage or deformation.
Other applications for shape memory alloys have been proposed for fixed-wing aircraft. Nitinol has been investigated as a method of twisting aircraft wings via its shape recovery characteristics. Wing twist, used to alter lift distribution across a wing, could be activated by heating Nitinol 'Torque Tubes'. Unfortunately, current technology can not provide enough force on a full-scale wing.
Disadvantages of Shape Memory Alloys and Their Future in Aerospace
The most glaring disadvantage of shape memory alloys is the difficulty in dynamically modeling their behavior; as air flows across the filler, its shape changes. The shape of the airflow is altered, creating an inconsistent model that is hard to analyze entirely, even with fluid dynamics modeling.
As shape memory alloys are new material, there is relatively little research on them. Still, as more explorations take place, attributes can be improved. Perhaps in the future, the strength of Nitinol 'Torque Tubes' can be increased to the point where they can be applied in the aerospace industry.
The current S-shaped filler design is implementable, but bulky and potentially heavy. Increasing the weight of an aircraft is highly undesirable, as it means payload must be reduced to meet its Maximum Take-Off Weight (MTOW). Hartl has suggested future research may result in smaller, different shapes that are capable of noise cancellation.
References and Further Reading
Arena, G., Groh, R., Pirrera, A., Turner, T., Scholten, W. and Hartl, D., (2021) Design of Shape-Adaptive Deployable Slat-Cove Filler for Airframe Noise Reduction. Journal of Aircraft, pp.1-17. Available at: http://dx.doi.org/10.2514/1.C036070
engineerguy, (2018) Nitinol: The Shape Memory Effect and Superelasticity. [video] Available at: https://www.youtube.com/watch?v=wI-qAxKJoSU
Hartl, D. and Lagoudas, D., (2007) Aerospace applications of shape memory alloys. Proceedings of the Institution of Mechanical Engineers, Part G: Journal of Aerospace Engineering, 221(4), pp.535-552. Available at: https://doi.org/10.1243/09544100JAERO211
Kang, G. and Song, D., (2015) Review on structural fatigue of NiTi shape memory alloys: Pure mechanical and thermo-mechanical ones. Theoretical and Applied Mechanics Letters, 5(6), pp.245-254. Available at: https://doi.org/10.1016/j.taml.2015.11.004
L. Lasagna, P., G. Mackall, K., W. Burcham, F. and W. Putnam, T., (1980) Landing Approach Airframe Noise Measurements and Analysis. [PDF] Edwards, California: NASA. Available at: https://www.nasa.gov/centers/dryden/pdf/87919main_H-1075.pdf
Real Engineering, (2018) How NASA Reinvented The Wheel - Shape Memory Alloys. [video] Available at: https://www.youtube.com/watch?v=2lv6Vs12jLc
Sadeghian, M. and Gorji Bandpy, M., (2020) Technologies for Aircraft Noise Reduction: A Review. Journal of Aeronautics & Aerospace Engineering, 9(219). Available at: https://www.longdom.org/open-access/technologies-for-aircraft-noise-reduction-a-review-47567.html
ScienceDaily. (2021) Shape-memory alloys might help airplanes land without a peep. [online] Available at: https://www.sciencedaily.com/releases/2021/07/210712183327.htm
Disclaimer: The views expressed here are those of the author expressed in their private capacity and do not necessarily represent the views of AZoM.com Limited T/A AZoNetwork the owner and operator of this website. This disclaimer forms part of the Terms and conditions of use of this website.