Additive Manufacturing (AM) is a fabrication technique that has gained significant traction because it offers an extensive range of industries greater scope and significant competitive advantages. Its attractive features have pulled AM into the orbit of aerospace with the processing of aluminum alloys.
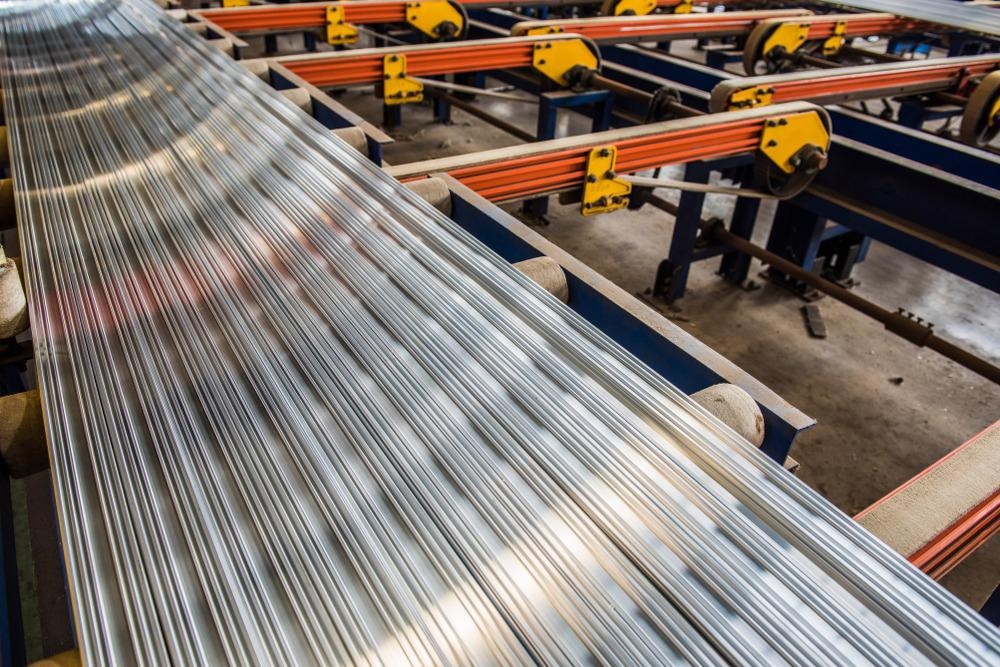
Image Credit: Xiangli Li/Shutterstock.com
Here, why AM is important within this industry is partially explained while explorations at Auburn University into processing aluminum alloys—of particular interest to aerospace using AM—are reported.
In addition to its green credentials and inherent cost-effectiveness, AM can make possible the realization of complicated parts that hold convoluted geometries while allowing freedom in design that reduces component weight and lead times.
Recently, strong Al alloys have become the materials of choice within the aerospace industry, not least due to their processing compatibility with AM; they have workability that facilitates intricacy and fabricating complex shapes.
This compatibility, in combination with such properties as high tensile strength and corrosion resistance, accounts for their selection as aerospace materials because damage tolerance and fatigue durability are key requirements in an industry that possesses the most exacting of standards.
Although manufacturing of this nature offers much, AM of Al alloys does present some challenges that could compromise safety should the structural integrity of the resulting products not be fully investigated.
In other words, it is essential that the materials are subjected to rigorous testing prior to deployment in any load-bearing application.
The innate characteristics of Al powder together with the induced surface roughness and stress inherent in AM processing makes investigating Al alloy properties critical because defect formation can result from the hydrophilic and low melt viscosity properties of Al powder.
These properties can promote porosity.
AM parts, in being produced by cyclic deformation at elevated temperatures, can introduce and elongate flaws such as pores and lack of fusions (LoFs) that ultimately can cause part deterioration if not addressed.
Although alloy development for AM is ongoing, and various bodies are collaborating in establishing an AM standardization road map, little hard data currently exists on fatigue performance in relation to different microstructural featured alloys that are receiving attention from aerospace AM-users.
These include Scalmalloy, possessing as it does a combination of high tensile strength with sufficient ductility resulting from a microstructure uniquely comprised of nano-sized grains and precipitates.
It is also known that Al-Si cast alloys in comparison to wrought Al alloys process much more easily. Hence, their potential is being investigated.
One of the most important properties to understand is the fatigue anisotropy behavior, by identifying how it is affected by the orientation of LoF defects with respect to the loading direction, fundamental to material selection.
Different values in ductility and fatigue strength are usually captured when measured in different directions, whether a loading direction is parallel to the build direction or perpendicular.
Although groups have studied the fatigue anisotropy behavior of LB-PBF Al alloys, further research is required to provide a more confident picture.
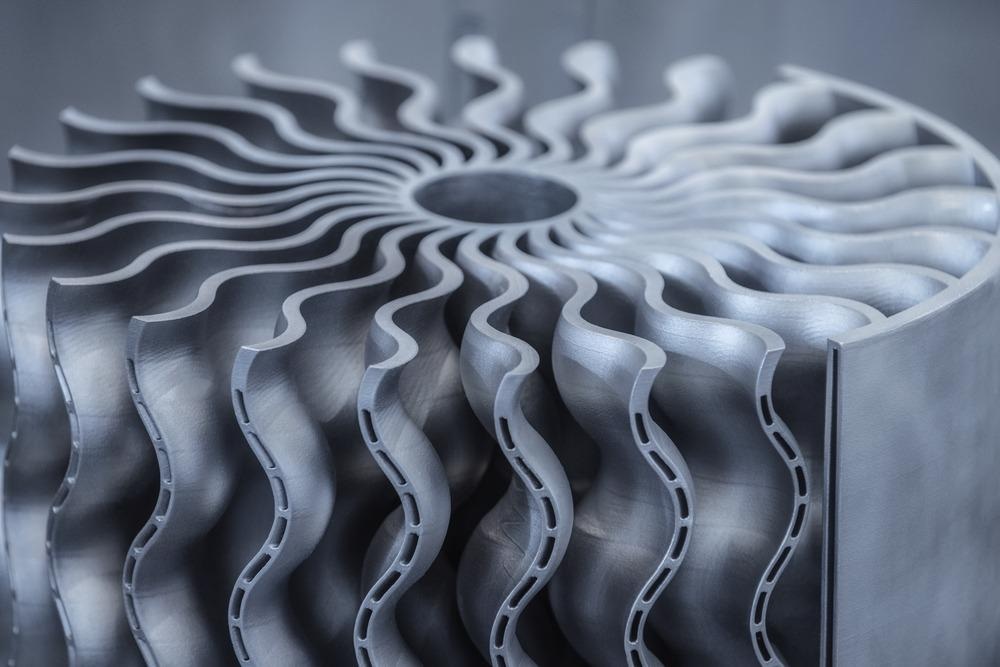
Image Credit: Sergii Chernov/Shutterstock.com
The paucity in performance data is where the initial exploratory research that Nezhadfar et. al, in the journal Additive Manufacturing, have conducted could prove so valuable in the context of newly developed Al alloys finding their way into future aircraft.
Using an AM process called laser beam powder bed fusion (LB-PBF), the team produced five contemporary Al alloys known as AlSi10Mg, Scalmalloy, QuesTek Al, AD1 (Addalloy® 5T), and AlF357.
In an attempt to correlate micro-/defect-structure with fatigue behavior and build orientation, the researchers chose to fabricate in both horizontal and vertical orientations.
In gathering such data, the team anticipated contributing specific knowledge largely unknown about the relationship between thermal history variation and different build orientations as determined by the defect type, size, and populations.
In having a range of alloys with differing microstructural characteristics such as grain structure, the influence that volumetric defects presents in affecting the anisotropy in mechanical behavior might be determined.
Significant Findings
The team found that Scalmalloy and AD1 (Addalloy® 5T) have the highest fatigue resistance among the five investigated. It is thought that their superfine microstructures may be the greatest contributing factor to this.
Although they were able to determine that AlF357 and QuesTek Al exhibit anisotropic behavior, the fatigue behavior of AlSi10Mg, Scalmalloy and AD1 (Addalloy® 5T) alloys has been determined to be independent of the micro-/defect-structure or vertical and horizontal specimen variations; there is simply no significant build orientation dependency.
From other work, enhanced fatigue strength was confirmed when porosity was reduced as a consequence of using smaller powder particles.
The Future of AM Al Alloys
Although Nezhadfar et. al. have been successful in garnering knowledge that is informative to AM adopters who need to select an appropriate Al alloy for their purpose, this has only been the start of a much-needed, wider study.
Damage tolerance design, for example, still requires more research and greater reach. A deeper dive into such structural integrity aspects as fatigue prediction modeling would greatly advance the topic.
How far is it possible to really go in minimizing fatigue failure? To what extent can the material scientist prevent the formation of micro-voids during the AM process? These questions still require answers.
References and Further Reading
Nezhadfar P.D. et. al. (2021) Structural integrity of additively manufactured aluminum alloys: Effects of build orientation on microstructure, porosity, and fatigue behavior. Additive Manufacturing. 47102292 https://doi.org/10.1016/j.addma.2021.102292
Gockel J. et. al. (2019) The influence of additive manufacturing processing parameters on surface roughness and fatigue life. International Journal of Fatigue. 124 380 https://doi.org/10.1016/j.ijfatigue.2019.03.025
Frazier W.E. (2014) Metal additive manufacturing: a review. Journal of Materials Engineering and Performance. 23 1917 https://doi.org/10.1007/s11665-014-0958-z
du Plessis A. et. al. (2020) Killer notches The effect of as-built surface roughness on fatigue failure in AlSi10Mg produced by laser powder bed fusion. Additive Manufacturing. 35 101424 https://doi.org/10.1016/j.addma.2020.10142
Disclaimer: The views expressed here are those of the author expressed in their private capacity and do not necessarily represent the views of AZoM.com Limited T/A AZoNetwork the owner and operator of this website. This disclaimer forms part of the Terms and conditions of use of this website.