The past five years have seen an increasing interest in the novel applications of electrical discharge machining, particularly from the Far East and Europe, with industry starting to see the potential of the technique for surface modification. Normally used for manufacturing dies/moulds and aerospace components, researchers at the University of Birmingham are adapting the technique to enable surface hardening of workpieces to create, in some cases, new, harder alloys on the surface of components to increase their working life and wear resistance. What is Electrical Discharge Machining? Electrical discharge machining (EDM) is a thermal process that involves melting and vaporisation of the workpiece electrode. It is widely used in the aerospace, mouldmaking and die casting industries for manufacturing plastics moulds, forging dies and die casting dies made from hardened tool steels, together with engine components, such as compressor blades made from titanium alloys and nickel-based superalloys. In addition to the more well known EDM operations of die sinking, scanning/milling with a simple electrode and wire cutting, other operations and machine configurations exist, one of which allows the surface of hardened steel rolls used in the production of steel and aluminium sheet to be textured. How Does Electrical Discharge Machining Work? The EDM process uses electrical discharges to remove material from the workpiece, with each spark producing a temperature of between 10,000-20,000°C. Consequently, the workpiece is subjected to a heat affected zone (HAZ) the top layer of which comprises recast material. The thickness, composition and condition of this layer depend on the discharge energy and the make-up of the workpiece, tool electrode and dielectric fluid, and both hard and soft surface layers can be produced despite perceived wisdom that the recast layer is always hard. With ferrous workpiece materials, the recast layer typically appears white and amorphous when viewed under a microscope, and is prone to tensile stress, microcracking and porosity. The Recast Surface Layer To increase the life of the tool or product, the recast layer is generally removed, particularly for applications in which the part is subjected to cyclical stress (aeroengine components) or fluctuating loads (forging and punching tools/dies). This is achieved either by hand polishing, etching or heat treatment. Alternatively, burnishing or shot peening is employed in order to impose a compressive residual stress regime. However, such processes are supplementary and may increase cost and time. With operations in which repeated high levels of mechanical impact are not a factor, such as plastics injection moulding, the EDM recast layer can be beneficial in providing increased abrasion and corrosion resistance. Surface Alloying During Electrical Discharge Machining Another way of improving the surface integrity and wear resistance of an EDM workpiece is by applying surface alloying during sparking, using either partially sintered powder metallurgy (PM) tool electrodes, or by dispersing metallic powders in the dielectric. Several published papers detail the use of powders suspended in the dielectric as a means of producing surface alloying. This is an extension of work where powders, typically graphite, aluminium (Al) or silicon (Si), varying in size from 1-100 µm, are used to produce mirror-like EDM surfaces with minimal microcracking. Although deionised water can been used, the majority of current work uses hydrocarbon oil dielectrics (kerosene/paraffin), which produce carbides through carburisation with pyrolytic carbon. Problems Associated with Surface Alloying This approach is not without its problems despite the potential to increase workpiece hardness from 2-6.5 times that of the bulk material and produce recast layers of 10-150 µm thick. It is difficult to achieve a uniform distribution of the powder in suspension and filtration of the dielectric can be counter-productive. Electrode Materials Very little surface alloying occurs when using ‘conventional’ tool electrodes under standard polarity compared to partially sintered PM electrodes, where the binding energy between grains is considerably lower. Negative tool polarity is usually employed and PM electrode materials used include Al, Cr, Cr/Ni, Cu/Co, Cu/Mn, Cu/Sn, Cu/W, Ni, Ni/Co, Ni/Fe, Ni/Mn, Ni/Si, Ti, Ti/A1, TiC/Ni, W/CrC/Cu and WC/Co. Figure 1 shows a schematic of the process. This approach to surface alloying is relatively new and there is little information on aspects such as preferred particle size, sintering temperatures and pressures. However, powder sizes of less then 50 µm are quoted with temperatures of ~900-1300°C and pressures of ~100-550 MPa. 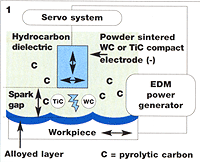 | Figure 1. Schematic of surface alloying with powder metallurgy electrodes. | Producing Wear and Corrosion Resistant Surfaces Current research at Birmingham involves the use of WC/Co and W/CrC/Cu partially sintered hardmetal tool electrodes for EDM surface alloying, together with non-standard wire materials to produce wear and corrosion resistant surfaces. One of the challenges of the research is to produce surfaces that are highly alloyed and have high wear resistance, but meet the surface roughness and topography requirements of the mouldmaking, die casting, rolling and aerospace industries. The effect of electrical parameters such as peak current, open circuit voltage, polarity, pulse on/off times and capacitance on recast layer thickness, and workpiece microstructure, microhardness and composition, are being evaluated. Much of the equipment being used is commercially available, with PM products manufactured by Vacuum Impregnated Products and standard hydrocarbon oil (paraffin) dielectric being used. However, in order to increase electrode wear (contrary to common practise where minimum wear is desirable) and achieve greater surface alloying, generators with higher than normal open circuit voltage - up to 300 V - are being used. The Effect of Open Circuit Voltage Work on tool and roll steels (AISI H13 hot work tool steel and 2% Cr steel) is being sponsored by the Engineering and Physical Sciences Research Council (EPSRC) in collaboration with Alcan, Charmilles, Dynacast, Erodex, The Gauge and Toolmaker’s Association (GTMA) and SparkTec International. Figure 2 gives a sample workpiece microstructure when die sinking AISI H13 heat treated to 600-640 HK0.025 using preferred operating parameter levels identified in a Taguchi fractional factorial experiment. Analysis of the machined surface revealed a 5-20 µm thick recast layer with some evidence of cracking and porosity Figure 3a shows the corresponding microhardness depth profile, while figure 3b illustrates the microhardness results from a test where all the parameters were the same except a lower open circuit voltage (125 V) was used. By comparison, the higher voltage caused microhardness at a depth of 5 µm to increase from 1,116 to 1,319 HK0.025. 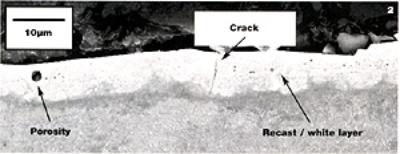 | Figure 2. Bottom surface microstructure of an AISI H13 die sunk cavity (270V). | 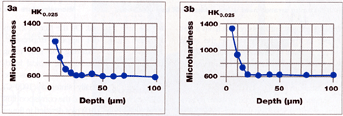 | Figure 3. Microhardness depth profiles for die sinking AISI H13 at (a) 270V and (b) 125V. | Production of Textured Rolls Surface alloying is also being used to produce textured rolls, see figure 4. Here, a PM tool electrode is used to scan along the axis of the rotating roll, while simultaneously moving normal to its surface due to the action of the DC servo system employed in order to maintain a constant spark gap. A number of texture bands can be seen, corresponding to tests made with varying operating parameter levels. The dielectric fluid, which normally floods the spark gap, has been switched off. Typically, the surface textures produced using the PM tool electrodes were very similar to the results obtained with conventional Cu/graphite and graphite electrodes. The Ra and peak count (Pc) values of the different texture bands were in the range of 2.1-2.4 gm and 113-121 peaks/cm, respectively. These values conform to the requirements needed to roll aluminium strip in the automotive industry. 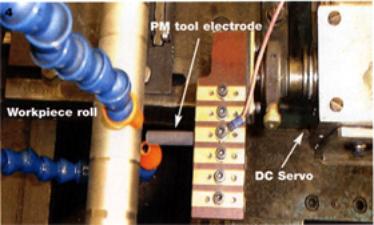 | Figure 4. Roll texturing arrangement using a single powder metallurgy tool electrode. | Hardness Increase Due to Surface Alloying A SEM of a typical roll cross section is given in figure 5, which shows a fairly uniform recast layer with a thickness of ~10 gm and a surface microhardness of 930 HK0.025 compared to 800-880 HK0.025 for the bulk material. On the face of it, this increase does not appear impressive. However, when texturing the rolls using conventional electrodes, the typical hardness is only 540 HK0.025 The roll was textured with a partially sintered (1000°C) WC/Co PM electrode and the corresponding X-ray diffraction (XRD) plot shows the presence of complex carbides in the recast layer. Currently, such surfaces are being evaluated using scratch and bi-directional wear tests in order to assess their performance when compared with textured surfaces employing a hard chromium plated layer. 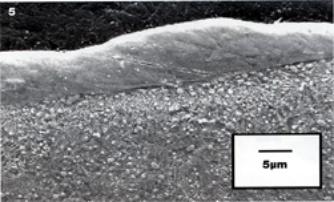 | Figure 5. Electron micrograph of the sample of the steel roll surface. | Surface Alloying of Titanium Alloys Universities UK, Rolls-Royce and Erodex are also supporting a parallel project on aerospace titanium alloys (Ti6Al4V and gamma TiAl). When EDM scanning Ti6Al4V using fully sintered WC/Co electrodes, 10-25 µm thick recast layers with high porosity have been observed. These contained cracks, which increased in density with negative tool polarity However, they did not penetrate into the bulk material. Surface microhardness values were extremely high, ranging from 600-2900 HK0.025 compared with 360 HK0.025 for the bulk material. Combining Powder and Powder Metallurgy Electrodes The application of powders and PM electrodes are not mutually exclusive and their simultaneous use offers the prospect for harder, more wear resistant surfaces with low roughness and minimal cracking. In general, the use of PM tool electrodes allows higher discharge energies than surface alloying with suspended powders, producing thicker recast layers (10-100 µm) and increased workpiece surface microhardness. Summary EDM surface alloying has the potential to open up new horizons but its take up in industry has been slow owing to the commercial availability of PM electrodes and the associated EDM technology. For example, current generator specifications (especially with regard to high open circuit voltage) are generally designed to minimise electrode wear and workpiece recast layers. This aspect will shortly be explored further at Birmingham with a new pulse generator capable of accommodating ultra high frequency discharges (1000 kHz) at up to 600 V. Work is also ongoing to evaluate the manufacture of PM electrodes via laser fabrication, which would allow the production of multi-element products with in-built dielectric flushing channels. While falling outside the scope of the majority of EDM users, the surface alloying approach, whether using solid electrodes or novel wires, will undoubtedly become established, albeit for specific applications. |