In this interview, AZoM talks to Sartorius and Anton Paar about battery cell development and the important role that weighing plays in this.
Does the format of the end product (battery cell) dictate what parameters are most important to characterize during the development process?
The battery cell's format (cylindrical, prismatic, pouch, or coin) and its intended use dictate what parameters and chemistries of the LIB are the most crucial during research and manufacturing.
Battery developers and manufacturers alike deal with the following trilemma: “High energy,” “Long life,” and “Fast charging.” These factors always compete with each other; for example, fast charging comes at the expense of cycle life, high energy cathodes can lead to faster degradation, therefore shorter battery life, and batteries with longer life, generally suffer from low energy density.
Thus, creating an “ultimate battery” is always an optimization of certain parameters at the expense of others based on the intended battery format and use.
For instance, a lithium-ion battery used in a cellphone does not need to last for several years as users tend to change their phone model once a year. Instead, in this case, having a fast-charging battery is more important.
Whereas the energy density, cycle life, and lifespan of a cylindrical battery cell are more important to electric vehicles as the end-user expects to drive long distances without frequently needing to charge the battery. Electric cars are also expected to be driven for several years before changing models.
Therefore, battery researchers and manufacturers design their batteries and pay specific attention to certain parameters of the battery material, bearing specific end-goals in mind.
What are some of the most important parameters to characterize in electrode material, whether in R&D or production?
Chemically, it is important to accurately measure the purity of the material being developed or used down to the parts per billion (ppb) level. Whether in electrode materials or electrolyte solutions, certain impurities at relatively high levels can be detrimental not only to the performance and the lifespan of the battery cell but also to its safety.
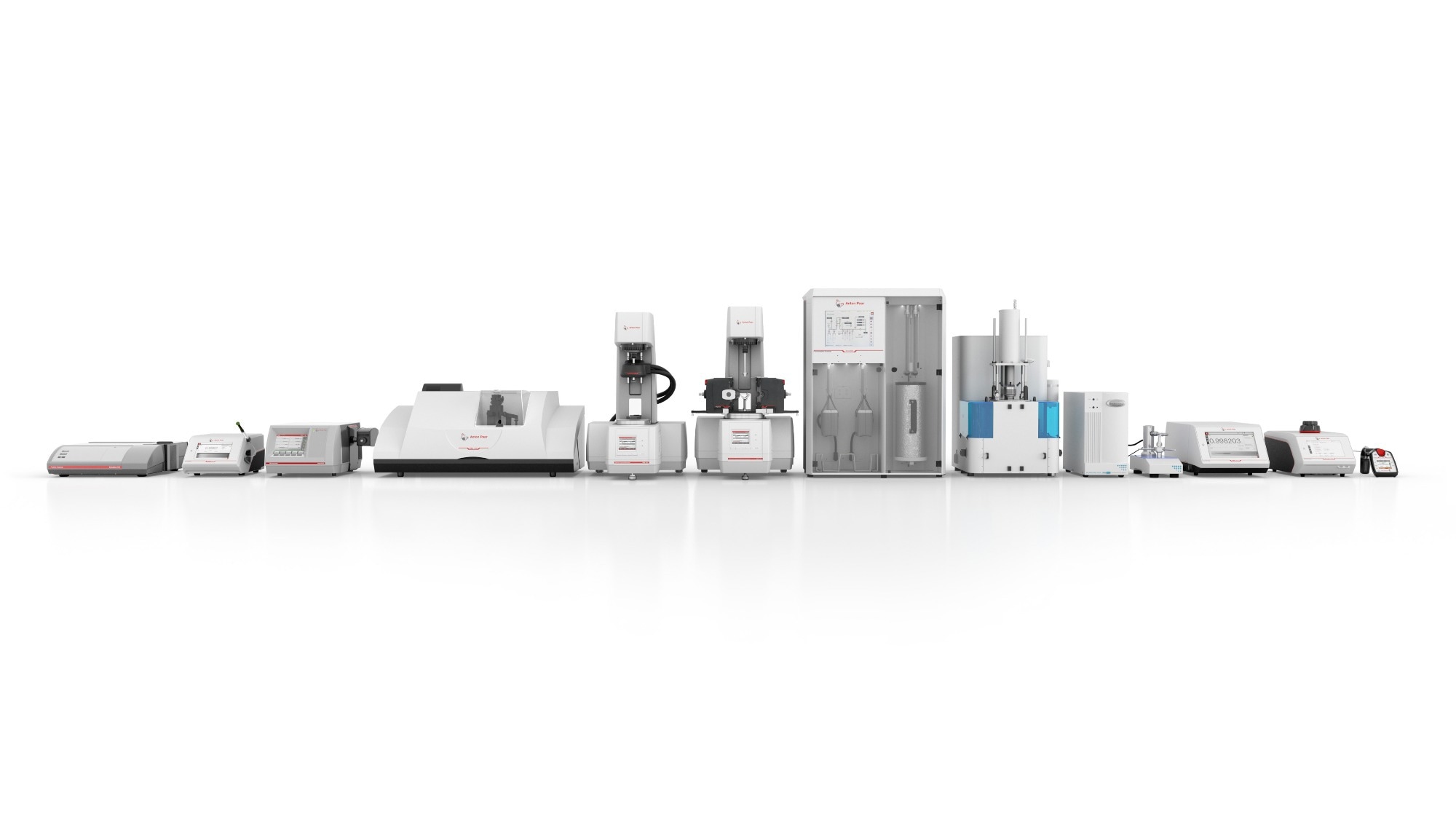
Image credit: Anton Paar GmbH
The analysis of material purity is usually done using Atomic Spectroscopy (AS) techniques such as Atomic Absorption (AA), Inductively Coupled Plasma Optical Emission Spectroscopy (ICP-OES), or Mass Spectrometry (ICPMS). Proper sample preparation, such as microwave-assisted acid digestion, is key to successful measurements in this case.
Some of the most important physical properties of electrode materials are:
- The specific surface area, or BET surface area, which is named after the three scientists, Brunauer, Emmett, and Teller, who developed this method. This parameter is measured by gas adsorption (or physisorption) of an inert gas at its boiling temperature; the most commonly used gas is liquid Nitrogen (at 77 K). The number of gas molecules adsorbed, forming a monolayer on the probing surface of the powder material, is measured in a specific relative pressure range (P/P0) and correlates with the specific surface area of this material. This parameter directly affects the energy density of the electrode material and, consequently, the battery cell itself.
- The solid density of the powder material. The skeletal density, measured by a technique called gas pycnometry, as well as the tapped density, calculated by measuring the volume of a known weight of a material after multiple taps, play an important role in the behavior of a material when mixed in solvents, and then coated onto a certain surface (in this case a current collector).
- Particle size, typically measured by laser diffraction, and particle shape are physical parameters that play an important role in active material behavior. For instance, the particle size distribution of a powder material needs to be optimized to maximize the effect of energy storage in a battery.
It is worth mentioning, too, that once the electrode powders are mixed in solvents (along with other additives and binders), it is very important to adequately measure 4) the rheological properties of that slurry, as this will determine the effectiveness of the mixing, the coating and the drying processes. Rotational rheometers are the most commonly used tools to measure these parameters.
There are several other physical characterization techniques that are relevant to battery researchers and manufacturers, but these are the most common and important ones.
What is the importance of weighing in the characterization of electrode materials?
As described by Anton Paar, accurate measurement of electrode purity is essential to ensure the performance, safety, and cyclability of rechargeable batteries. Whether for the determination of BET surface area, density, or moisture content, precise and error-free weighing is paramount. It is, therefore, crucial to overcome both the influence of environmental factors and the effects of static electricity.
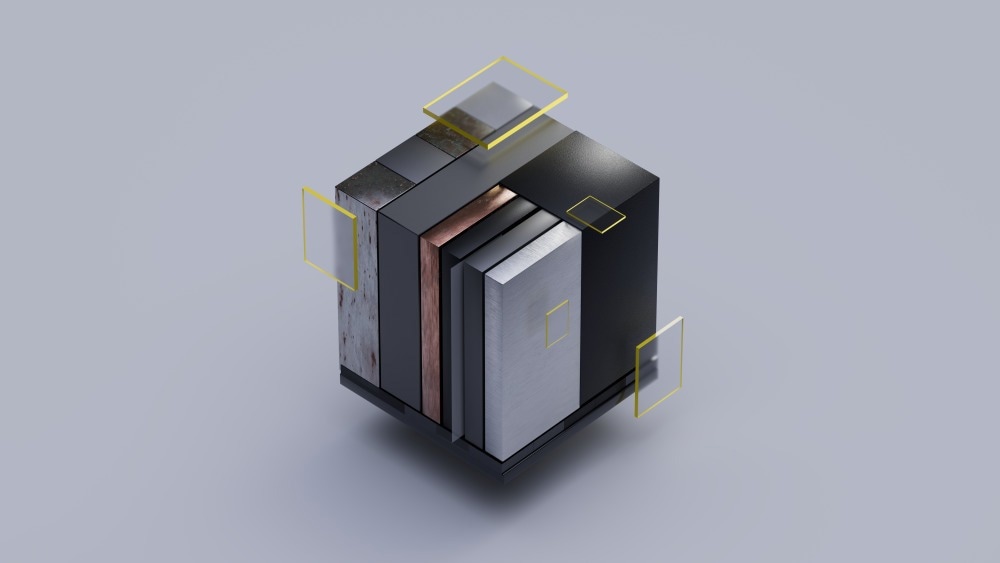
Image credit: Sartorius
What factors influence and cause weighing errors in electrode and general battery characterization?
Three main factors can influence the accuracy and precision of a lab balance:
- The specification of the balance itself: capacity, readability, repeatability, linearity, rounding error, off-center load, calibration
- The environmental influences: vibration, location, air drafts, humidity, inclination, inert gas atmosphere
- The effects from samples | vessels | users: magnetic effects, electrostatic charges, non-acclimatized samples, operator techniques, hygroscopic or volatile samples
How can Sartorius balances help with the optimization and the preparation of calibration curves for spectrometry, chromatography, spectroscopy, or titration?
External standards are separate samples used for comparison to test samples, whereas internal standards are added to the samples to be analyzed.
However, all standards have a defined concentration of one or several known component(s). The concentration of these standards must be as accurate as possible to prevent subsequent errors in determining unknown concentrations in samples.
The preparation of standards is also routine in analytical laboratories, and problems can occur when standards are manually prepared from soluble solids:
The required weight of the soluble component(s) is calculated based on the desired final component(s) concentration and the final solution volume. If the component weight does not precisely equal the calculated weight, the volume of the solvent has to be adjusted to reach the desired final concentration.
The Cubis® MCA software Standard preparation (QAPP001) is designed to eliminate the described problems. The system automatically guides the user through preparing standards, and the application software automatically handles all calculations in the background.
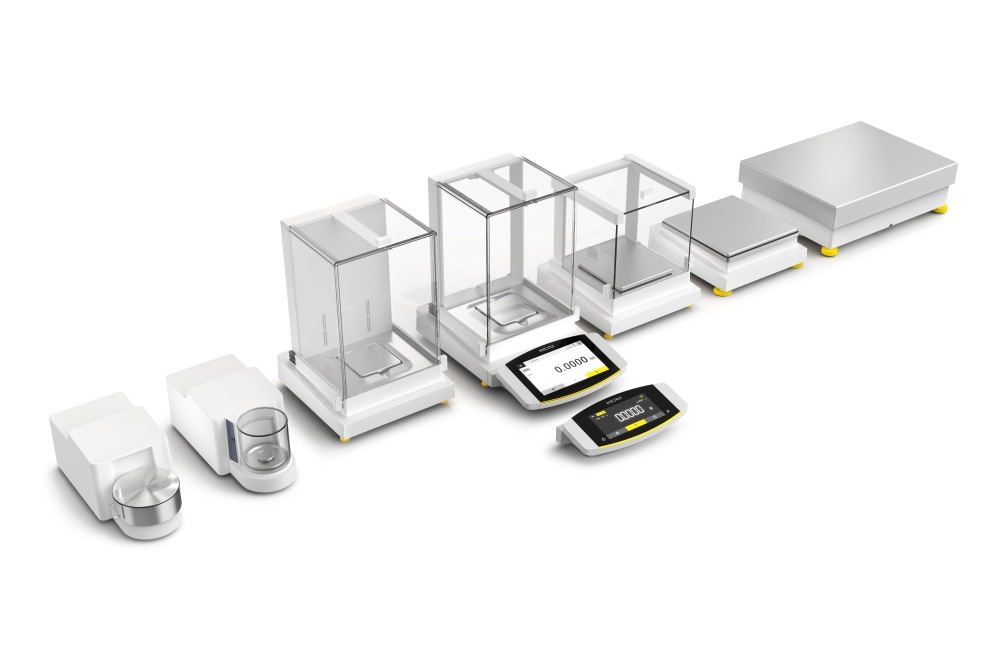
Image credit: Sartorius
There is no need to reach the target weight exactly as the software automatically calculates the required solvent volume based on the gravimetrically measured component(s) weight(s). After the user applies the solvent, the added weight is gravimetrically checked, and using this value, the verified concentration(s) and the verified volume of the standard prepared is calculated.
Also, weighing sample quantities at the milligram level requires a high-sensitivity instrument and skilled personnel. However, even a small spillover can lead to measurement inaccuracies due to residues left over on the weighing pan.
This is because although the balance correctly displays the total amount of sample, not all the sample is in the weighing boat or crucible. This causes immerse errors in the weighing results and negatively influences the outcome of the analysis.
The YSH48 Anti Spilling Weighing Pan fits to the Cubis® II Ultra-micro and Micro Balances. These balances offer up to 10 g capacity and 0.1 microgram readability.
Thanks to the minimized surface design, no residues are left on the weighing pan, which ensures reliable and high-accuracy measurement results.
Reference and Further Reading
Gravimetric Uniformity Checking - Rechargeable Batteries | Sartorius
About Mitesh Chhana
Mr. Mitesh Chhana is the Regional Business Manager for Lab Weighing (EMEA) at Sartorius. He has 15 years of commercial & technical experience in the Laboratory weighing industry, highly experienced in selling weighing & software solutions to laboratories where chemical analysis is required across all segments. The key to supporting customers is understanding challenges & pain points to offer appropriate products and technical solutions that are appropriate.
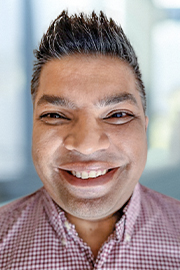
About Dr. Martin Thomas
Dr. Thomas, Anton Paar QuantaTec’s Lead Scientist, has more than forty years of experience in the characterization of powders and porous materials. He obtained his Ph.D. from the University of Birmingham (UK) for studies relating to the nickel hydroxide electrode. After a period of working in ceramics and catalyst characterization, he joined Quantachrome Instruments (Anton Paar QuantaTec since 2018) in 1991. He is named on 10 patents relating to porous materials and their characterization and is co-author of “Characterization of Porous Solids and Powders: Surface Area, Pore Size and Density” published by Springer
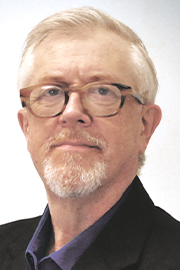
About Anthony Chalou
Anthony Chalou joined Anton Paar in April 2022 as a Global Market Development Manager for the battery industry. He has two Master’s degrees in Analytical Chemistry and Food Quality Management, and 18 years of experience in the analytical instrumentation industry in various capacities.
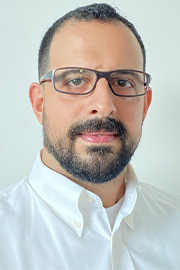
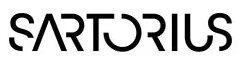
This information has been sourced, reviewed and adapted from materials provided by Sartorius Lab Instruments GmbH & Co. KG.
For more information on this source, please visit Sartorius Lab Instruments GmbH & Co. KG.
Disclaimer: The views expressed here are those of the interviewee and do not necessarily represent the views of AZoM.com Limited (T/A) AZoNetwork, the owner and operator of this website. This disclaimer forms part of the Terms and Conditions of use of this website.