The market for personal electric vehicles (EVs) was arguably non-existent a decade ago. Today, the transportation industry landscape looks very different and faces a future fueled by electricity. According to a recent report from the International Energy Agency, a total of 1.4 million cars registered in Europe in 2020 were electric, representing a 10% share of total vehicle sales.1
That figure in China and the US stood respectively at 6% and 2%. Several factors can be attributed to this significant growth in industry and the increased number of people buying EVs. These factors include government policies that can bolster alternative energy technologies, as well as the greater range and power of new EV models.
Lithium-ion (Li-ion) batteries are driving the EV revolution. This electrochemical cell is a powerhouse of a battery, which consists of anode and cathode materials that are supported by an electrolyte often containing lithium hexafluorophosphate (LiPF6) with a mixture of organic carbonate solvents, charge-carrying electrodes, and a separator.
This separator permits the migration of lithium ions between the anode and cathode during the process of battery charge and discharge. The past 20 years have wrought engineering improvements that have boosted the energy density of a cell, ensuring an ever-smaller container can contain more energy.
Combined with automated techniques for precision mass manufacturing, these design improvements have been behind the prices of Li-ion batteries dropping 89% over the past ten years.2
The production of Li-ion batteries for EVs has introduced new demands for manufacturers, even though the manufacturing process for Li-ion batteries destined for small consumer electronics is well established.3
Marc Locke, chair for production engineering of e-mobility components at RWTH Aachen University, notes that although equipment and workflows are similar, “automotive cells do require higher quality batteries and controls than smaller devices do”.
Hundreds of individual cells wired together make up a single EV lithium-ion battery pack. Precision is essential and just one flaw in a single cell has the potential to reduce performance and cause internal short circuits, which could lead to an ignition of a battery’s flammable electrolyte.
Andrew Jansen, a chemical engineer and group lead for the Cell Analysis, Modeling, and Prototyping (CAMP) Facility at Argonne National Laboratory, commented: “Internal shorts in cells are what keep battery engineers up at night. It is a tremendous amount of energy in a little space.”
Battery manufacturing processes need to meet narrow precision thresholds and incorporate quality control analyses that are compatible with a high-throughput, automated production line to ensure that Li-ion batteries for EVs fulfill safety and performance requirements. Quality control during production is key for success, and it takes days to get a battery in a workable state to undertake these performance tests.
Meeting the Quality Control Challenge
Manufacturing Li-ion batteries requires three general stages, each of which comprises several individual steps. These manufacturing steps have almost no room for error. For example, the standard tolerances for the thickness of electrode film might be as small as ±2 μm.3
EV lithium-ion battery production lines are largely automated to achieve such narrow thresholds. To assess quality and achieve precision, these automations incorporate a suite of analytical instruments on a production line and measurements performed after production.
In addition to providing sufficient accuracy, tools used on such production lines must be sufficiently robust and highly responsive to tolerate the fast speed of a production line, according to Junkichi Azuma, a manager of industrial applications at Sartorius. These systems, like the manufacturing process itself, are fully automated and therefore equipped to provide responsive control over manufacturing stages or recognize quality defects.
Performance checks, such as monitoring for stable voltage output, can only be tested after a battery cell is fully assembled.
Preparing the Electrodes
Preparing each electrode, called the anode and the cathode, is the first stage of producing Li-ion batteries.
Separate mixing takes the place of the slurries of the anode and cathode components. Generally, the anode slurry contains polymeric binders, other additives, and purified water as the solvent, along with graphite as the anodic material.
The cathode slurry usually contains a layered oxide material comprising cobalt, nickel, and manganese (NMC) for EV lithium-ion batteries.
An N-methyl pyrrolidinone (NMP) solvent is used to disperse the NMC oxide with binders and additives.
A production line is used, through which long sheets of copper and aluminum foils are fed. The electrode slurries are deposited as thin films on the foil sheets. For the anode and cathode, respectively, the conductive copper and aluminum foils serve as the current collectors.3
The films are dried after the coating step, using a heating gradient that minimizes cracking, flaking, and other deformations on the films. 3, 4
In a process called calendaring, the sheets are then passed through heavy rollers. To achieve optimal porosity for the active electrodes, this step compresses the dried films.
For several hours, the sheets are then transferred to a vacuum drying room to remove any remaining moisture. For this part of the process, typical production line speeds can reach 50 m/min.3
Quality Control: Optical Inspection
The main method of quality control for the electrodes is visual inspection.
Given the speed at which electrode assembly occurs, human inspection is not feasible.
Locke comments: “The most common thing to do is to conduct visual inspections with camera systems and line detection devices”.
Optical cameras, for instance, can inspect electrode films to identify whether there are any macroscopic defects, such as cracks and irregular geometries at the edge of the films.
Such optical tools, according to Locke, feature computers with algorithms that can flag these defects. Furthermore, X-Ray imaging can monitor whether the anode and cathode films are precisely aligned with one another in a cell during assembly.

To keep up with the speed of battery production lines, cameras and line detection devices optically inspect lithium-ion batteries during component production and battery cell assembly. Image Credit: u3d / Shutterstock.com
Download the full paper
References
- International Energy Agency, Global EV Outlook 2021, April 2021, https:// www.iea.org/reports/global-ev-outlook-2021.
- BloombergNEF, “Battery Pack Prices Cited Below $100/kWh for the First Time in 2020, while Market Average Sits at $137/kWh,” (Dec. 16, 2020), https:// about.bnef.com/blog/battery-pack-prices-cited-below-100-kwh-for-the-first-time-in-2020-while-market-average-sits-at-137-kwh/.
- Arno Kwade et al., “Current Status and Challenges for Automotive Battery Production Technologies,” Nat. Energy 3 (April 2018): 290–300, https://www.nature.com/articles/s41560-018-0130-3
- W. Blake Hawley et al., “Electrode Manufacturing for Lithium-Ion Batteries—Analysis of Current and Next Generation Processing,” J. Energy Storage 25 (Oct. 2019): 100862, https://doi.org/10.1016/j.est.2019.100862.
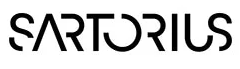
This information has been sourced, reviewed and adapted from materials provided by Sartorius Lab Instruments GmbH & Co. KG.
For more information on this source, please visit Sartorius Lab Instruments GmbH & Co. KG.