Analyzing particle size and shape is essential for understanding metallic powder behavior during processes such as sintering, compaction, and filling. This article will discuss techniques used in particle analysis and why this field is so important for multiple industries.
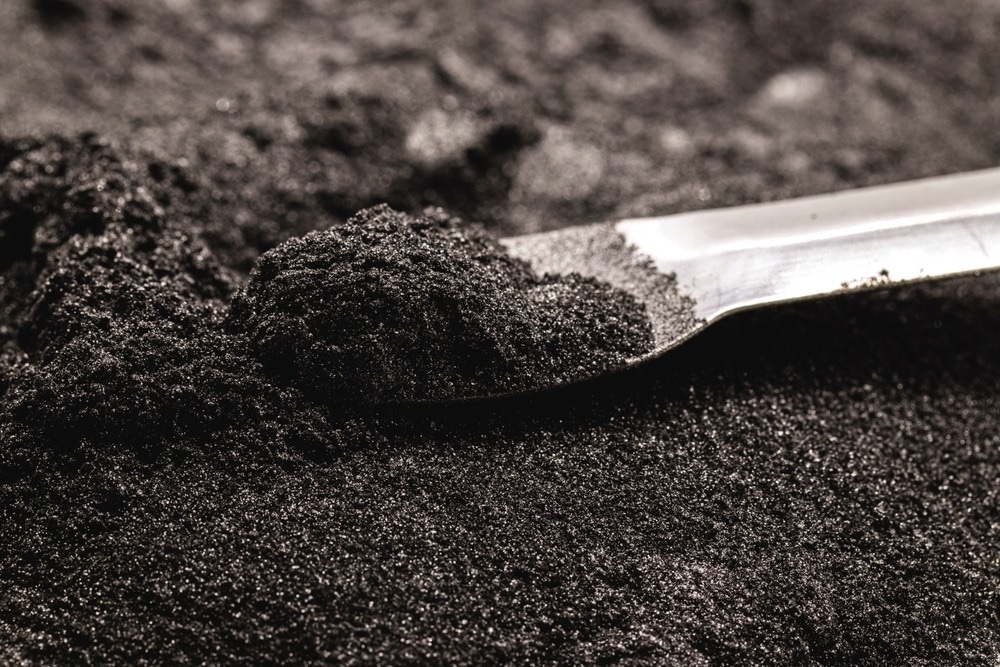
Image Credit: RHJPhtotos/Shutterstock.com
The Importance of Metal Powder Size and Shape Distribution
Metal powders are used to produce a variety of industrial parts and products. A number of techniques are used to manufacture parts from metal powders, with two popular techniques being sintering and injection molding.
Powder behavior during parts manufacturing is affected by particle shape and distribution, which in turn impacts the physical properties of products. Powder shape is incredibly important, with spherical particles preferred due to their improved flowability and compaction.
The study of metal powder characteristics and behaviors is known as powder metallurgy. Inter-particle friction, which impacts powder compaction and flow, is reduced by larger spherical metal powder particles, making them the optimal choice for parts manufacture.
Whilst nanoscale particles exhibit enhanced strength and hardness, they are expensive. If particles are too large, the performance of parts can be impacted with very little cost benefit. For this reason, metal powder particles with diameters of 0.8 – 3.0 µm are preferred as they represent the best cost-benefit ratio.
How are Metal Powders Produced?
Atomization is a commonly used method for creating metal powder particles. In this process, the raw material is melted and broken to produce small particles. A furnace is used to melt the material, which then flows into a tundish and finally into the atomization chamber under constant flow.
Fine metal droplets solidify in the atomization chamber and are then subject to electrolysis, which removes any impurities and covers the cathode with powdered metal, which is then washed and dried.
Various chemical reactions are employed in the manufacturing process to reduce the metals into elemental powders. Finally, mechanical comminution produces metal powder particles in the desired size range. The powder can then be used to produce industrial parts.
Particle Characterization Methods
Various techniques are used to characterize metal powders. These include sieves, laser diffraction, optical and electron microscopy, and aerodynamic time of flight methods. Laser diffraction is the most popular analytical technique in use currently in the field of powder metallurgy.
Laser diffraction provides a number of benefits for analytical scientists, such as improved ease of use, rapid measurement capabilities, and enhanced cost benefits due to a better ROI.
Automated optical microscopy provides some advantages over laser diffraction analysis. The main advantage is that this method can characterize the shape of micronized metal powders. Commercially available automated image analyzers can easily classify material grades according to particle shape.
Powder Metallurgy and Additive Manufacturing
Characterizing the shape and size distribution of metal powder particles is incredibly important for the field of additive manufacturing (3D printing) as the flow characteristics of materials can significantly impact the printing process and final product quality.
In additive manufacturing, it is vital to precisely match powder properties to specific machines, thereby ensuring consistent production. Metal powders can be processed in additive manufacturing by techniques such as binder jetting, selective laser sintering, and electron-beam powder-bed fusion.
Whilst the selection of additive manufacturing technology leads to different qualitative properties in finished products, characterizing the metal powder is highly important. Flowability, chemical composition, optical properties, particle size, and thermophysical properties are critical material parameters.
Much like conventional parts manufacturing processes, particle sphericity is highly desirable in 3D printing. Whilst irregularly shaped particles can improve green strength, flowability is a critical behavior that affects the final properties of a 3D-printed part.
Size distribution of metal powder particles employed in additive manufacturing is another key parameter. Wide size distribution can negatively impact shrinkage, densification, and packing behaviors. Furthermore, studies have shown that the sintering behavior of complex biomedical parts can be affected by this parameter.
One key powder characteristic in the field of 3D printing is its tap density, which influences the random dense packing of a powder. If the tap density is sufficient, the powder layers are packed better, and optimal green density is achieved. Conversely, high porosity leads to undesirable shrinkage and issues with final product density.
In Summary
Several key material properties can affect the final quality of parts, whether they are produced by conventional subtractive manufacturing methods or the emerging field of additive manufacturing. Metal powders are an essential raw material in many manufacturing techniques in multiple industries.
Two of the most important physical parameters in metal powders are their shape and size distribution, with optimal sphericity and particle density significantly improving the flowability characteristics of powders. Consequently, this enhanced flowability leads to minimal problems during parts production.
Therefore, it is crucial that process engineers and scientists accurately characterize the physical parameters of metal powders during parts production by employing a variety of analytical techniques such as laser diffraction, automated optical microscopy, and physical inspection methods.
More from AZoM: How Does Dynamic Light Scattering Contribute to Particle Analysis?
References and Further Reading
Zegzulka, J et al. (2020) Characterization and flowability methods for metal powders Nature Scientific Reports 10, 21004 [online] nature.com. Available at:
https://www.nature.com/articles/s41598-020-77974-3
Slotwinski, J.A et al. (2014) Characterization of Metal Powders Used for Additive Manufacturing Journal of Research of the National Institute of Standards and Technology 119 [online] nvlpubs.nist.gov. Available at:
http://dx.doi.org/10.6028/jres.119.018
Horiba (2008) Particle Size and Shape Analysis of Powdered Metals [application note] horiba.com. Available at:
https://static.horiba.com/fileadmin/Horiba/Application/Materials/Nonferrous_Metals/Powdered_Metals.pd
Disclaimer: The views expressed here are those of the author expressed in their private capacity and do not necessarily represent the views of AZoM.com Limited T/A AZoNetwork the owner and operator of this website. This disclaimer forms part of the Terms and conditions of use of this website.