Epoxy powder coatings provide various properties determined by the choice of epoxy resin, curing agent, and curing schedule. Typical advantages include high-temperature durability, dielectric strength, and resistance to chemicals.
Dianhydrides represent a unique category of curatives enabling high-temperature performance when paired with uncomplicated solid epoxy resins (SERs) based on bisphenol A.
This article will introduce dianhydrides, particularly BTDA® (benzophenone tetracarboxylic dianhydride), and their suitability for epoxy powder coatings with elevated glass-transition temperatures (Tg).
It will also share findings from a collaborative study exploring the development of high Tg BTDA-epoxy formulations, considering variables such as resin EEW, formulation stoichiometry, and cure profiles.
Author Bios
Vinay Mishra is the Technical Director for Thermoset Additives at Jayhawk, boasting 25 years of experience in epoxy and thermoset applications with a Ph.D. in Chemical Engineering from Lehigh University. Contact Vinay Mishra at [email protected] for more information.
Kevin Biller is President at ChemQuest Powder Coating Research, a division of the ChemQuest Group located in Columbus, OH. For inquiries, contact Kevin at [email protected].
Jeff Dimmit, Vice President of Technology at Jayhawk, possesses over 30 years of industrial chemistry experience and holds a Ph.D. in Chemical Engineering from the University of New Hampshire.
Nikola Bilic is a Senior Scientist at the Kansas Polymer Research Center, affiliated with Pittsburg State University, Kansas, and brings over 15 years of experience in polymer research. He holds an MS in Chemistry and an MBA from Pittsburg State University.
Introduction
Epoxy-based products find application in numerous scenarios facing demanding operating conditions. Examples (Figure 1) encompass electrically insulative encapsulants or powder coatings (e.g., within electrical motors), chemical-resistant pipe linings, adhesives, and composite components.
Under severe service conditions involving heat, chemical exposure, and mechanical stresses, traditional epoxy formulations often deteriorate over time.
Conventional solutions necessitate shifting from epoxy to alternative chemistries like cyanate ester, bismaleimide, and polyimides. While effective, this transition can introduce complexity and raise costs.
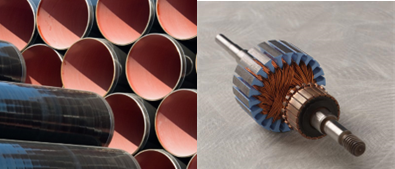
Figure 1. Among other applications, dianhydride curatives are used in long-lasting epoxy powder coatings for pipes and as electrical insulation coatings in motors (see blue coating in the rotor above). Source: Jayhawk Fine Chemicals Corporation
Aromatic dianhydrides, like BTDA® (3,3’,4,4’-benzophenone tetracarboxylic dianhydride), have a well-known capacity to instill high crosslinking densities in epoxy formulations.1,2 Refer to Table 1 for specific molecule details and Figure 2 for its chemical structure.
The resulting dense crosslinking, combined with the structure of BTDA linkages, leads to epoxy powder coatings exhibiting elevated glass-transition temperatures and resistance to heat.
These formulations offer superior dielectric and mechanical properties, along with chemical resistance. Consequently, BTDA-based powder coatings find utility in demanding environments such as high temperatures, chemical exposure, and long-term electrical applications.
Such achievements are attainable using simple, bisphenol-A-based solid epoxy resins (Figure 2). While specialized resins like epoxy novolacs and other multifunctional resins can enhance performance, they are not mandatory when employing a dianhydride curing agent.
Table 1. Chemical & Physical Characteristics of JAYHAWK BTDA®. Source: Jayhawk Fine Chemicals Corporation
Chemical Name: |
3,3’, 4,4’-benzophenone tetracarboxylic dianhydride |
Molecular Wt. (MW) |
322 g/mole |
Anhydride Equiv. Wt. (AEW) |
161 g/equiv. |
Physical Form |
Off-white fine powder |
Specific Gravity |
1.6 |
Melt point in pure state |
220-230 °C (will dissolve in and react with epoxy resin at lower temperatures) |
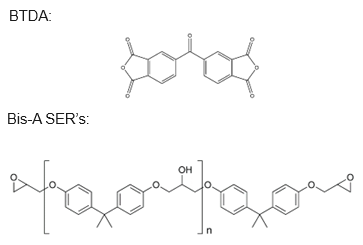
Figure 2. Chemical structures of 3,3’,4.4’-benzophenone tetracarboxylic dianhydride (BTDA) and simple solid epoxy resins based on bisphenol A. Image Credit: Jayhawk Fine Chemicals Corporation
A Note on Proper Stoichiometric Treatment of Dianhydride-Epoxy Formulations
Several factors need to be considered to ensure the correct design of dianhydride-epoxy formulations. Dianhydrides facilitate the curing of epoxy formulations by forming highly interconnected structures through esterification reactions.
An in-depth examination of the intricate reaction mechanism is beyond the scope of this article.3-6 Figure 3 illustrates a simplified two-step esterification reaction model adopted by the epoxy industry.
In the overall esterification reaction, one epoxide group reacts with one anhydride group. This suggests that the stoichiometric ratio of anhydride to epoxide groups (A/E ratio) should be 1.0.
However, for most dianhydride-epoxy formulations, especially those used in powder coatings, the optimal A/E ratios are considerably lower, typically falling between 0.65 and 0.80. Two primary reasons support this choice.
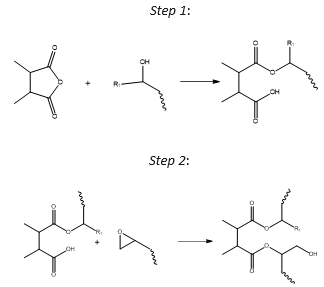
Figure 3. A simplified two-step cure mechanism for the esterification reaction between epoxides and anhydride groups which leads to crosslinking. Image Credit: Jayhawk Fine Chemicals Corporation
The first reason is that an A/E ratio <1.0 helps to counteract the side-reaction of epoxy etherification, also known as homopolymerization. This reaction can consume epoxides without involving anhydride groups.7 Refer to Figure 4.
This is a well-established practice, particularly in epoxy formulations employing mono-anhydrides like MTHPA, where A/E ratios in the range of 0.90 to 0.96 are common. This approach minimizes the presence of residual anhydride groups after the curing process while optimizing properties such as Tg and others.
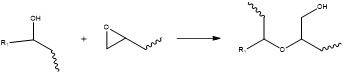
Figure 4. Epoxy etherification (homopolymerization), a side reaction that can consume epoxide functional groups without using up anhydrides. Image Credit: Jayhawk Fine Chemicals Corporation
Dianhydrides introduce a second critical consideration due to the exceptionally high levels of crosslinking they induce. When used near stoichiometric proportions, formulations may solidify prematurely before complete curing, trapping unreacted functional groups, which is undesirable for long-term performance.
While it is true that post-curing at elevated temperatures can achieve full cure, in many instances, the resulting crosslink density may be excessive for the intended application, leading to suboptimal performance.
Therefore, in the context of epoxy powder coatings, dianhydride usage should be maintained well below stoichiometric levels, typically within A/E ratios ranging from 0.65 to 0.80. Any surplus epoxide groups in the formulation will be consumed through etherification side reactions (epoxy homopolymerization).
This approach helps prevent excessive crosslinking while enhancing performance. Determining the optimum A/E ratio for a specific application is best accomplished through experimentation, with the suggestions provided in Table 2 serving as a useful starting point.
Table 2. Suggested ranges for anhydride/epoxide equivalent ratio (A/E ratio) for BTDA-cured epoxy formulations, based on resin epoxy equivalent weight (EEW). Source: Jayhawk Fine Chemicals Corporation
Epoxy Resin EEW
g/(equiv. of epoxide) |
Suggested equivalent ratio of BTDA:
[anhydride/epoxide] ratio (A/E) |
200 – 500 |
0.5 – 0.7 |
500 – 800 |
0.6 – 0.8 |
> 800 |
0.7 – 1.0 |
Example Applications
Dianhydride-cured epoxy powder coatings have a long history of serving demanding industrial applications. For instance, epoxy powder coatings based on BTDA find extensive use in electrical applications.
They effectively insulate the surfaces of stators and rotors inside electric motors, ensuring uninterrupted service throughout the motor's lifespan. These motors typically operate semi-continuously under high-temperature conditions, either due to the steady flow of electric current or their service environment, such as the under-hood of an automobile.
Other applications involve high-performance pipe coatings, where the substantial crosslinking achieved by BTDA-epoxy powder coatings provides a combination of heat and chemical resistance.
An analogous application of epoxy molding powders is the encapsulation of sensitive electrical components, often in semi-continuous, high-temperature environments found under the hood of an automobile. Although this last example is not a coating, these products employ the same formulation technology as powder coatings.
A Technical Exploration of BTDA-Based Epoxy Powder Coatings
The study aimed to gain a deeper understanding of the factors contributing to the distinct performance of BTDA-epoxy formulations. The objective was to establish connections between crucial elements, such as formulation variables and curing parameters, and the glass transition temperature (Tg) achieved in model BTDA-epoxy powder coatings.
It was presupposed that, within a similar range of formulations, the degree of crosslinking achieved and the resulting properties are directly associated with the obtained Tg values.
Materials and Processing
Solid epoxy resins based on Bisphenol-A (SERs) were generously supplied by Olin Epoxy. Three grades were employed in this study: D.E.R.TM 6224 (EEW 675-725, a 2.5-Type resin), D.E.R. 664UE (EEW 860-930, a 4-Type resin), and D.E.R. 667E (EEW 1600-1950, a 7-Type resin).
The intention was to encompass a spectrum of epoxy equivalent weights (EEWs) in this investigation.
Jayhawk Fine Chemicals Corporation provided BTDA® Polymer Fine, while Evonik Corporation furnished a commercial sample of the catalyst Imicure® AMI-2 (2-methylimidazole). Other materials, including pigments and additives, were procured from their respective producers or distributors (see Table 3).
A formulation matrix was devised for this study, employing four stoichiometric ratios of BTDA for each of the three epoxy resins (as detailed in Table 3). These model formulations were intentionally kept straightforward, primarily focusing on Tg development.
Compounding was executed using a twin-screw extruder, with an estimated residence time of under 15 seconds. The barrel temperatures needed for proper compounding were approximately 5 °C higher than the epoxy resin's softening temperature.
The resulting extrudate was cooled, ground into powder form, and sieved through a 140-mesh screen. Powder formulations were subsequently spray-applied onto Q-panels at 50-60 µm thickness and then cured in an oven for 20 minutes at 200 °C.
Table 3. Formulation matrix and raw materials. Source: Jayhawk Fine Chemicals Corporation
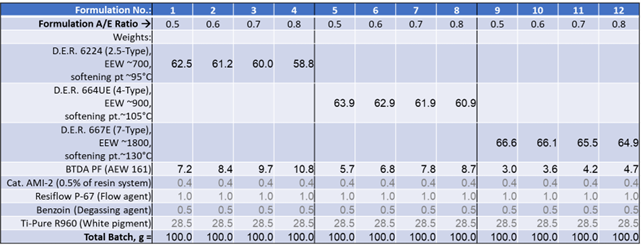
A/E ratio: Ratio of anhydride/epoxide functional groups in the formulation
BTDA PF: BTDA Polymer Fine, from Jayhawk Fine Chemicals Corporation
D.E.R.: Solid epoxy resins from Olin Epoxy
Cat. AMI-2: Imicure AMI-2 (2-methylimidazole), cure catalyst/accelerator, Evonik Crosslinkers
Ti-Pure R960: Titanium dioxide, The Chemours Company
Resiflow P-67: Flow agent, Estron Chemical
Characterization
To assess the properties of cured film specimens, thermal analysis was performed using a differential scanning calorimeter (DSC Q100, TA Instruments) to measure their glass transition temperatures (Tg) and detect any remaining curing.
Uncured powder formulations were subjected to thermal ramps or isothermal curing processes, followed by analysis in the DSC to determine the resulting Tg values.
A selection of powder formulations was also evaluated using dynamic mechanical analysis (DMA Q800, TA Instruments) to comprehend shear modulus behavior concerning temperature and ascertain Tg.
Results and Discussion
DSC thermograms of formulations simply cured for 20 minutes at 200 °C revealed Tg values of approximately ~105 °C ± 15 °C, depending on the resin used and the A/E ratio applied. However, these specimens also exhibited a significant exothermic reaction above the Tg, indicating incomplete curing.
To gain a more comprehensive understanding of crosslinking and Tg development, various curing experiments were conducted on uncured powders, followed by DSC scans to determine Tg, as depicted in Figure 5, which combines several thermograms for a specific formulation (No. 3 in Table 3), subjected to different curing conditions.
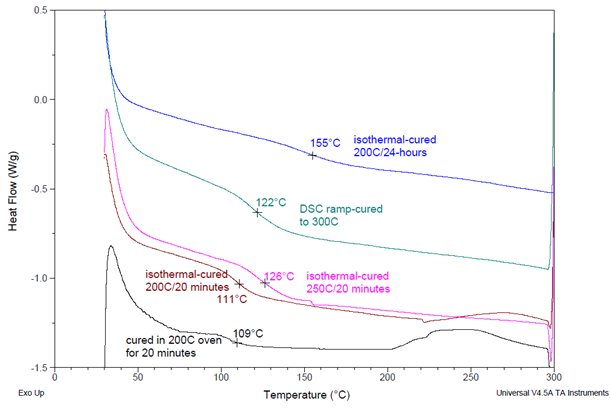
Figure 5. DSC thermograms showing Tg’s (as marked) for the same formulation when cured under different conditions. Formulation #3 from Table 3 using DER 6224 resin and BTDA at A/E = 0.7. Image Credit: Jayhawk Fine Chemicals Corporation
Commencing with the lowest curve in the image, the specimen that underwent isothermal curing at 200 °C (in an oven) for 20 minutes exhibited Tg of 109 °C. A similarly treated specimen with isothermal curing within the DSC cell displayed a similar Tg of 111 °C.
Both of these thermograms indicate a remaining exothermic reaction, implying incomplete curing of the specimens.
After subjecting them to isothermal curing at 250 °C for 20 minutes, the resulting Tg increased to 126 °C. A comparable outcome (Tg of 122 °C) was achieved with a specimen cured through a thermal ramp (heating from 30 to 300 °C at a rate of 10 °C per minute).
These two thermograms do not exhibit any residual exothermic reactions and demonstrate higher Tg values. These observations point to complete curing in these two specimens, as anticipated due to the higher temperatures employed during their curing processes.
However, the blue curve illustrates an even higher Tg of 155 °C, achieved after an extended 24-hour isothermal cure at 200 °C. This specimen also exhibits a faint Tg, indicating that its specific heat does not change dramatically during the transition as is typically observed in polymers.
This suggests a substantial level of crosslinking, which has a significant impact on specific heat and other properties at temperatures above the Tg. These observations are consistent with reports in the literature, which indicate that at high levels of crosslinking, the Tg increases while the transition intensity is diminished.8
Some formulations cured under the same conditions (24 hours at 200 °C) did not exhibit Tg values via DSC, as depicted in Figure 6.
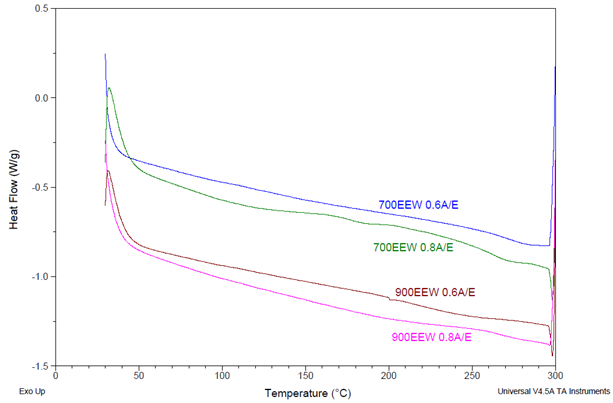
Figure 6. DSC thermograms showing Tgs (as marked) for other formulations cured 24 h/200 °C. Formulation details noted as resin EEW and BTDA usage A/E ratio. Most scans do not show a Tg where anticipated. Image Credit: Jayhawk Fine Chemicals Corporation
DMA analysis (in shear mode) was conducted on three formulations derived from the D.E.R. 6224 resin (700 EEW) to ascertain these missing Tg values better.
Figure 7 displays the complex shear modulus behavior in relation to temperature for these specimens. Notably, the modulus experiences relatively minor decreases during the transitions, only about one order of magnitude, as opposed to the expected two orders typically seen in cross-linked epoxy networks.
The relatively elevated position of the rubber plateau in these curves once again suggests a very high degree of cross-linking.9
Figure 8 illustrates the loss tangent (tanδ) peaks, indicating the Tg values for these specimens. As anticipated, higher A/E ratios (BTDA usage) result in higher Tg values. For optimal performance, the data imply that an A/E ratio of 0.7 is a promising choice, as further increasing it to A/E 0.8 yields only a modest Tg gain (from 164 °C to 170 °C).
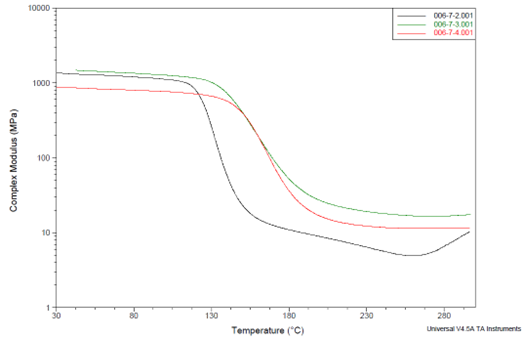
Figure 7. DMA data showing complex shear modulus vs temperature for formulations made from solid epoxy resin (700 EEW). BTDA usage is indicated as A/E ratios. Image Credit: Jayhawk Fine Chemicals Corporation
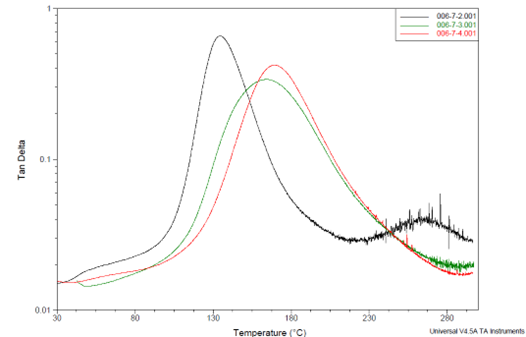
Figure 8. DMA data from shear modulus measurements showing tanδ peaks as Tg’s for formulations made from solid epoxy resin (700 EEW). BTDA usage is indicated as A/E ratios. Image Credit: Jayhawk Fine Chemicals Corporation
Although specimens cured for 24 hours at 200 °C yielded the highest Tg values in this study, not all formulations underwent testing under this curing profile. Nevertheless, the other curing profiles proved valuable for broad comparisons of Tg data in relation to epoxy EEWs and A/E ratios, as shown in Figure 9.
As expected, increasing the A/E ratio (BTDA usage) consistently elevates the Tg. It is also evident that employing a higher EEW resin, specifically with an EEW of 900, lowers the Tg compared to the 700 EEW resin.
This is rationalized by the longer molecular chain of the higher EEW resin, which somewhat reduces the average crosslink density and consequently softens the cured network. It should be noted that data from the lowest A/E ratio (0.5) and the third resin (1800 EEW) are omitted from this chart for simplicity, but similar trends were observed.
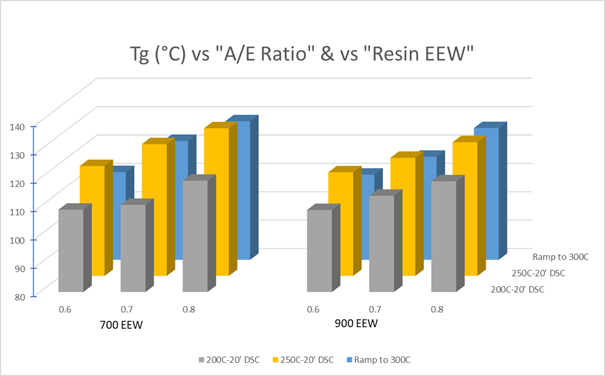
Figure 9. DSC Tg data for the 700- & 900-EEW resins at different A/E ratios are noted on the x-axis. Cure profiles used are indicated on the z-axis. Image Credit: Jayhawk Fine Chemicals Corporation
A DSC experiment was conducted to simulate the cure of a thinly coated panel placed in an oven at 200 °C for 24 hours. The objective was to comprehend how the degree of curing changes over time. As shown in Figure 10, the curing exotherm is entirely overshadowed by the strong exotherm from the rapid heating rate of 100 °C/min.
The exothermic reaction indicating curing is discernible only around the five-minute mark, which coincides with the conclusion of the heating phase.
The rest of the thermogram exhibits a steady heat flow, signifying that the thermally measurable curing is completed within a minute of reaching the target temperature of 200 °C. The noted increase in Tg with prolonged curing times at 200 °C suggests that gradual crosslinking reactions persist over time.
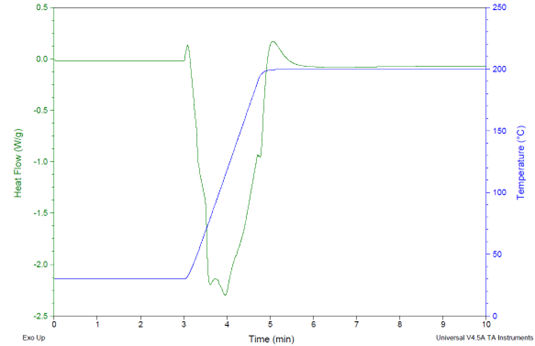
Figure 10. DSC thermograms on a sample, cured in the DSC cell via a heating ramp of 100 °C/min. from 30° to 200 °C followed by a 200 °C hold for 24 h. The cure exotherm (to be pointed upwards) is overshadowed by the strong endotherm (pointed downwards) from rapid heating, with only the tail end of the exotherm visible at the end of the heating ramp. Formulation: #3 from Table 3, using 700 EEW resin and BTDA usage at A/E = 0.7. Image Credit: Jayhawk Fine Chemicals Corporation
Based on the above observations and measurements of certain coating application characteristics, an overarching summary of performance concerning formulation or process variables is outlined in Table 4.
Ongoing efforts are in progress to expand upon this table, providing valuable guidance for formulators employing BTDA as a curing agent in epoxy coatings.
Table 4. Qualitative Summary of Performance vs. Formulation and Process Variables. Source: Jayhawk Fine Chemicals Corporation
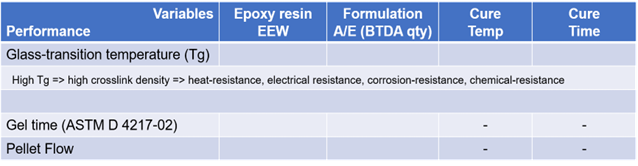
Conclusions and Summary
Dianhydrides, exemplified by BTDA, impart notably high levels of crosslinking in epoxy powder coatings. This results in remarkably elevated Tg values, even when using basic bisphenol-A-based solid epoxy resins (SERs), without necessitating the use of more complex epoxy resins like Novolacs.
Achieving Tg values as high as 170 °C was observed using a basic SER with an epoxy equivalent weight (EEW) of 700 (Type 2.5) in conjunction with BTDA. Optimal performance is attained by reducing BTDA's utilization to stoichiometric ratios ranging from 0.6 to 0.8.
Although higher A/E ratios can maximize Tg and properties linked to crosslink density, this research indicates that an A/E ratio 0.7 serves as a suitable starting point for standard SERs.
Under isothermal curing conditions, gradual reactions persist, enhancing crosslink densities over 24 hours, ultimately elevating Tg. The comprehensive data suggests that while high temperatures can achieve these elevated crosslink densities, extended curing times may play a more substantial role.
Future Work
Further investigations are underway to understand better model formulations based on BTDA and standard solid epoxy resins. The subsequent phase will reduce curing times and temperatures to maximize crosslinking and Tg values.
This work will also aim to optimize formulations with respect to performance and handling characteristics, such as gel time, pellet flow, and film appearance. The finer particle size of BTDA will be explored to compare and contrast with the grade used in this study.
Acknowledgments
The authors express their gratitude for the meticulous efforts of Mr. Nick Page and Mr. Nathan Biller in compounding and applying the powder formulations.
Dr. Lingyun He and Dr. Rajesh Turakhia of Olin Corporation provided invaluable technical guidance and generously supplied epoxy resin samples. Imidazole catalyst support was extended by Dr. Pritesh Patel of Evonik Corporation.
References and Further Reading
- EP0587757B1, see example 1 for epoxy powder coatings (1998).
- Barie and Franke, Ind. Eng. Chem., Vol. 8, No. 3, 72-76 (1969).
- Barabanova et. al., Polymer 178, 121590 (2019).
- Kolar and Svitilova, Acta Geodyn. Geomater., Vol. 4, No. 3, 147, 85-92 (2007).
- Corcuera et. al., J. Appl. Polym. Sci. 64, 157–166 (1997).
- Bouillon, Pascault et. al., J. of Appl. Polym. Sci., Vol. 38, 2103-2113 (1989).
- Mishra & Campanella, Anhydride-cured epoxy composites: overview & recent advances, presented at the annual meeting of Thermoset Resin Formulators Association (TRFA) in Charleston, SC (2019).
- Greenberg & Kusy (see Figure 1), Journal of Applied Polymer Science, Vol. 25,1785-1788 (1980).
- Ferry, Viscoelastic Properties of Polymers, 3rd Ed. (1980).
BTDA® is a trademark of Jayhawk Fine Chemicals Corporation.
D.E.R.™ is a trademark of Olin Corporation.
Imicure® is a trademark of Evonik Corporation.

This information has been sourced, reviewed and adapted from materials provided by Jayhawk Fine Chemicals Corporation.
For more information on this source, please visit Jayhawk Fine Chemicals Corporation.