The characteristics of dry and moist powders can differ significantly. The absorption of even small amounts of moisture can alter powder properties, making humidity and its effects a crucial concern for powder processors.
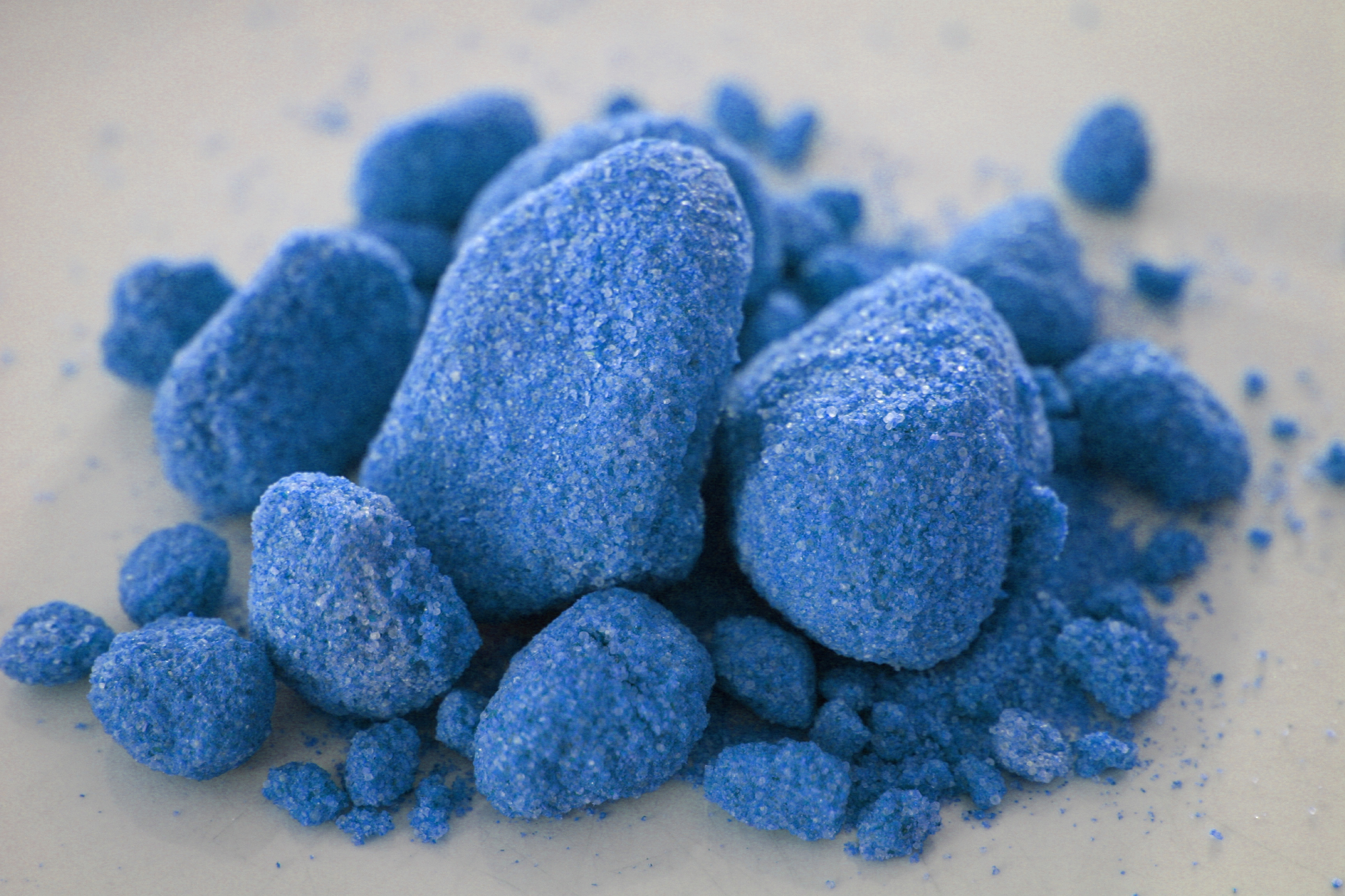
Image Credit: Freeman Technology
While measures can be taken to manage moisture levels, such as pre-processing drying or controlled storage, cost-effective implementation hinges on recognizing their necessity.
Inadequate humidity control can lead to process inefficiencies, yet excessive control adds unnecessary expenses.
It is important to dispel the misconception that any moisture deteriorates powder properties, as different materials respond uniquely. This article explores practical approaches for measuring humidity's impact and offers data examples for limestone and microcrystalline cellulose, two vital industrial powders.
These findings demonstrate how multi-faceted powder characterization gives a comprehensive insight into the effect of moisture uptake, providing a solid foundation for developing efficient humidity control strategies.
Tools for Powder Characterization
The initial step in assessing how humidity affects powder processing is pinpointing analytical methods that yield pertinent and suitable data.
Numerous powder testing techniques exist, but for optimizing processes, it is most effective to focus on methods capable of producing sensitive, consistent data that are reliably related to process performance.
Refining conventional powder testing methods, such as shear and bulk property measurement, using modern instruments and approaches has increased their reliability and reproducibility, making them more informative for this type of study.
Dynamic powder testing has recently emerged, enabling a range of complementary tests that furnish detailed insights into powder behavior.
Dynamic characterization involves gauging axial and rotational forces on a blade as it moves through a sample along a fixed helical path. The resultant flow energy values directly quantify powder flowability.
Highly sensitive dynamic characterization offers the advantage of measuring powders in consolidated, conditioned, aerated, or fluidized states, facilitating a direct examination of the air's impact.
The subsequent experimental study illustrates how measuring various powder properties enhances our understanding of the distinct responses to moisture exhibited by limestone [BCR116, European Commission] and microcrystalline cellulose (MCC) [PH200, FMC].
Comparing the Impact of Humidity on MCC and Limestone
The quantity of moisture absorbed and adsorbed by powders can vary significantly. Nevertheless, for those dealing with powders, the crucial aspect often lies in how this moisture impacts the behavior of the powder.
In tests that aimed to assess the effect of humidity on both MCC and limestone, it became evident that the moisture sorption properties of the two materials differed considerably. MCC, for instance, absorbed approximately ten times more water than limestone when left to reach equilibrium in controlled humidity environments.
Subsequent tests, however, showed that moisture significantly altered both materials' behavior.
Figure 1 displays a range of dynamic and bulk data demonstrating how the behavior of limestone and MCC changes with moisture. These measurements were obtained using an FT4 Powder Rheometer from Freeman Technology in Tewkesbury, UK. This highly automated powder tester encompasses dynamic, shear, and bulk test methods.1,2
Reference 1 contains a comprehensive explanation of the methods used, and collectively, this data quantifies the impact of humidity in a manner relevant to the processing of these materials. Moreover, this information supports the development of an explanation for the observed behavior.
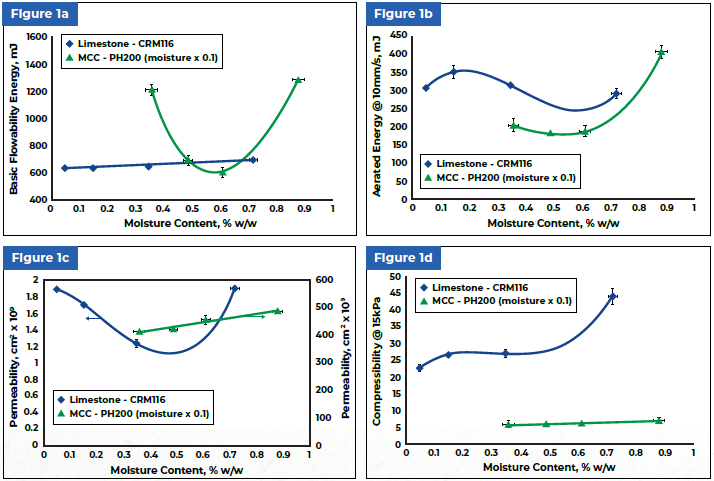
Figure 1. Data showing how the dynamic and bulk properties of limestone and MCC change as a function of water content (a) basic flowability energy (b) aerated energy (c) permeability and (d) compressibility.
Image Credit: Freeman Technology
Note: The moisture content values for MCC are an order of magnitude greater than the limestones.
Microcrystalline Cellulose
In Figure 1, two curves representing dynamic data for MCC, one for basic flowability energy (BFE) and the other for aerated energy (AE), though distinct, share a common trait of exhibiting a minimum flow energy.
Both suggest that moisture enhances MCC's flow characteristics up to a certain threshold, after which flowability deteriorates.
During the study, it was observed that the MCC sample adhered to the inner wall of the glass storage vessel before testing, indicating a propensity for electrostatic charging. This insight helps explain the peculiar behavior of the powder.
If the high BFE value for the drier sample is due to electrostatic interactions among the particles, an increase in moisture could reduce BFE by discharging the sample.
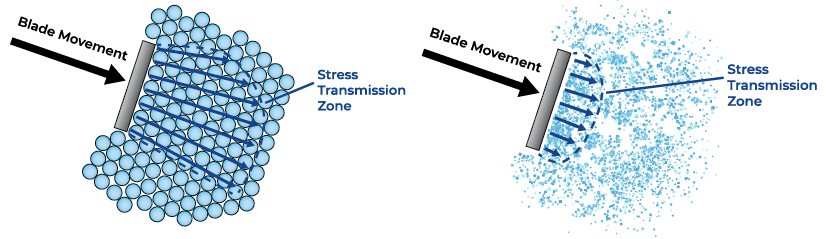
Figure 2. Efficiently packed large particles transmit blade movement through a significant flow zone, generating a high BFE value, while with more cohesive powders the flow zone tends to be much smaller.
Image Credit: Freeman Technology
The steady rise in BFE beyond a certain moisture level is a more commonly observed pattern. It can be attributed to the material absorbing enough moisture to begin agglomerating due to increased adhesion and capillary forces between particles.
Large particles or agglomerates can create substantial resistance to the compacting flow pattern used in BFE testing, often resulting in higher BFE values compared to finer, more cohesive powders with greater void spaces within their structures (refer to Figure 2).
During aeration tests, the ability of the air to separate particles and decrease flow energy depends on electrostatic and mechanical adhesive forces acting between them.
However, in this context, it is evident that agglomeration significantly influences behavior due to agglomerates having greater mass, larger size, and increased adhesive forces. The distinct shapes of the two dynamic curves are thus explained by the process of sample discharge and subsequent agglomeration
This formation of agglomerates creates substantial empty spaces within the powder bed, a trend reflected in the gradual increase in permeability observed in bulk property tests. Beds with larger particles and substantial voids, though challenging to fluidize, offer relatively low resistance to airflow, resulting in higher permeability.
Conversely, compressibility and bulk density (unseen data) remained relatively constant across the range of moisture levels studied, suggesting that, in the case of this powder, packing behavior does not significantly affect changes induced by humidity.
This underscores a limitation in using bulk density measurements to infer information about alterations in flow behavior since these two parameters may or may not directly correlate.
Data from shear tests (not displayed) for this material likewise exhibited little sensitivity to changes caused by increasing moisture content, underscoring the importance of selecting appropriate test strategies for specific investigations.
One crucial point to note about the MCC is that it demonstrates changes in flowability and other characteristics across a range of conditions relevant to the industry, spanning from 25-50% Relative Humidity, which can easily represent ambient conditions.
This suggests that MCC could exhibit varying flow properties when handled in an industrial environment.
Limestone
Limestone, with particles as small as 4 microns, differs significantly from the coarser MCC at 180 microns. Regarding limestone, the dynamic data initially seem contradictory, showing a consistent rise in BFE and varying results in aeration tests.
However, a closer look at the permeability graph for limestone reveals why the aeration tests may have produced such results. The limestone displays very low permeability due to its fine particles.
While permeability seems to shift with moisture content, these changes are quite minor, and permeability remains extremely low at all moisture levels.
This means the limestone samples resist aeration, and upward-flowing air primarily follows channels to the surface rather than promoting steady fluidization.
As a result, the introduction of air has a limited and unpredictable impact on flow energy, with the extent and influence of channeling varying irregularly with moisture content.
Turning to the BFE data, these data indicate a consistent upward trend with moisture, suggesting that water makes the limestone more adhesive, acting as a binder, forming liquid bonds, and creating small agglomerates.
Looking at the compressibility data, even slight changes in moisture content appear to have a significant effect, with compressibility steadily increasing with moisture. This trend aligns with the idea of growing agglomeration.
Typically, more cohesive powders exhibit high compressibility values because strong forces between cohesive particles lead to the formation of loose agglomerates that trap air, allowing for substantial compression of the bed.
In contrast, less cohesive powders enable particles to move more freely relative to each other and tend to pack tightly, making further compression difficult. Bulk density is similarly influenced by particle packing, which is why increased cohesiveness often leads to reduced bulk density.
In these tests, the bulk density of limestone progressively decreased with increasing moisture content, consistent with the steady increase in trapped air in the bed and rising compressibility.
Just like with MCC, shear data for limestone (not displayed) reflected this overall flow behavior trend. However, other parameters more sensitively quantified the impact of humidity on the properties, making them a better choice for this study.
Conclusion
Accurately managing the impact of humidity on process performance requires quantifying and comprehending how adsorbed moisture influences powder characteristics.
This experimental study involving MCC and limestone demonstrates that specific dynamic and bulk property data measurement can offer the necessary insights and highlights crucial concerns for individuals investing in powder testing approaches to explore this matter.
First and foremost, the data reveals that a material's sorption properties do not reliably indicate the extent of changes in powder characteristics. Even when a material absorbs relatively small amounts of moisture, like limestone, it can significantly alter important powder traits such as compressibility and permeability.
Secondly, the results emphasize the effectiveness of a comprehensive approach to powder characterization, as the combination of these results fully explains how moisture impacts the powder.
Lastly, the study provides solid data disproving that all moisture adversely affects powder behavior. For instance, under certain conditions, the flowability of MCC improved with increasing moisture content, possibly due to water's ability to dissipate accumulated electrostatic charge.
What is evident is that minor fluctuations in moisture content can substantially influence powder behavior, even with hydrophobic powders, resulting in neither linear nor predictable effects. Therefore, suitable testing strategies are indispensable for those seeking a profound understanding of humidity's effect on powder processing.
References and Further Reading
- Freeman R. “Measuring the flow properties of consolidated, conditioned and aerated powders - A comparative study using a powder rheometer and a rotational shear cell”, Powder Technology 174 (2007) 25-33.
- Storage and flow of solids, Bulletin 123 of the Utah Engineering Experiment Station, November 1964 (Revised 1980), A.W.Jenike, University of Utah.

This information has been sourced, reviewed and adapted from materials provided by Freeman Technology.
For more information on this source, please visit Freeman Technology.