This article provides an overview of the recent development of the novel cooling system, Indirect Cryogenic Grinding (I.C.G.), for the machining process, its uses, and implications for metals analysis and how it enhances the properties of steel alloys.
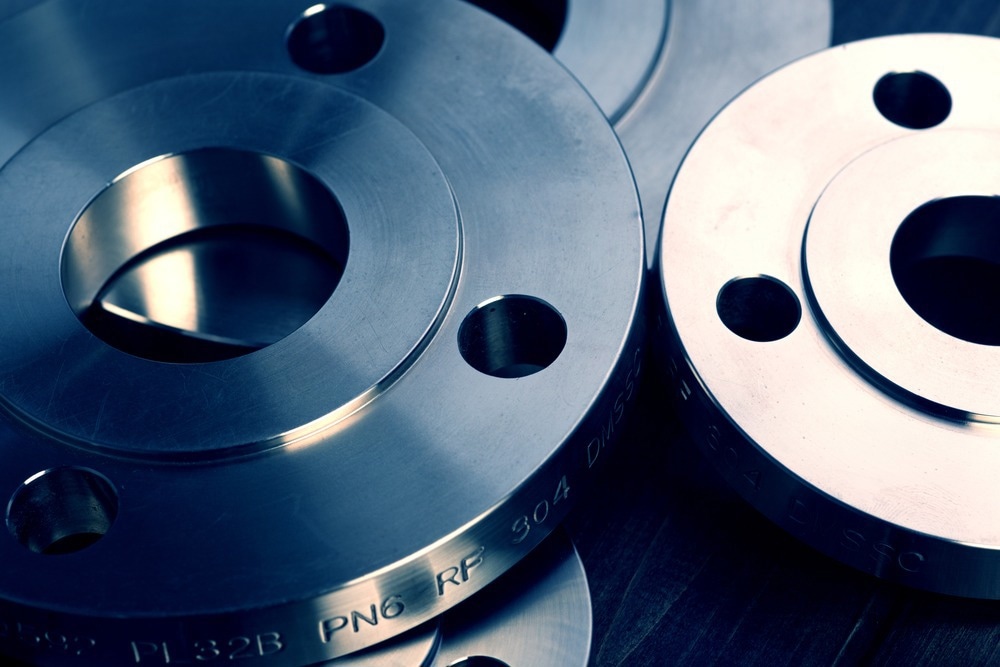
Image Credit: chinasong/Shutterstock.com
Importance of Grinding Operation
The machining process covers many material removal procedures; among them, grinding is one of the most important. Improved grinding is crucial to improve the overall machining process; hence, many researches focused on enhancing the performance of grinding operations by focusing on factors like wear, chattering vibrations, grinding wheel topography, temperature, and force surface roughness.
The cooling systems play a critical role in deciding the surface roughness of the workpiece after the grinding process. Hence, the goal of the study under consideration was to examine the factors influencing the cooling function and develop a method to optimize it.
What is Indirect Cryogenic Grinding (I.C.G.)?
Indirect cryogenic grinding is a method employed in material processing, specifically in the grinding of metallic alloys, by using cryogenic cooling fluids to enhance the properties of the material being worked on. The cooling effect helps in managing heat generation during grinding, influencing the microstructure and surface characteristics of the material.
The conventional use of coolant in grinding poses challenges like surface oxidation, rapid cooling-induced hardening, and limited recyclability. The indirect cooling grinding system, on the other hand, avoids direct coolant contact with the workpiece, which enhances coolant lifespan and enables extended working hours without the need for frequent replacement, offering a more sustainable and efficient grinding solution.
Performance of Four Steel Alloys
The researchers studied the influence of indirect cryogenic grinding on the surface roughness of four distinct steel alloys, 1.2312, 1.2344, 1.2080, and 1.119,1, scrutinizing the impact of coolant temperature and volumetric flow rate across various cutting depths. The subsequent analysis of the surface roughness of steel alloys revealed intricate relationships between coolant parameters and surface quality.
1.2312 Steel Alloy
The examination of the 1.2312 steel alloy demonstrated that optimal surface roughness was achieved with indirect cryogenic grinding at a coolant volumetric flow rate of 40 mL/s and a temperature of 0 °C. Significantly, this improvement was most pronounced at low workpiece temperatures, underscoring the critical role of cooling rates. Further analysis of the microstructure reinforced these findings, highlighting enhanced surface roughness with an increased martensitic phase volume.
1.2344 Steel Alloy
In the case of the 1.2344 steel alloy, the study revealed that optimal conditions for surface roughness were attained at a high cutting depth, 0 °C temperature, and a flow rate of 40 mL/s. Unlike Alloy 1.2312, the surface roughness improvement was consistent across temperatures, demonstrating the versatility of indirect cryogenic grinding in different alloy compositions.
1.2080 Steel Alloy
For the 1.2080 steel alloy, the use of coolant at a volumetric flow rate of 40 mL/s at 0 °C resulted in fast surface hardening, leading to increased surface roughness. The nonlinearity of material behavior and the alloy's chromium content played a role in the observed variations. Optimal conditions for surface roughness were identified at a cutting depth of 0.05 mm, a flow rate of 40 mL/s, and a coolant temperature of −10 °C.
1.1191 Steel Alloy
1.1191 steel alloy exhibited improved surface roughness with indirect cryogenic grinding, with optimal results at a coolant flow rate and temperature of 40 mL/s and −10 °C, respectively. The absence of chromium in this alloy contributed to its favorable response to the cooling method.
Enhanced Surface Quality
The investigation into the metallography structure of the workpieces provided crucial insights into the phase transformations occurring during the indirect cryogenic grinding process. The comparison of cooling paths and Continuous Cooling Transformation (C.C.T.) diagrams for different steel alloys highlighted the role of cooling rates in the formation of hard phases, such as martensite and bainite. The study establishes a connection between the volume of these hard phases and surface roughness, explaining the observed improvements in surface quality.
Future Directions
Future research directions could explore using nanofluids as an alternative to traditional coolants, and improvements in the fluid flow path and heat exchanger design could enhance the overall performance of indirect cryogenic grinding. The economic efficiency and surface quality considerations presented in the study provide a foundation for further exploration and application of indirect cryogenic grinding in industrial settings, offering potential advancements in metal processing.
This thorough examination of indirect cryogenic grinding and its impact on steel alloys opens avenues for potential benefits ranging from improved manufacturing processes to the development of alloys with enhanced mechanical properties.
Conclusion
In conclusion, the research on enhancing the properties of steel alloys using indirect cryogenic grinding demonstrates the potential of indirect cryogenic grinding in improving the surface roughness of steel alloys. The optimal conditions vary for each alloy, considering factors such as coolant temperature, flow rate, and cutting depth. The study emphasizes the importance of controlling the cooling process based on the alloy composition, especially the chromium content.
More from AZoM: Metallography for Structural Analysis of Metallic Components
References and Further Reading
Heydari, A., Pour, M., & Gharib, M. R. (2023). Improvement of steel alloys using indirect cooling grinding (I.C.G.). Heliyon. https://doi.org/10.1016/j.heliyon.2023.e22738
Disclaimer: The views expressed here are those of the author expressed in their private capacity and do not necessarily represent the views of AZoM.com Limited T/A AZoNetwork the owner and operator of this website. This disclaimer forms part of the Terms and conditions of use of this website.