Electroplating refers to the process of plating one metal onto another by hydrolysis and is most commonly used to prevent the corrosion of metal or for decorative purposes. The pulse current electrodeposition (PCE) method and direct current electroplating (DCE) method are the two major techniques for electroplating on steel. This article discussed the use of these techniques and their long-term effects on steel.
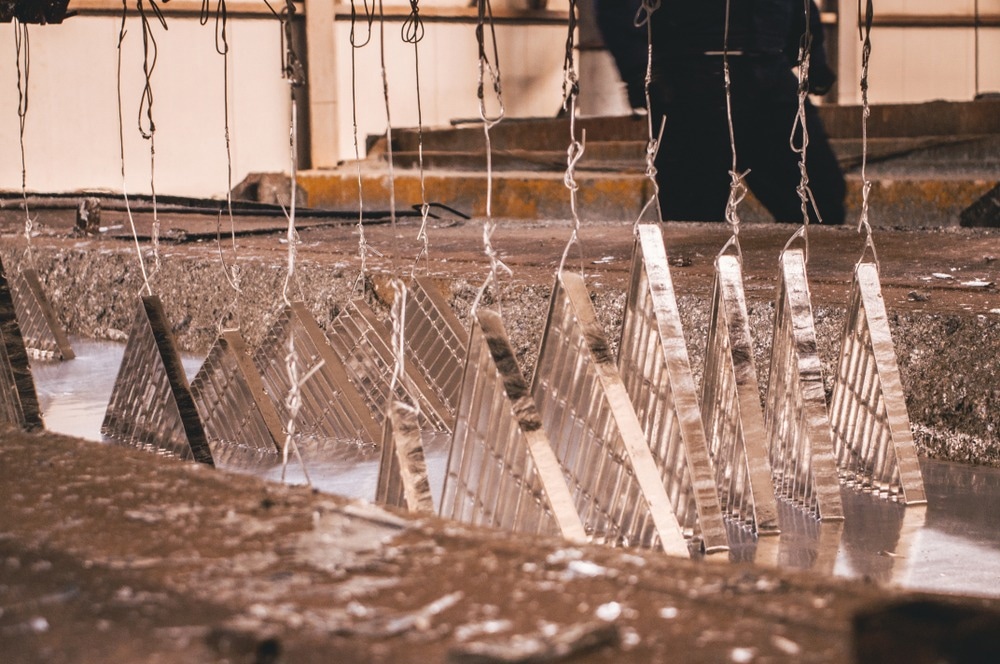
Image Credit: HF media art/Shutterstock.com
Electroplating on Steel Using DCE and PCE
Electroplating is a simple and low-cost process that produces a uniform and dense coating with good adhesion to the substrate. This method is also suitable for coating complex-shaped interconnects.
Although DCE is commonly used for coating on steel due to its simplicity, cost-effectiveness, and high deposition rates, PCE can be used to produce coatings with enhanced surface properties and generate a fine-grain, uniform, and more compact coating with greater deposition rate and low porosity compared to DCE.
Thus, electroplating using pulse current is a more effective approach than DCE to improve metallic coating properties. In PCE, the current has a periodic behavior with a rectangular waveform, while DCE utilizes a constant current.
Several studies have shown that the pulse plating technique affects the mechanical properties and microstructure of deposits due to the differences in recrystallization, nucleation rates, and mass transport behaviors during the anodic and interruption times.
For instance, the grain size, micro-cracking, and micro-morphologies of chromium coatings can be modified by pulse plating. Specifically, pulse plating decreases the crack formation of chromium coatings. Such cracks are observed frequently in coatings electroplated using the DCE method.
A Comparative Analysis of DCE and PCE
In a study published in the journal Surface and Coatings Technology, researchers investigated the interrelations among electroplating parameters, such as electroplating duration and pulse current, structural properties, such as coating thickness, micro-cracking, grain size, and crystalline structure, and physical properties, such as hardness, of chromium barriers.
They electroplated chromium coatings on HT9 steel disks using pulse current and direct current for different durations to examine the influence of coating thickness and pulse current on the resulting microstructure and fuel and cladding chemical interaction (FCCI) resistance.
Results showed that pulse current and over 20 μm thick coating were effective in improving the chromium coatings' barrier properties. Electron backscatter diffraction and scanning electron microscopy (SEM) analyses revealed sound microstructures with no micro-cracking and twofold grain structures that included large and small grains near the outer surface and HT9 substrate of the pulse-plated chromium coatings with over 20 μm thickness, respectively.
These led to reduced interdiffusion depth and interdiffusion area in the diffusion-coupled specimens' microstructure. Heat treatment of chromium coatings at 650 °C for durations ranging from 50 to 1000 h demonstrated that the grain size increases with the increasing heat treatment time. However, the chromium coatings' Vickers hardness reduced with the increasing grain size.
Improvement in the electrical conductivity and oxidation resistance of solid oxide fuel cell (SOFC) interconnects has been an active research area.
In a study published in the journal Materials At High Temperatures, cobalt coating was fabricated on the Crofer22APU ferritic stainless steel interconnect using the PCE and DCE methods. Researchers investigated and compared the electrical behavior and oxidation of the coatings.
The cross-section and surface of the samples were characterized using the SEM-energy dispersive X-ray (EDX) and X-ray diffraction (XRD) techniques. Investigations displayed that PCE resulted in a decrease in the porosity, roughness, and grain size of cobalt deposits compared to the cobalt coating formed by the DCE method.
Subsequently, the steel samples were exposed to air for 500 h at 800 °C and their oxidation rates were calculated. The oxidation rates were reduced significantly for PCE-cobalt-coated samples compared to the uncoated and DCE-cobalt-coated samples.
Moreover, the electrical conductivity of samples was also assessed in air at 800 °C as a function of the temperature. The PCE-cobalt coated Crofer22APU ferritic stainless steel displayed an electrical conductivity of 54.64 S cm² at 800 °C.
Long-term Corrosion Resistance Through Electroplating
Electrodeposited zinc-manganese (Zn-Mn) alloy coatings provide exceptional corrosion resistance to steel as they form compact corrosion products when exposed to corrosive media.
However, good-quality coatings cannot be easily obtained from additive-free baths using the conventional DCE method. Pulsed current deposition can be used for different Zn-based alloy systems to realize coatings with improved corrosion resistance properties.
In a study published in the journal Electrochimica Acta, researchers electrodeposited Zn-Mn coatings containing up to 9.2 wt. % Mn on steel from additive-free chloride electrolytes using pulse current and direct current electrodeposition.
SEM-EDS, cyclic voltammetry, potentiostatic measurements, and Hull cell experiments indicated good-quality direct current deposited Zn-Mn coatings in the 40-60 mA cm⁻² current density range with cauliflower morphology and clustered plate morphology at higher and lower current densities, respectively.
Pulse current deposited coatings demonstrated improved corrosion rates and increased Mn contents. The coating deposited at a high frequency and a low-duty cycle displayed a compact and fine microstructure with the highest 9.2 wt. % Mn content.
XRD studies displayed a change in phase composition from a monophasic η-Zn-Mn coating containing 1-2 wt. % Mn with direct current to a monophasic ε-Zn-Mn containing 15-45 wt. % Mn with pulse current deposition.
Electrochemical impedance analysis showed porous corrosion products in the direct current coating, while the pulse current coating formed a compact corrosion product, which prevented the dissolution of Mn and Zn, resulting in a higher corrosion resistance.
XRD analysis of the steel samples after corrosion confirmed the existence of zinc hydroxy chloride (ZHC) as a corrosion product. Overall, the pulse current electrodeposited Zn-Mn coatings provided superior corrosion resistance compared to the direct current electrodeposited Zn-Mn coatings.
To summarize, electroplating, using both direct current and pulse current methods, can improve various properties of steel coatings. PCE offers advantages like finer grain structure, lower porosity, and improved corrosion resistance compared to DCE, as demonstrated in the studies discussed in this article. However, the choice of method depends on the specific application and desired properties.
2D Materials Beyond Graphene: Properties and Potential
References and Further Reading
Electroplating. [Online] Available at https://chem.libretexts.org/Bookshelves/Analytical_Chemistry/Supplemental_Modules_(Analytical_Chemistry)/Electrochemistry/Electrolytic_Cells/Electroplating (Accessed on 06 February 2023)
Yeo, S., Kim, J. H., Yun, H. S. (2020). Effect of pulse current and coating thickness on the microstructure and FCCI resistance of electroplated chromium on HT9 steel cladding. Surface and Coatings Technology, 389, 125652. https://doi.org/10.1016/j.surfcoat.2020.125652
Saeidpour, F., Zandrahimi, M., Ebrahimifar, H. (2020). Oxidation and electrical behaviour of direct and pulse current electroplated cobalt coatings on Crofer22APU stainless steel interconnect. Materials at High Temperatures, 37(2), 89-100. https://doi.org/10.1080/09603409.2019.1709292
Deo, Y., Ghosh, R., Nag, A., Kumar, D. V., Mondal, R., Banerjee, A. (2021). Direct and pulsed current electrodeposition of Zn-Mn coatings from additive-free chloride electrolytes for improved corrosion resistance. Electrochimica Acta, 399, 139379. https://doi.org/10.1016/j.electacta.2021.139379
Disclaimer: The views expressed here are those of the author expressed in their private capacity and do not necessarily represent the views of AZoM.com Limited T/A AZoNetwork the owner and operator of this website. This disclaimer forms part of the Terms and conditions of use of this website.