By Owais AliReviewed by Lexie CornerMay 8 2025
Carbon fiber is known for being incredibly strong, lightweight, and versatile—but how is it actually made?
This article breaks down the key stages of carbon fiber manufacturing and shows how different starting materials affect the properties of the final product.
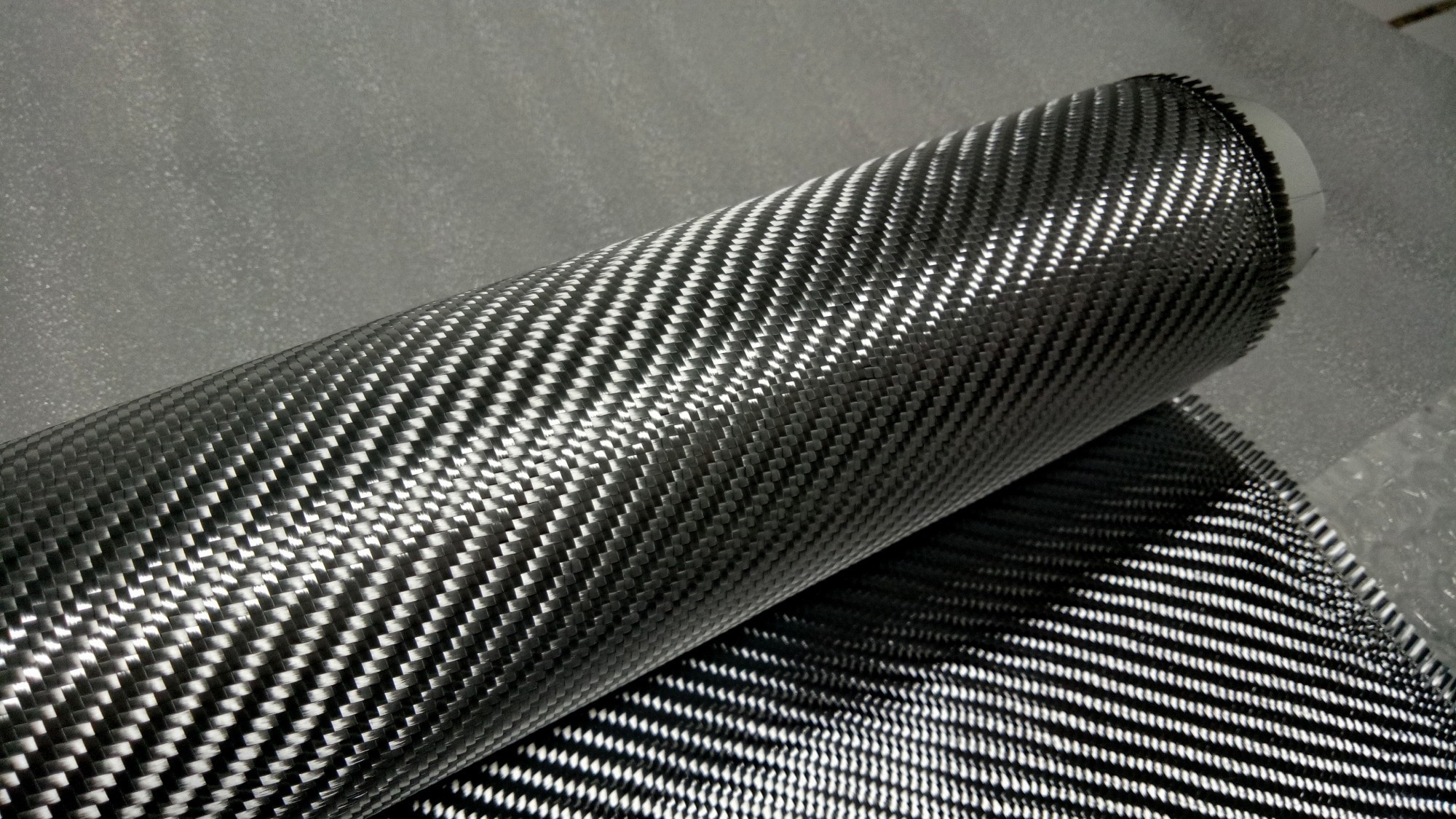
Image Credit: Composite_Carbonman/Shutterstock.com
What is Carbon Fiber?
Carbon fibers consist of thin filaments (5–10 micrometers in diameter) made of long chains of carbon atoms arranged in a polycrystalline structure. These fibers contain 92–100 wt% anisotropic carbon organized in a two-dimensional hexagonal lattice, with limited crystallographic order along the z-axis.
They offer a unique combination of high tensile strength (up to 7 GPa), high modulus (up to 900 GPa), low density (1.75–2.00 g/cm³), excellent creep resistance, minimal thermal expansion, and strong chemical and fatigue resistance. This makes them highly valuable in high-performance applications across aerospace, defense, automotive, construction, nuclear, and biomedical sectors.1
Carbon Fiber Precursors
The production of carbon fibers begins with selecting suitable organic polymer precursors, which determine the structural characteristics and performance of the final fibers. Three types of precursors are commonly used in the industry: polyacrylonitrile (PAN), cellulose, and pitch.
Polyacrylonitrile (PAN) Precursors
Approximately 90 % of commercial carbon fibers are derived from PAN, which contains over 85 % acrylonitrile.
PAN can be used as a homopolymer or a copolymer, with comonomers such as itaconic acid, methacrylic acid, and methyl methacrylate. These additives help regulate the exothermic stabilization reaction, promote molecular orientation, and lower the cyclization onset temperature, ultimately improving the properties of the final fibers.
PAN-based precursors are highly valued for their high carbon yield and superior mechanical performance, making them the industry standard.
Cellulosic Precursors
Cellulose was the first material used to develop carbon fibers, with industrial products such as carbon cloth and yarns appearing in the 1950s and 1960s.
While cellulose-based carbon fibers generally offer lower tensile strength and modulus than PAN-derived fibers, they provide benefits such as high thermal conductivity, mechanical flexibility, high purity, and lower precursor cost.
Pitch-Based Precursors
Pitch precursors come from carbon-rich sources such as petroleum and coal tar pitches, or synthetic pitches formed through polymer pyrolysis.
Pitch-based carbon fibers have a high modulus due to their graphitic microstructure but exhibit relatively poor compressive and transverse mechanical properties compared to PAN-based fibers. Despite this, their low cost and high carbon yield make them appealing for applications where axial stiffness is more important than strength in multiple directions.1,2
Download your PDF copy now!
Manufacturing of PAN-Based Carbon Fibers
The production of carbon fibers from PAN-based precursors involves six essential steps: polymerization, fiber spinning, thermal stabilization, carbonization and graphitization, surface treatment, and finally, drying, sizing, and winding.
Polymerization of the Precursor
The polymerization process converts acrylonitrile monomers into long polymer chains, which are essential for fiber formation. This step allows for the control of molecular properties, allowing for the production of fibers with specific mechanical and thermal characteristics.
Several polymerization methods are employed in the industry:
- Solution Polymerization: Acrylonitrile and comonomers are dissolved in a non-reactive solvent with a catalyst. This method controls reaction heat but is not commercially viable due to challenges in solvent removal.
- Bulk Polymerization: This is a simpler method where a soluble initiator is added to pure liquid monomer, initiated by heating or radiation. It produces polymers with broad molecular weight distributions suitable for small-scale manufacturing.
- Emulsion Polymerization: This method involves radical polymerization in an emulsion containing water, monomer, and surfactant, which is used for PAN-based precursor production.
- Aqueous Dispersion Polymerization: This technique produces monodisperse polymer particles with a narrow size distribution, achieving diameters as low as 3 ± 1.5 microns. It is particularly important for high-performance applications that require consistent polymer dimensions.
Fiber Spinning
The polymerized PAN precursor is spun into continuous fibers, typically using wet spinning, although dry-jet wet spinning (also known as air-gap spinning) is increasingly preferred for improved fiber properties.
To enhance the performance of the precursor, 2–10 % of comonomers such as methyl acrylate, methyl methacrylate, or itaconic acid are commonly added.
The spinning process involves applying high temperatures and pressures to shape the fibers. Precise control of these conditions is essential to avoid degradation of the PAN polymer and to ensure that the resulting fibers maintain the desired structural integrity and mechanical properties.
Thermal Stabilization
Thermal stabilization is a crucial step in converting PAN-based precursors into fibers that can withstand subsequent high-temperature processing. Depending on the specific characteristics of the precursor, fibers are heated in air at 200–300 °C for several hours.
During this stage, the polymer chains undergo cyclization, transforming from linear to cyclic structures. This structural change prevents the fibers from melting during later stages and prepares them for carbonization.
Carbonization and Graphitization
Carbonization occurs under inert atmospheric conditions, typically using nitrogen or argon, at temperatures between 1500-1600 °C.
Above 1600 °C, tensile strength decreases, and graphitization, conducted between 1600 °C and 3000 °C, becomes necessary to achieve high-modulus fibers. This temperature determines the degree of crystallinity and tensile strength of the resulting carbon fibers.
Nitrogen is a more economical choice for carbonization, but becomes unsuitable above 2000 °C due to the formation of toxic cyanogen gas. Argon, although more expensive, is preferred at higher temperatures due to its greater density and viscosity, which contribute to improved fiber strength.
Surface Treatment and Washing
Surface treatment is essential for enhancing the mechanical performance of carbon fiber composites by improving fiber-to-resin bonding.
One common method is anodic oxidation, where the carbon fibers act as the anode in an electrochemical process. This generates carboxyl (COOH) functional groups on the fiber surface, which promote better adhesion with resin systems.
Following surface treatment, the fibers are thoroughly washed to remove any residual electrolytes that could interfere with composite fabrication.
Drying, Sizing, and Winding
After surface treatment, carbon fibers are dried and coated with a sizing agent to protect and improve handling. Sizing materials, typically epoxy resins or similar formulations, are used with matrix resins to facilitate resin penetration and fiber-resin bonding.
The fibers are then wound onto spools and stored for further processing or composite fabrication, with the sizing materials ensuring the fibers' physical properties are not degraded during storage.1-4
Manufacturing of Cellulose-Based Carbon Fibers
The manufacturing of cellulose-based carbon fibers involves four main stages: precursor production, stabilization, carbonization and graphitization, and post-treatment.
Rayon Precursor Production
The process begins by converting cellulose into continuous filament rayon. The most common method for this is the viscose process, in which purified cellulose pulp is treated with sodium hydroxide, aged, and then reacted with carbon disulfide to form cellulose xanthate.
This xanthate solution becomes a viscous spinning fluid, which is wet-spun into filaments in a coagulation bath. The resulting filaments are then stretched, washed, and dried to improve molecular alignment.
Alternative production routes include cuprammonium rayon (produced by dissolving cellulose in cuprammonium hydroxide) and saponified acetate rayon (derived via acetylation, followed by hydrolysis and saponification).
Stabilization
Stabilization prepares the cellulose-based precursor for high-temperature processing by making it infusible and dimensionally stable. This is achieved by heating the fibers to 200–380 °C in an inert or mildly oxidative atmosphere, triggering crosslinking and partial oxidation of hydroxyl groups.
During this process, volatile compounds such as water, carbon monoxide, and acetic acid are released. The resulting structure becomes partially aromatized, with an associated mass loss of 10–30 %. Despite this reduction, stabilization is essential for forming defect-free carbon structures in the next phase.
Carbonization and Graphitization
Carbonization and graphitization of cellulose-based precursor fibers involve multi-stage thermal decomposition. Initial dehydration occurs between 25 and 150 °C, followed by physical desorption and chemical dehydration from 150 to 240 °C, forming double-bonded intermediates.
Carbonization starts at 300 °C and continues to 900 °C in an inert atmosphere, where glycosidic linkages break, leading to depolymerization and formation of carbon-rich intermediates. The process continues with graphitization from 900 °C to 3000 °C, improving the crystalline structure and enhancing fiber modulus.
This high-temperature treatment increases the carbon content above 99 % and promotes the growth of crystalline graphite-like structures.
Surface Treatment, Sizing, and Winding
Post-carbonization processing for cellulose-based carbon fibers mirrors that of PAN-based fibers.
Surface treatment typically involves mild oxidation, using electrochemical or gaseous methods, to introduce polar functional groups that enhance interfacial bonding with polymer matrices in composite applications. Sizing agents such as epoxy, polyvinyl alcohol, or polyurethane are applied to protect the fibers during handling and weaving while improving matrix compatibility.
The treated fibers are then wound onto spools or bobbins under controlled tension to ensure alignment and prevent damage during further processing.1-4
How is Nanocellulose Used in Water Purification?
Manufacturing of Pitch-Based Carbon Fibers
The production of pitch-based carbon fibers involves several key stages: precursor preparation, melt spinning, thermal stabilization, carbonization, and high-temperature graphitization.
Preparation of Pitch-Based Precursors
Pitch-based carbon fibers are made from either petroleum pitch or coal-tar pitch.
Petroleum pitch is produced by solvent deasphalting, oxidation, and thermal treatment of heavy petroleum fractions. In solvent deasphalting, light paraffinic solvents like propane, butane, or pentane precipitate high-molecular-weight aromatic components, resulting in dense pitch with a specific gravity of around 1.0 g/cm³ at 60°F, containing significant heteroatoms and metals.
Subsequent oxidation and thermal treatment (300-480 °C) increase aromaticity and molecular weight, producing isotropic or anisotropic pitch.
Coal-tar pitch, a by-product of coal coking, is obtained by distilling coal tar, which yields 30-45 liters of tar per ton of coal. The resulting pitch is characterized by a high aromatic content, typically over 90 %, and provides excellent carbon yield, making it ideal for high-performance carbon fiber production.
Production of Precursor Fibers
The precursor pitch is melted, extruded through a spinneret, and drawn into fibers during cooling. This step determines the structural orientation of the fibers and establishes the foundation for further ordering during heat treatment.
The melt temperature is critical: each mesophase has an optimal temperature window for spinning. Even a modest reduction in melt temperature (e.g., 15 °C) can quadruple viscosity, significantly lowering tensile strength and Young’s modulus. Therefore, maintaining low melt viscosity is essential for producing high-quality, well-aligned fibers.
Stabilization
Stabilization is essential for making pitch-based fibers infusible, preventing deformation during the high-temperature carbonization process.
This step involves controlled oxidation in air at temperatures between 250–350 °C for durations ranging from 30 minutes to several hours, depending on the pitch type and fiber morphology.
During oxidation, functional groups such as ketones, carbonyls, and carboxyls are introduced, promoting inter-chain hydrogen bonding and three-dimensional crosslinking. This stabilizes the fiber structure and prepares it for carbonization by preventing softening or melting.
Carbonization and Graphitization
Following stabilization, fibers undergo carbonization and graphitization to develop their final carbon-rich structure.
Precarbonization is typically conducted at 700–900 °C for a short duration (0.5 to 5 minutes) to reduce structural defects. This is followed by carbonization at 1500–1800 °C, which removes non-carbon elements and begins crystallization. A temporary drop in modulus may occur due to initial structural changes, but it improves with extended heat treatment.
Graphitization is performed near 3000 °C, further increasing crystallinity and Young’s modulus through better alignment of graphite layers. The final microstructure is heavily influenced by the alignment of precursor fibers, which in turn is affected by spinning dynamics. This results in radial, circumferential, or random graphite orientations.
Surface Treatment, Sizing, and Winding
As with other carbon fiber types, pitch-based fibers undergo standard surface treatment, sizing, and winding steps.1-4
How to Turn Pitch into Carbon Fiber for Automotive Applications
Looking Ahead
As the demand for stronger, lighter, and more sustainable materials grows, researchers are exploring alternative production methods and feedstocks for carbon fiber. To learn more, visit: Utilizing Petroleum Residue to Create Carbon Fiber Composites
For a detailed walkthrough of carbon fiber manufacturing, watch:
How Carbon Fiber is made animation | Karthi Explains
References and Further Reading
- Park, S. J. (2018). Carbon fibers (Vol. 210). Dordrecht, The Netherlands:: Springer. https://doi.org/10.1007/978-981-13-0538-2
- Vicki McConnell. (2018). The Making of Carbon Fiber. [Online]. https://www.compositesworld.com/articles/the-making-of-carbon-fiber
- Frank, E., Hermanutz, F., & Buchmeiser, M. R. (2012). Carbon fibers: precursors, manufacturing, and properties. Macromolecular materials and engineering, 297(6), 493-501. https://doi.org/10.1002/mame.201100406
- Lengsfeld, H., Mainka, H., & Altstädt, V. (2020). Carbon fibers: production, applications, processing. Carl Hanser Verlag GmbH Co KG. https://doi.org/10.1016/C2020-0-01636-1
Disclaimer: The views expressed here are those of the author expressed in their private capacity and do not necessarily represent the views of AZoM.com Limited T/A AZoNetwork the owner and operator of this website. This disclaimer forms part of the Terms and conditions of use of this website.