The modern day process has developed and matured significantly to the level where fully automated, closed loop, microprocessor controlled machines are the 'norm', although in principle injection moulding is still a relatively simple process. Thermoplastic injection moulding requires the transfer of the polymeric material in powder or granule form from a feed hopper to a heated barrel. In the barrel, the thermoplastic is melted and then injected into a mould with some form of plunger arrangement. The mould is clamped shut under pressure within a platen arrangement and is held at a temperature well below the thermoplastic melt point. The molten thermoplastic solidifies quickly within the mould, allowing ejection of the component after a pre determined period of cooling time. The basic injection moulding process steps with a reciprocating screw machine are as follows. Mould Close and Clamping The mould is closed within the platen arrangement and clamped using necessary force to hold the mould shut during the plastic injection cycle, thus preventing plastic leakage over the face of the mould. Present day moulding machines range from around 15 to 4,000 metric tonnes available clamping force (150 to 4000 kN). Many systems are available for opening/closing and clamping of mould tools, although usually they are of two general types. Direct Hydraulic Lock is a system where the moving machine platen is driven by a hydraulic piston arrangement which also generates the required force to keep the mould shut during the injection operation. Alternatively, smaller auxiliary pistons may be used to carry out the main movement of the platen and a mechanical blocking arrangement is used to transfer locking pressure from a pressure intensifier at the rear of the machine, which moves only by a few millimetres, through to the platen and tool. The second type of general clamping arrangement is referred to as the Toggle Lock. In this case a mechanical toggle device, which is connected to the rear of the moving platen, is actuated by a relatively small hydraulic cylinder, this provides platen movement and also clamping force when the toggle joint is finally locked over rather like a knuckle arrangement. Injection At this stage in the machine cycle the helical form injection screw (Figure 1) is in a 'screwed back' position with a charge of molten thermoplastic material in front of the screw tip roughly equivalent to or slightly larger than that amount of molten material required to fill the mould cavity. Injection moulding screws are generally designed with length to diameter ratios in the region of 15:1 to 20:1, and compression ratios from rear to front of around 2 : 1 to 4 : 1 in order to allow for the gradual densification of the thermoplastic material as it melts. A check valve is fitted to the front of the screw such as to let material pass through in front of the screw tip on metering (material dosing), but not allow material to flow back over the screw flights on injection. The screw is contained within a barrel which has a hardened abrasion resistant inner surface. 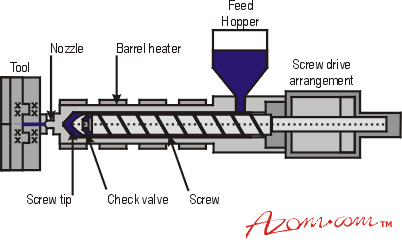 | Figure 1. Reciprocating screw injection moulding unit | Normally, ceramic resistance heaters are fitted around the barrel wall, these are used to primarily heat the thermoplastic material in the barrel to the required processing temperature and make up for heat loss through the barrel wall, due to the fact that, during processing most of the heat required for processing is generated through shear imparted by the screw. Thermocouple pockets are machined deep into the barrel wall so as to provide a reasonable indication of melt temperature. Heat input can therefore be closed loop controlled with a Proportional Integral and Derivative (PID) system. The screw (non-rotating) is driven forward under hydraulic pressure to discharge the thermoplastic material out of the injection barrel through the injection nozzle, which forms an interface between barrel and mould, and into the moulding tool itself. Holding Pressure and Cooling The screw is held in the forward position for a set period of time, usually with a molten 'cushion' of thermoplastic material in front of the screw tip such that a 'holding' pressure may be maintained on the solidifying material within the mould, thus allowing compensating material to enter the mould as the moulded part solidifies and shrinks. Holding pressure may be initiated by one of three methods: by a set time in seconds from the start of the injection fill phase; by the position of the screw in millimetres from the end of injection stroke; or by the rise in hydraulic pressure as measured by a pressure transducer in the mould itself or in the injection hydraulic system. As the material solidifies to a point where hold pressure no longer has an effect on the mould packing, the hold pressure may be decayed to zero, this will help minimise residual stresses in the resultant moulding. Once the hold pressure phase has been terminated the mould must be held shut for a set period of cooling time. This time allows the heat in the moulding to dissipate into the mould tool such that the moulding temperature falls to a level where the moulding can be ejected from the mould without excessive distortion or shrinkage. This usually requires the moulding to fall to a temperature below the rubbery transition temperature of the thermoplastic or Tg (glass transition temperature). Depending on the type of plastic this can be within a few degrees or over a temperature range. Mould temperature control is incorporated into the tool usually via channels for pressurised water flow. The mould may be connected to a cooling unit or water heater depending on the material being processed, type of component and production rate required. Material Dosing or Metering During the cooling phase, the barrel is recharged with material for the next moulding cycle. The injection screw rotates and, due to its helical nature, material in granule or powder form is drawn into the rear end of the barrel from a hopper feed. The throat connecting the hopper to the injection barrel is usually water cooled to prevent early melting and subsequent material bridging giving a disruption of feed. The screw rotation speed is usually set in rpm which is measured using a proximity switch at the rear of the screw. Screw rotation may be set as one constant speed throughout metering or as several speed stages. The material is gradually transferred forward over the screw flights and progressively melted such that when it arrives in front of the screw tip it should be fully molten and homogenised. The molten material transferred in front of the tip progressively pushes the screw back until the required shot size is reached. Increased shear is imparted to the material by restricting the backward movement of the screw, this is done by restricting the flow of hydraulic fluid leaving the injection cylinder. This is referred to as `back pressure' and it helps to homogenise the material and reduce the possibility of unmelted material transferring to the front of the screw. Mould Open and Part Ejection When the cooling phase is complete the mould is opened and the moulding is ejected. This is usually carried out with ejector pins in the tool which are coupled via an ejector plate to a hydraulic actuator, or by an air operated ejector valve on the face of the mould tool. The moulding may free fall into a collection box or onto a transfer conveyer, or may be removed by an automatic robot. In this latter case the moulding cycle is fully automatic. In semi-automatic mode, the operator may intervene at this point in the cycle to remove the moulding manually. Once the moulding is clear from the mould tool, the complete moulding cycle can be repeated. |