Introduction
Calcium phosphate (CP), especially hydroxyapatite (Ca10(PO4)6(OH)2, HA), coatings deposited on titanium alloy implants have shown promising effects on rapid bone remodeling and suitable functional life in orthopedic and dental applications. There is no doubt that the microstructure of the coatings significantly influences their mechanical properties [1, 2]. It is well known that a thermal sprayed coating shows a layered structure composed of individual accumulated splats. Due to this anomalous inhomogeneously-layered structure, the coatings show a significant dependence of their mechanical performances on microstructure. Generally, splat formation is an isolated procedure, which means a minor influence of the subsequent splat on the phases of the former one. Therefore, the overall in vitro behavior and microstructure of a bulk HA coating should be directly related to those of an individual HA splats. Consequently, a good understanding of the in vitro behavior and microstructure of an individual HA splat would significantly contribute to knowledge on HA coatings. To date, some interesting results have been reported by many researchers on the microstructure of thermal sprayed splats [3-5]. In order to reveal detailed structural features of a single splat, transmission electron microscopy (TEM) must be adequately involved. Furthermore, in vitro study of individual CP splats can probably give insight into the mechanism of biocompatible CP interaction with cells. In addition, a previous in vitro study has shown that nano-sized ceramics have a significant ability to enhance osteoblast adhesion on them [6]. Nanostructures within a biocompatible coating could therefore show the same effect. In the present study, the nanostructures and in vitro osteoblast behavior of individual CP splats were characterized. The splats were deposited using both plasma spraying and HVOF onto polished Ti-6Al-4V substrates.
Experimental
HA powders synthesized in-house via the wet chemical method were utilized for splat deposition employing both HVOF and plasma spray processes. The starting powder particles have typical nanostructures with cylindrical grains <500 nm in length and 40-70 nm in diameter (Figure 1). A nanostructured HA particle is formed by the agglomeration of individual nanosized cylindrical HA grains. The splats were collected on Ti6Al4V plate substrates polished using 1 μm diamond paste. The microstructure of the samples was analyzed using scanning electron microscopy (SEM, JEOL JSM-5600LV), field emission SEM (FESEM, JEOL JSM-6340F), and transmission electron microscopy (TEM, JEOL, JEM-2010) operated at 200 kV. The in vitro cell culture work was conducted using the commercially available hFOB 1.19 cell line. The splat samples were incubated in Dulbecco's modified eagle medium (DMEM) containing 10% fetal bovine serum (FBS) and 0.5% antibiotics with 5×104 cells. Cells were cultured in an atmosphere of 100% humidity, 5% CO2 at 37°C in 24-well culture plates with 1 ml of medium contained in each well. After 2 days’ incubation, the morphology of the cells attached onto the samples was observed using SEM. Prior to the SEM observation, 2.5% glutaraldehyde in 0.1 M sodium cacodylate buffer was used for pre-fixing the cells, followed by post-fixation with 1% osmium tetroxidein in 0.1 M cacodylate buffer. The final steps for fixing the samples were dehydration and critical point drying.
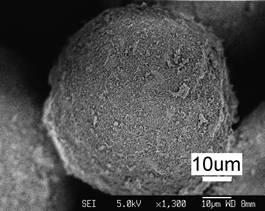
(a)
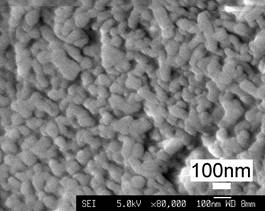
(b)
Figure 1. Typical topographical morphology of the starting nSD-HA particles (a). Close examination of the HA particle (b) shows the agglomeration of nanosized HA grains.
Results and Discussion
Figure 2 shows typical topographical nanostructures within the CP splats observed by TEM (Figure 2a) and FESEM (Figure 2b). It is seen that the HA splat is composed of nanostructured ~30 nm grains. FESEM observation of the HA coatings reveals consistent nanostructures (Figure 3). This further suggests that during the accumulation of individual HA splats to form the bulk coating, there is no obvious grain growth of the nanosized grains. However, it must be noted that for the nanostructures in the splats, there are a lot of phases apart from HA, e.g. α-TCP (tricalcium phosphate) and β-TCP. This may not be desirable since these phases result from HA decomposition and are less bioactive than HA. Furthermore, it is noted that the nanostructures in the splats/coatings are not the same as those present in the starting feedstock. After the high temperature spray processing, the nano-fibers have changed to nanosized spheres with a size range of 40 nm ~ 120 nm. This suggests that during the melting/resolidification process, the nano-fibers were mostly split into one or more individual parts form which by surface tension, the nanosized spheres were formed. The results may also indicate the importance of existing nanostructures in the starting powders on the final nanostructures in the coatings.
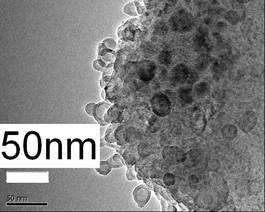
(a)
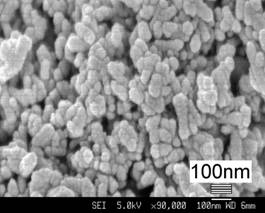
(b)
Figure 2. Typical TEM morphology at the splat’s fringe (a) and FESEM morphology taken at the splat’s surface (b) of the CP splat showing the consistent nanostructures.
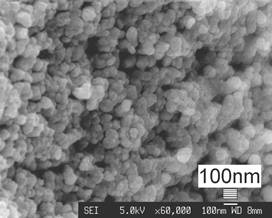
Figure 3. FESEM photo of the HA coating showing consistent nanostructures inside the coating.
Furthermore, amorphous CP was revealed at the extreme surrounding areas of the splat (Figure 4), which indicates very rapid cooling of the droplet upon impingement on the substrate.

(a)
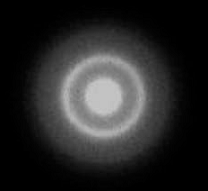
(b)
Figure 4. Typical TEM microstructure of the HA splat (a) taken at the splat fringe, showing the predominant presence of amorphous calcium phosphate (ACP), as suggested by a selected diffraction pattern (b).
It has also been revealed that, for the HVOF HA coatings/splats, the areas inside the HA splats with intimate contact with the substrate surface exhibited a typical cuboid structure (Figure 5). Most of the grains are <250 nm in length and <50 nm in diameter. Very few of them have a larger size of 0.4-1.2 μm in length and 80-120 nm in width. The appearance of such cuboid shape structures only in the HVOF coating possibly indicates a critical condition for formation of the structure: full molten state, rapid cooling, and fast impingement.
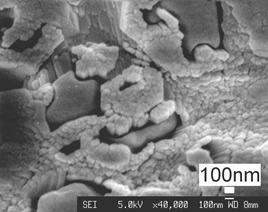 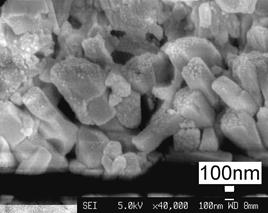
Figure 5. Typical FESEM photos taken at the bottom of the HVOF coating (with intimate contact with the substrate) showing a cuboid structure.
The primary cell culture testing suggests that the HA splats are bioactive such that they attracted marked cell attachment and proliferation after 2 days’ incubation (Figure 6). However, there is significant dissolution of the splats prior to the attachment and proliferation of the cells on the substrate. This may suggest that the (partial) dissolution of the splats into the culture media enhances the proliferation of the cells.
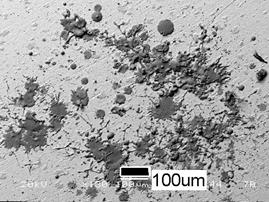
(a)
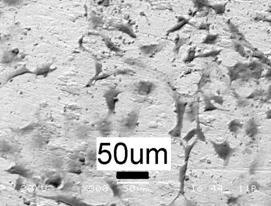
(b)
Figure 6. Obvious attachment and proliferation of the osteoblast cells on the HA splats, (a) SEM picture before the incubation and (b) after the incubation.
For comparison purpose, the HA coatings were also incubated in the media for 2 days. The cells also proliferated well on the coating surface (Figure 7). However, there is no remarkable dissolution of the coating. It is noted that the number of the cells proliferated on the coating is less than that on the splats. It hence indicates that dissolution of the Ca-P-rich phase into the medium might promote cell proliferation. The dissolution behavior of the CP splats has been discussed in another paper from our laboratory [7]. It must be noted that the phases inside the splats that act as the first layer of the coating consist of less HA than in the coating surface. This might partially account for the dissolution. The resorbable CPs would promote the uniform deposition of new mineralized bone matrix, thus enabling rapid integration with the surrounding host bone tissue in vivo. Other researchers have found that dissolution of the CP coating was accompanied by good goat bone marrow stromal cell attachment [8] and high proliferation rate and ALP activity of osteoblast-like cells [9].
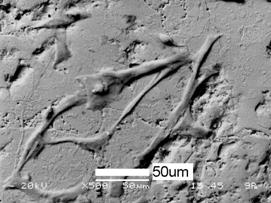
Figure 7. SEM picture showing attachment of the osteoblast cells on the HA coating.
Conclusion
The thermal sprayed HA splats are actually composed of ~30 nm nanostructures. The nanostructures in HA feedstock were retained and re-organized after the coating deposition. The melting/solidification of the nanosized fibers resulted in formation of spherical nanosized grains in the coatings. The nanostructured HA splats are capable of enhancing the attachment and proliferation of the osteoblast cells. The present study also revealed that the dissolution of the Ca/P-rich phases into the culture medium might promote the proliferation/differentiation of the cells.
References
- I. Sevostianov and M. Kachanov, “Modeling of the anisotropic elastic properties of plasma-sprayed coatings in relation to their microstructure”, Acta. Mater., 48 (2000) 1361-1370.
- S.H. Leigh, C.K. Lin and C.C. Berndt, “Elastic response of thermal spray deposits under indentation tests”, J. Am. Ceram. Soc., 80 (1997) 2093-2099.
- M. Pasandideh-Fard, V. Pershin, S. Chandra and J. Mostaghimi, “Splat shapes in a thermal spray coating process: simulations and experiments”, J. Therm. Spray Technol., 11 (2002) 206-217.
- J.P. Delplanque, W.D. Cai, R.H. Rangel and E.J. Lavernia, “Spray atomization and deposition of tantalum alloys”, Acta Materialia, 45 (1997) 5233-5243.
- X. Jiang, S. Sampath and H. Herman, “Grain morphology of molybdenum splats plasma-sprayed on glass substrates, Mater. Sci. Eng., A299 (2001) 235-240.
- T.J. Webster, R.W. Siegel and R. Bizios, ”Osteoblast adhesion on nanophase ceramics”, Biomaterials, 20 (1999) 1221-1227.
- K.A. Khor, H. Li, P. Cheang and S.Y. Boey, “In vitro behavior of HVOF sprayed calcium phosphate splats and coatings”, Biomaterials, 24 (2003) 723-735.
- J. Wang, P. Layrolle, M. Stigter and K. de Groot, “Biomimetic and electrolytic calcium phosphate coatings on titanium alloy: physicochemical characteristics and cell attachment”, Biomaterials, 25 (2004) 583-592.
- H. Kim, G. Georgiou, J.C. Knowles, Y. Koh and H. Kim, “Calcium phosphates and glass composite coatings on zirconia for enhanced biocompatibility”, Biomaterials 25 (2004) 4203-4213.
Contact Details
K.A. Khor
School of Mechanical and Aerospace Engineering
Nanyang Technological University
Nanyang Avenue, Singapore 639798
E-mail: [email protected]
|
H. Li
School of Mechanical and Aerospace Engineering
Nanyang Technological University
Nanyang Avenue, Singapore 639798
|
P. Cheang
School of Mechanical and Aerospace Engineering
Nanyang Technological University
Nanyang Avenue, Singapore 639798
|
|
|