May 4 2001
Article updated on 12/02/2020 by Ben Pilkington
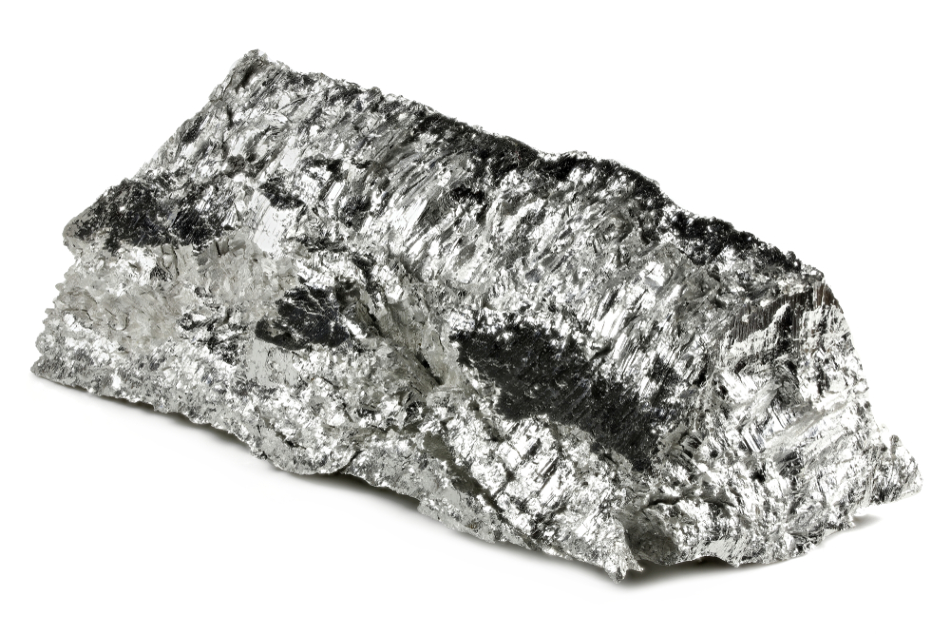
Image Credit: Bjoern Wylezich/Shutterstock.com
The 1937 discovery of the intense grain refining effect of zirconium was a major step forward in the development of magnesium alloys. The presence of zirconium gives a fine, equiaxed grain structure in sand castings, with typical grain sizes of 30-50 microns. This is compared to the relatively coarse dendritic structure of magnesium-aluminum-zinc (Mg-Al-Zn) alloys. As zirconium forms stable compounds with aluminum and manganese, it could not be used to grain refine Mg-Al-Zn alloys and, consequently, a totally new series of magnesium-zirconium (Mg-Zr) alloys was required.
The first Mg-Zr alloys contained zinc as a strengthening element, while subsequent alloys contained thorium, silver and, most recently, yttrium. Most Mg-Zr alloys contain rare earth elements such as cerium, neodymium and lanthanum, each of which form simple eutectic systems with magnesium and enhance castability due to the formation of grain boundary networks of relatively low melting point eutectics.
Continuous alloy development has led to major improvements in ambient temperature mechanical properties of Mg-Zr alloys. However, the significant improvement in high-temperature properties also allows the most recent alloys to be used up to 300 °C, which is compared to 150 °C for earlier Mg-Zr alloys. Figure 1 shows the variation of tensile strength and yield strength with temperature for various magnesium casting alloys.
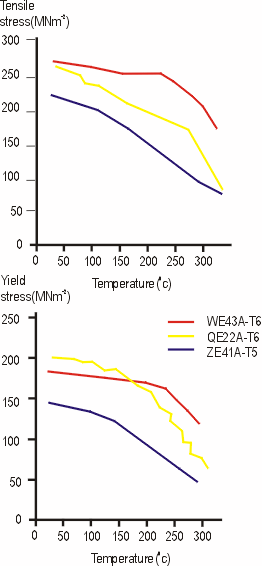
Figure 1. The effect of temperature on the ultimate tensile strength and yield strength of WE43, MSR (QE22) and RZ5 (ZE41).
Key Properties of Mg-Zr Alloys
- Lightweight
- Low density (two thirds that of aluminum)
- Good high-temperature mechanical properties
- Good to excellent corrosion resistance
Applications of Mg-Zr Alloys
Some of the common applications of Mg-Zr alloys within the aerospace industry can be found in gearboxes, transmissions, intermediate compressors, auxiliary gearboxes, generators, canopies and engine components are common.
Due to their lightweight and mechanical properties, Mg-Zr alloys are used in motor racing applications to reduce vehicle weight.
Other applications include electronics, sporting goods, nuclear applications, office equipment, flares, sacrificial anodes, flash photography and tools.
Mg-Zn-Rare Earth (RE)-Zr Alloys
For many years, Mg-Zn-RE-Zr alloys containing RE elements like cerium or lanthanum have been the most widely used for sand and gravity casting purposes. The single most used alloy for gearbox casings is RZ5 (ZE41), which retains mechanical properties up to about 150 °C. A second alloy, ZRE1 (EZ33), has been used extensively in jet engines where good creep properties are required at around 150 °C. Both types of alloys have excellent castability; in fact, complex castings can be made with virtually no microporosity.
Some Mg-Zn-Zr alloys without rare earth elements, including ZK51 (Mg 4.5%Zn 0.7%Zr), have been developed but are not widely used due to their poor castability and weldability.
Thorium-Containing Alloys
Magnesium thorium alloys, ZT1 (HZ32) and TZ6 (ZH62), were originally developed for high temperature creep resistance up to 350 °C. Today, these alloys are used primarily in aircraft engines, where good creep properties are essential, as lightweight alternatives to high-temperature aluminum alloys or titanium.
However, concerns over the manufacturing and foundry handling of Mg-Th alloys have led to complex and costly production operations, while environmental factors have increased disposal costs significantly. Mg-Th alloys are not being considered for new projects and yttrium containing alloys are likely to be used for similar future applications.
Silver-Containing Alloys
Silver-containing alloys were originally developed in an effort to improve ambient and high-temperature properties compared to Mg-Zn-RE-Zr alloys. While silver is the main strengthening element, neodymium or praseodymium rare earth elements are also used. In the T6 heat-treated condition, good tensile properties are maintained at temperatures above 200 °C; however, the creep properties of these alloys are often inferior as compared to those of thorium-containing alloys.
The most common silver-containing alloy is MSR (QE22), which contains 2.5% silver. In a later development, EQ21, which is a cheaper low silver alloy, was produced and found to have similar ambient temperature and slightly better high-temperature mechanical properties. These alloys are generally used in aerospace gearbox and engine casings, where improved high-temperature performance is required, such as the Rolls Royce Tay intermediate casing.
Yttrium-Containing Alloys (WE Alloys)
The Mg-Y-Nd-RE-Zr alloys, WE43 and WE54, were developed primarily to improve the mechanical properties of already existing magnesium alloys, particularly when used at elevated temperatures, as well as an alternative to thorium-containing alloys. WE43 contains less yttrium and rare earth elements than WE54, thereby allowing these alloys to have so lower strength but higher ductility. A major feature of WE alloys is their inherently superior corrosion resistance than other magnesium alloys. Corrosion rates of WE alloys in salt fog tests are similar to high purity AZ91 alloys and many aluminum casting alloys.
The aerospace industry has shown considerable interest in WE43 as a result of its combination of strength, ductility and corrosion resistance. Figure 1 shows that WE43 has superior strength to MSR at elevated temperatures and RZ5 at all temperatures. The properties of WE43 also compare very well with those of common aerospace aluminum alloys, such as A356 and A203, especially when exposed to temperatures greater than 200 °C, as demonstrated in figure 2. Additionally, the strength of WE43 is not reduced significantly after long term elevated temperature exposure whereas some aluminum casting alloys show substantial loss of properties.
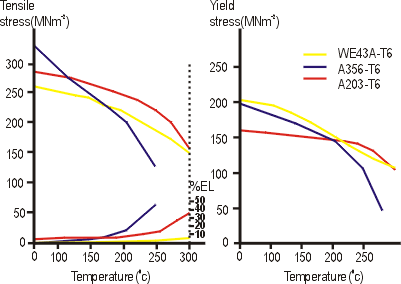
Figure 2. The effect of temperature on tensile properties of WE43 compared to aluminum alloys A356 and A203.
The WE54 alloy is stronger than WE43, despite being less ductile, and is aimed at applications where high strength is critical and/or ductility is less important. To date, much of the interest in WE54 has come from the high-performance racing car market as an alternative to aluminum alloys for large engine castings like cylinder blocks, heads and sumps, as well as smaller parts including covers and pump housings. Foundries in Europe, North America and Japan now have considerable expertise in casting WE alloys and offer WE alloy castings as part of their product range.