Superplastically formed (SPF) aluminium alloys have the ability to be stretched to several times their original size without failure when heated between 470-520°C. It is this superplasticity which allows components to be formed to a required shape by applying air pressure and/or tool movement within custom designed forming machines.
Thus the process effectively combines the enhanced design freedom of vacuum-formed plastics with all the material advantages and superior mechanical integrity of high performance alloys.
Benefits of Superplastic Forming
Commercially exploited for just over two decades, the process offers a range of important benefits, from both the design and production angles. To begin with there is the ability to form components with double curvature and smooth contours from single sheet in one operation, with exceptional dimensional accuracy and surface finish, and none of the ‘springback’ associated with cold forming techniques.
Because only single surface tools are employed, lead times are short and prototyping is both rapid and easy, because a range of sheet alloy thicknesses can be tested on the same tool. By the same token, the (already modest) tooling costs are significantly lower than those employed by more conventional alternatives - typically costing around 10% of those used for matched die stamping, for example.
Forming Techniques
There are five forming techniques currently in use to exploit these advantages. The method chosen depends upon design and performance criteria such as size, shape, and alloy characteristics. Two methods are frequently employed for the telecommunications and electronics industries.
Cavity Forming
The first and most commonly used is cavity forming, in which a preheated (SPF) aluminium sheet is clamped into position and forced into a mould cavity by air pressure. This method is ideal for producing more than one component from the same sheet, thus reducing unit costs (figure 1a).
Bubble Forming
For the second technique, bubble forming, the preheated alloy is clamped between a bubble plate and the tool plate, with air pressure being introduced from below to stretch the sheet into the bubble, fig 1. The tool is then pushed up through the plane of the sheet’s original position and into the bubble until the sheet is evenly tensioned at the required height. Air pressure is then applied above the bubble, forcing the sheet into close contact with the tool, thus allowing the production of highly complex forms with increased aspect ratios and more uniform thickness distribution.
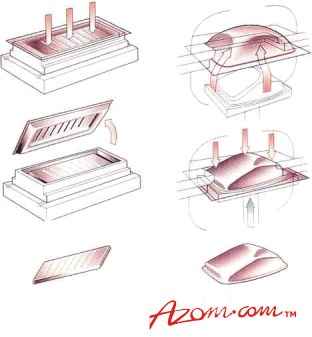
|
Figure 1. (a) Cavity forming and (b) bubble forming of SPF aluminium alloys.
|
In both cases it should be noted that only one component surface comes into contact with the tool, thus enabling exceptional finish standards to be achieved. Other key benefits include the ability to reduce subassemblies, simultaneously eliminating joints. In fact, many new applications develop from design enhancements which not only reduce weight but also decrease or even obviate the need for fabrication, welding or cold forming as well as improving strength and repeatability.
Wider advantages include the flexibility to produce tools from models, drawings or CAD data also used for machining and the incorporation of special features to improve stiffness and ease of assembly. With a maximum forming size of some 2.7 x 1.5m, the scope for fresh applications is extremely wide, whereas the alloys themselves can be joined by adhesive bonding or welding if necessary. They will also accept a wide range of surface treatments, paints and powders to international standards.
Applications in the Electronics Industry
The potential for the electronics industry is obvious, because many of these attributes are virtually standard enclosure requirements. For telecommunications manufacturers in particular, in which the process is increasingly challenging both synthetics and conventional metal forming, these attractions are heightened still further by the naturally strong RF and EMI shielding characteristics of the alloys.
Nortel’s Micro BTS Outdoor enclosure covers illustrate how this combination of design and production advantages can be exploited (the Micro BTS Outdoor is an environmentally-hardened mobile phone transceiver base station now being deployed in France, North America and Hong Kong, fig 2).
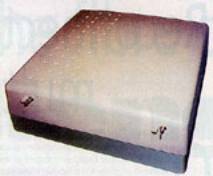
|
Figure 2. An example of a superplastically formed aluminium enclosure used for mobile phone base stations.
|
Design and production specifications for the 95 x 95cm outer and inner covers produced, respectively, from 2.0mm starting gauge 2004 and 1.6mm 5083 (SPF) aluminium alloys using the cavity forming method were particularly demanding.
As well as achieving aesthetic criteria that would complement Nortel's existing product portfolio, the covers had to provide protection from the elements and temperature extremes, together with a high level of vandal resistance within very tight weight limits. In addition, they also had to meet stringent standards of EMC compliance and LTV stability all within a short lead-time, as well as remaining cost effective in relation to anticipated product volumes.
After careful evaluation of alternative methods by the customer, superplastic aluminium emerged as the material best able to meet all of the criteria. Other options that were explored included glass-filled polymer mouldings and vacuum-formed plastic with internal Faraday cages and fabricated aluminium enclosures. None of these were able to satisfy all criteria. The external covers were so successful that the process was employed for the inner cover as well.
|