Several types of nanoscale filler are already commercially important, including fillers based on carbon. The most ubiquitous of these is carbon black, which finds widespread industrial application, particularly in vehicle tyres. Even with such a well established technology, further technical advances are possible and Degussa-Hüls has developed a nanostructured carbon black, called ECORAX, the surface of which consists of smaller and more disordered graphitic crystals than in normal carbon black. The resulting increased surface activity improves filler-polymer interactions and reduces rolling resistance and consequently fuel consumption (by about 2%) and exhaust emissions. Carbon Nanotubes and Nanofibres Another important type of carbon filler is carbon nanotubes and nanofibres. Much publicity has surrounded the development of single wall carbon nanotubes, the so-called Buckytubes, but while these are still some way off large-scale commercial production, the corresponding multi-layer carbon nanotubes have been known for some time and, furthermore, are available in practical commercial quantities. The layers consist of graphitic carbon and the tubes typically have an internal diameter of ca. 5 nm and external diameter of ca. 10 nm (Figure 1). Nanofibres of diameter up to 200 nm are also being produced (e.g. Pyrograf-III from Applied Sciences Inc., Ohio, USA). The Pyrograf-III fibres are manufactured by pyrolysis of hydrocarbon in the presence of a metal catalyst, which can remain embedded in the end of the fibre. The proportion of graphitic structures in the nanotubes and fibres can vary over a fairly wide range, with a concomitant variation in surface energies. The nanotubes tend to be of high purity and produce low outgassing during processing and, in comparison with carbon fibre and carbon black reinforced composites, the resultant nanocomposites have a much reduced tendency to shed particulates in use. Because of the electrical conductivity of the carbon nanotubes and nanofibres, the nanocomposites have much reduced surface resistivity in comparison to the unfilled polymer. These properties impact on the potential applications of the composites. 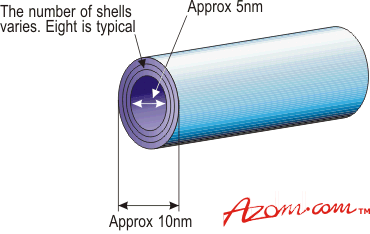 | Figure 1. Typical structure of a multi-layer carbon nanotube. | Carbon Nanotube Composites The nanotubes have been used in composites with a variety of matrix resins, including polyamides, polyesters, polycarbonates and their blends, polystyrene and high performance polymers such as polyphenylene sulphide (PPS), PEI and polyetheretherketone (PEEK). Extension to polyolefin systems is anticipated in the near future. Effective dispersion of the nanotubes into the polymer is essential to achieve the required properties. Addition of nanotubes to a polymer system leads to an increase in viscosity during processing and this effect can vary from small to significant; however, compared to incorporation of carbon fibre, melt flow can be significantly improved. The composite mechanical properties reported tend to be comparable to those found for composites based on conventional fillers and fibres, including a reduction in impact strength in some cases. Although the modulus of carbon nanotubes is very high, this has not yet been translated into big improvements in composite modulus, for reasons which are not fully understood. Applications A number of application areas are being pursued for the nanocomposites, particularly where the purity and electrical conductivity characteristics noted above are important. These include trays and wafer carriers for use in microelectronics, components with electrostatic discharge protection, electromagnetic interference (EMI) shielding and automotive fuel lines. PEEK, PEI and polycarbonate composites are all being actively investigated. The nanofibres have also been used to reinforce cement, where only a few % can have a significant effect on increasing compressive strength and reducing crack propagation. Work is also in progress at Trinity College, Dublin to incorporate both single wall (Buckytubes) and multi-wall carbon nanotubes into a luminescent poly(phenylene vinylene) (PPV) copolymer. The nanocomposites exhibit high electrical conductivity, significant third order non-linear optical behaviour and electroluminescence, while having substantially improved mechanical strength relative to the neat polymer. |