May 28 2008
"For the third trading period under the CO2 emissions trading system, ThyssenKrupp Steel needs allowances to be allocated largely free of charge. This is the only way we can remain competitive in the international markets, even if it means that the model iron and steel mills in Europe will face disadvantages as a result. We have to ensure a level global playing field for all market players."
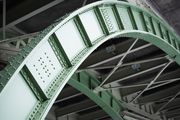
That was the opinion stated by Thomas Schlenz, Chairman of the Works Council of the ThyssenKrupp Group, and Dr. Gunnar Still, Group Environmental Protection Officer, during discussions with journalists in Düsseldorf. The European steel industry is jointly demanding full exemption from auctions on the basis of a benchmark, to be set in accordance with the lowest CO2 emissions to date on the respective production lines. In the allocation for the trading period from 2013 to 2020, producers must not fall short of this technically achieved benchmark.
Steel production outside Europe is not being impacted by costs for CO2 certificates. An international agreement, under which countries such as China and India are not obligated to reduce emissions, is also leading to a divergence in competitive conditions. Serious cost disadvantages are expected which ThyssenKrupp Steel cannot pass on to its customers or offset through rationalization measures. "As a consequence of a costly EU solution for emissions trading, we expect investments in steel production to be stopped, jeopardizing our integrated iron and steel making site in Duisburg with more than 10,000 jobs," said Schlenz, who warned that the industry could slowly abandon Europe as a production location.
But moving out of Europe would do nothing to improve the global CO2 balance. On the contrary: in the majority of cases, standards at overseas production facilities are significantly lower than those applied by European producers. CO2 emissions would therefore increase. Moreover, with production of 1.3 billion metric tons per year, steel is the number 1 material in the 21st century. Consumption will continue to increase in the coming years, particularly as there is still high catch-up demand in the BRIC states (Brazil, Russia, India and China). To compare: per capita steel consumption in Germany is 436 kg per year; in China the figure is 251 kg and in India only 35 kg.
Emissions trading is hitting power-intensive steel production doubly hard, as electricity prices are rising all the time. For ThyssenKrupp, the EU's plans will have a further substantial negative impact because they will also affect the energy network in Duisburg, Europe's biggest steel production site. Process waste gases created during the production of coke, pig iron and crude steel are reused in a similar way to the use of waste heat in combined heat and power plants.
"Yet Brussels is demanding that we purchase certificates for this eco-friendly process, which in this case even enables electricity to be generated," said Dr. Still. "Where is the justice in putting this exemplary use of residual energy to generate electricity – which we have been practicing for over 60 years – on a level with electricity production methods involving the combustion of coal, oil or gas?" Additional electricity also needs to be purchased from the grid for the production and processing of steel.
ThyssenKrupp is facing up to the challenges of climate change. "When it comes to climate protection, we are active on two fronts. On the one hand we undertake every possible effort to reduce the pollution associated with the production of our material. On the other hand we are developing steel further so that it can play an ever greater role in active climate protection," said Dr. Still. By way of an example he referred to the subject of weight reduction in auto construction: lighter steel bodies save more CO2 over their useful lives than is created during the production of all the steel used in a car. And he also quoted an example of advances in technology: since 1990 ThyssenKrupp Steel has reduced its CO2 emissions by 15%, since 1960 by as much as 40%. The limits of what is technically achievable in the blast furnace process have been reached. Together with the EU, the European steel industry is now concentrating on the ULCOS research project, which aims to develop completely new processes for the production of pig iron. Initial trials have been encouraging, but it will take decades until industrial-scale use is feasible.